Aircraft Inspections With Drones Accelerate Toward Next Evolution

Artificial intelligence could help inspectors more quickly assess images taken by drones during visual inspections.
A decade after drone use for aircraft inspections first started gaining aftermarket traction, the technology is finally making serious headway with regulators and OEMs.
Several aviation companies made headlines last year for achieving regulatory acceptance to conduct drone-based inspections from their local civil aviation authorities. Delta Air Lines in the U.S. is now authorized to conduct inspections on its Airbus and Boeing aircraft, and Jet Aviation in Switzerland is allowed to perform general visual inspections (GVI) and lightning strike inspections on all the aircraft it handles, including Airbus, Boeing, Bombardier, Dassault, Embraer and Gulfstream models.
Drone inspection startups Mainblades and Donecle moved the needle on OEM approval as well. Airbus had already approved both companies’ drones, and Boeing recently incorporated them into its 737 aircraft maintenance manual.
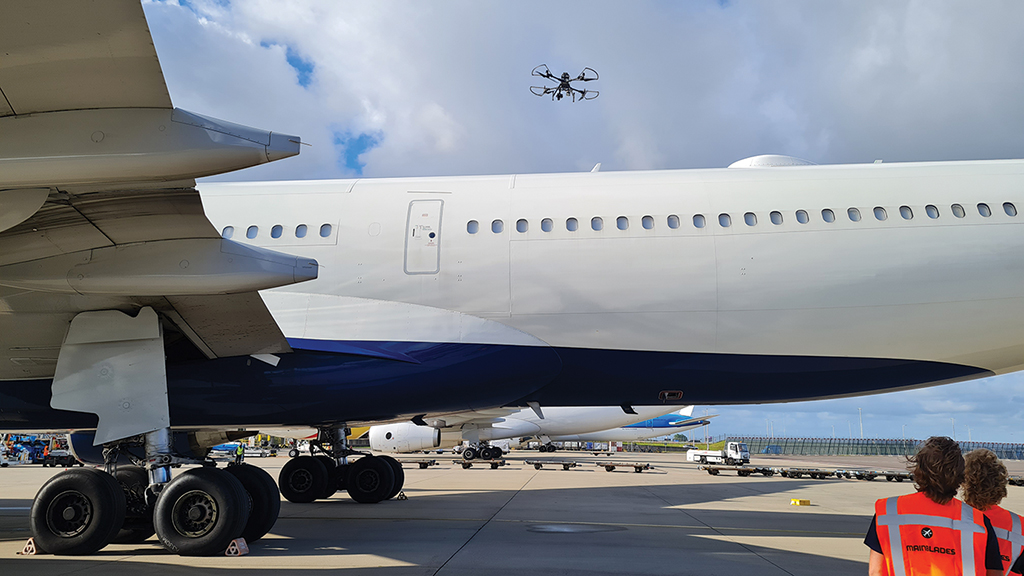
“Everyone has been talking about drones for the last 10 years,” Donecle CEO Matthieu Claybrough tells Inside MRO. “Now they’re being qualified. We expect that by the end of 2025, all the key players will have all the key approvals—so all aircraft, all tasks. It’s probably still one year until all that rolls out, and we expect to be basically scaling drone technology throughout 2026 with higher-volume production.”
Donecle raised approximately $6 million in new funding in 2024 to support a future U.S. subsidiary in Chicago and opened new offices in its home base of Toulouse to support its planned ramp-up. The manufacturer has more than 30 drones operating worldwide and a production capability of four drones per month.
In the past decade, a growing lineup of global airlines and MROs have been testing and incorporating drones into maintenance processes. In the U.S., Donecle says it has an unnamed major airline customer that has also achieved FAA approval, and the agency tells Inside MRO it has authorized United Airlines to use drones for conditional inspections.
