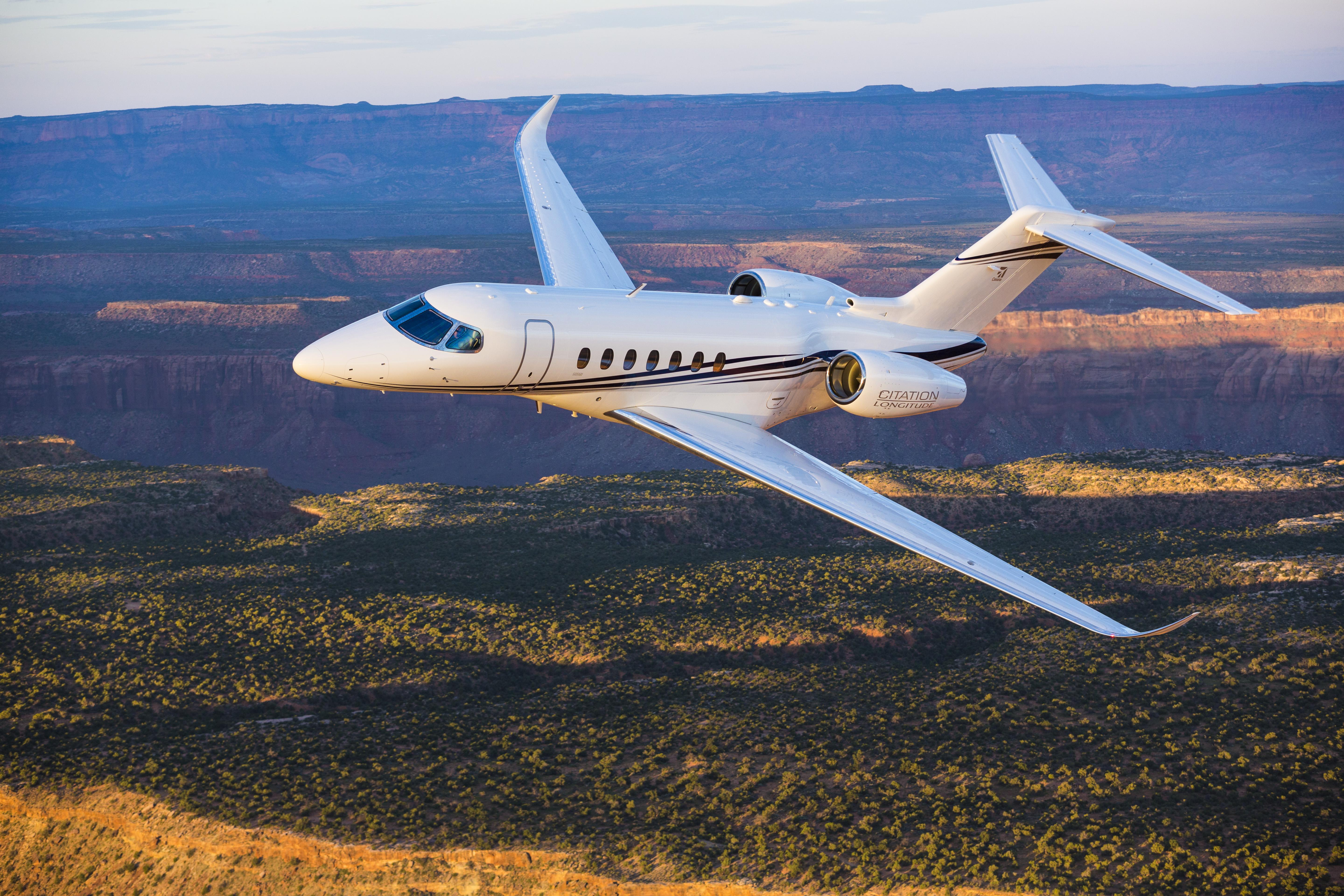
We were cleared for takeoff on Runway 01R at Dwight D. Eisenhower National Airport (KICT) and the Citation Longitude’s FADEC-controlled engines allowed me to simply push the throttles full forward. Hitting the Takeoff/Go Around (TO/GA) buttons earlier armed the autothrottles, which took over after I pushed them full forward. The engines responded quickly to takeoff thrust. Keeping the aircraft aligned with the runway centerline was simply a matter of steering with my feet and each V-speed came quickly. Our V1, decision speed was 107 kt., rotation speed was 113 kt., and V2, takeoff safety speed was 125 kt. As with many over-powered aircraft, these speeds seem to be of little consequence with all engines operating: They come and go very quickly.
