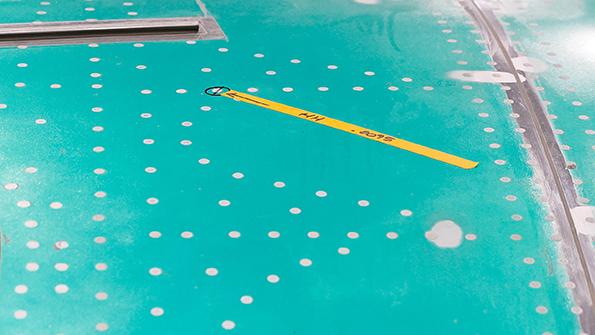
Increased inspections have cut down on defects such as this high-head rivet on fuselages coming from Spirit.
If Boeing’s latest plan succeeds, a single mishandled job will have prompted some of the manufacturer’s most fundamental production-line process changes in decades.
That job was supposed to have fixed a routine nonconformance—five fuselage rivets incorrectly installed by aerostructures supplier Spirit AeroSystems. But a lack of proper documentation detailing the process, done in Boeing’s factory, meant that four retaining bolts securing a door plug that had been opened to clear space near the rivets were never reinstalled.
- The manufacturer spotlights new production improvements
- Changes target tracking of parts and reducing rework
- 737 lines see slow, steady progress
The missing bolts eluded post-repair inspections, and the aircraft was delivered to Alaska Airlines in October. The panel-like plug worked its way free over 153 flights and blew off on the 154th, Alaska Airlines Flight 1282, on Jan. 5 (AW&ST Feb. 12-25, p. 18).
The plug’s stunning yet easily preventable inflight failure dispelled any notion that Boeing’s approach to managing incomplete jobs—known as traveled work—was effective.
“The fact that one employee could not fill out one piece of paperwork . . . and [that] could result in an accident was shocking to all of us,” Elizabeth Lund, senior vice president of quality, said during a June 25 media briefing at Boeing’s 737 production facility in Renton, Washington. “We knew this could never happen again.”
Boeing’s first task: prioritize production quality over volume, even if it meant slowing already reduced rates further while introducing initial changes. The first step in improving quality is doing more work correctly the first time.
“We don’t want to disappoint our customers,” Lund said. “We want to get them this airplane. We want to get it to them clean, but we really want to get it [to them]. What we haven’t had over time is a way to ensure we’re managing traveled work.”
Traveled work is inherent in aircraft manufacturing. But too much can create bottlenecks and process documentation headaches. This is particularly true if there is no system to track jobs being done at different places on the production line or to evaluate what work can be safely done later.
When one North American business jet manufacturer was struggling with traveled work on one program, Porsche Consulting, a subsidiary of the sports car manufacturer, was tapped to assess the situation.
The problem? The aircraft-maker was being too reactive, explains Joshua Hirschheimer, an associate partner in the consultancy’s aerospace and transportation group. Crucially, too many critical items were being delayed to manage the traveled work effectively without pushing back delivery dates.
Porsche Consulting worked with the manufacturer to create tactical approaches both for the entire production process and for each individual tail. The goal: keep airplanes and traveled work moving without affecting quality or delivery targets.
“To be effective, you need to bring the critical path items, including defects, down to zero. You don’t want things being done where it’s going to delay the aircraft rolling off the line complete,” Hirschheimer says.
The business jet manufacturer’s problems cropped up on a new program. At Boeing, the 737’s traveled work problems stem from pressure introduced by production rate increases.
Up until January, Boeing had taken a reactive approach. It accepted fuselages from Spirit with scores of nonconformances that needed to be fixed as the aircraft was being completed within Boeing’s walls. Incomplete jobs and related paperwork went to the next spot on the production line for someone else to handle.
But the short path from a botched routine fix to a near-catastrophic in-service accident laid bare the depths of Boeing’s production problems and risks in its approach. Two fatal 737-8 accidents in 2018 and 2019 placed the once-revered manufacturer’s aircraft design and engineering bona fides under heavy scrutiny, leading to changes in how both Boeing and regulators approach aircraft certification. The Jan. 5 737-9 accident, while not fatal, has done the same for Boeing’s decades-old production operation and how the FAA oversees it.
