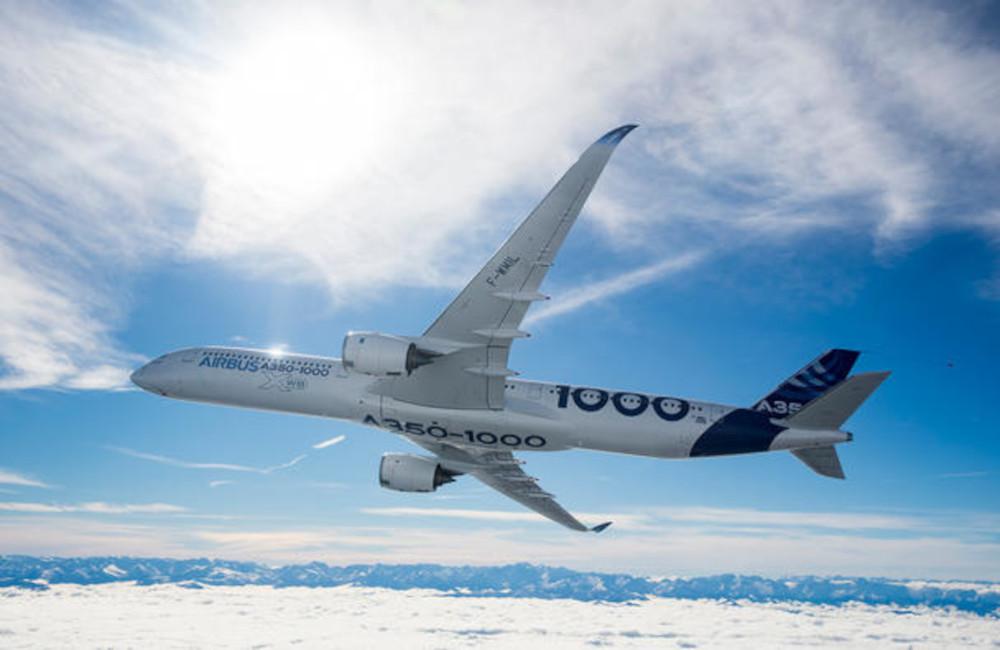
German MRO provider Lufthansa Technik was one of several companies that recently worked with Airbus on a project combining real and simulated product data for an Airbus A350-1000 cabin on the Circularise platform.
In recent years efforts have grown to improve the recycling of aircraft, with new facilities opening and new partnerships forming to address the reuse of materials like titanium and carbon fiber.
Yet having the right technologies and industrial capacity in place is only one piece of the puzzle, for a material can’t be effectively repurposed unless a recycler knows what it is made of, an issue that will become increasingly important as cabin suppliers explore the use of new materials to save weight.
For example, lightweight concept panels using bio-sourced resins or thermoplastics for cabin sidewalls are being tested with a view to certification and reliability.
The current honeycomb-based panels contain resins to make them safe from fires, and these pose problems for recycling, as they cannot easily be separated out once the part is no longer in use.
However, suppliers may not want to publish detailed information on their materials for fear of compromising their intellectual property, which can hinder the recycling of components from areas like the cabin, which forms up to 15% of an aircraft’s empty weight.
To address this Airbus and traceability platform Circularise have recently completed a proof of concept for digital product passports (DPP) for cabin items.
Working with suppliers like Thales, Diehl and Stelia, as well as MRO provider Lufthansa Technik, the project combined real and simulated product data for an Airbus A350-1000 cabin on the Circularise platform.
This included 88 nodes representing individual cabin components, with end goal was to ensure that materials are effectively reused or recycled at the end of their lifecycle, rather than ending up in landfills.
The group tested the implementation of DPPs as a data carrier for cabin interior components, enabling comprehensive traceability from raw material sourcing to end-of-life disposal or reuse.
As well as helping recyclers, the data is also useful for suppliers that need to measure their Scope 3 emissions.