Winglets Evolve To Boost Efficiency Across Aircraft Spectrum

API has certified its split scimitar winglet on all models of the Boeing 737NG, including the Boeing Business Jet variant.
Anyone who occupies a window seat with a clear line of sight over the wing might notice an upswept wingtip. These end-of-wing devices, known as winglets, were developed to reduce drag, improve fuel efficiency and extend range.
As an aircraft flies, it creates a pressure differential between the lower- and higher-pressure air flows moving over the upper and lower surfaces of the wings, respectively. At the wingtip, the two airflows mix, producing drag-inducing vortices. Winglets essentially stop the mixing process, mitigating pressure differences and vortices, with less drag and greater fuel savings as the payoff.
“What we typically call ‘winglets’ is most likely attributable to Richard Whitcomb, who pioneered the addition of near-vertical extensions to wing tips in a 1970s NASA study,” Aviation Partners Inc. (API) President Gary Dunn explains.
Seattle-based API was formed in 1993. That same year, the company certified its first winglet retrofit for the Gulfstream II business jet using its own blended winglet design and proprietary technology. Blending seamlessly with the wing and characterized by a racy outward curve, Dunn reports the blended winglet is the most common type in use today on both business and commercial jets.
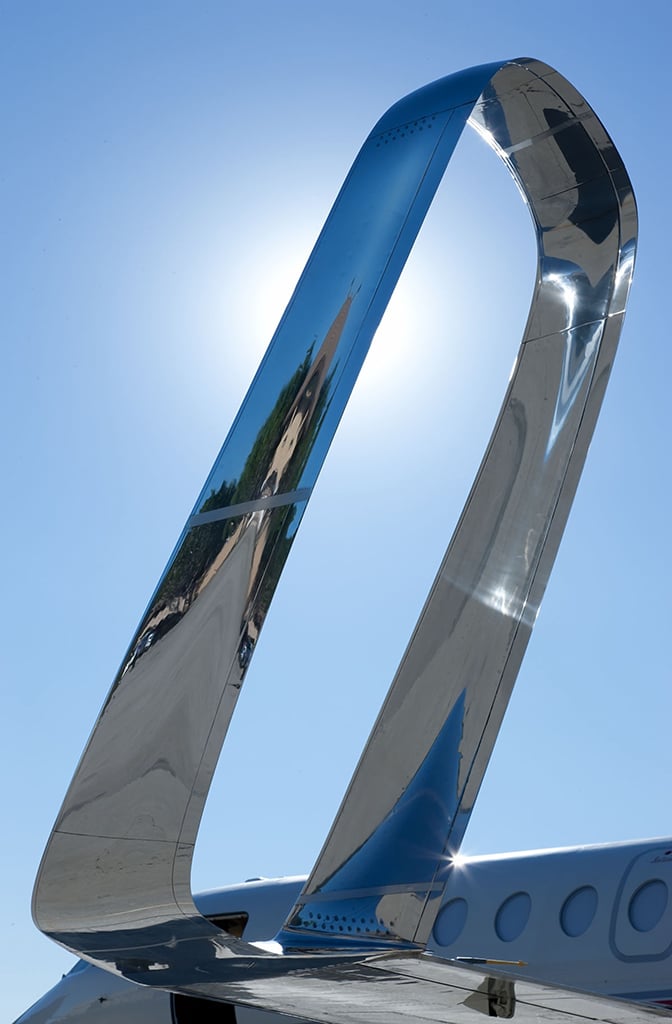
“The blended winglet was an improvement both aesthetically and in performance over previous, more angular transition winglets,” he notes. “API pioneered the blended winglet and the industry norm of retrofitting winglets to existing business and commercial aircraft.”
Dunn adds that in 1999, a separate joint venture company, Aviation Partners Boeing (APB), was created to make API’s proprietary technology available for line- and retrofit on a wide range of Boeing jets. To date, API’s blended winglet has been certified on all models of the 737 Classic, 737NG and 737-based Boeing Business Jet, as well as the 757-200, 757-300, 767-300ER and 767-300ERF.
