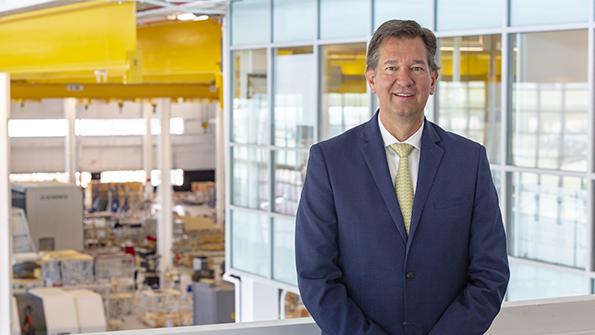
Don Mitacek is Delta TechOps senior vice president and president of Delta Technical Services Group.
Don Mitacek, Delta TechOps senior vice president and president of Delta Technical Services Group, speaks with Lee Ann Shay about when new-generation engine teething pains will end and how Delta’s new engine shops are dealing with supply chain issues.
Delta Tech Ops has invested a lot in new engine capability. What’s the breakdown between work for Delta and for others? This year, we’ll do about 55% third-party and 45% for Delta.
Is it fair to say engine MRO generates a bigger part of Delta TechOps’ overall work? If you’re talking dollars, engines and component MRO makes up the vast amount of our budget. Engines probably account for 55-60%, components about 20% and airframe the rest.
What engine work is coming into your shops? With the geared turbofan (GTF) and Leap having teething problems, how is this affecting your engine shop work? All new engines go through some type of teething problem. We’ve heard a lot in the news lately about the GTF issues. We work very closely with Pratt & Whitney, which has resolved a lot of the introduction issues. But that said, we’ve got a few more we’re working on, and I think they have a really good line of sight on solving those. They are not unlike other teething problems on other new platforms. It’s just things you work through, but I think when you take a step back, specifically talking about the GTF, it’s a really good engine. It’s really quiet and very efficient. When we get past these issues, I think it’s just going to be a stellar engine.
So you don’t have a concern about this next generation of engines? Engines like the CFM56 set the reliability bar very high. The CFM is a great engine, but I can remember when it had teething problems. I’ve seen this in too many new engine platforms, so I don’t think it’s anything to be overly alarmed about. The vast majority of the issues are resolved, and we’re working on the tail end of where I think the engine is going to stabilize and be really good.
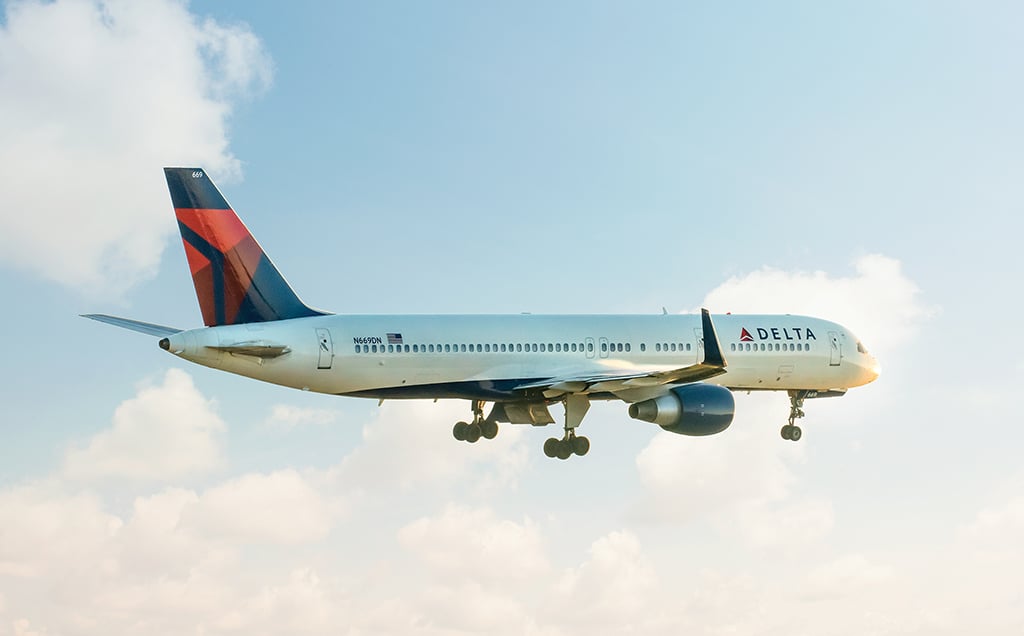
When do you think Pratt will reach that stabilization point for the GTF? Pratt has more concerns about engines running in challenging environments. I don’t want to speak for them, but given what we’ve been working with Pratt on, the remaining issues should be resolved in early 2024. There have been a lot of reliability challenges that it has already resolved.
