Flight Control System Designs Get Smaller, More Powerful
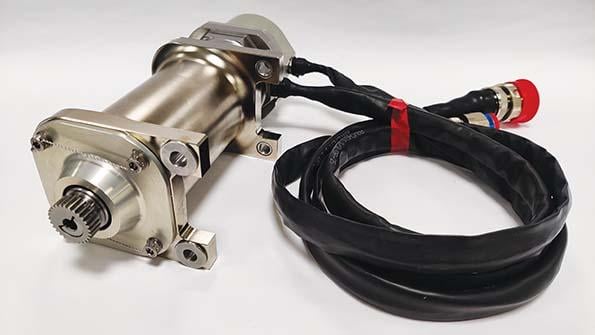
Emerging electromechanical actuation technologies for flight control systems will support more electric architecture.
With a new age of electrically driven advanced air mobility aircraft just over the horizon and net-zero sustainability goals looming, flight control systems are moving toward greater power and smaller packages. Both fly-by-wire and electromechanical actuation systems are presenting a two-pronged approach.
“The trend toward fly-by-wire is irreversible,” says Marc Duval-Destin, vice president for strategy, product policy and innovation at Thales Group’s flight avionics business line. “New aircraft designs—envisioned for single-pilot, electric vertical takeoff and landing—are complex and potentially unstable unless controlled using a fly-by-wire system. Only [those] systems, with their level of automation, will be able to cope with the rising level of complexity and provide the expected level of safety.”
Duval-Destin adds that flight control system (FCS) technologies have been extended to support functions that are today supported by lower-integrity aircraft systems.
“This will allow aircraft manufacturers to introduce new functions to expand the capabilities and safety of their aircraft,” he explains. “For instance, we see supporting autopilot, navigation or some surveillance functions, which are impossible to do with conventional flight controls. New capabilities could include unlosable permanent autopilot. Currently, autopilot systems sometimes disengage because of conditions that evolve out of the autopilot domain.”
The autopilot is the natural candidate to enrich FCS functionalities, as it will provide the “permanent autopilot” that aircrews have expected for years, Duval-Destin says. “Considering single-pilot operations, permanent flight management systems should be the cornerstone for emergency functions,” he says. “Also, permanent terrain protection is an interesting function to avoid collision with the ground.”
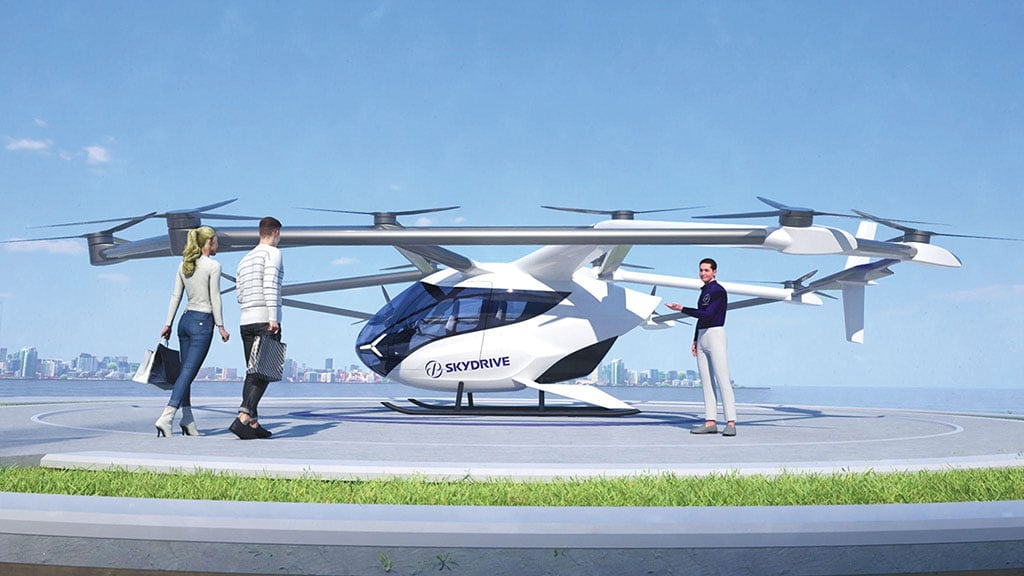
Then there are weight savings. According to Duval-Destin, FlytRise, Thales’ newest FCS, weighs 50% less than current systems, thanks to electronic integration and adapting to urban air mobility constraints. Airbus has selected FlytRise for its CityAirbus electric vertical-takeoff-and-landing (eVTOL) aircraft, as has SkyDrive in Toyota City, Japan, for its first eVTOL product. Certification of FlytRise is planned for 2027.