From Scimitars to Spiroids
In addition to the conventional blended winglet, API designed an improved version for the Boeing 737NG. Called the split scimitar winglet, this design added a lower blade to the original blended winglet. A similar design is used on the 737 MAX, which was created by Boeing based on its ecoDemonstrator technology demonstration program (AW&ST May 7, 2012, p. 37). When Boeing was asked specific questions about the winglet’s technology, the OEM declined to respond.
Dunn also says API has designed a novel spiroid winglet with a continuous loop in place of a wingtip. Proof-of-concept flight testing was first carried out on a Gulfstream II in 1993, with an improved version tested on a Dassault Falcon 50 in 2010. So far, API has yet to certify or even offer this design commercially for any aircraft type.
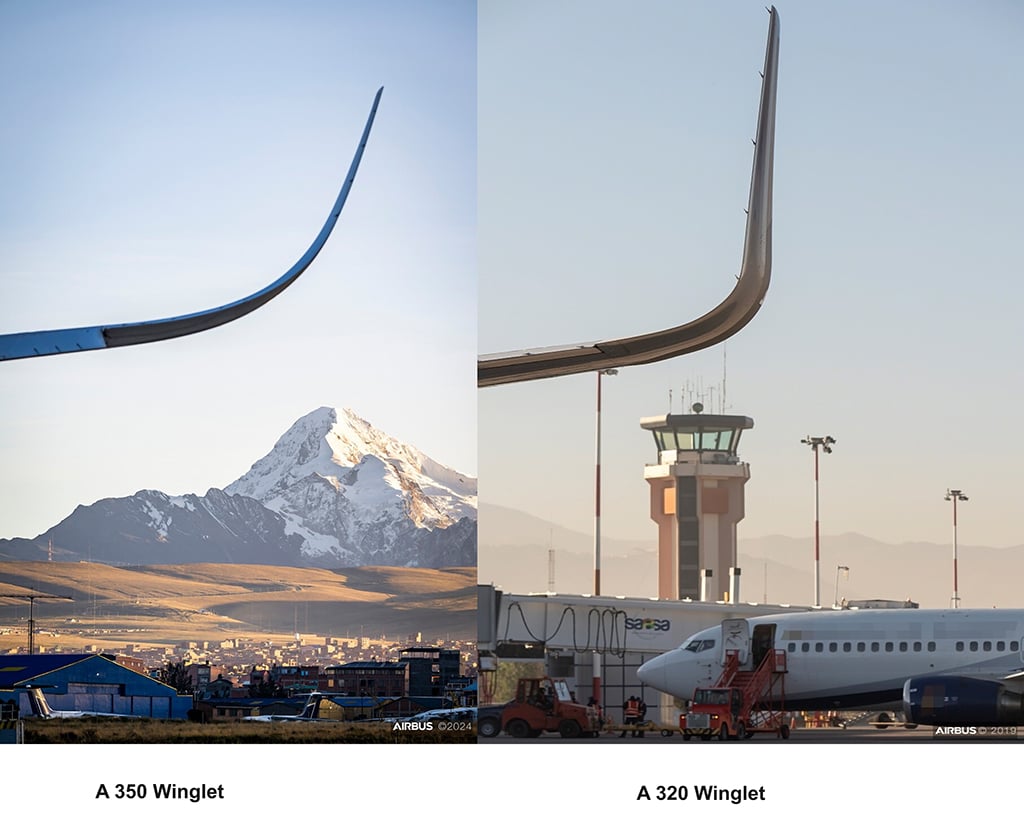
“The spiroid winglet is considered an ongoing program,” says Dunn. However, he stresses API’s continuing emphasis on the blended winglet. “That shape has been optimized for reducing tip vortices and provides the greatest drag reduction of any basic winglet shape. Adding an additional blade, as with our split scimitar winglet, can increase the drag reduction achieved while also minimizing any impact to wing stresses.”
