Engine-Makers Wrestle With Production, Durability Issues As Market Rebounds

Certification tests of the GE Aerospace GE9X-powered Boeing 777-9 are expected to begin in early 2024.
With yet another bruising year in the rearview mirror, commercial engine-makers are hoping for better things in 2024 as supply chain pressures slowly ease and production continues to catch up with surging demand from aircraft manufacturers.
The coming year marks the start of a new era for GE Aerospace, which is expected to be spun off as a stand-alone entity from General Electric at the start of the second quarter. Underpinned by the steady success of its GEnx-1B on the Boeing 787 and ongoing sales of the Leap 1 through its CFM International joint venture with Safran, the engine-maker appears to be in a solid position as it enters this new phase.
- GE Aerospace prepares for spin-off
- Pratt focuses on GTF damage control
- Rolls searches for UltraFan partners
Through the end of the third quarter of 2023, GE had seen orders for 2,333 commercial engines, of which 1,445 were Leap 1s. These healthy numbers were bolstered by a busy Dubai Airshow in November with additional orders for 240 Leaps, 12 GEnx-1Bs and 202 GE9X engines.
Designed for the Boeing 777X, the GE9X remains a key focus for the two manufacturers as the big twinjet enters long-deferred certification flight testing in 2024. Although GE has long since solved a compressor second-stage variable vane durability issue that delayed the program in 2019, the subsequent holdup to 777X certification has given it breathing room to correct a combustor liner problem that temporarily halted 777-9 flight tests in November 2022.
Stan Deal, president of Boeing Commercial Airplanes, says the liner issue is one that “GE Aerospace has got well in hand.” The bulk of the certification effort will be performed by Boeing’s third 777-9 test aircraft, WH003, which originally joined the program in August 2020. The aircraft will be configured with the production-standard GE9X engine with an updated combustor liner and has until now been used primarily to evaluate flight loads and performance of the auxiliary power unit, avionics and GE9X engines.
Overall, GE remains broadly optimistic, Chairman and CEO Larry Culp says. “The widebody market is in a much better place than it was just a few years ago,” he told Aviation Week in June. “We’re on the cusp of no longer talking about where we are vis-a-vis 2019 departure levels. I suspect as we go through the back half of this year and certainly into 2024, we’ll be free of that unfortunate history and just talk about this business growing. Our view is that this industry is poised to grow, even with some of the macro pressures that are weighing on other sectors.”
Meanwhile, CFM’s three-year struggle to overcome sometimes debilitating supply chain problems is nearing an inflection point as it steers a course to return to pre-pandemic levels of engine output in 2025. Together with its position of exclusive engine supplier for the Boeing 737 with the Leap 1B and majority provider to Airbus for the A320neo with the Leap 1A, CFM is gearing up capacity to produce around 230 Leap engines per month in 2025 to keep pace with expected demand.
In addition, CFM plans to introduce upgraded components into the Leap 1 in 2024 to improve the engine’s durability and time on wing, in some cases particularly for Middle East and Asian operators. These include a redesigned starter air valve for the Leap 1A and a revised wear couple housing around the No. 3 bearing in both the Leap 1A and B to counter a nonsynchronous vibration (NSV) that has caused high-pressure compressor stalls in extreme cases.
Other fixes to be introduced in 2024 include an anti-coking reverse bleed system and a redesigned high-pressure turbine blade and nozzle designed to better withstand dusty and polluted environments in which Leap 1s with the current turbine configuration have experienced premature removals.
CFM has been working with Airbus on a lower thrust rating for climb power on the Leap 1A. Described as an “optimized climb thrust” setting, the initiative manages the climb thrust ratings of the engine in order to help minimize the temperature experienced by the core. The revised thrust rating will also be introduced in 2024.
