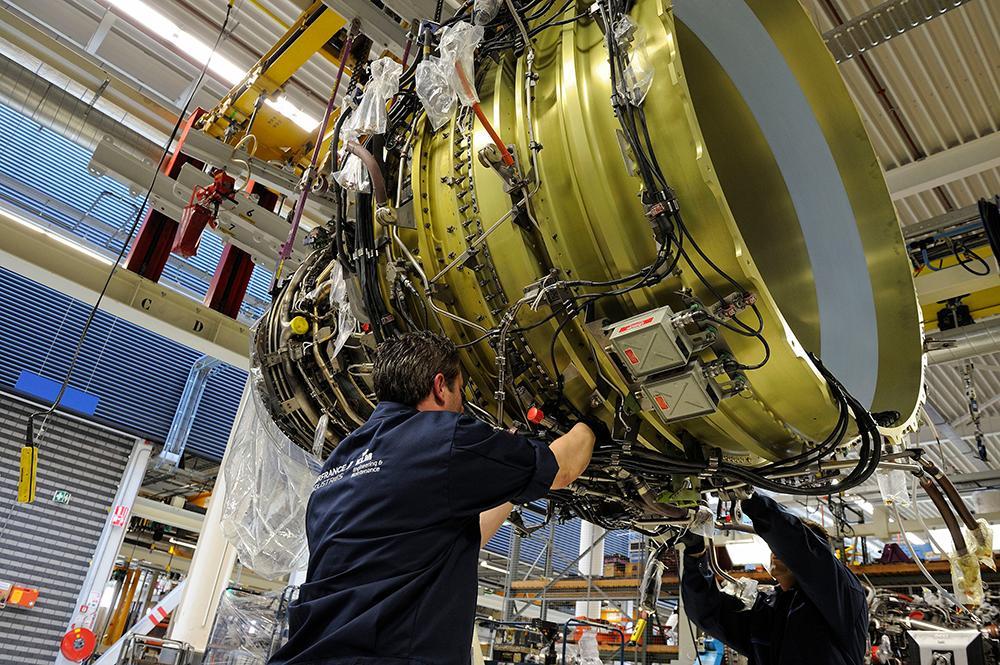
AMSTERDAM—Air France Industries KLM Engineering & Maintenance cites factors such as new engine durability issues and extended lead times for parts as some of the biggest stress factors in today’s engine aftermarket supply chain.
Speaking at Aviation Week’s Aero-Engines Europe conference on Sept. 10, leaders from both the French and Dutch parts of the engine MRO business of Air France Industries KLM Engineering & Maintenance (AFI KLM E&M) shared some of the major challenges the airline MRO is dealing with in 2024.
Ton Dortmans, executive vice president of Amsterdam-based KLM Engineering & Maintenance, says the balance of supply and demand is among the foremost issues, with lead times still longer than expected due to parts supply problems stretching across several divisions of its repair business.
He cites recent examples of this as a five-day waiting time for a thrust reverse bumper on a Boeing 777 and a heat blanket for a 737 resulting in a lead time of seven days for parts. “That's incredible, and it means that the aircraft are on the ground,” he says of the extended lead times. “We have to overcome the supply chain challenge because it has an enormous impact,” Dortmans adds, referring to workforce shortfalls due to personnel lost during COVID and a scarcity of raw materials as other factors contributing to the industry’s supply chain imbalances.
As part of AFI KLM E&M, the company’s engine business services GE Aerospace’s GEnx, General Electric CF6 and CFM International CFM56-7B and Leap 1A and 1B engines from Amsterdam. In Paris, it services GE90, Rolls-Royce XWB, CFM56-5B, Leap 1A and 1B and Pratt & Whitney Geared Turbofan (GTF) engines.
As well as increasing passenger flying volumes leading to higher maintenance demand, the industry is also battling issues related to new-generation engine durability resulting in sooner than expected shop visits, says Martijn de Vries, vice president at KLM Engine Services. “There's a slot constraint, because the new engines coming in do not yet perform at the anticipated reliability, partly due to the new materials,” he says. “This constraint is one of the biggest challenges.”
Jean-Louis Forest, senior vice president for engine services at Paris-based Air France Industries, says it favors open maintenance networks when working with OEMs as it sees them being a way of driving innovation, change and adding capacity. AFI KLM E&M also sees developing new engine repairs as a long-term solution to combating rising maintenance costs. “Maintenance costs have to go down. Everybody's saying inventions, of course, will deliver less fuel, that's for sure, but in general, the maintenance costs are going up,” Dortmans adds.
With the cost question in mind, the MRO provider also does not rule out increasing its attention towards PMA parts. “It's linked to the availability of material and the cost of material,” Forrest says. “As an airline, we have to decrease the cost. What kind of an equilibrium can we find with the cost? If the catalogue of OEM parts is increasing too high, then at some point there will be PMA and DER repairs, because it's just a fact of the market.”
De Vries also cites access to skilled labor such as mechanics and engineers, particularly for younger generations, as another primary long-term concern. “Are we as an industry interesting for the new generation? Are they the same, or are they different?” he asks. “They [young people] learn differently. They switch quicker and don't want to stay in one job for the rest of their lives. They are interested in different, new stuff, which is interesting, but can we support it?” he ponders. “We need to attract them, train them and make sure that they get the positions to help us to make this industry interesting and profitable in the long term.”
Technology is seen by de Vries as a route toward attracting new talent into the industry, demonstrated by the company’s own investments in this area. “We have new techniques. We have digital solutions. We make use of artificial intelligence. There's huge investments in automatic inspections, laser stuff, predictive maintenance [and] prescriptive maintenance,” he says.