“We’re just asking that question of manufacturers: Have you considered the risk that comes with not only that one event, but the 10 other ones?” FAA Associate Administrator of Aviation Safety David Boulter said at a recent industry safety conference. “Are you really using that risk analysis and saying, ‘You know what? There comes a time where there’s too many things missing from the supply chain. We’re going to stop right here and not move [the aircraft] down the line, because the risk is too high.’”
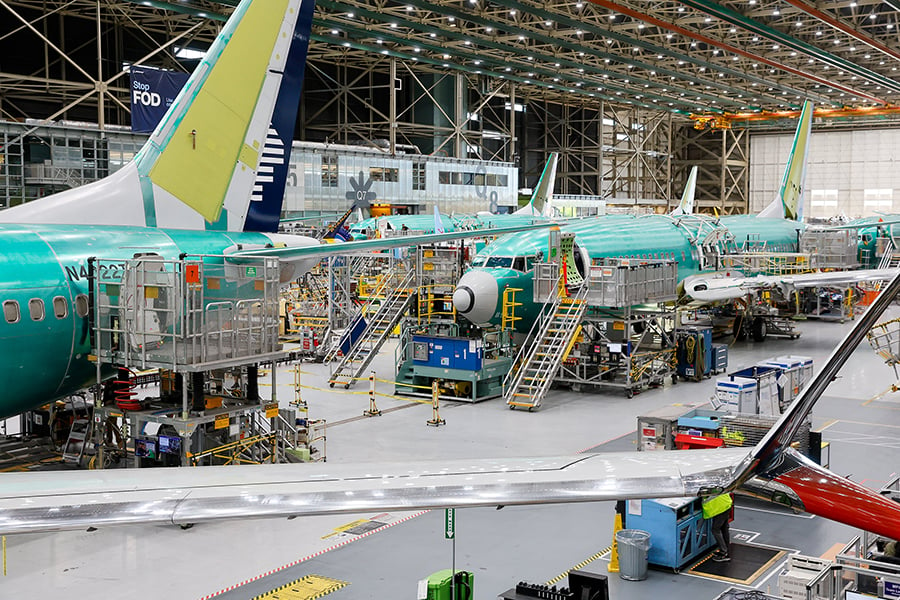
Boeing groups its changes, some voluntary and some ordered by the FAA based on an audit, into three categories: fewer defects, better processes and improved training (AW&ST Feb. 12-25, p. 16). If effective, the steps will feed into a fourth: a more deeply rooted safety culture. Traveled work touches on all four areas.
Boeing’s first order of business is to cut down on the number of problems entering its final assembly lines. Starting in March, the airframer set up about a dozen new inspection stations at Spirit’s 737 fuselage manufacturing facility in Wichita, staffing it with 200 Boeing engineers and twice as many Spirit workers.
“We demanded that Spirit treat us as an inspection authority on their premises and treat it like an FAA ticket so that not a single fuselage would leave that facility that wasn’t in perfect condition,” Boeing CEO David Calhoun told U.S. lawmakers during a June 18 hearing on the company’s safety culture.
Consistently perfect fuselages are a tall and likely unachievable order. But the effort seems to be paying off. Lund says defects such as incorrectly installed rivets are down 80% since the checks were set up at Spirit.
With fewer problems showing up on Boeing’s doorstep, the company—which is buying Spirit to ensure full control over the critical supplier’s work—can channel more resources into minimizing organic issues. Better training for both new hires and those on the floor has been rolled out.
A longer-term change is improving the thousands of pages of work instructions and related process and procedures documentation required to assemble aircraft.
“Our build plans are at times complicated, particularly for a new employee [with] no aerospace experience,” Lund noted. Boeing is reviewing all of its production documentation and making updates where prudent.
“This will take several years to get all the way through, but I think it will really set us up for the future,” Lund said.
Some internal changes already are being rolled out. Among the most significant are new protocols for moving aircraft down the production line.