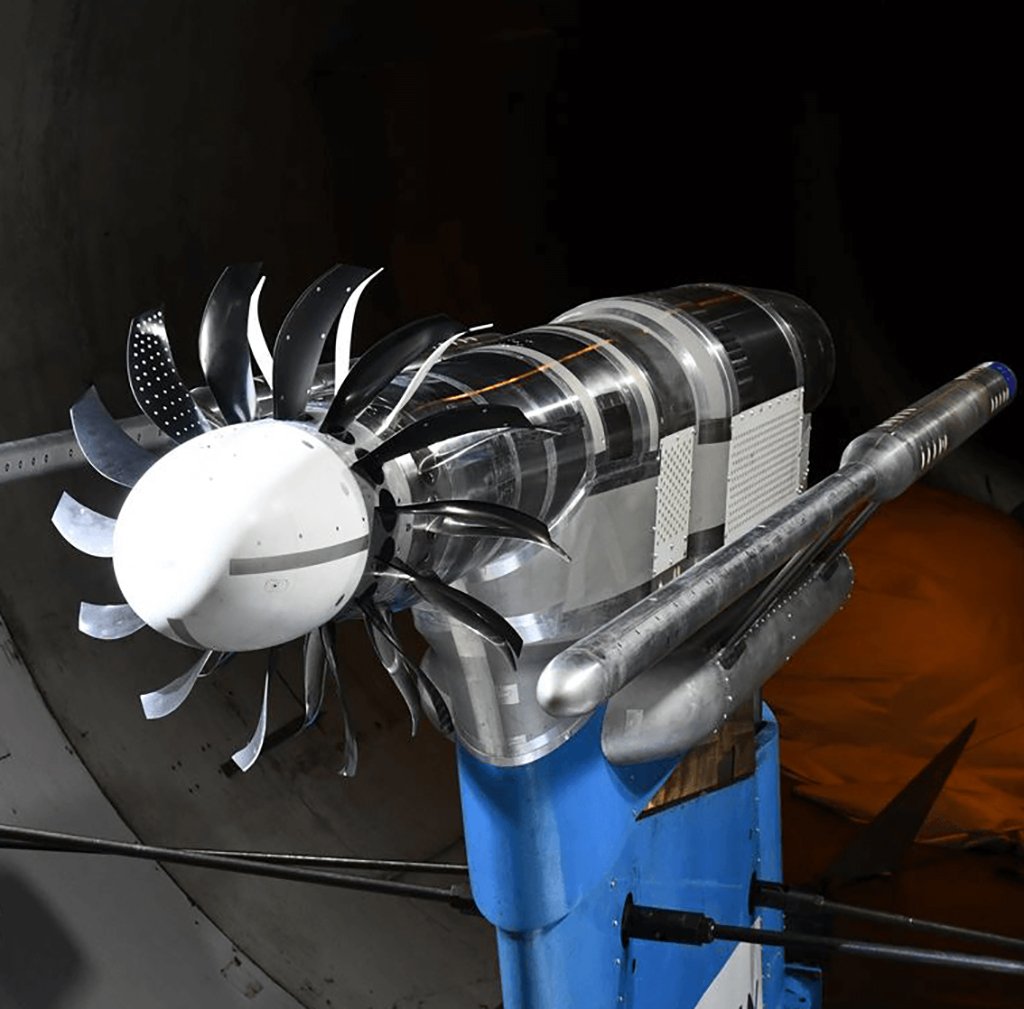
Looking to the next-generation engine, CFM has completed the conceptual design review for the RISE (Revolutionary Innovation for Sustainable Engines) open-fan propulsion system, which is targeting a 20% improvement in fuel efficiency compared with its current Leap 1 turbofan.
“We are starting to cut metal to produce parts with the goal of running a demonstrator and perform flight tests later in this decade,” says CFM CEO Gael Meheust. More than 100 tests have been carried out as part of a technology maturation phase, and over 1,000 engineers are now engaged in the design of the demonstrator. “We are learning a lot and are pleased with the results we are achieving,” Meheust says.
Besides a 13-ft.-dia. open fan, the demonstrator will also include a high-power gear system and a new compact high-pressure core to boost thermodynamic efficiency. The initial fan set will be tested with a modified GE Passport business jet engine as the gas generator.
The RISE program will also include a recuperating system to preheat combustion air with waste heat from the exhaust as well as the application of advanced materials such as ceramic matrix composites in the hot section and resin-transfer-molded composite fan blades. Initial evaluations of the first rotating components of RISE began this year when tests of the first full high-speed low-pressure turbine stage began at GE’s Evendale, Ohio, facility using an F110 military donor engine (a military engine used for civil development). Supercomputers are helping to test the design of the high-pressure turbine blades and nozzles.
CFM’s RISE program includes hybrid-electric and hydrogen studies, too, putting it “on track to be the first company to introduce hybrid electric in the single-aisle segment,” the company says. Tests conducted recently at NASA’s Electric Aircraft Testbed facility in Sandusky, Ohio, as part of the agency’s Electrified Powertrain Flight Demonstration project have already validated GE’s hybrid-electric propulsion system architecture approach and pave the way toward mildly hybridized turbofans—in which the hybrid element provides only a small share of the overall power generation—as part of the RISE program.
