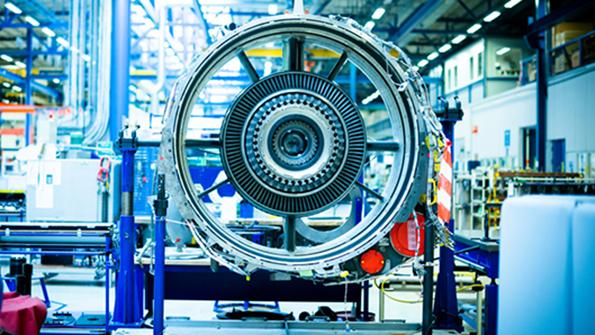
Stavanger-based CFM56 repair specialist Aero Norway is looking to become more proactive in its planning, especially in such areas as quick-turn engine repairs.
As global airline traffic numbers edge closer to 2019 levels, the engine aftermarket is enjoying an upward trajectory while facing undeniable obstacles. Demand for engine services is broadly recovering after a sluggish three years since the beginning of the pandemic. Yet engine MRO providers are struggling to accommodate airlines seeking engine maintenance work, such as full overhauls, life-limited parts repairs or less-intensive services, such as quick-turn and hospital shop work. Many engine MROs have reported shops at full capacity over the past year, motivating them to find ways to accommodate more shop visits.
This capacity shortfall is attributed to several factors, including the shortage of skilled labor, a continuing issue because of COVID-19. “The labor shortage remains a concern, specifically with regard to technicians, with MRO providers frequently finding themselves competing against airlines and other aerospace companies for experienced mechanics,” says Lewis Prebble, president of airlines and fleets at U.S.-headquartered StandardAero. Singapore-based ST Engineering has also seen this in its engine shop, says Tay Eng Guan, the company’s senior vice president and general manager of engine MRO. He cites skills shortages and supply chain constraints—another lingering legacy of the pandemic—as the biggest challenges facing the MRO provider today.
Supply Chain Constraints
MROs have sought ways to address supply chain constraints, which have challenged the industry during the past two years. More recently, ramp-ups by airframe manufacturers have seen their engine counterparts struggle to keep up with increased production targets. In turn, the aftermarket has been affected by longer lead times for engine repairs; some new-generation programs have seen lead times surpass more than 200 days in severe cases. “Parts supply remains a capacity constraint with every OEM, due to the recovery in aircraft utilization and the associated growth in MRO demand coming at the same time that engine OEMs are ramping up production to meet the needs of aircraft manufacturers,” Prebble notes.
Other factors resulting from extended turnaround times (TAT) are impacting engine MROs and operators alike. “One of the most notable challenges is the availability of rental engines due to the increase in TATs [itself primarily a consequence of parts shortages],” Prebble says. “Operators are tending to hold on to rental assets for longer periods than is traditional, which is in turn reducing the availability of such assets for customers attempting to avoid AOG [aircraft-on-ground] situations while waiting for their powerplants to be inducted.”
In the short term, acquiring slots for engine teardown and parts repair poses a challenge, which has led to Stavanger-based CFM56 repair specialist Aero Norway to become more proactive in its planning, especially in such areas as quick-turn repairs. “Ensuring a short turnaround time requires MROs to have all parts prepared in advance, as prolonged repair lead times could result in extended turnaround times,” says Jeremy Colin, global business development and marketing manager at Aero Norway. He notes that materials such as those for Evolution -7B engines are scarce but are experiencing growing demand while the company is reevaluating its parts-stocking strategies. “The lead time for part repairs is not diminishing, compelling the need for strategic planning or stockpiling of parts,” Colin says. “This approach ensures a viable solution for potential exchanges, subject to customer approval.”
Supply chain issues are also impacting Indonesia-based GMF AeroAsia. Company CEO Andi Fahrurrozi anticipates increased requirements for various engine materials and parts, with a specific focus on component piece parts and overhauled-condition components. “This heightened demand is likely to create a global shortage concern that could affect our supply chain management,” he says. “We anticipate that this trend will persist during the post-pandemic recovery period, which began in 2022 and is expected to continue for several years into the future.”
Supply and Demand
Like his contemporaries, Fahrurrozi highlights challenges related to skilled labor and rising costs as key challenges in its engine business. “The costs associated with materials used in aircraft engine maintenance, particularly those like titanium and aluminium, have shown a consistent upward trend in recent years,” he says, attributing these cost increases to macroeconomic factors and geopolitical events like the Russia-Ukraine war. In response, he says that the company has negotiated with suppliers to secure more favorable materials prices.
On a positive note, growing demand places the industry in a favorable position to navigate challenges relating to capacity. Much of the growth is expected to center on the narrowbody engine segment, notably CFM56-family and V2500 engines—options for Boeing 737 and Airbus A320 aircraft respectively, and some serious activity for turboprops is also anticipated. “We are expecting to see continued strong growth both in the turboprop segment—driven by the continuing recovery in Asia-Pacific and Europe—and in the CFM56-7B market, with the long-awaited bow wave in shop visits augmented by additional demand for Boeing 737NG aircraft as a fill-in for newer-generation aircraft affected by teething issues,” Prebble says.
Aero Norway foresees a steady rise in overhaul visits in the next few years for current-generation engines. Colin says the increasing number of CFM56-5B and -7B engines reaching maturity and undergoing their initial shop visit will drive this, a trend somewhat delayed by the impact of COVID-19. “We [Aero Norway] anticipate that the CFM56-5B market will mirror the pattern seen with the CFM56-7B, emerging as a highly sought-after asset,” he says. “This is attributed to challenges faced by other aircraft types, potentially prompting a contingency plan for the A320.”