Boeing has developed “move-ready criteria,” or sets of critical jobs that must be completed at each of the 10 737 production line stations before an aircraft is cleared to move along. For example, at the third station—the last before landing gear and flight control surfaces are installed—six steps must be done before a fuselage can move to the fourth station. Among them are installing the dorsal fin and four key flight deck panels.
“Deviations require a safety risk assessment or approval of manufacturing/quality assurance/engineering leaders,” says a banner posted in the third station listing the criteria.
“Here’s the criteria at every position, here’s the critical job, here’s what you really need to make sure is done before you move,” Lund said.
Boeing’s three 737 MAX production lines are each producing aircraft well below the notional maximum capacity of 20-21 per month. In recent months, the company produced about 25 per month combined, or about eight per line, data compiled by Aero Analysis Partners/AIR shows.
At that pace, stopping a fuselage—and all progress on one line—to correct issues is disruptive but not disastrous. Two other lines can pick up the slack, accepting aircraft flowing into the system.
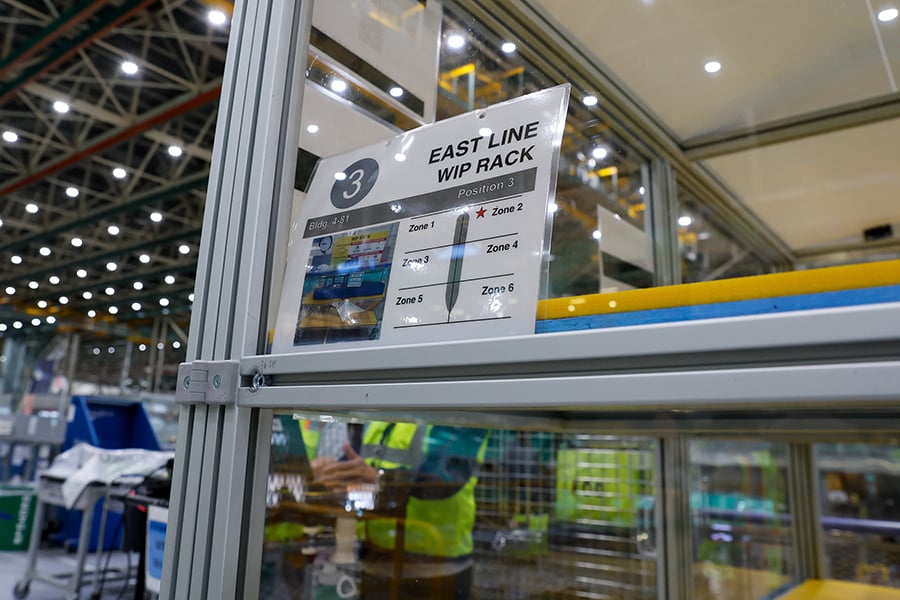
But achieving Boeing’s notional target of 50-plus per month within two years will test its new protocols. Managing inevitable traveled work effectively and consistently becomes not just a goal but a requirement. The company says changes to its work-in-progress (WIP) rack process will help meet that challenge.
The WIP racks are for incomplete work. Issues caused by missing or nonconforming parts are managed using a different process. The concept is simple enough, yet more systematic than what Boeing used before.
WIP racks, which are not new, are metal cages that house parts needed to complete jobs. Under a process introduced in April across all 737 production—the three 737 MAX lines and the dedicated P-8 line—and that is steadily being expanded to all final assembly facilities, parts and their installation plans are loaded onto the racks and electronically tagged using a barcode. Racks now move with the fuselages, and their contents are inventoried at each station.
Before, parts often would disappear daily from the racks as mechanics sourced material needed to finish jobs. The new electronic tracking links parts not just to their WIP carts, but also to mechanics who check them out. Jobs are being completed more quickly, and reports of lost parts have dropped to 1-2 per week.
A fifth line for 737 MAXs is being set up in Everett, Washington, the site of 747 production and, more recently, extensive rework on 787s. That line is subject to FAA approval that Boeing must earn by demonstrating consistency on its existing ones and will give the airframer capacity to ramp up steadily while honing its refined processes.
The road ahead is long, but Boeing executives are confident the company is heading in the right direction.
“We have slowed down our factories over the last few months to make sure that these measures are under control and our factory is under control,” Lund said. “The results show it.”