Many airlines in Europe and South America have embraced the technology. European carriers, such as Austrian Airlines and KLM, are using drones, and Donecle is launching aviation authority approval requests in Germany and the Netherlands. LATAM and Viva Aerobus are using the technology in South America, where Claybrough says Donecle has drones “in most of the countries” and is in talks with other airlines. “We may actually be in a position where, in less than one year, the entire South American region will already be using that technology,” he says.

Donecle is beginning to target the Middle East and Asia, too. Mainblades is seeing interest from Japanese operators and is working with Lufthansa Technik Philippines, aiming to expand its partnership to other Lufthansa Technik locations. The Civil Aviation Authority of Singapore (CAAS) has authorized ST Engineering Aerospace to conduct drone-based inspections, while Korean Air is developing a novel “drone swarm” concept.
According to Mainblades CEO Dejan Borota, Asia—particularly Singapore—is “very interested” in drone inspections. “Even in Asia, where labor is cheaper and there are many aircraft down for heavy maintenance, they’re also looking at this because they don’t have the capacity,” Borota says. “We’ve talked to a number of MROs who are fully booked this year, next year and the year after” but wish they could take on more, he notes.
“Regulatory trajectories are key,” since the technology is “taking very long to take off,” Borota adds. “But the fact that we now have drones in production with our customers and we can actually circle back to profits is bringing a lot of energy.”
THE REGULATORY HURDLE
Why has it taken so long for aviation authorities and OEMs to provide acceptance and approvals? While some in the industry say regulators are notoriously slow to embrace new technology, several factors create additional complications.
“There are essentially two ways of authorizing drone usage,” Claybrough explains. The first is for an aircraft operator to update their maintenance manual with the technology and submit it to their local authority. From there, the operator must prove that the drone technology is equivalent to traditional inspection methods, after which the aviation authority provides feedback and acceptance.
“The advantage is that it’s possible to immediately address all aircraft types,” Claybrough says. “It’s one document for multiple fleets. However, it’s local to the operator, so they can use it in all their stations, but no one else can take a direct credit from it.”
The second option is for an aircraft manufacturer to test the technology and list the drone as an alternative task in its maintenance manual. “Here, the difference is that it’s per aircraft type and per task,” Claybrough says. “It’s also slower, because typically the aircraft manufacturers do one task at a time or one aircraft at a time. However, as soon as it’s published, it’s valid worldwide for all the operators that have that aircraft.”
An airline that has already gone through the first option but operates a fleet type that also has the manufacturer’s maintenance manual approval for drone inspections can choose whether to operate under the OEM task or the internal task. “There are very few differences,” Claybrough says. “There are just responsibility and insurance transfers because more of the responsibility is offset to the aircraft manufacturer when they approve, whereas when the airline or the operator approves, they carry a slightly higher responsibility.”
“There are an increasing number of operators and MROs realizing, ‘We have to do this ourselves because if we follow the OEM route, it will have implications,’” Borota says. “If they approve it themselves, they can dictate what the terms are and under what conditions they’re going to approve the drone, for what use cases.”
Delta took the individual approach, submitting a data package to the FAA in the fall of 2023 before achieving acceptance in early 2024. According to Emma Galarza, senior engineer for Delta TechOps’ technology development team, “it was certainly a longer process,” requiring a lot of work in partnership with the FAA and Mainblades.
“We essentially designed an experiment to understand how this new technology would work within our airline and within our MRO space and then how that would compare to traditional methods,” Galarza says. “It was a lot of working with our technicians, mechanics and inspectors, understanding from them how this would affect our process and making sure that they had everything they needed for it to be a true equivalency to a traditional inspection.”
That process required considerable data collection, including for different shifts, technicians and types of aircraft. “During that entire process, we invited the FAA to come and observe our operations to have them understand where we were going and where we saw the future of this type of program,” she says. It also entailed “working with some OEMs and shedding some light on what we were doing there as well, and making small adjustments along the way with [Mainblades] based on the feedback that we got from our technicians and inspectors here,” she adds.
