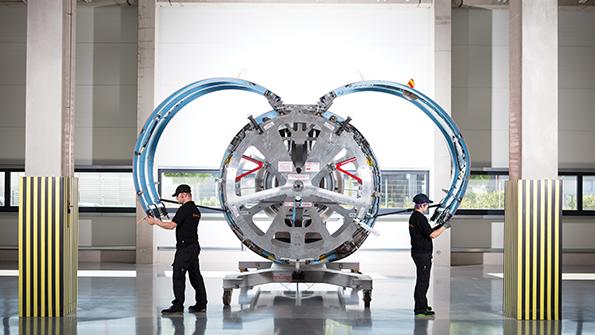
Cautious about the potential for hydrogen, Safran CEO Olivier Andries instead favors ultra-efficiency and airframe improvements.
Safran CEO Olivier Andries finds himself deeply involved in the aerospace industry’s main two challenges—its supply chain woes and the longer-term need for a sustainable way to power aircraft. Aviation Week European Technology Editor Thierry Dubois spoke with him in a wide-ranging interview, covering everything from today’s commercial turbofans to hydrogen propulsion, military engines, cabin equipment and, last but not least, space launchers.
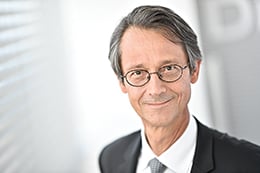
AW&ST: For the CFM Leap engine that powers the Airbus A320neo and Boeing 737 MAX, is your objective still to deliver 1,700 this year? We are still planning on that number—1,700 Leap engine deliveries this year. We talked to our CFM partner GE Aerospace, and we see no reason to change our plan. During the first quarter, we were producing at the required rate, which is 50% higher than in 2022.
During the summer of 2022, our engines were the determining factor in Airbus’ and Boeing’s delivery schedules. That is no longer the case.
Nevertheless, supply chain issues will still shape Safran’s activities this year and probably in 2024. We are most impacted in landing gear and helicopter engine manufacturing. More precisely, problems can be found in raw materials such as steel and upstream components such as forgings and castings.
What about the Leap 1C for the now-in-service Comac C919? It will remain marginal in deliveries this year. Our customer plans to ramp up to 50 aircraft per year by 2025 and hopes to reach 150 per year eventually. On our end, Leap 1C production will begin to be significant in 4-5 years. But it will never come close to the Airbus A320neo’s Leap 1A or the Boeing 737 MAX’s Leap 1B.
- Download Aviation Week’s new app at AviationWeek.com/App for our team’s up-to-the-minute coverage from the Paris Air Show
Do you plan to have a performance improvement program for the Leap? When we see something easy to modify to improve the fuel burn, we go ahead with it. But there is no such thing as a performance improvement program for the Leap.
We had to solve teething issues. The problem with turbine shrouds is behind us. Same goes for the Leap 1B’s accessory gearbox. We also have a coking issue on fuel nozzles-—we have developed a fix and now have to implement it.
In extreme environments, we have seen durability issues on high-pressure turbine blades. This is the case in the Persian Gulf and India, typically. We may have found a solution, and new endurance tests are giving encouraging results. Meanwhile, we make a point of keeping aircraft flying. Whatever the difficulties, we strive to have zero aircraft-on-ground situations.
Where are you with the RISE open-fan technology demonstration program? We are on schedule. We plan 400 partial tests before the first engine’s ground test in 2025. The first partial test in a wind tunnel will take place by year-end. The first flight test is planned for 2026 on a GE flying testbed. The first flight on a modified A380 will take place afterward, at a date to be determined.
We have altered our usual work-sharing scheme with GE. In an open-fan architecture, the low-pressure system has greater importance. Therefore, instead of our 50-50 split along the lines of the low-pressure spool (for us) and the high-pressure spool (for GE), we agreed that GE should work more on the lower-pressure part. Via Italian subsidiary GE Avio, they work on the gearbox and the low-pressure turbine.
You have consistently expressed caution about the use of hydrogen for aircraft propulsion. With recent progress, such as Universal Hydrogen’s first flight with a modified Dash 8-300 and Onera’s laboratory testing of hydrogen fuel nozzles, have you changed your mind? My comments have focused on aircraft burning hydrogen, as opposed to relying on fuel cells. At issue is the volume liquid hydrogen takes for storage—four times that of conventional fuel. For long-range aircraft, that is a nonstarter. For a short-to-medium-range aircraft, it is complicated. For a regional aircraft, it might be doable.
Imagine that the successor of the A320 runs on hydrogen. By 2035, every airport would be equipped. Investments are in the hundreds of billions of euros globally.
Also assume that drastic safety measures are in place. Keep in mind that at Europe’s spaceport in Kourou, French Guiana, filling up the liquid-hydrogen tanks on an Ariane 5 launcher calls for evacuating the launchpad area.
Fuel cells pose another problem: weight.
To meet our 2050 goals, we’d better rely on ultra-efficiency and airframe improvements. Our RISE demonstration program targets a 20% improvement in efficiency.
Targeting 2030 for entry into service would be too short a time frame. For an airframer to launch a program, it needs to reach Technology Readiness Level 6. We are investing in research and technology until 2026, and program launch may take place in 2027. Performance demonstration must happen before that.