A gentle pull to what looked to be around 10 deg. of pitch allowed us to alight gently and we were airborne. Pull forces were not substantial and it was easy to bring the nose up without over-rotating. If there was any pitch change due to flap retraction, I didn’t notice it; I was too busy adding nose-down trim to compensate for our rapid acceleration. The flaps had just made it to their fully retracted position when we were asked to turn 40 deg. Here again the aileron forces seemed heavy, reminding me of my days flying a Gulfstream III. But I soon got used to needing more muscle power in the roll axis and after a while I forgot it was ever a concern. Capturing and holding a 250-kt. climb speed was easily done, and passing about 10,000 ft. I decided to give the autopilot the fun of flying the airplane while I turned my attention to navigation and other cockpit duties. The autopilot accelerated us to 270 kt. until Mach 0.76, which it then maintained.

We made it to FL 400 in less than 20 min. I opted for an altitude less than 41,000 ft. to keep the crew off oxygen; 45,000 ft. was easily within our reach. I wanted to see the aircraft at its maximum speed and it easily accelerated to Mach 0.84. As we nibbled into the red and white “barber pole” of the airspeed tape, the autothrottles gently reduced our thrust to keep us right at Mach-Maximum Operating (Mmo). Roll control remained responsive and I did not detect any aileron buzz or other signs that my earlier concerns about a less than laminar flow off the ailerons were valid. In fact, other than the PFD indication, we had no other signs the aircraft was at its maximum speed, not even an aural clacker.
The “good manners” of the aircraft’s handling at high altitude and high speed prompted a lot of questions on my part about the Longitude’s partial fly-by-wire (FBW) system. While the ailerons and elevators are strictly conventional cables and pulleys that you would have found on the Citation I, which was certified more than 50 years ago, the rudder, spoilers, brakes and throttles use concepts unheard of back then. Many of us equate FBW with the old Airbus versus Boeing debate, arguing if the aircraft should have the ability to override the pilot. That debate is no longer valid, as Boeing has adopted FBW in its latest aircraft and Airbus has tweaked its version of FBW to prevent accidents like the June 26, 1988, crash of an Airbus A320 during an air show at Basel/Mulhouse-EuroAirport (LFSB), France. In that incident, the aircraft decided it was landing just as the pilot decided he was going around. In an odd twist of fate, a Boeing 777 had a similar accident on Aug. 3, 2016, at Dubai International Airport (OMDB). What those aircraft have in common are flight control computers that can make decisions and can, indeed, override pilot decisions.
The partial FBW on the Longitude is different—in fact very different. One of the advantages of FBW is a drastic reduction in weight and space requirements for all those cables and pulleys. Placing electrons between the pilot and the flight controls also allows more precise control when the pilot might be too busy or simply unable to provide the precision needed. The speed envelope provides a good illustration of this in the Longitude.
If you fly too fast and the autothrottles are engaged, the airplane has the good sense to bring the throttles back just far enough to keep you at the limiting speed. If the autothrottles are not engaged, they will automatically engage to retard the throttles. The aircraft will not automatically adjust pitch in an effort to reduce speed, but the flight director will provide the pilot with pitch-up commands. If you fly too slowly, the autothrottles will advance and if the speedbrakes are deployed, they will automatically stow. The aircraft is also equipped with a conventional stick shaker and pusher.
The Longitude includes an emergency depressurization mode (EDM), which activates if cabin pressure exceeds 14,700 ft., provided the autopilot is engaged and the aircraft is above 30,000 ft. In this situation, the aircraft will turn 90 deg. left, the autothrottles will retard to idle, and the aircraft will descend 15,000 ft. at Mmo/Vmo. Once level at 15,000 ft., the autothrottles will advance to provide a safe margin above stall speed. This automatic descent is becoming more or less standard on many high-altitude business jets, but the selection of 30,000 ft. as the minimum altitude for an EDM is not. Most of the aircraft that I’ve flown use 40,000 ft., a number that is too high in my opinion. Isn’t 39,000 ft. just as much a problem? I like the 30,000-ft. solution better.