Notably, Delta’s FAA acceptance authorizes the airline to perform drone-based inspections both in the hangar and outside at its maintenance bases in Atlanta, Detroit and Minneapolis. Outdoor approval has been trickier for operators because it requires coordination not just with the local aviation authority but also with local airports, airport authorities and air traffic control.
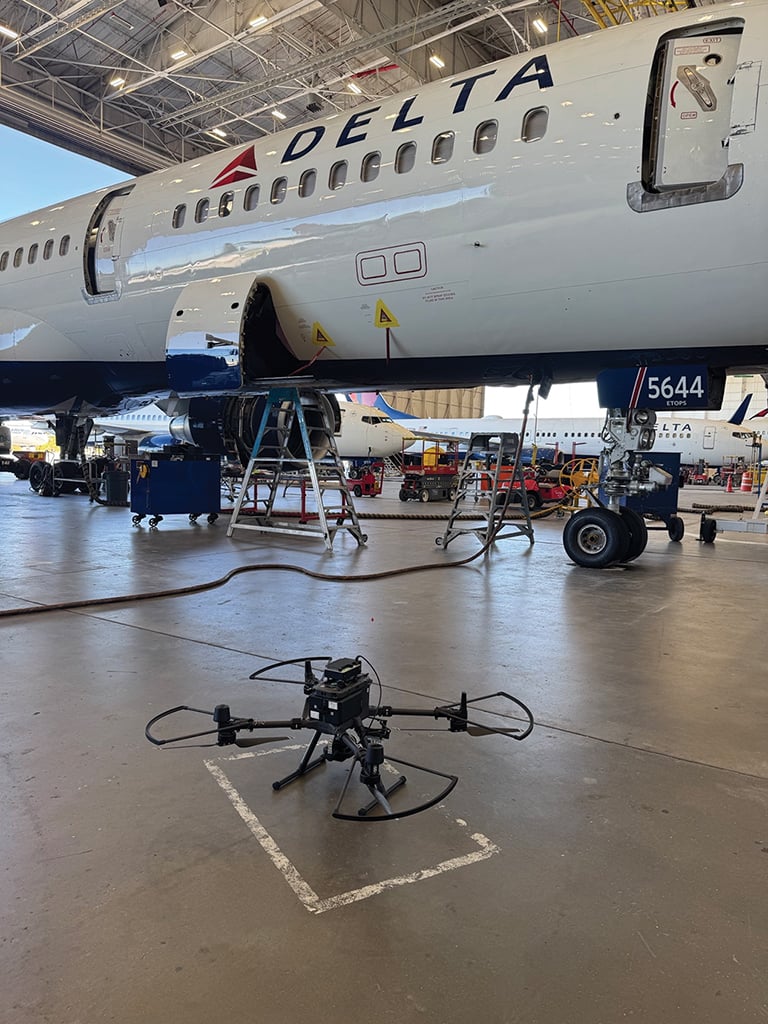
Borota notes that outdoor approval is further complicated for companies that operate hangars without doors, such as some MROs in Asia, since some aviation authorities regard those operations as outdoor.
“We have approximately 20 airports [that] are authorized [for outdoor drone inspections], but that’s throughout the world, and it’s still case by case,” Claybrough says.
In addition to Delta, Borota says KLM has outdoor approval in Amsterdam, and “we’re now doing cross-border applications for different countries in Europe” as well as in Asia, he notes.
Delta had to expand its stakeholder collaboration to receive the outdoor approval. “Overarchingly, the philosophy as it comes to working with the regulator and the stakeholders with this program was to be frequent, early and often with their inclusion,” says John Mathis, manager of technology development engineering at Delta Air Lines. While the airport was an obvious stakeholder, “we soon learned it was the Department of Homeland Security and the city of Atlanta and so on and so forth,” Mathis says.
He notes that much of the process boiled down to “seeing is believing”—bringing various parties on site to demonstrate the safety of the drone inspection process.