Engine OEMs are relying on MROs in their networks to provide the extra capacity, particularly for the narrowbody engine segment—both for current and new-generation powerplants—the latter of which have seen first-time inductions by several maintenance specialists over the past few years. StandardAero has already started this process by adding more capability across its network, initially in the U.S. The company is due to establish CFM Leap-1A and Leap-1B MRO lines at its new facility in San Antonio, due to come online in February 2024. It is also adding additional CFM56-7B maintenance capabilities—including full engine testing—at its shop near Dallas-Fort Worth International Airport. Prebble says continuing demand for quick-turn services, which picked up significantly at the height of the pandemic as cash-conscious operators postponed shop visits, influenced the company’s decision to set up its CFM56-7B line in Dallas.
“The relatively long lead times currently experienced for induction slots has indeed driven interest in quick-turn services, and this is especially true in the case of older-generation engines, such as the CFM56 and V2500, due to operators seeking to extend the in-service lives of such types as the 737NG and A320ceo in order to cover for newer-generation aircraft facing unplanned maintenance work,” Prebble says.
Over the next few years Aero Norway plans to alter its current engine mix, a combination of CFM56-3 and -5B/-7B types, by progressively shifting toward a focus on CFM engines on 737NG aircraft. “This strategic move aims to create additional capacity for the mature engines in our portfolio,” Colin adds. However, he is realistic about the challenges facing engine maintenance specialists. “Despite our efforts to strategically plan ahead for materials and induction slots, the existing conditions at vendors and in the aftermarket may result in increased costs and longer lead times,” Colin says.
GMF AeroAsia has a mix of narrowbody and widebody engine MRO capabilities but is actively focusing on the CFM56 Leap variant. Fahrurrozi says this is a strategic decision partly influenced by the many MRO providers channeling efforts into expanding capacity for the Leap engine over the next few years. “Moreover, the requirement for service bulletin compliance, which mandates the replacement of CFM56-7B high-pressure turbine blades at 17,000 cycles in alignment with engine age, will further increase our available capacity,” he says.
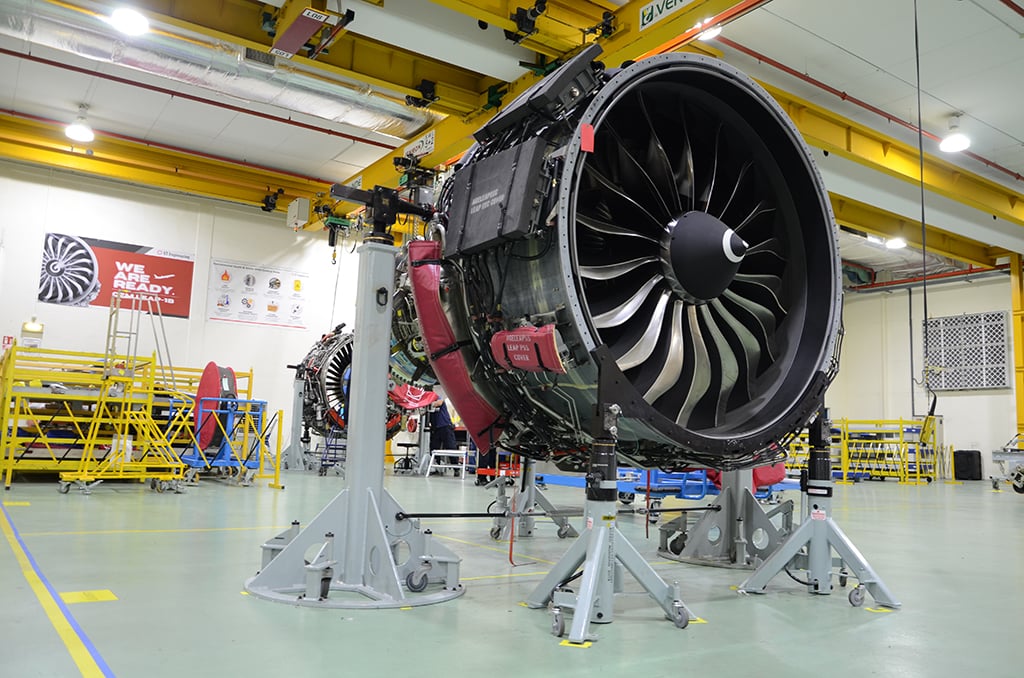
ST Engineering is another company adding capacity to service the wave of narrowbody current and new-generation engines. Last year, the company announced plans to expand engine capacity at its home base by enlarging shop floor and office space, along with additional warehousing facilities. It anticipates high volumes of engine shop visits for both CFM56 heavy maintenance and Leap engine quick-turn services in the next 1–2 years.
The MRO is also looking to add to its workforce by recruiting technicians locally and from overseas, including collaboration with technical institutes and universities. Technology investments to aid capacity are also being targeted. “We continue to invest in robotics and automation to perform the more repetitive tasks to maximize labor efficiency,” Tay adds.
Pratt & Whitney’s PW1000G geared turbofan (GTF) program, currently undergoing fixes mandated by regulators and agreed to by the OEM, will see about 350 engines grounded annually from last year through to 2026 and is also expected to feed near-term capacity. Iberia Maintenance, which acquired GTF approval in 2022, says that the groundings will take up a lot of its near-term capacity. “It is a new engine, and we are building a separate workflow for it,” Enrique Robledo, chief technical officer of Iberia Maintenance, told Aviation Week in September 2023 about its GTF plans. “We have designated capacity isolated for it, so the capacity of the GTF won’t influence the rest of the shop.” Meanwhile, providers are also allocating capacity for its predecessor, the V2500—about 30% of its engine fleet has yet to undergo initial shop visits.