Component MRO Predictions: Shops Downsize Expectations But Work On Backlogs
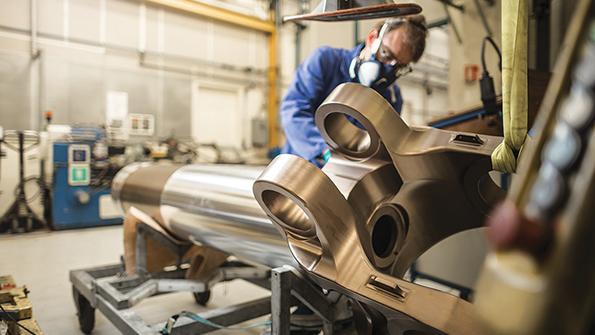
Growth in the parts repair segment is expected to be stunted by the novel coronavirus pandemic but component MRO specialists believe demand will remain in specific areas of the market.
Accounting for around 28% of the market, according to Aviation Week Fleet & MRO Forecast data published before the novel coronavirus pandemic, growth in the segment was occurring at a compound annual growth rate of 4.8% annually. Shops were routinely full, with some smaller operators routinely working to backlogs surpassing more than one month.
However, given the mass fleet grounding worldwide, these backlogs will likely dry up in 2020. Yet, still existing pre-crisis backlog will mean some repair shops will maintain some workflow in the short-term before expected shortfalls occur.
“We currently have a healthy backlog, with two to three weeks of workload, but we are slowly seeing a drop-off in demand and adjusting to match customer requirements,” says Sajedah Rustom, CEO of AJW Technique, the company’s in-house MRO facility based in Montreal. She states that while no existing work has been cancelled, the company has fielded customer requests for hold of components until they are required.
Rustom also identifies a slight upturn in components being removed from aircraft, due to some airlines choosing to use the downtime to perform heavy maintenance inspections. In terms of specific components, Rustom is seeing removals based on calendar life rather than flight hours in demand, such as escape slides, rafts and crew oxygen masks.
“We have not seen a reduction in this group of components, but that may change as most aircraft are grounded,” she says. “However, we expect operators to maintain their fleet in airworthy condition, therefore these segments will continue to be in demand.”
Another aftermarket services provider adjusting its strategy is AFI KLM E&M, which along with its core MRO business, operates a network of parts specialists including its Spairliners joint venture (JV) with Lufthansa Technik. Like many businesses in the commercial aftermarket, it has had to change its working schedules due to weakening demand for parts repairs.
“Our component shops have adapted their productions to the downsizing of the demands,” a company spokesperson told Aviation Week via email. “Due to local government restrictions, some shops have locally reduced their activities to AOG situations, management of long-term contracts and, when they can’t manage by themselves, do their best to provide a solution based on our global network of JV and subsidiaries.” They added that the company’s substantial supply chain operations, which to date have held up relatively strongly, have also been adapted accordingly to lower volumes.
Lena Watters, senior vice president and general manager of U.S.-based STS Aviation Services, hasn’t seen any new maintenance demand resulting from the new environment in which the industry finds itself. “Not on the commercial side of our interior component overhaul business,” she says. “While there isn’t much of a demand for galley equipment repairs, seat overhauls, we are seeing a slight uptick in requests from cargo carriers,” she says.