Under an agreement signed in February 2022, Airbus and CFM also plan to flight-test a GE Passport engine modified for direct combustion of hydrogen fuel. The tests, scheduled for around 2026, are part of the RISE effort and are intended to prove technology for entry into service for the first of several generations of planned Airbus zero-emission aircraft by 2035.
For 2024, Pratt & Whitney’s focus remains centered on damage control over the troubled PW1000G geared turbofan while simultaneously supporting increasing production rates at Airbus and Embraer. The engine-maker’s problems grew during 2023 with the revelation that long-running issues with contaminated powder metal were worse than previously feared and will significantly increase mandated removals and inspections.
Most of the unscheduled removals for the PW1100G version powering the A320neo will take place by mid-2024, Pratt says. In September 2023, the manufacturer revealed that 600-700 engines will need to come off wing for unscheduled inspections by 2026—on top of another 500 already scheduled for overhauls. Given ongoing shop capacity limitations and parts shortages, operators have been warned that wing-to-wing turnaround times could take up to 300 days. This will inevitably lead to extensive groundings, which Pratt says will peak in 2024 but in some cases extend through 2026.
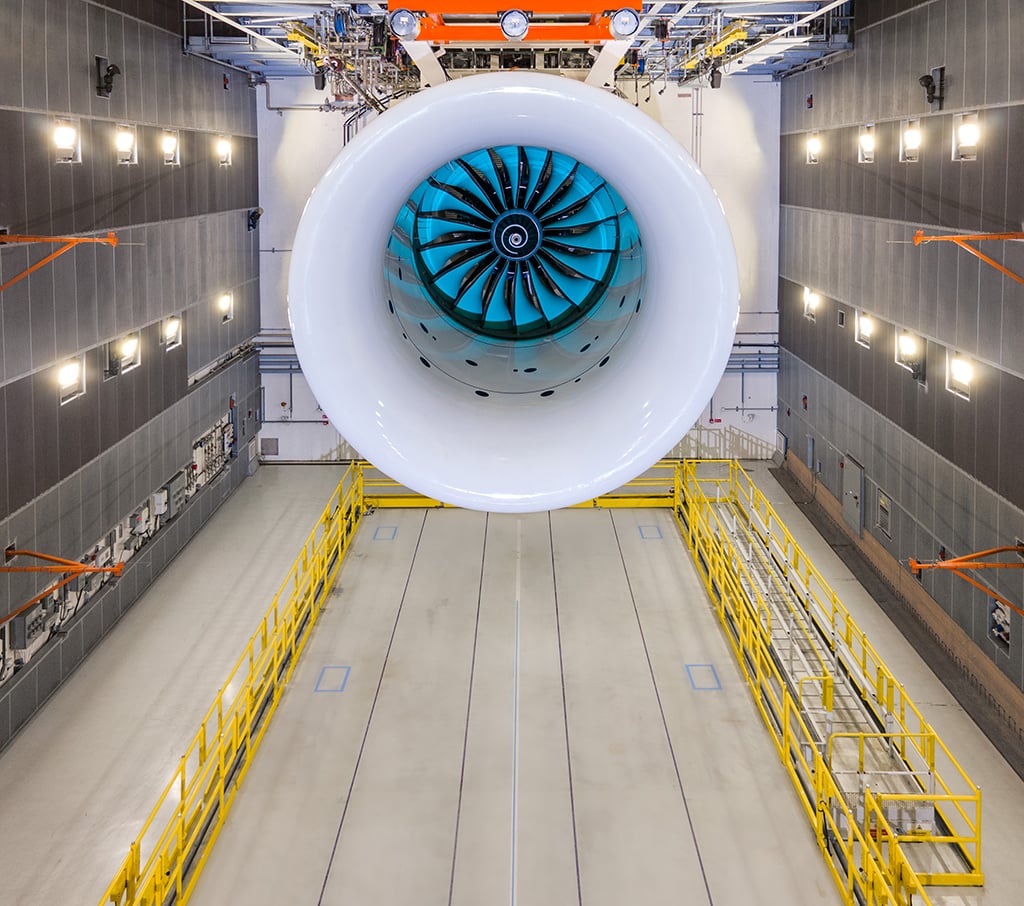
The smaller fleets of PW1500G-powered A220s and PW1900G-powered Embraer E2s are less affected, and in October the manufacturer said most inspections required for these fleets will largely fall within scheduled intervals. At the time, Aviation Week Tracked Aircraft Utilization data showed about 350 grounded PW1100G-powered A320neos—25% of the fleet.