The GTF shop just opened in February. How is it operating so far? It’s going really well. We’ve been doing that engine for about 18-20 months already. We industrialized the [PW]1100 first, which powers the A321. Delta wasn’t flying that engine when we industrialized it, so this was sheer MRO volume. The new shop is very lean and includes 5S [pillars].
When will Delta get its first Boeing 737 MAX 10s and the CFM Leap 1B capability? The plane isn’t certified yet, but it’s looking like we’ll get it in early 2025. We will bring in Leap capabilities sooner than that. If things go reasonably well, we should start industrializing the Leap late this year or early next year.
How is the Rolls-Royce shop and test cell performing? Exceptionally. It was a really good investment, and I think Rolls—and certainly Delta—is proud we did it. We’re very good partners. We crammed a bit of the GTF shop into the Rolls-Royce shop because the GTF shop got a bit delayed during [the pandemic], so when the GTF shop opened in February we were really pleased to get the Rolls-Royce shop back. We industrialized every new platform of the Trent engine—the XWB, Trent 1000 and Trent 7000. The TechOps team has just done an over-the-top great job.
Is that shop sold out, or do you have available capacity? We’re doing about 80 engines per year. We’re basically at capacity for phase one of the Trent shop. We’re working up to 150 or 180 in phase two. Now we’re working on getting the tooling and people to ramp up to that second phase.
When do you hope to implement Phase 2 of the Rolls shop? We probably won’t be at the full capacity until about 2024, but we’re implementing Phase 2 now.
Supply chain shortages are prevalent. How are you dealing with parts shortages? Are you seeing any longer turnaround times for MRO as a result? Our engine turn times—across the board, and it doesn’t matter which platform—haven’t gone back to 2019 turn times because of all these supply chain problems. Early during [the pandemic], we saw it on the repair side because people weren’t there to repair parts. It was a people issue. That has gotten better, but the new-part side of it got worse because we kind of lived off the inventory on the shelf. And I don’t think any of the suppliers recognized that the industry would heat up so quickly. I thought things were getting much better right before the [2022 winter] holidays, but since then, we’ve not been doing as well. Unfortunately, it’s a vicious cycle of sorts because we put more of the key parts into the repair process to try to buffer a lot of those key bits that we need in the engine. The problem now is that there is literally no buffer material available. So [work-in-progress] in our shops is way up because a lot of the parts we need are actually in the engines. It’s starting to get better. A lot of suppliers thought things would be getting somewhat back to normal in mid-2023, but I don’t see any real silver bullet that suggests “normal”—what I would consider the 2019 level. It’s going to be another challenging year.
To mitigate this, are you trying to develop more repairs and seek more used serviceable material? Teardowns have been slower than predicted. Our strategy for years has been to assertively develop new repairs. We have done an incredible job developing high-tech repairs for hot sections, fan blades and similar parts. Then we have Delta Material Services, which is good at finding used material, including green-time assets. We’ll also buy an entire airplane and part it out if the green-time assets are worth it. Given that OEMs, including Airbus and Boeing, are behind on delivering airplanes, we feel the crunch. Airplanes we would have considered retiring in the past we simply can’t because the new deliveries are so far behind schedule. I suspect that when Airbus and Boeing catch up—and they will—there will be more assets available.
In Delta’s 2022 full-year results, the aircraft maintenance material and outside repairs were 13% higher than the previous year. Other airlines reported higher figures, too. What are you anticipating for this year? Our numbers are not going to be very clean for a little bit, and let me explain why. During [the pandemic], we borrowed a lot of engines and components from grounded airplanes to conserve cash. This resulted in a big maintenance burden for 2021, 2022 and 2023. But one of our big strategies is to use used serviceable material instead of new. It’s a major strategy for us to develop new repairs and to be able to aggressively go out in the marketplace and look for used material. We’re good at that. And I think the Delta team—better than anybody that I’ve worked with—is really good at sunsetting fleets. We sunsetted the MD-88 and the MD-90s in such a fashion that we got to use the assets for as long as possible—right down to that very last airplane, the last engine. We work with our network team and have a systematic process for retiring airplanes.
This year, we’re still rebuilding some airplanes. We’re going to bring [Boeing] 717s and 757s out of storage, so our costs will be a little bit artificially increased this year, because it’s not status quo, i.e., “regular” maintenance.
How many 717s and 757s? The number keeps moving around. If we can build enough engines, there will be 18-22 717s. We’d like to bring back nine more 757s. But again, all those airplanes need engines and airframe checks, so it’s not as simple as taking the covers off the wheels. They need quite a bit of maintenance.