“It’s something very new,” Galarza adds. “There’s not a lot of precedent set for having these types of approvals to fly in controlled airspace. It was a lot of relationship-building and understanding who needed to be involved.”
Delta has permission to fly drones outdoors in specific locations at its approved bases, and it is hoping to expand elsewhere as the program grows. “We will continue to work with all of those groups to make sure that, year over year, any adjustments that are necessary are made and that we are open and flexible to making that a cooperative setup with them,” Galarza says.
AI VERSUS HUMAN INSPECTORS
Another piece of the regulatory acceptance puzzle is the role of artificial intelligence (AI) in reviewing the images that drones capture during inspections.
When asked about the regulatory timeline for certification of AI in conjunction with drone inspections—and what a company would need to prove to achieve it—the FAA and European Union Aviation Safety Agency (EASA) pointed to their respective AI road maps.
Both road maps acknowledge the potential benefits of AI for maintenance, and EASA’s specifically lays out a technology level readiness timeline. At the first level—which the road map says is taking place now—AI will augment a human’s ability and serve as an assistant to help make decisions. At the highest level, which EASA estimates will not take place until around at least 2035-50, an AI-based system would perform decisions and actions that a human could not override.
“There has been no request to deploy AI in drone-based inspections in Singapore,” says Alan Foo, director of flight standards at CAAS and senior director of its Safety Regulation Group. But Foo notes that if a company intends to use the technology, it “will need to work with an OEM and airline to demonstrate the efficacy of the inspection result, which should be similar or better than when the aircraft is being inspected by an aircraft engineer.”
Mathis at Delta says: “There’s a lot of regulatory conversation that needs to happen” before the airline publicly discloses any details about possible incorporation of AI into its drone inspections. Its maintenance team reviews now all photos taken by the drones.
“Our program is structured,” Galarza explains. “[The drones] take a certain amount of pictures set with a certain amount of overlap for each aircraft, and each of those images is reviewed by our maintenance team. While the drone is flying, we have teams that are reviewing the images that it’s already taken, and that’s been a really interesting process to get to our most efficient setup with the program.”
Borota says Mainblades’ software already uses AI, which is being trained on different use cases and models to classify types of damage on aircraft. “We have people who are using [AI] to shorten their view time, but . . . it’s still a manual review,” he says. On average, Borota says it takes users 20-30 sec. to assess each photo. Mainblades hopes AI assistance can reduce that time to less than 10 sec.
“AI really complements the technicians well in the sense that the technicians are very good at finding unexpected or out of the ordinary damages or strange things with a large defect, and the AI is very good at finding the small ones,” Claybrough says. He notes that Donecle sees AI performing better than human inspectors at identifying small cracks and lightning strikes, so the technology’s first phase is focused on “combining the best of both worlds” between technician and machine.
In the second phase, the AI would automatically assess “the easy images” and remove them from the scope to reduce workload for technicians, Claybrough says. “Say there are 1,000 pictures now on large aircraft,” he explains. “Maybe the AI can filter out 500 of those easy ones and have the technician focus on the more complex areas.”
However, it will be a while before technicians’ only role in the process will be reviewing or signing off on the job, Claybrough says. Donecle is collaborating with EASA and aligning milestones to its AI road map. In drone inspection cases, he expects the industry will not see fully qualified AI for finishing task cards until around 2028.
SWARM APPROACH
While every company interviewed by Inside MRO touts the safety benefits that drones provide by reducing the need to place technicians at height, the companies are also aiming to reduce turnaround time. For instance, Delta notes that its drones can photograph a narrowbody aircraft in less than 90 min. and a widebody aircraft in less than 2 hr., compared with manual inspections that average about 16 hr.
Galarza adds that the technology was particularly helpful last summer: When storm events grounded several of Delta’s aircraft, the airline was able to inspect more aircraft simultaneously than it could have through traditional inspection methods.
