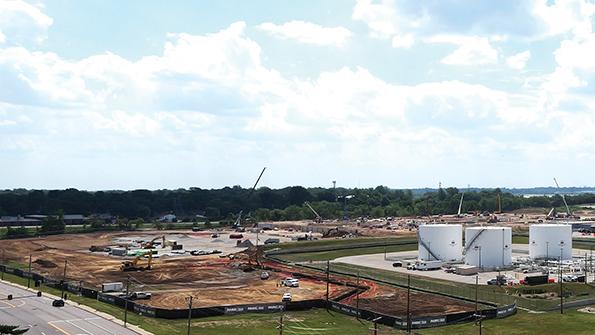
A new plant under construction in St. Louis will expand capacity for Boeing to produce the next generation of combat aircraft.
Boeing’s F/A-18 line is at risk of expiring in a few years, and the F-15 Eagle is flirting with its own twilight years. But looking south from what was once James S. McDonnell’s seventh-floor conference room, Steve Nordlund, vice president and general manager of Boeing’s air dominance division, points to a vacant patch of dirt a few thousand feet away as the company’s future.
The 110-acre tract on the southeast corner of St. Louis Lambert International Airport is supposed to give rise to the $1.8 billion Brownleigh project, a highly secure Advanced Combat Aircraft Facility to assure Boeing’s combat aircraft future for the coming decades. The Phase 1 plan calls for a three-bay, 979,000-ft.2 final assembly building and a 94,550-ft.2 radar cross-section test site, according to filings Boeing submitted to local government offices.
The construction site marks a surprising turnaround for the fighter manufacturing center that McDonnell established in St. Louis 80 years ago. After spending half a century mainly producing derivatives of two 1970s-era designs—the F-15 and F/A-18—Boeing, which merged with McDonnell Douglas in 1997, is investing billions in new facilities in St. Louis and two other sites with a goal of building the next generation of tactical combat aircraft.
- The fighter industry is rebuilding capacity after dismal streak
- Boeing unveils new fighter plant in St. Louis
- Delivery rebound planned for F-35s and F-16s
“We think this is a pretty big moment for the St. Louis site. Therefore, it’s a pretty big moment for the defense industrial base,” Nordlund says.
But it is still unclear when—or whether—Boeing will build a spiritual successor to the F-15. The U.S. Air Force passed over Boeing’s proposal for the first increment of the uncrewed Collaborative Combat Aircraft (CCA) family. Congress, meanwhile, is still weighing the Navy’s recent proposal to defer the start of full-scale development of the F/A-XX fighter by several years. At the same time, Air Force leaders are reevaluating the requirements for the Next-Generation Air Dominance (NGAD) program, risking a long delay of a pending contract award to Boeing or Lockheed Martin.
Although constrained by security rules from discussing plans for the CCA or NGAD programs, Nordlund is explicit about the impact of potential delays to funding for the next generation of U.S. combat aircraft.
“We will take it one day at a time and see how things unfold,” Nordlund says. “And we will make the appropriate business decisions, but we’re trying to lean forward to be ready for whatever our customer wants to do. And I think if you really want to keep up with your adversary, there is a capacity issue that has to be addressed.”
Around the Western fighter manufacturing industry, Nordlund’s call appears to resonate after several years of disappointing results.
Amid surging demand for current tactical aircraft types, industrial capacity shortfalls plague customers of most Western fighters. Lockheed and Dassault have amassed more orders in the past decade than all other competitors but are struggling to meet the demand, with backlogs stretching out years.
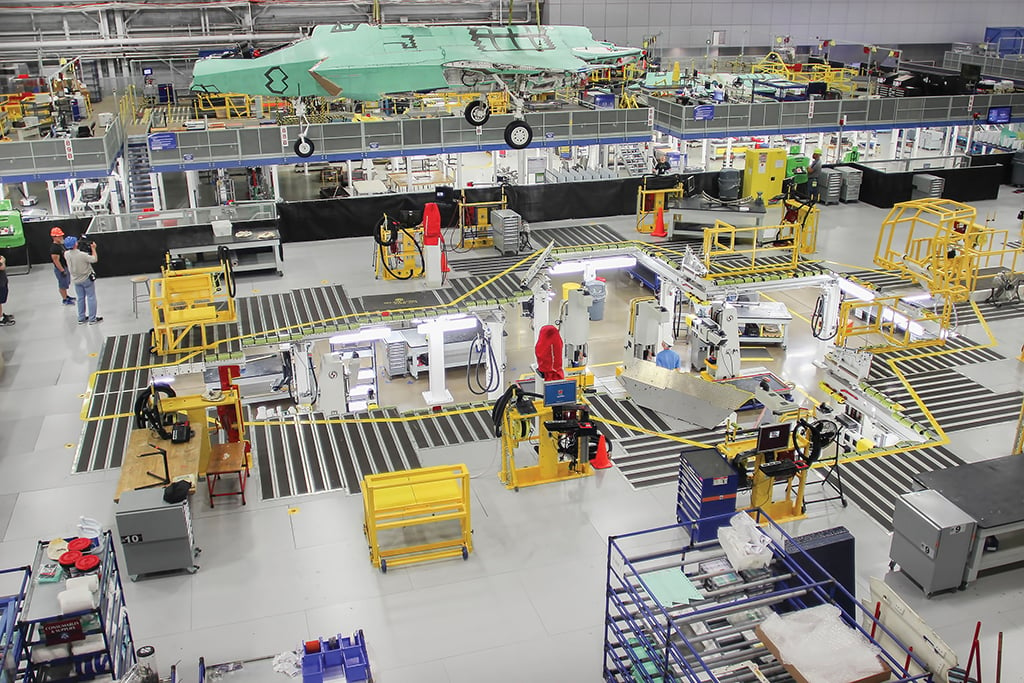
The global bottleneck became acute in 2023. Lockheed delivered only 97 F-35s due to software certification delays and supply chain shortages, meeting less than two-thirds of the planned annual total.