Where are you with increasing the accepted proportion of sustainable aviation fuel (SAF) to 100%? We perform joint flight tests with Airbus. We look at what happens with 100% SAF in the fuel tank. At issue is the absence of aromatic compounds, which otherwise keep seals fuel-proof. We also cooperate with Boeing.
In addition, we look at how SAF can improve aviation’s non-CO2 effects on the climate.
In SAF production, the U.S. is off to a good start to go twice as fast as Europe. Their policy of incentives creates a high risk that the first significant decisions to create SAF factories will take place in the U.S.
But at least European mandates give a long-term assurance to investors, don’t they? Yes, the European approach must be welcomed with great satisfaction. Before them, nothing was in place on our continent. But look at Air France’s situation. Carriers are under pressure to decarbonize. They may have to purchase their SAF outside Europe.
How have Safran Cabin and Safran Seats performed recently? Safran Cabin and Safran Seats are very different companies. Safran Seats’ customers are carriers. Safran Cabin manufactures toilets, galleys and other monuments. Its customers are airframers most of the time. Those are different dynamics.
Safran Cabin’s priority is cost. Safran Seats essentially produces business-class seats, which are part of a carrier’s differentiation. They have a high degree of customization.
In our portfolio, Safran Cabin and Safran Seats were the companies most impacted by the COVID-19 crisis. They have a high exposure to demand for long-range aircraft, and retrofit activities stopped during the pandemic.
In 2021, revenues fell 65% compared to 2019, so restructuring was needed. We cut jobs, rationalized our industrial footprint and closed sites. Nevertheless, 2023 will be far from 2019 in revenues. We hope to see that level again in 2025.
In terms of profit, Safran Cabin broke even in the fourth quarter of 2022. We hope to be in the black in 2023.
For Safran Seats, the situation is even more difficult. We are facing supply chain issues. We won numerous sales campaigns in 2021-22, meaning we have several development efforts running in parallel. It takes 18 month until a development program turns into productive activity. We are in a period of development investment, seeing much greater costs than usual.
So are you keeping Safran Seats and Safran Cabin in the group? We performed a review of our activities last year. Of our activities, 70% are considered core, so they are staying with Safran. The other 30% remain under review. We have sold some of them, such as cabin trolleys. I will leave it to you to draw your own conclusions.
Are you planning evolutions of the Rafale’s M88? On the Rafale, the armed forces have been perfectly pleased with the M88. No one has requested an evolution in performance.
On the Rafale F4 standard, we have designed a new electronic control unit for the M88. It can manage more data, and we addressed any obsolescence.
On the future F5, will the armed forces need more thrust? That’s a question for them. We know how to do it, and we have a road map for that. A customer just has to action it.
Have you been able to stop using Russian titanium? That’s in progress. We are securing other sources. But the qualification process is long; it is not just a question of three months or so.
Let me remind you that titanium is not part of the EU sanctions regime against Russia. We first increased our inventory. Second, we found an alternative source of titanium billets—a more expensive one—in the U.S.
We are now devising an alternative with supplier Aubert & Duval and others in the titanium sector.
The time all this is taking is critical. We see a ramp-up in long-range aircraft production. They require more titanium than average for engine compressors and landing gears.
What is the impact of the strong variations in energy prices? We saw energy prices skyrocket in the fall of 2022. That caused us to postpone the creation of an additional carbon brake factory in France. We chose to increase production at our plants in the U.S. and Malaysia instead. Energy accounts for 40% of a brake’s manufacturing cost.
Since then, energy prices have decreased but are still higher than in North America or Asia. We will make a decision on a French factory by the end of 2024.
The lesson learned is we cannot afford extreme price volatility. When choosing the location for our additional site, a criterion will be the ability for the electric power provider to sign a 10-year contract with a commitment on price. You can do it in North America, but not in Europe. Here, the way the energy market works creates volatility. It is time for governments to act on this.
In space launchers, do you still foresee the first flight of an Ariane 6 this year? This year remains the objective. But we will be in a better position to answer after some critical trials. One of them will be the last hot-fire testing phase for Ariane 6’s upper stage at the German aerospace center’s DLR test facility in Lampoldshausen. Another is the ongoing combined testing in Kourou [where the launcher and the launchpad are being assessed jointly].
Once those milestones are passed, the risk curve will be sufficiently abated for us to have a clear idea.
As lessons from Ariane 6 program delays are learned, can you see Europe’s space sector engaged in a reorganization? We have a problem with the rule of geographical return (geo return) and the way it is implemented. When a country invests public money into a given percentage of a space program, it may expect the same percentage of contracts for its national industry. The entire space sector in Europe has successfully grown with that principle.
Now we have competition from SpaceX. Their fixed costs are covered by generous contracts from the U.S. government. The launch cadence is high, thanks to the needs of SpaceX’s constellation, Starlink. That’s a business model.
Meanwhile, geo return implies that European prime contractors partner with companies they do not choose. Those partners more or less define the price and do not feel competitive pressure.
For ArianeGroup [of which Safran is a 50% shareholder], on the Ariane 6 program, they represent 65% of the launcher’s added value.
The European Space Agency must reconsider that principle. For future space launchers, I recommend a risk- and revenue-sharing scheme. When a country has a given percentage of a program, it should receive the same percentage of the revenues. The commercial pressure should trickle down to the supply chain. With that, we can be competitive.
That necessitates political will. You will see some push-back; some states will resist the idea. By the way, those who criticize ArianeGroup’s profitability the most are those who most protect their national industry.