Some companies are looking to boost efficiency benefits further by doubling up on technologies. Korean Air, for example, uses a drone swarm model that pairs four systems simultaneously with a rover and AI hardware. The airline says the technology reduces inspection time by 75% compared with the deployment of a single drone and ensures complete coverage if one malfunctions.
Korean Air first publicized the technology in 2021 and is developing it further through a government initiative. This year, the airline will focus on fabricating and evaluating the swarm drone inspection components. Next year, it plans to integrate and validate the system in simulated environments using a decommissioned aircraft. In 2027, the carrier intends to conduct airport demonstrations during a pilot operation.
Korean Air says it eventually aims to provide the product as a service to third-party customers and has received inquiries about its potential use for other large-scale inspections, such as for maritime vessels.
Borota says Mainblades tested multidrone inspections and acknowledges that smaller, swarm-based drones could have use cases for inspections of small, difficult-to-reach areas, such as between the airframe and engine on a narrowbody. However, he asserts that even if flying multiple drones might reduce groundwork time during an inspection, the major bottleneck in drone inspections is review time , and he says that a multidrone approach could actually complicate this.
“It’s not about your flight time,” he says. “You can fly 20, 30 or 40 min., but it doesn’t matter because the current regulatory approvals still require people to manually look at photos. The current implementation should actually focus on, ‘How can I get the least amount of photos?’ because it’s still manual labor. But if I have to go to 200 or 800 photos, that’s going to cost me a lot of time.”
Borota notes that Mainblade’s current focus is on enabling photo review while the drone is still flying. “I see competitors of ours say: ‘We’re super quick. We can fly in 20 min.’ Who cares?” he remarks. “You can fly 1 hr., but if you can parallel your review process and be finished in 1.5 hr., that’s the winner. You want to have better camera systems which can have greater pictures that you can review faster and a system that can work [in] parallel so the review can happen at the same time.”
Claybrough says he generally agrees with this viewpoint, although he could see potential value for lightning strike events on large aircraft, such as Korean Air’s Airbus A380s.
PAIRING TECHNOLOGY
Chasing further efficiencies, Donecle has been developing additional concepts that combine its inspection drones with other damage detection technologies. In 2020, the company paired up with 8tree, a provider of handheld 3D surface inspection tools, to combine Donecle drones with its DentCheck 3D sensor. The companies say the combined product, called Iris DentCheck, can detect and measure dents and buckles on aircraft surfaces 50 times more quickly than manual methods.
Claybrough says the technologies are complementary, in part because of common training, usage and reporting and also because of DentCheck’s existing OEM approvals, which will shorten approval time and time to market for Iris DentCheck.
Donecle is looking into pairing its drones with active thermography technology, which heats aircraft surfaces and measures the response with a thermal camera to detect debonding, delamination and water ingestion on composite surfaces. The technology is still in an internal pilot phase, but Claybrough expects this to become Donecle’s third product line.
Mainblades is investigating the incorporation of external technologies, such as dent sensors, but Borota is still cautious about their efficacy when mounted on a drone. “[These technologies] are approved by the OEMs to have a certain accuracy, but [when you] put it on a drone, it’s always going to be wobbly because the drone has vibrations in it,” he says. “Will the OEM accept that? Will the airlines do the same as with the drone—check it themselves and put it in their manuals?”
Borota has similar apprehension about incorporating such technology as infrared. “If you look inside the structure of a composite aircraft and you see something with an infrared [that] is inside, it’s not part of a GVI,” he says. “You might have to ground that vehicle because you see something on the inside.
“I don’t think it’s good to be only technology-driven,” he adds. “There’s this general trend in the aviation world where everybody wants to be innovation-driven, but as soon as they start looking into these solutions . . . they come to the practicality of, ‘Is this actually going to help me?’ You have to think of it as, ‘What helps the operation, what helps the airlines minimize their time on the ground, and what makes it safer?’ ”