The FBW rudder is electrically controlled and hydraulically actuated and feels perfectly conventional in all respects. In a way, many aircraft have a bit of FBW in the rudder, like the Longitude, with electronic yaw dampers and turn coordinators. The FBW spoilers also feel perfectly conventional in flight, helping to crisp up the roll rate of those cable-driven ailerons and to increase the descent rate when used as speedbrakes. The speedbrake handle is large and gives a good tactile sensation of how much is being used. The gentle buffet of the airflow from the spoilers to the tail was hardly noticeable.
Pilots who don’t trust these “Buck Rogers” FBW aircraft will have nothing to fear from the Longitude in that there are no flight control computers to take control away from them, aside from a gentle movement of the throttles when flying too fast or slow. As a former FBW-phobic pilot I would warn these wary pilots that full FBW is inevitable; nothing beats a flight control computer for extracting maximum performance and efficiency from an airframe. But I digress! The Longitude’s hybrid system reduces weight, increases efficiency and is really transparent to the pilot.

Cruising at 40,000 ft., I noted our cabin was at 4,700 ft. with a 9.6 PSID. Even at 45,000 ft., the cabin altitude would be below 6,000 ft. with a 9.66 PSID. While not the lowest I’ve seen in a business jet, it is easily the lowest for a super-midsize business jet. The Longitude achieves this performance with an air-conditioning system setup I have not seen before. A single air cycle machine (ACM) is paired with a heat exchanger (HE), which provides significant weight savings over a more conventional dual ACM solution. Combined, they provide the low cabin altitudes while the aircraft is at its ceiling of 45,000 ft.; alone, either the ACM or HE can do the same up to 41,000 ft. A small portion of the air is recycled through high-efficiency particulate air (HEPA) filters and all cabin air is exchanged every 2.5 min.
Also notable was the noise, or the lack of it, even in the cockpit. Many aircraft tend to get noticeably louder at high speeds, the air rushing around the nose giving the loudest impact in the cockpit. I did not sense any of that effect in the Longitude, which has the lowest noise level in class.
Descent and Landing
Finishing our air work, I turned us toward Hutchinson Regional Airport (KHUT), Kansas. Using a combination of vertical navigation (VNAV) and vertical speed commands made descent planning easy and the FMS helped position us for the RNAV (GPS) Runway 31 approach. We accepted vectors from Wichita Approach Control and configured with Flaps 1 and slowed to 200 kt. The navigation display simplified descent planning while the moving aircraft symbol overlayed on the Jeppesen approach plate increased situational awareness. A few miles outside the final approach fix I asked for Flaps 2 and slowed further to 160 kt. The autopilot handled the speed and configuration changes easily and I did not perceive any adverse G-loading found in some aircraft as flaps are extended. My plan was to allow the autopilot and autothrottles to bring the airplane down to LPV minimums, 250 ft. above the runway, and then go around as if missing the approach. With the vertical path a dot above us, I asked for the landing gear, which extended quickly and placed us ready for our descent. I delayed the last notch of flaps until we were established on about a 700-fpm descent and then asked for “Flaps Full.”
The autopilot commanded about a 5- to 8-deg. pitch change with the flaps and gradually returned the pitch to just a few degrees above the horizon as the airspeed settled at 140 kt. I didn’t feel any decrease in G-loading, but the pitch change took me by surprise. Pitcher explained that the 140-kt. bug speed was selectable by the pilot and would automatically reduce to Vref with 2 nm to go. That distance was also pilot-selectable.
The artificially high approach speed is a common practice among jets capable of lower Vrefs, helping to expedite the approach while not hindering following traffic. I wasn’t sure about the 2-nm distance, however. On a 3-deg. glidepath that leaves just over 600 ft. to go and just over 100 ft. to become stable by the industry-standard 500-ft. stable approach call. I was also unsure about slowing to Vref, but as the student in this situation, I was prepared to learn.
