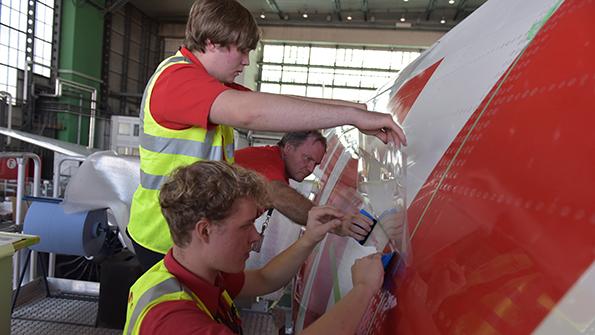
Lufthansa Technik and BASF strive to reach the highest possible riblet coverage to maximize fuel and emission savings.
Lufthansa Technik and coating specialist BASF are continuing to develop their AeroShark surface technology, which is designed to optimize aerodynamics and reduce fuel usage and carbon dioxide emissions.
The AeroShark technology uses riblet films that mimic the properties of shark skin, which the companies say has favorable flow characteristics. In December 2022, Lufthansa Technik (LHT) obtained a supplemental type certificate (STC) from the European Union Aviation Safety Agency to provide AeroShark modification on Boeing 777s and 777-300ERs. It recently also received STC approval from the FAA. LHT and BASF say AeroShark can reduce fuel consumption by approximately 1%.
In May 2021, Lufthansa Cargo became the launch customer for AeroShark, and last year, Swiss International Air Lines (Swiss) became the first passenger airline to install the technology. In October 2022, Swiss’ first Boeing 777 modified with AeroShark technology entered service. According to LHT, it provided fuel savings of slightly more than 1%. “This equates to an annual savings of 400 tons of jet fuel and over 1,200 tons of carbon dioxide [CO2] for just one aircraft,” says Oliver Oeser, AeroShark project manager of aircraft modification at the German MRO provider.
To date, LHT has modified 10 Swiss 777-300ERs, and their fuel consumption data shows a clear reduction in usage, Oeser notes.
In February, Lufthansa Cargo’s first freighter modified with AeroShark technology entered service. The modification of the next freighter is scheduled for July. LHT estimates that Lufthansa Cargo’s entire fleet of 777s will result in annual savings of more than 4,000 tons of kerosene and about 13,000 tons of CO2 emissions.
Oeser notes that following the modification of Lufthansa Cargo’s fleet of 777Fs and Swiss’ fleet of 777-300ERs, the Lufthansa Group’s carbon footprint will decrease by more than 25,000 tons annually.
Oeser says the technology requires little maintenance. The riblet film, used for drag reduction, has a minimum durability of four years, which is designed to coincide with standard 777 heavy check intervals. No additional downtime is required for the application or exchange of the riblet films.
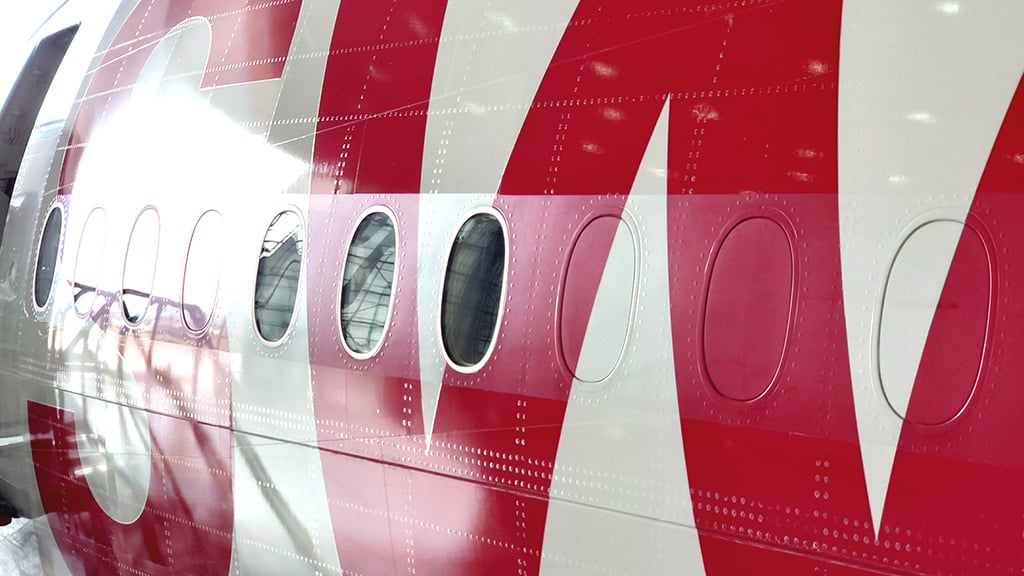
“The riblet film is applied in small patches of 0.5 m2 [5.4 ft.2]. Thus, they can be partially removed in case of repair, inspection or other MRO operations on certain parts of the aircraft and can be reapplied,” Oeser explains.
Following the installation, LHT has received positive feedback from both Swiss and Lufthansa Cargo. “We have recently started to offer AeroShark's 777 modification to first customers outside our parent Lufthansa Group,” Oeser says. “In the coming months, we hope to announce the next AeroShark adopters.”
LHT and BASF intend to develop AeroShark technology to improve support for airlines in achieving their emissions targets. Oeser notes that the companies are focusing on long-haul aircraft, since they spend significantly longer periods of time in cruise flight, for which AeroShark design is optimized.
“We will be guided by factors such as market penetration or the remaining life cycle of certain aircraft types,” Oeser says. “A hot candidate for the next AeroShark type could be, for example, the Airbus A330.”
The companies also are looking to develop and certify AeroShark modifications for additional aircraft types and larger surface areas. Currently, the riblet films cover a substantial portion of the fuselage and engine nacelles, comprising about 40% of the aircraft’s total surface area.
Oeser points out that it is not possible to reach 100% coverage due to airflow efficiency and the need for sensors to have specially defined flow conditions. “However, our aim is to come as close to a full modification as possible and certifiable,” he says. “We see even more fuel and emission savings potential for this technology.
“In initial model calculations (based on computational fluid dynamics), the shark skin technology in its maximum expansion stage (the ‘close-to-100%’ configuration outlined above) could even avoid CO2 emissions on the scale of up to 3%,” Oeser adds.