Cool Running: How AeroKool Helps Airlines Bypass A Slow Supply Chain
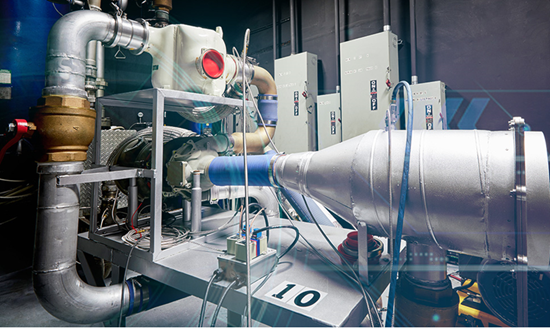
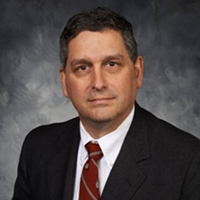
Q AW: As a PMA parts and DER repair provider, has Aerokool benefitted from the supply chain crisis?
A Jon Silva: It’s been a net positive for us. Offering PMA/DER solutions has driven a lot of customers to AeroKool because the OEMs or the OEM-licensed shops are struggling with lead times, which keep going out to the right – we can see upwards of a year to get an Air Cycle Machine (ACM) housing, for instance. There’s also the price differential, which could be up to $80,000 for an ACM overhaul when we use PMA versus OEM parts. In addition, we've seen anywhere from 8-12% year-over-year increases for the last 12 years on OEM parts – that's pretty significant on just the environmental control system [ECS]!
Q AW: Have shorter lead times improved customer acceptance of PMA?
A Jon Silva: Five years ago we had a significant number of customers that only wanted OEM repairs from us. In other words, they wanted us to use all OEM parts in the repair. That group has shrunk significantly. In fact, I can think of only one serious repeat customer that still requires a repair with OEM parts. It’s not just the price, it's the lead time – they need their airplanes back.
Also, the ECS system doesn't inhibit anybody from the safe operation or landing of the aircraft, which, I believe, has made the adoption of PMA easier for AeroKool customers. For a lot of folks that insisted on OEM, it was just policy versus any real hard thinking about it, but as lead times and price have increased customers started to look at some of these non-flight-critical parts differently.
Q AW: How do you minimize repair and overhaul times and costs for your customers?
A Jon Silva: We can turn around just about everything we do within 21 days. That’s a pretty good lead time, but if you need a part tomorrow, we'll have a component ready to go. AeroKool has acquired core units, overhauled them, and put them on our shelf for use as rotable units for customers that need an immediate exchange. We have acquired a good stock of rotable units and that gives us a different lever on the market. Then there are the 400-plus individual PMA piece parts that AeroKool has for the mechanical components we repair. We also have over 1,000 different DER repairs for the different components of an ECS system – components like control valves, heat exchangers, temperature sensors.
Q AW: Many specialized repair shops struggled to retain or re-hire skilled technical staff during or after the pandemic. What was AeroKool’s experience?
A Jon Silva: The pandemic hurt everybody, and AeroKool had its challenges too. Fortunately for AeroKool, about 50% of our business is military, which was not affected by the pandemic to the degree commercial aviation was. So, we were able to hang on to most of our skilled technicians and we weathered the storm. The other advantage we had, perhaps like other independents, is that we just had to make sure we did not get into financial trouble – there was no one beating on Aerokool to make 21% EBITDA or whatever. We were able to hold our own, protect our staff, stay out of debt, and not get into trouble.
Q AW: How much overlap is there in your capabilities for commercial and military aircraft customers?
A Jon Silva: There's a lot of crossover. Anything pressurized is most likely going to be pressurized from bleed air off the engines, and that bleed air is anywhere from 300-400°F. The system to pressurize the cockpit or even the cabin of a military aircraft, therefore, is very similar to the ECS system that pressurizes, say, a Boeing 737.
Q AW: What can airlines do to maximize the service life of an environmental control system?
A Jon Silva: The ECS is not flight critical, but nobody's going to push back an airplane without the ECS system operating. These things can last well over a year of operating, and to up to three or more for some of our customers once we get them on a good cleaning schedule. There are some things that the operator of the aircraft should be doing to keep the ECS system functioning correctly.
The root cause of a failure is often a dirty or clogged heat exchanger, but what most people see is the ACM/Cooling Turbine has stopped spinning, so they pull the ACM/Cooling Turbine and send it to us. In turn, we always recommend customers check their heat exchanger first, as there’s no point putting a fresh turbine behind a dirty exchanger.
Q AW: For the components you cover, do new-generation aircraft feature any new technology and can you foresee any changes for future aircraft types?
A Jon Silva: I won't speculate on the all-electric plane yet, but essentially the systems have remained the same, which is engine bleed air pressurizing the cabin and cockpit. The two types of turbo-machinery that we deal with are either oil-bearing-based units or foil-air-bearing-based. The older technology is oil-fed ball bearings, but even the foil air bearing technology is not new. Foil air bearings were first developed in the 1970s. There have been improvements to foil air bearing designs, but the basic technology is the same.
Q AW: What changes would you like to see from OEMs or regulators in your section of the market?
A Jon Silva: Certain OEMs have stopped giving access to manuals [Instructions for Continued Airworthiness] outside their licensed repair networks and that's a problem for the maintenance industry. Sometimes this forces us to no-quote something because we can't get the most recent manual quickly enough. That’s a problematic because the FAA requires that Repair Stations have the most recent manual. The regulations also require that OEMs make the manual available. Currently the FAA has tasked an Aviation Rulemaking Advisory Committee (ARAC) to address the issue of Manuals/ICA availability.
Leads times of up to a year for OEM parts have pushed many airlines towards PMA replacement, especially for non-flight critical components like the environmental control system, which AeroKool specializes in. The MRO provider offers turn times of just a few weeks, as well as a large stock of rotable components for immediate dispatch. It also feeds its own PMA parts into its repairs, offering significant savings over the OEM alternatives.