According to Dunn, adding a scimitar tip to the blended winglet—effectively a raked extension to the end of the winglet—decreases the tip vortices coming off the winglet and further reduces drag. He reports that APB has certified the scimitar tip on the 757-200. “But the greatest efficiencies are achieved with our spiroid winglet device, as it essentially eliminates the wing tip,” he adds.
Dunn reports that blended winglets typically reduce drag by approximately 7% at long-range cruise, which can increase range and fuel savings. At higher cruise speeds, the benefit is lower—for example, 5% at Mach .80 for the Falcon family, including the 50, 900 and 2000 variants on which the API winglets are certified. “This also means a corresponding reduction in greenhouse gas emissions,” he says.
The numbers are even better with the scimitar blade tip extension and split scimitar designs, says Dunn. “On the Hawker 800 and 800XP series, we added a revised tip to the top of the existing blended winglet, which resulted in an additional approximately 0.5% drag reduction compared to the original design,” he says. “For the split scimitar winglet, now flying on almost 2,000 Boeing 737NGs, the addition of both a revised scimitar tip on the upper winglet and a new lower blade projecting below the wing . . . have improved the drag reduction of the original blended winglet by up to 2%. The spiroid winglet design demonstrated a drag reduction of approximately 10% in our first testing in the early 1990s; the improved version flown in 2010 saw a 12% benefit.
“Adding an additional blade, as with our split scimitar winglet, can increase the drag reduction achieved while also minimizing any impact to wing stresses,” he continues. “The addition of a scimitar tip to the blended winglet decreases the tip vortices coming off the winglet and results in yet more drag reduction. The greatest efficiencies are achieved with our spiroid winglet device, as it essentially eliminates the wing tip.”
Dunn says API and APB continue to run as separate companies, although the former’s winglet designs are common to both. He adds that API has done preliminary studies for winglet turboprop applications but does not currently offer a turboprop winglet.
Efficiency Gains
Meanwhile, Airbus has developed large, fully curved winglets for the A350 and A330neo, says Simon Galpin, head of aerodynamics at the OEM. For the A220, A330 and A340, the design incorporates planar winglets, while winglets with curved junctions at the wingtip are on the A320/A321. Airbus parlance terms the A320/A321 winglets as “sharklets.”
“In principle, all winglets are doing the same thing, which is providing an improved drag-to-weight balance for the overall aircraft,” Galpin says. “Each offers a slightly different balance according to the aircraft they are fitted to, its mission and other aerodynamic properties.”
Galpin reports that, on average, these winglets provide a 4% fuel efficiency gain, reducing emissions during flight. Other benefits include increased range, payload and better takeoff performance. “Winglets are standard equipment on all new A320 family aircraft in the narrowbody sector, but also on our widebody family as a fully integrated design on the A350 and A330neo,” he says.
Galpin says Airbus uses a range of metallic and composite technologies for its aerostructures, including the winglets. For example, he explains, the lighter-weight materials in Airbus-designed winglets include carbon-fiber-reinforced plastic (CFRP), which he says has “reached new proportions” on the A350. “With most of the A350 wing made from lightweight carbon composites, this contributes to less fuel burn, allowing airlines to fly further with less impact,” he says.
Asked about weight savings, Galpin says more modern CFRP types of winglets offer about a 10-20% reduction each compared with older winglets. However, he cautions that the overall weight balance for a winglet implementation also depends on whether the addition requires reinforcement of the wing structure.
“CFRP can offer a weight reduction opportunity compared to metallic structures,” he says. “Material choice is always a trade between performance, cost and other criteria. Further improved weight and new repair solutions are just two areas of interest as we investigate new materials alongside factors such as manufacturing process improvements.”