The situation appeared only slightly better in Merignac, France. Dassault delivered just 13 Rafales last year, missing the goal of 15 and with another 228 jets in the backlog. Meanwhile, Lockheed managed only five deliveries from a transplanted, four-year-old F-16 assembly line in South Carolina.
Manufacturers may struggle to keep pace with order demand for at least another year. Aiming to return a full delivery rate, the F-35 Joint Program Office (JPO) expects Lockheed to resolve an avionics shortage by year-end and complete full certification of a critical new block of software in 2025. Moreover, German supplier Rheinmetall is scheduled to open a new assembly line for the stealth fighter’s intricate center fuselage in 2026, eliminating a bottleneck that constrains F-35 deliveries to an annual maximum of 156. In France, Dassault executives have outlined plans to nearly double deliveries to 22 Rafales this year and expand the line to 33 as early as 2026 or 2027.
Other U.S. and Western assembly lines also are being readied for growth. In late June, South Korea awarded Korea Aerospace Industries a three-year contract to launch production of the first 20 KF-21 fighters. Saab Gripens, meanwhile, will be delivered for the first time in 2025 from Embraer’s final assembly line in Brazil, and even more of the single-engine jets will roll out of the Swedish manufacturer’s Linkoping site for its air force. The F-16 revival is accelerating, too, with 19-21 deliveries expected this year and plans to produce 48 annually in the “mid-2020s,” Lockheed Martin says.
This planned global ramp-up comes as fighter manufacturers cope with a broader manufacturing labor shortage. In Greenville, South Carolina, alone, Lockheed’s payroll nearly tripled to 1,700 workers this year, compared with only 600 when the line opened in 2019. The hiring binge came “with a lot of training and activity and growth in the line itself,” says OJ Sanchez, vice president of Lockheed’s Integrated Fighter Group.
A key part of the mitigation strategy is expanding the supplier network. Poland’s PZL Mielec, for example, now builds aft fuselages for the F-16 Block 70/72. Lockheed added 80 positions in Johnstown, Pennsylvania, in 2021 as well to fill gaps in the F-16 supply chain.
“We’ve tried to be very proactive about reducing the risk we’re all feeling in the ramp-up from COVID and the strain in the supply chain,” Sanchez says.
Other companies are adopting new manufacturing practices, albeit with some difficulty. Boeing, for example, has embraced the practice of full-size determinant assembly (FSDA) to speed up final assembly. By switching from a paper-based to a digital design process, Boeing’s suppliers are given a level of accuracy needed to drill holes precisely at the piece-part level, allowing workers on the final assembly line to join and fasten large aircraft sections without the need for cumbersome and time-consuming tooling jigs. But the transition to FSDA in St. Louis got off to a difficult start and was blamed for a two-year delay in MQ-25 production and monthslong setbacks during the first F-15EX lot.
As the Advanced Combat Aircraft Facility rises on the Brownleigh site, Boeing officials say both the MQ-25 and F-15EX programs are in ramp-up mode again. And next comes the start of low-rate initial production for the T-7A Red Hawk, the new advanced jet trainer ordered by the U.S. Air Force.
As the first crewed aircraft to enter Boeing’s FSDA process, the company expects each T-7A will spend only four months in final assembly in St. Louis. In addition to pre-drilled holes, electrical wiring and hydraulic lines are planned to be pre-installed in the forward fuselage by Texas-based Qarbon Aerospace and the aft fuselage by Saab’s plant in Indiana.
“I think this is one of the most visible aspects of how digital engineering has helped us,” says Nathan Russell, Boeing’s program manager for T-7A low-rate initial production. “You’ve got to think about a forward fuselage that was designed by Boeing and an aft fuselage that was designed by Saab. So you’re talking two different countries separated by six . . . time zones, with different languages, different engineering tool sets, and yet we’re able to design two major aircraft assemblies that come together in a very, very short period of time.”
Comments