Will Delta do all that maintenance?
We’ll build the engines, and if it’s a lighter C check, we’ll fly the aircraft to Minneapolis or Atlanta for the check, but if it’s a heavier check, we’ll probably send it to one of our partners.
Who are your major airframe MRO suppliers? We work a lot with MRO Holdings, AAR and ST Engineering.
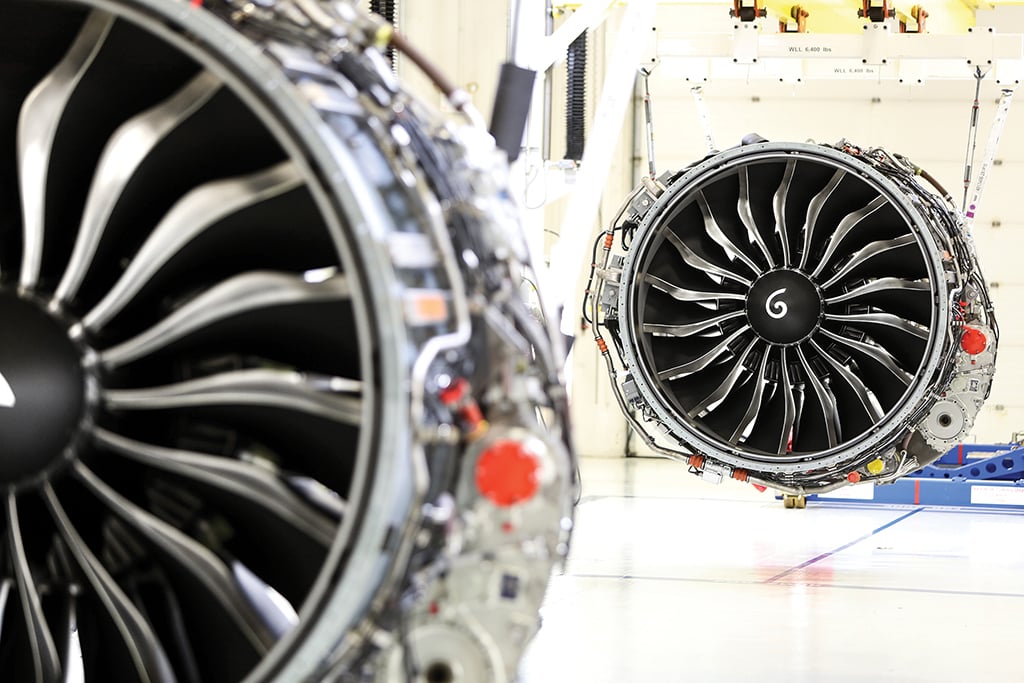
Speaking of MRO holdings, you are the chairman of TechOps MX. How’s that joint venture going?
Aeromexico and Delta each own 50% of the joint venture, and MRO Holdings manages it. We used to manage it on our own, but we think there are better synergies by having MRO Holdings manage it. The facility’s quality is really good, and the costs are favorable.
Delta and Joby Aviation plan to launch electric vertical-takeoff-and-landing (eVTOL) home-to-airport transportation service from selected airports. What involvement will TechOps have with Joby for eVTOL maintenance? Discussions are at a fairly high level right now, but it’s across all of Delta—including our safety group, our reliability group, our maintenance group. We’re just starting to put the group together, so there’s not a lot of activity yet, but once the team forms, I’m sure it will ratchet up.
Delta has trialed different technologies, including aircraft structure-monitoring sensors (SMS) and drag reduction. Are there other new technologies you’re evaluating? There is not a ton of new stuff because COVID-19 really slowed everybody down. We have an ongoing implementation of the SMS comparative vacuum-monitoring sensors on the aft pressure bulkhead of the 737-800. So far, 23 of 77 aircraft have these sensors installed. Instead of taking the whole back of the airplane apart to complete an inspection, the sensors enable us to inspect for cracking without the need to remove galleys or other monuments to access the inspection area. This significantly reduces aircraft out-of-service time and enables us to provide more aircraft back to our network by reducing special scheduling that is typically required to accomplish the manual inspection method.
We’ve never stopped working on predictive maintenance. We have a joint venture with Airbus and GE Digital. We’re still working the drone idea for inspections. The drone moving around the airplane is the easy part. What we’ve been very focused on is building up the data and the AI so that the drone knows the difference between a grease mark and a lightning strike. The team has been really progressing well, and there’s a good chance we’ll get something in front of the FAA this year that will help us inspect aircraft with a drone.