Upgrades to improve the baseline durability of the PW1000G are also in the works for introduction in 2024. This will include upgrades to airfoil coatings, hot-section cooling and air seals. The oil system part of the upgrade is also being introduced on the PW1500G/PW1900G. A follow-on upgrade package planned for 2025 will add further improvements to airfoil coatings as well as hot-section durability upgrades.
Looking beyond the current GTF issues, Pratt continues to invest in further PW1000G developments to maximize the fuel-burn benefits of the geared architecture without suffering the durability problems the initial versions have experienced. The GTF Advantage, currently in testing, is the first upgraded version and is rated at up to 34,000 lb. thrust. Planned to debut in 2024, the variant incorporates material, design and airflow upgrades in the low- and high-pressure spools.
The Advantage is designed for a 4% thrust improvement at sea level and up to 8% at higher elevations, all without increasing operating temperatures. The engine, which is interchangeable on wing with existing PW1100Gs, will become the new production standard over a two-year transition period starting in 2024.
The coming year will also see Pratt & Whitney working more with Boeing on the early design stages of fitting the PW1100G to the slender wing of the X-66A transonic truss-braced wing aircraft for NASA’s sustainable flight demonstrator program. Although the aircraft—based on a converted MD-90—is only a technology demonstrator and not due to fly until late 2023, the X-66A could eventually pave the way for a 737 successor. Pratt sees its selection as a possible strategic opening into the future Boeing single-aisle market.
“We would love to find a way to get back in,” says Christopher Calio, RTX president and chief operating officer. “Our view [is that the X-66A] is a great way to get back in working with Boeing in the commercial engine space in the commercial narrowbody market,” he adds. But Calio is realistic about Pratt’s immediate priorities. “The focus right now is on getting through our issues on the GTF for Airbus and our customers. So make no mistake, we are not taking our eye off that ball, but longer-term—in 12-15 years—you’ve got to invest. You can’t just wake up in 2030 and go, ‘Hey, we’d love to get back on the Boeing aircraft.’ You have got to be investing along the way in some of these enabling technologies.”
Of the “big three” engine-makers, it is the immediate future of Rolls-Royce that will attract the broadest interest in 2024 as the UK-based manufacturer begins a radical restructuring under plans outlined in late November by CEO Tufan Erginbilgic.
Targeting a fourfold increase in annual operating profits to $3.5 billion by 2027, the strategic reset aims to continue the engine-maker’s recovery from several years of losses—particularly in its large commercial engine business—following the COVID-19 pandemic and durability problems on the Trent 1000. Key elements include divesting noncore assets and streamlining operations to cut costs while improving widebody long-term service agreement margins by extending time on wing, lowering shop visit costs, reducing product costs and tightening up contractual terms and conditions.
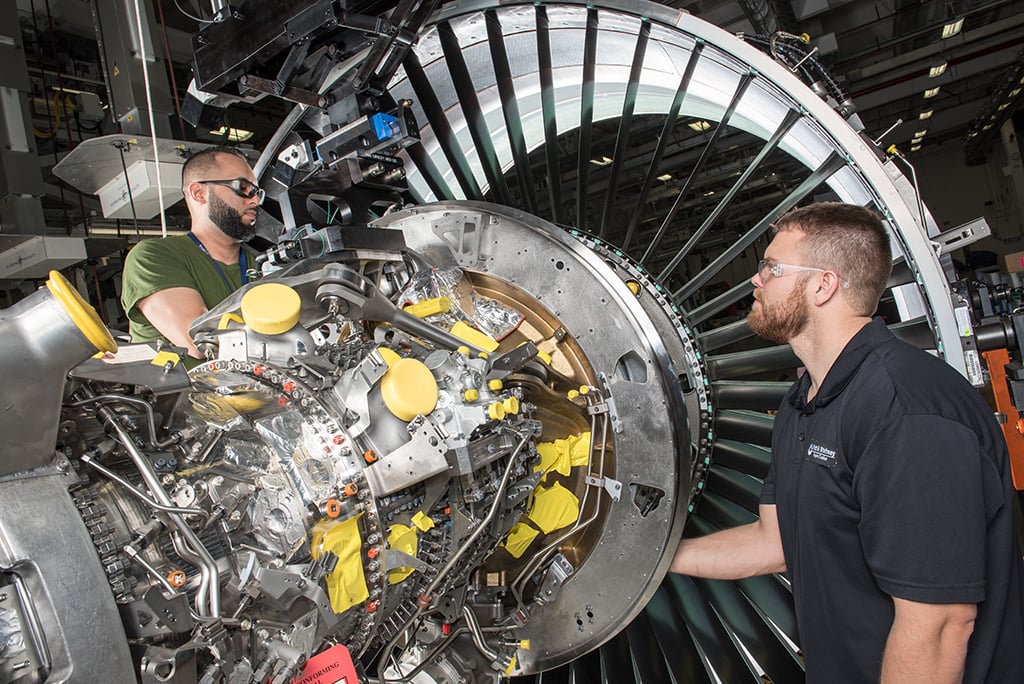
Two major features of Rolls’ transformation plan include selling off the company’s recently established electrical propulsion unit and beginning the search for partners to reenter the single-aisle market with a smaller variant of the UltraFan.