“Our next-generation flight control products will open a path to application to light business jets under Part 23 as they shift from mechanical flight control to fly-by-wire,” Duval-Destin says. “Thales is also engaged in uncrewed aerial vehicle (UAV) applications with ScaleFlyt, which Thales is proposing for lightweight UAVs, with the capability to support even beyond-visual-line-of-sight flights.”
AAM Market
Honeywell Aerospace is also pursuing the lighter, more compact fly-by-wire (FBW) systems. The Phoenix-based company introduced its Compact Fly-By-Wire system in June 2019, targeting the weight-sensitive advanced air mobility (AAM) market as well as other electric aircraft types. Swedish startup Heart Aerospace announced in October that it had selected Honeywell’s Compact Fly-By-Wire system for its ES-30 30-seat electric regional aircraft, now in development. The Lilium Jet, Vertical Aerospace VX4 eVTOL air taxis and Pipistrel’s Nuuva 300 eVTOL uncrewed cargo carrier are among the other applications previously announced.
“This will bring all of the benefits of larger, more complex systems to these markets at a size, weight, power and cost aligned with the needs of these lighter and more complex aircraft,” says Andrew Barker, vice president for integrated avionics at Honeywell. “The goal is to bring the safety of FBW to segments of the market that traditional systems would not fit due to size and cost.”
While the AAM market continues to be the focus, Barker says the technology was developed to also have potential application to other aircraft types. “Its advanced capabilities, light weight and small size enable the application of FBW controls to the Part 23, Part 25 and Part 27 markets, creating safer and smarter aircraft that better handle complex aerodynamics, weather and even pilot error,” Barker says.
By way of comparison, he points out that Honeywell’s Compact Fly-By-Wire system incorporates flight control computers the size of a book. “Just a few years ago, it would have taken a flight control computer the size of a bookshelf to offer the same capabilities,” Barker notes.
The flight control computer and actuators have lost considerable weight for the Compact Fly-By-Wire system, which Barker attributes to the use of smaller, less power-hungry electronics. Those electronics save space and reduce requirements for heavier materials that would be used for cooling/heat dissipation. “This holds true for both the actuation and computers,” he says.
Along with its reduced size, Barker says the Honeywell system offers triplex architecture and lockstep processing to maintain a level of safety expected of high-end FBW systems. The triplex architecture provides AAM aircraft the level of safety they will need in the challenging environments they will face, he says.
Triplex architecture, Barker explains, refers to the option to have three flight control computers working together to perform all requirements of the system—but employing dissimilar hardware and software to provide redundant backup options. “In that way, common failure pathways are eliminated, enhancing overall system safety,” he says. “Lockstep processing is also used to improve system safety by utilizing two processing channels that are constantly checking each other’s work.”
Electromechanical Actuation
But electromechanical actuation (EMA) systems will still command a major presence in FCS, and they have room for further development.
“The emerging technologies for FCS are those that support more electric architectures and sustainable net-zero flight,” says Jean-Marie Carvalho, vice president for actuation systems at Collins Aerospace. “This includes small, efficient electromechanical actuators applicable to high-lift systems and some primary flight control systems on commercial, military and AAM platforms.”
Carvalho further explains that electric architecture supports lighter-weight aircraft solutions—including future wing designs that will have smaller volumes and eliminate the need for hydraulic distribution systems. “EMA technology also provides better prognostic health-monitoring capability, supporting better aircraft dispatch reliability and maintenance effectivity,” he says. “Electromechanical technology will be core to FCS for the foreseeable future.”