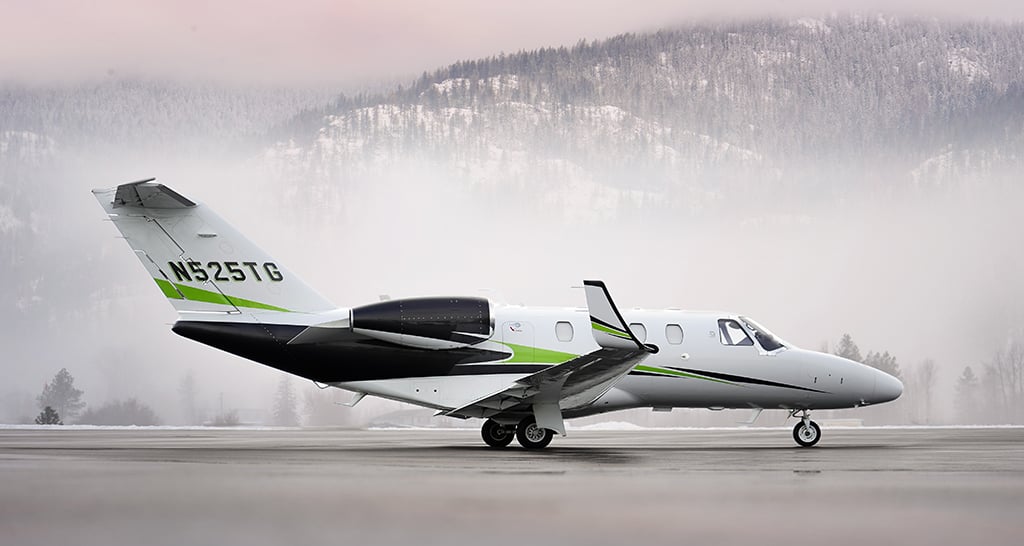
A revolutionary approach to winglet technology is currently certified on Textron’s CitationJet (CE 525) family. According to Tamarack Aerospace President Jacob Klinginsmith, his company’s active winglet system could find applications in the near future on narrowbody commercial jets such as the A320. In fact, the company has contract work in progress with the U.S. Air Force for application to an undisclosed larger aircraft, as well as a memorandum of understanding with a regional airline for installation on a De Havilland Canada Dash 8-Q400.
“Our sustainability white paper states that if our active winglet technology were deployed on the commercial narrowbody jet fleet alone, 1.6 billion tons of CO2 would be saved by 2040, reducing the emissions gap by approximately 20%,” Klinginsmith says.
Tamarack presented an active winglet solution for the A320 at the Colorado Cleantech Challenge in March. He is looking for partners to bring it to market. “This program aims to reduce airline emissions by 8–12%, saving about $1 million per year, per aircraft,” says Klinginsmith.
As its name implies, the Tamarack active winglet moves, unlike traditional static winglets. In addition to the composite winglet, the installed package includes Tamarack’s proprietary Atlas load alleviation system and 20-in. per wing extension. However, the wingtip extension and design will be aircraft model-specific to maximize performance improvement. Klinginsmith says the wingspan increase improves climb performance and reduces drag, resulting in range increases, fuel savings and higher cruising altitudes.
“Because these are active winglets, wing stresses are reduced, allowing us to certify an increased maximum zero fuel weight, which translates to higher payloads,” he says. “For example, on the Citation CE 525 Series, the upgrade has enabled an 800-lb. zero-fuel weight increase. At the same time, the active load alleviation component offers passengers a smoother ride because of active turbulence cancellation.”
Klinginsmith says the winglet is a Tamarack-patented carbon-fiber composite structure, while all other components are aluminum. “The Tamarack active camber surface (TACS)—the active portion of the upgrade—is fully autonomous and is located on each of the horizontal wing extensions, and moves the winglet at approximately 20 deg. trailing edge up, and 10 deg. trailing edge down,” he explains. “Both the left and right TACS move the winglets in unison to reduce wing bending in turbulence or a maneuver condition. Near 1g, the TACS are held in a neutral position, similar to how the ailerons are held in straight and level flight.”
Klinginsmith adds that through an algorithm that senses load factor on the aircraft, the TACS responds in less than 0.1 sec. to counteract increased wing loads using proprietary electric actuators. “This provides aerodynamic safety, stability and turbulence cancellation that passengers can actually feel,” he says.