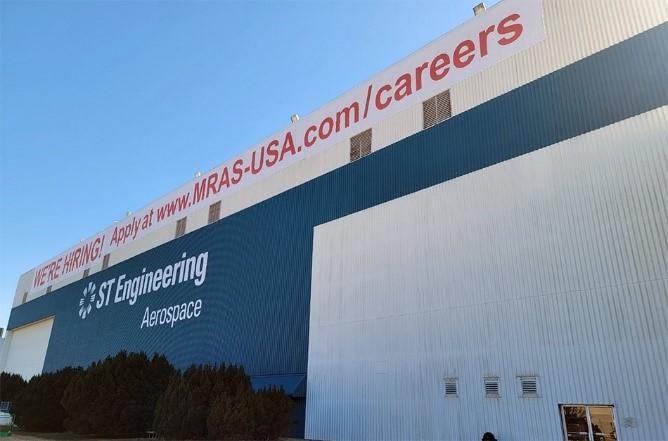
Through solar power and other innovations, Singapore Technology Engineering is cutting carbon fuel use in its aircraft maintenance operations.
Meanwhile, ST Engineering’s design and manufacturing subsidiary, Middle River Aerostructure Systems (MRAS), is shaving fuel burn and CO2 emissions by making smarter nacelles for commercial airframe OEMs like Airbus, Boeing, Bombardier and COMAC.
MRAS increasingly collaborates with engine OEMs to develop integrated propulsion systems with lower weight, less fuel burn, better aerodynamics and less noise.
It is currently involved with two nacelle systems: for the GE Passport engine on Bombardier’s Global 7500 business jet, with some 200 nacelles delivered to date; and for CFM’s LEAP-1C for COMAC’s C919, which is completing flight tests and certification for entry into service.
Both programs have been developed jointly with Safran Nacelles through the Nexcelle joint venture.
Lower weight is primarily achieved by the extensive use of composites in components. For the Global 7500, Nexcelle uses composites extensively, including on the large two-piece fan cowl doors that enable access for inspection and maintenance.
To improve aerodynamics of the C919, Nexcelle is pinning the inner fixed core cowl to the pylon, eliminating a large duct sidewall and beam structure. This narrows the total pylon structure, reducing weight and drag.
To reduce noise on the C919, inlets are fabricated using a proprietary process to splice honeycomb core together. These splices are acoustically ‘transparent’ and do not reduce the benefit of inlet acoustic liners.
Other nacelles were also reduced in weight and improved in performance. For LEAP-1As powering A320neos, weight was cut by replacing several metal components with composites, for example beavertail fairings.
For the GEnx-2Bs powering 747-8s, an acoustic attenuation system with two degrees of freedom is located in the fan duct outer wall composite bond, attenuating engine noise over a wider range of frequencies.
MRAS also introduced a trailing edge feature, chevrons, to reduce noise by optimizing the mixing of secondary engine flow with surrounding air. This feature is designed and manufactured as part of the translating cowl.
All these design features were developed through MRAS’s independent research and development. Each design innovation, by itself, saves less than 1% in fuel burn and CO2 emissions. Cumulatively, innovations can save more and are, of course, part of the overall effort to cut fuel burn and emissions substantially on new aircraft.
MRAS’s and Nexcelle’s line-fit nacelles will be flying on aircraft for a long time, as nacelles are typically repaired or replaced with the same design. Nevertheless, MRAS continuously looks for ways to introduce technology to enhance its products’ performance and reduce costs.