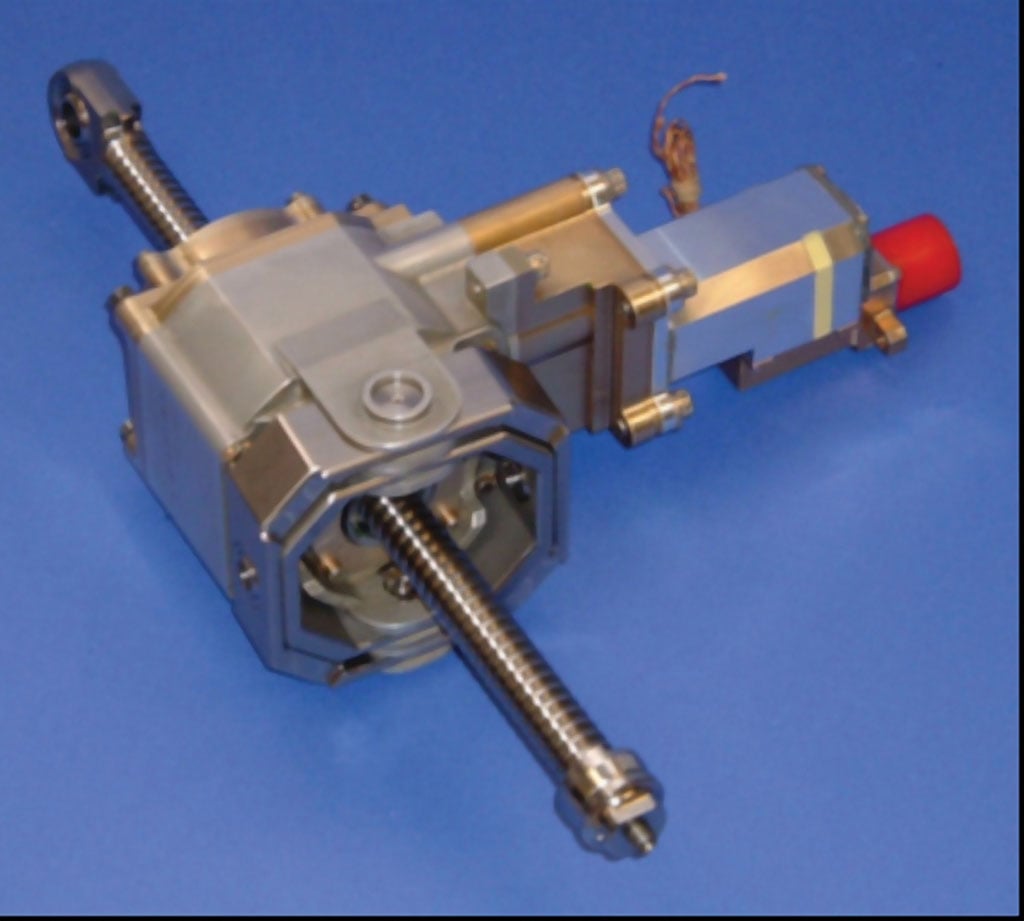
EMA systems convert electric energy directly into mechanical force. At Eaton Aerospace Group, flap and spoiler EMA systems are under development for high-lift functionality and variable camber performance during flight. “These systems are based upon a flap system that Eaton provided for the Embraer Phenom 100 business jet and the Bombardier CRJ200 regional jet,” says Jeffrey Skinner, director of engineering at the Irvine, California-based group. He notes that the Phenom 100 EMA architecture differed from the CRJ200 in that it removed the mechanical coupling, which used torque tubes to maintain synchronization of the flap panels through electronic control.
To illustrate, Skinner cites the Airbus A350 and Boeing 787, which began using flaps for inflight variable cambers to improve efficiency through small changes in the position of the flap panels. They did so by using differentials and additional motors to help disconnect a flap panel from the rest of the system during variable camber operations.
“Our specific system uses electrical synchronization, which allows independent control of the actuators when variable camber operations are necessary,” he says. “This eliminates the torque tubes, differentials and additional motors to drive a flap surface. By adding more functionality to the wing and improving wing efficiency, more fuel savings for the aircraft are possible.”
Skinner says Eaton has expanded the capabilities of the synchronization technology previously used on the Phenom 100 to enable more actuators to be synchronized. “There is also development on the use of sensor data to allow for higher-accuracy position control,” he says. “We’ve also been investigating different gear trains and motor configurations to allow for more compact and higher-power-density EMAs with improved safety and reliability goals.”
At the same time, he points out, EMA provides weight-saving benefits through the elimination of hydraulic lines, mechanical couplings, torque boxes and power drive units. “Additionally, the integration and assembly of the system allow for structural changes that may benefit the weight of the aircraft,” Skinner says.
He also points out that EMA systems add intelligence, expanding health-monitoring capabilities while using the existing sensors. “This results in assistance of monitoring the availability of the EMA system,” he explains.
Asked about time-on-wing advantages of EMA systems, Skinner stresses that the intent is for the system to stay on wing with no maintenance. “There are opportunities to improve the maintenance schedule and duration through use of the health monitors within the electronic control of the EMA system,” he notes.
Given the technology advancements in both EMA and FBW, it is logical to ask if there will be complete replacement of traditional hydraulic flight controls. According to Skinner, that depends on several factors.
“One of the main areas is the further development of motor technology and increase in power density of the motors. If motors can become a direct drive for the actuator and remove the need for gear trains and ball screws, then there is an opportunity for complete replacement,” he stresses.
“The other factor to consider is the architecture of the aircraft,” Skinner continues. “If the flight control surfaces changed in a way to reduce the loads and increase the number of redundant surfaces, then that improves the safety performance of the EMA system and further increases the chance of direct-drive actuators. However, if environmentally safe hydraulic fluids are created that maintain the same power density and thermal performance as current fluids, then there could be certain systems on the aircraft that stay hydraulic.”