The Rolls-Royce Electrical sale is part of a raft of divestitures that aim to raise up to $1.5 billion and have been considered likely since February 2023, when Erginbilgic announced the start of a company-wide strategic review. The decision comes as the unit enters a key phase of tests on a range of electric motors, batteries and a gas turbine turbogenerator core, which are in development for a range of all-electric and hybrid-electric advanced air mobility vehicles.
Rolls-Royce’s proposed single-aisle market gambit with the UltraFan engine comes 12 years after it exited the lucrative sector by selling its share in International Aero Engines to Pratt & Whitney for $1.5 billion. It remains unclear which potential partners Rolls could team with on a smaller-scale UltraFan, although potential candidates include Tier 1 companies such as GKN Aerospace, ITP Aero and possibly members of the Japanese Aero Engine Corp.
Meanwhile, tests continue with the full-size demonstrator, which ran at 85,000 lb. thrust in November—a power level higher than originally designed and the highest thrust ever achieved with a gear-driven turbofan. Although Rolls has consistently outlined its intent to offer scaled versions of the new design across a potential thrust range of 25,000-110,000 lb., its focus to date has remained on demonstrating the engine at a larger scale more suitable for widebodies.
The pivot to focus on the single-aisle market reflects the increasing likelihood of new product launches in this sector in the late 2020s, and the reality that, barring reengining of the A350 and 787 toward the end of the decade, no new widebody applications are likely in the near term. Spinoff technology from the UltraFan is, however, at the heart of plans to upgrade the Trent 1000 and XWB families.
Plans to upgrade the latter engine—particularly the XWB-97 version— could be accelerated in 2024, following stinging criticism from Emirates Airline President Tim Clark, who cited durability problems with the powerplant as the airline’s reason to defer possible orders for the XWB-powered A350-1000. Rolls meanwhile continues to enjoy its position as the exclusive engine provider for the A350 family, orders for which are now nearing the 1,100 mark.
Rolls’ hopes of reenergizing both its market share on the 787 and its recently strained relations with Boeing have been boosted by the start of certification testing of an upgraded high-pressure turbine blade configuration on the Rolls-Royce Trent 1000 TEN version. The tests mark a key step toward finalizing a package of fixes developed by the engine maker to correct long-running corrosion and fatigue issues on the 787 powerplant.
For Rolls, the FAA certification campaign for the high-pressure turbine blade change for the Trent 1000 TEN marks the last major stage of a long and expensive recovery from problems that will have cost the company an estimated £2.3 billion ($2.9 billion) in 2017-23. The engine-maker also sees the effort as a critical milestone in its campaign to rebuild bridges with Boeing and operators of 787s powered by Trent engines.
The same basic engine fix has already been certified by the European Union Aviation Safety Agency (EASA) on the Trent 7000, the almost-identical Rolls engine variant to the Trent 1000 TEN powering the Airbus A330neo. The upgraded engine was approved by EASA at the aircraft level in August 2022, enabling the new-build standard to enter service shortly afterward with Kuwait Airways, the initial operator.
Supersonic airliner developer Boom meanwhile completed its conceptual design review of the purpose-developed Symphony propulsion system in advance of initial hardware rig tests planned for 2024. The new centerline engine will power its Overture Mach 1.7 airliner and is under development by a Boom-led team including Kratos subsidiary Florida Turbine Technologies, GE Additive and Standard-Aero. The two-spool, 35,000-lb.-thrust, medium-bypass turbofan engine is configured with a single-stage 72-in.-dia. fan and optimized for prolonged supersonic operation with an air-cooled, single-stage, high-pressure turbine and a three-stage low-pressure turbine.