
Lufthansa Technik is using what it says is the world’s first automated adaptive robot system that can be applied to a multitude of MRO processes for composite aircraft parts, including radome repairs.
Radome technology continues to advance as new materials are certified to meet the growing demands of structural performance and higher operating temperatures. To appreciate that, it is necessary to have some basic understanding of radome design.
In today’s radomes, the only metal parts are hinges, latches, the attachment ring and thin lightning-diversion strips that redirect static electricity to the fuselage. The radome shell itself is made of composite materials.
“There have been limited designs using aramid fiber-reinforced plastics, but today most radome shells on commercial aircraft are made of glass-fiber-reinforced plastics (GFRP),” says Marc Homann, head of technology and development engineering for aircraft component services at Lufthansa Technik. “These materials provide sufficient permeability for the radar waves while simultaneously allowing functional designs that are able to withstand many of the significant forces the aircraft nose is usually exposed to.”
Homann adds that GFRPs are considered highly durable but come with their own issues. “An FOD [foreign object debris] event, for example, usually not only leads to chipped paint, but also to further delamination of the structure,” he explains. “This can occur in areas that are usually invisible to the naked eye.”
The radome structure design is highly complex and variable. The typical radome fabrication process involves a composite sandwich or multilayer design, explains Keith Loss, executive vice president of Rock West Composites. To start, he says, there is the “A-sandwich,” a simple construction in which two low-dielectric composite material skins—typically fabric-reinforced—surround a low-density/low-dielectric composite core.
“The outer skin thickness is selected to address impact damage, while the other skins and core thicknesses are optimized to minimize radio-frequency [RF] transmission loss for the frequencies of interest over the range of view angles for the antenna,” he says.
Loss says additional skin and core layers can be added to the sandwich design to optimize transmission. This is especially true for designs that must work over a very broad range of frequencies and configurations—where RF rays intersect the radome surface at near-grazing angles. “Radome designs with three skins and two core layers are called ‘C-sandwich,’ while those with even more layers are termed ‘multilayer,’” he says.
Loss says the typical aerospace flightworthy materials for radomes are fiberglass-epoxy and quartz- cyanate ester.
“BMI [bismaleimide], phenolic or polyimide resins may be required for higher-temperature applications,” Loss notes. “Fabric-reinforced thermoplastic materials also can be used for skin. Core materials are typically honeycomb core such as NomexTM, glass/phenolic cores or low-density foam cores.”
Asked about new materials for radome applications, Loss reports that some composite material suppliers have introduced fiber reinforcements, which have lower dielectric properties than traditional E- or S-glass fabrics, though not as low as quartz fibers. “Those materials are being introduced at price points which make sense for some customers,” he says.
“Dielectric properties” refers to dielectric constant, which Loss explains is a measure of the ability to store electrical energy. “For a radome designer, the goal is to minimize the difference between the dielectric constant of the radome skins and that of air, [which has a] dielectric constant of 1.0,” he says. “In general, the lower the dielectric constant of the skin, the less the reflected energy—transmission loss—off that skin.”
He adds that the other layers of the sandwich radome work together to mitigate the initial reflection through constructive interference of the reflections off their surfaces. “The challenge is the cost of qualifying these new material systems for their mechanical properties as required by either a U.S. military customer, the FAA or EASA [European Union Aviation Safety Agency],” he says.
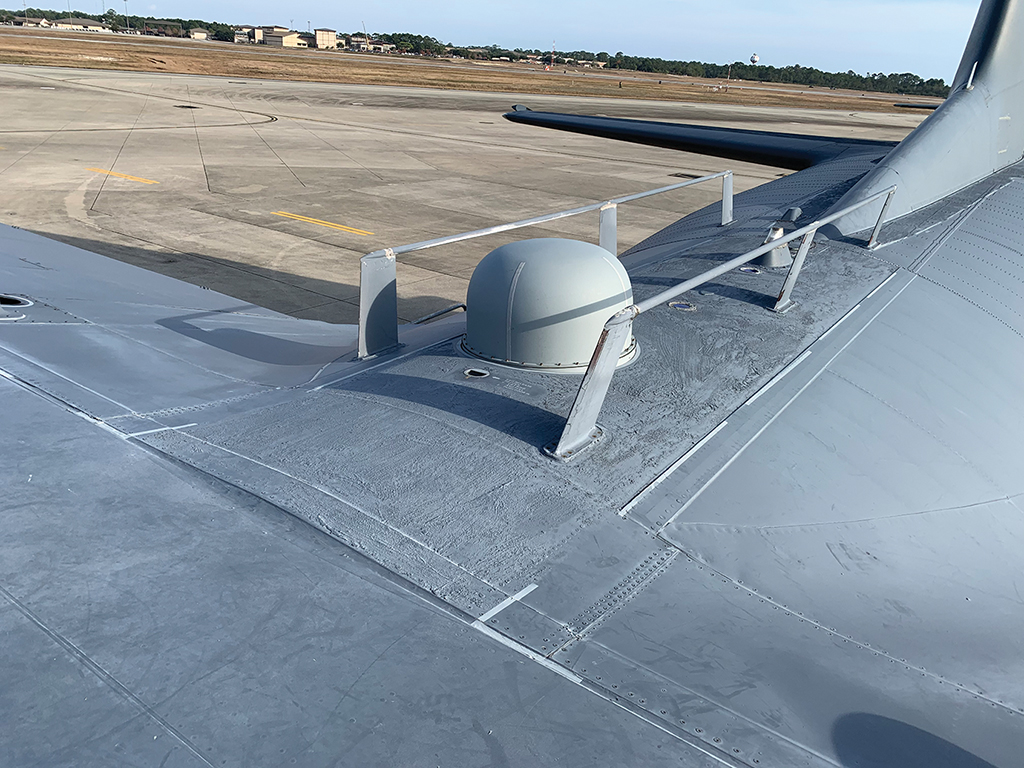
In addition, there are challenges that come with day-to-day operations. Loss says hail, ground equipment, foreign objects and lightning are, in that order, the main sources of damage. To mitigate damage risk, Rock West Composites is moving away from honeycomb cores for radome sandwich structures to tougher foam cores.