The sight picture from the large cockpit windshield made tracking the 7,003-ft. runway’s touchdown zone easy. Just as predicted, at 2 nm the bugged speed reduced from 140 kt., lower but not all the way down to our Vref of 120 kt. As before when slowing to 140 kt., the aircraft’s pitch changed slightly and we settled at Vref plus about 5 kt. by about the time we got to minimums.
After Pitcher’s “Minimums” call, I hit the TO/GA button on the left throttle and both throttles advanced to go-around thrust. The autopilot automatically disengaged and I rotated into the command bars and followed the navigation cues selected to match our climb-out instructions. We cleaned up the airplane and steered back to KICT for one more approach and landing, this time fully hand-flown.
Pitcher quickly downloaded the ATIS and programmed the landing data into the FMS, leaving us with time for more of my questions about approach speeds. I noticed on our first approach that the speed never made it to Vref. Pitcher explained that the FMS uses inputs from the air data system as well as acceleration and deceleration inputs from the IRUs to come up with an adjustment, similar to the one-half steady and full gust factor used on other aircraft. He also said that we didn’t want to land hot, because even with an extra 5 kt., the airplane likes to float. I asked if the airplane can simply be flown onto the runway in that situation and he readily agreed.
We received vectors to shoot the ILS Runway 01R and configured as before, extending the first notch of flaps about 5 mi. short of glideslope intercept. With Flaps 1 and 2, pitch changes were minor and the aircraft slowed to target speeds easily. I did not feel any need for excessive pitch or trim changes with gear extension, and capturing and maintaining the glidepath was not a problem. The winds were called at 320 deg., 16 kt. gusting to 20, about a 12-kt. crosswind without the gust.
I asked for full flaps right after glideslope intercept and again noticed the large pitch change, which I countered with aft yoke pressure. I trimmed and trimmed some more before Pitcher called me “a dot low.” With a little more effort, I got us back on glidepath and trimmed for 140 kt. Our Vref was 118 kt. and Vapp was 130 kt., but I was unsure what additive the airplane would choose once we were inside of 2 nm. Most aircraft that I have been typed in use half the steady state wind and all of the gust, with a minimum of 5 kt. and a maximum of 20 kt. Vref additive. That would come to 12 kt. above Vref, or 130 kt.
“Here comes the speed,” Pitcher called at 2 nm. The airspeed reduced quickly to about 125 kt. The trim change was noticeable but manageable and the autothrottles did a good job of keeping us on speed. I crossed the end of the runway at about 50 ft. and found myself ready to flare at 20 ft., just as the autothrottles retarded to idle. I gave the right rudder a little push to align the aircraft with the runway and my hands subconsciously leveled the wings. Rotating to the flare attitude required minimal force and the wheels kissed the runway right at the 1,000-ft. fixed distance markers, proving once again that trailing-link main landing gear make pilots look better than they are.
As soon as the main gear weight-on-wheels system signified the aircraft was on the ground, the six panels of the ground spoiler system fully deployed, making the aircraft settle nicely as I slowly released back pressure. The automatic ground spoilers use throttle lever angle, weight on wheels and airspeed to trigger deploy and stow actions.
I lifted the thrust reverser levers to the reverse position and slid both throttles to full reverse. “Keep them there,” Pitcher reminded me. The FADEC automatically began to reduce the amount of reverse thrust at 85 kt., ending at idle by 45 kt. This allowed me to keep the levers at full reverse, not having to worry about any engine or aerodynamic limitations while maximizing the stopping force. At 30 kt., the ground spoilers automatically stowed.
Taxiing back to where we started, I was again hit by the simplicity of it all. Many mundane pilot tasks are automated, and many tedious tasks are simplified. This was further emphasized during shutdown, which was simply a matter of shutting down the engines and turning off the batteries. “Gear pins?” I asked. “Not needed,” I was told. The gear-down locks require hydraulic pressure to release, removing yet another pilot worry.
As I walked away from the aircraft, I remembered a caution during my last aircraft initial training, in the Gulfstream GVII: “You have to get through the complexity to get to the simplicity.” For pilots, simplicity promotes safety. I think that perhaps for the Citation Longitude, the mantra should be: “You have to embrace the simplicity to maximize the safety.”
To read James Albright's preflight experience with the Cessna Citation Longitude, click here.