“We incorporated a few thermoplastic foam cores that were already qualified by the FAA for aircraft interiors,” he notes. “They have good mechanical-environmental properties and notably bond well to our composite skins. Those bonds provide superior impact- damage tolerance.”
Park Aerospace, a supplier of epoxy and cyanate ester-based resin systems, has developed RadarWave, a family of composite fabrics for commercial and business aircraft radome applications.
Rob Cathcart, director of sales for Park Aerospace, says RadarWave bridges the performance and cost gap between E-glass and Astroquartz-based materials for radome and antenna applications. Astroquartz is a proprietary silica-grade fabric from JPS Composite Materials.
“The reinforcement used in RadarWave is a low-loss, glass-based fabric, available with various low-dielectric resin systems,” Cathcart says. “Depending on the resin system selected, RadarWave can be tailored to provide improved levels of foreign-object-damage resistance.”
As Cathcart explains, RadarWave is “biased toward” the higher performance of quartz, with a cost roughly halfway between E-glass and quartz. At the same time, he stresses that weight must be considered as an additional design factor in radomes. “RadarWave is available in two weights—RW-8-100 (8HS weave, 100 GSM [grams per square meter]) and RW-8-300 (8HS weave, 300 GSM)—that are closely aligned with the fiber areal weights of Astroquartz 4503 and 4581, respectively,” he notes.
Cathcart stresses that durability is tied to the customer’s operating temperatures, electrical performance and cost constraints. “Park Aerospace defers to our customers that have more experience with skin and core combinations that influence durability,” he says.
He also points out that there is seldom a one-size-fits-all approach to radome design. “For example, cyanate ester/Astroquartz III offers superior performance, but raw material costs alone can be an order of magnitude higher when compared to an epoxy/-fiberglass system,” Cathcart says. “If an adhesive is required to bond the skins to core, the system is more complex and costs are increased further. All the design and cost constraint requirements have to be identified and prioritized from the beginning because it’s common to run into conflicting requirements resulting in necessary design compromises.”
Scott Huth, general manager for aerospace at Saint-Gobain, explains that improving the durability of the radome structure is a complicated process, since changes can affect weight and cost. For example, he says, while quartz fiber is more durable than fiberglass, it is also more expensive.
“The composite matrix is also a factor. Saint-Gobain is developing thermoplastic composites for radomes. Testing indicates a notable improvement in impact resistance,” Huth says, also pointing out that coating technology has improved.
How the individual coatings are selected and applied is more important for damage resistance, he adds: “Due to numerous factors, several coatings are applied to a radome in order for the coating system to be damage-tolerant.”
At the same time, Huth says excessive paint coating thickness can impair radar performance—as do added material thickness and moisture intrusion. “Saint-Gobain has periodically performed evaluations of coatings materials for radomes by testing the individual RF properties and the coating systems’ erosion resistance,” he says.
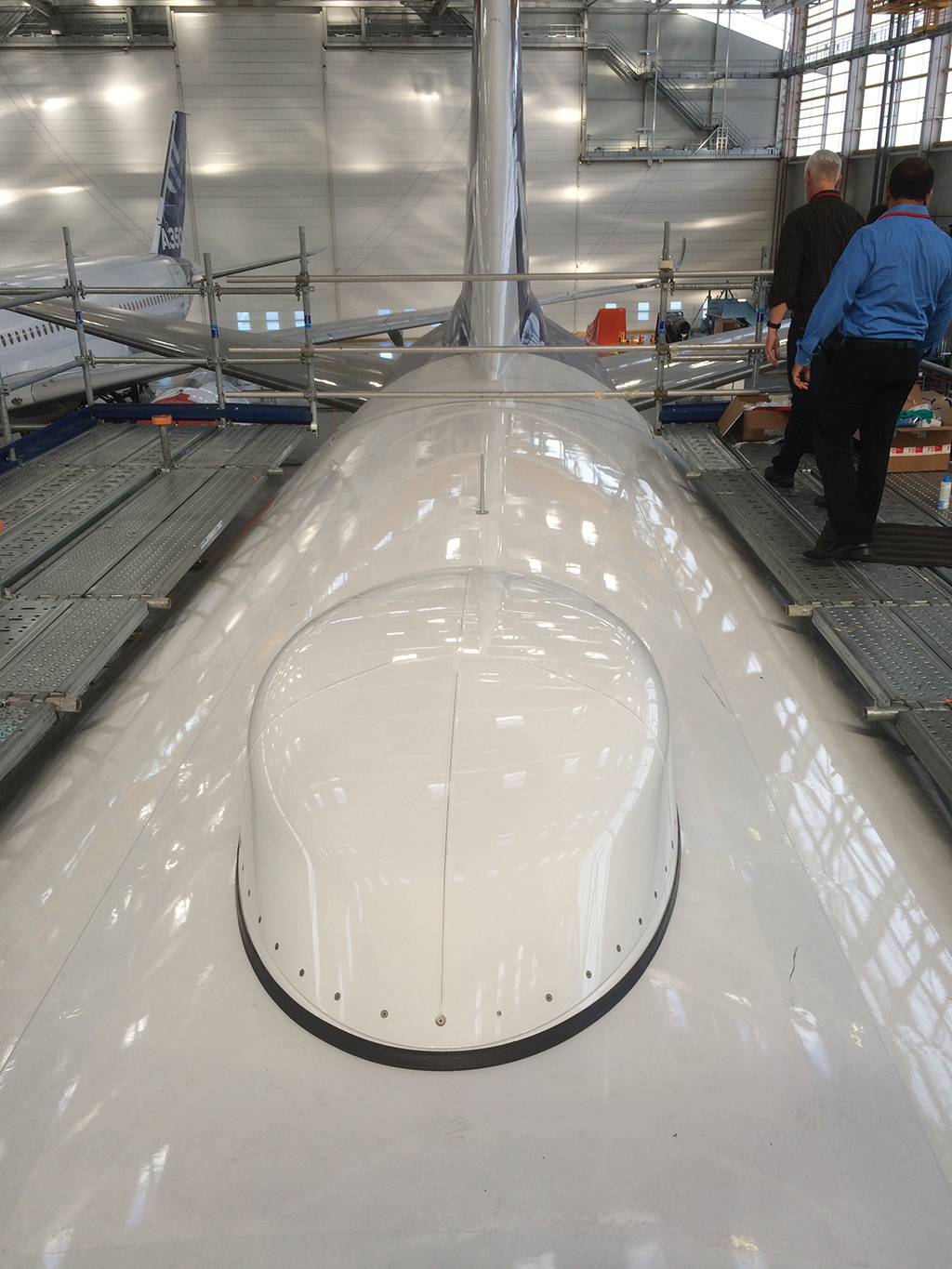
Given an ongoing focus on weight reduction in aircraft design, are lighter-weight radomes as damage-resistant as the heavier products they are replacing?
“Yes, radome construction can be made lighter and yet have improved damage resistance,” Huth says. “However, that may not be feasible for all aircraft types due to other factors of certification and cost.”
Huth stresses that the radome engineering and design process can utilize a myriad of materials layered in multiple orientations—optimizing key performance variables such as strength, impact resistance and RF performance at different frequency bands, as well as weight and cost. He adds that the proprietary Maxio Aero optimization tool developed by Saint-Gobain allows for the evaluation of more than a million potential combinations of materials and orientations within a very short time.
“We can share this data with customers, then ‘tune’ the design to balance the performance variables to meet final requirements,” he explains. “We can then use our proprietary radio-frequency simulation tool to ensure the design meets the critical RF performance requirements without the tedious testing in an anechoic chamber.”
Durability is always a customer concern. Tim Davis, senior manager for service engineering at Southwest Airlines, cites the application of an erosion boot as “one of the best advancements” in radome design.
“In the early years, the protective coatings, which include paint, would wear down, and then ultimately the erosion would break down the fiber of the composite layers,” he says. “This was not deemed a safety concern, but it led to repairs and operational disruptions. The erosion boot is a thin layer of polyurethane film material that protects from erosion. It has made nose radomes much more reliable.”
Davis also reports that one area of radome technology currently advancing is the capability to withstand more significant bird strikes. “This hasn’t been rolled out for the [Boeing] 737,” he says. “But I have heard that for other models, Boeing has started looking at more robust structural designs for radomes to better absorb the impacts of larger birds.”