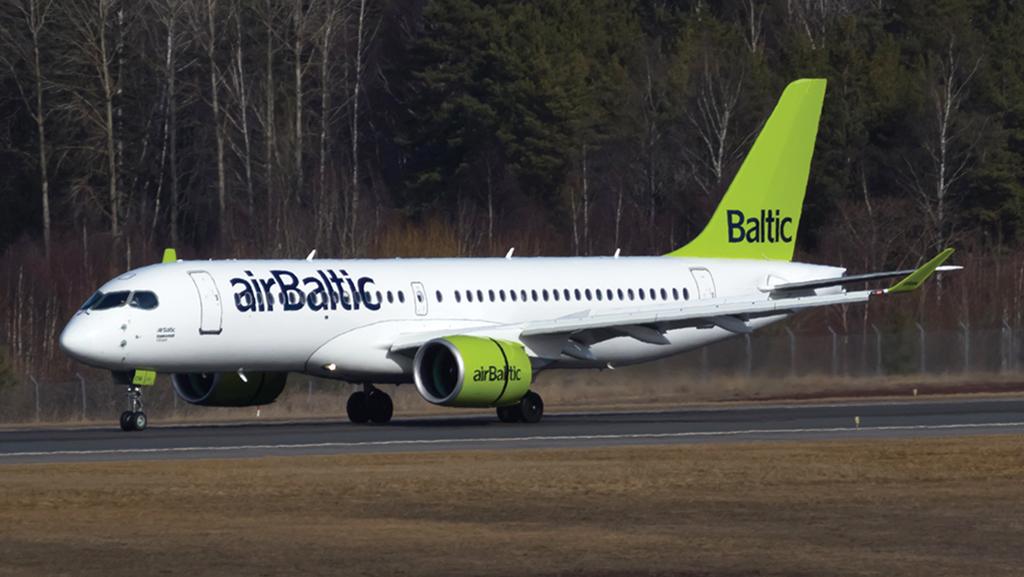
Air Baltic has confirmed ongoing supply chain issues with the Pratt & Whitney engines on the airline’s A220-300 aircraft.
Passengers are returning to the skies and airline performance is surging back toward pre-pandemic levels, so one might expect the maintenance market to be resuming its normal rhythms. After all, shops are full, slots are in high demand and the big MRO providers are reporting a healthy uptick in profits and sales.
Scratch the surface, however, and many of the changes wrought by the pandemic endure as airlines continue to prioritize cost savings as they seek to rebuild their businesses and their balance sheets. Furthermore, supply chain challenges and inflationary pressures exacerbated by Russia’s war on Ukraine have added extra considerations, especially regarding turnaround times, fleet availability and parts procurement.
“We still see many airlines looking for flexibility—while the majors are reporting great results, there are many more airlines that are thinking short-term as they repay loans and remain short-term cash-focused,” says Phil Seymour, president of consultancy IBA Group.
One such airline is Riga, Latvia-based Air Baltic. “Everyone is still affected and trying to fully recover from the consequences of the pandemic and the war in Ukraine,” notes Oskars Zalkalns, vice president for engineering at the airline.
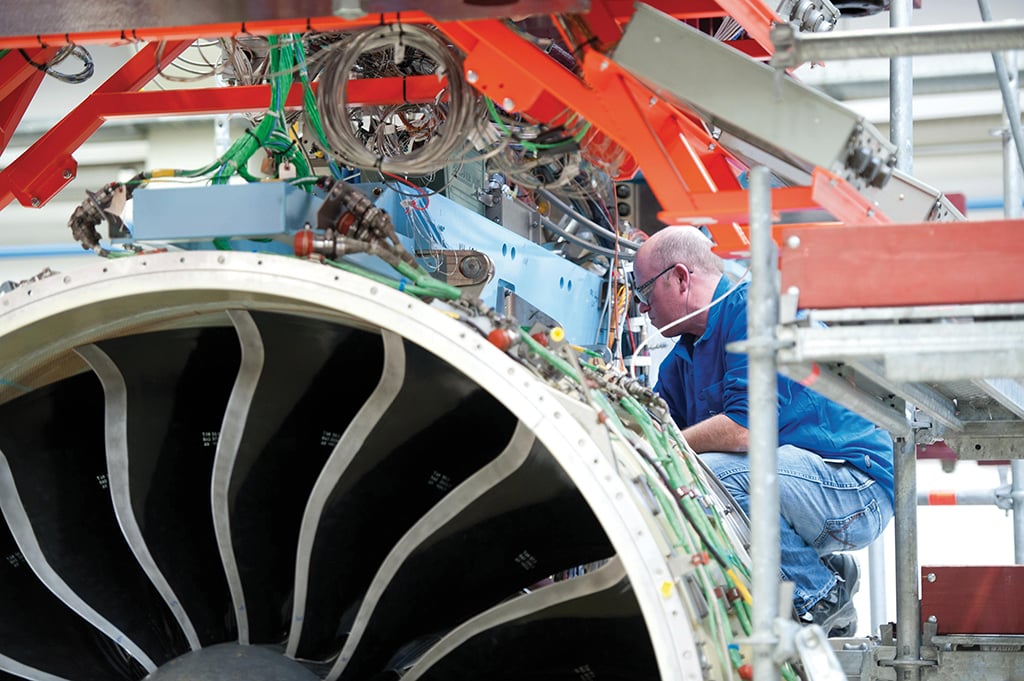
New-Gen Challenges
Another challenge for Air Baltic and many other airlines: the reliability problems and revised inspection mandate for Pratt & Whitney Geared Turbofan (GTF) engines, which have created considerable uncertainties for their maintenance and fleet planning departments.
Air Baltic operates an all-Airbus A220 fleet, meaning it is also affected by Pratt & Whitney GTF engine problems that have hit aircraft availability for operators around the world and led to new—and usually confidential—maintenance and inspection deals between the operators and OEM.
Speaking to investors in August, V2500 and GTF operator Wizz Air would not be drawn on the details of any compensation arrangements with Pratt & Whitney, but did expect that as the largest airline customer of the OEM, it would receive “treatment according to that status.”
However, Wizz Air CEO Jozsef Varadi also noted that it was too early to cost-out a maintenance plan for the latest problems revealed by Pratt—which will require the removal of up to 1,000 engines worldwide—because the OEM had not finalized the inspection program. “Pratt & Whitney is saying that in the best-case scenario they might be able to come up with a designated short program. So it wouldn’t affect the current operations of the engine shops, but this is not yet fully confirmed,” he said.
There is also uncertainty around the 12 GTF engines that Wizz Air must remove by mid-September under a service bulletin. The airline has budgeted for reduced capacity in the second half of this year due to these removals, but Varadi said it still does not understand exactly what the scope of the inspections will be, how long they will take, or how the work will fit in with Pratt’s available shop capacity.
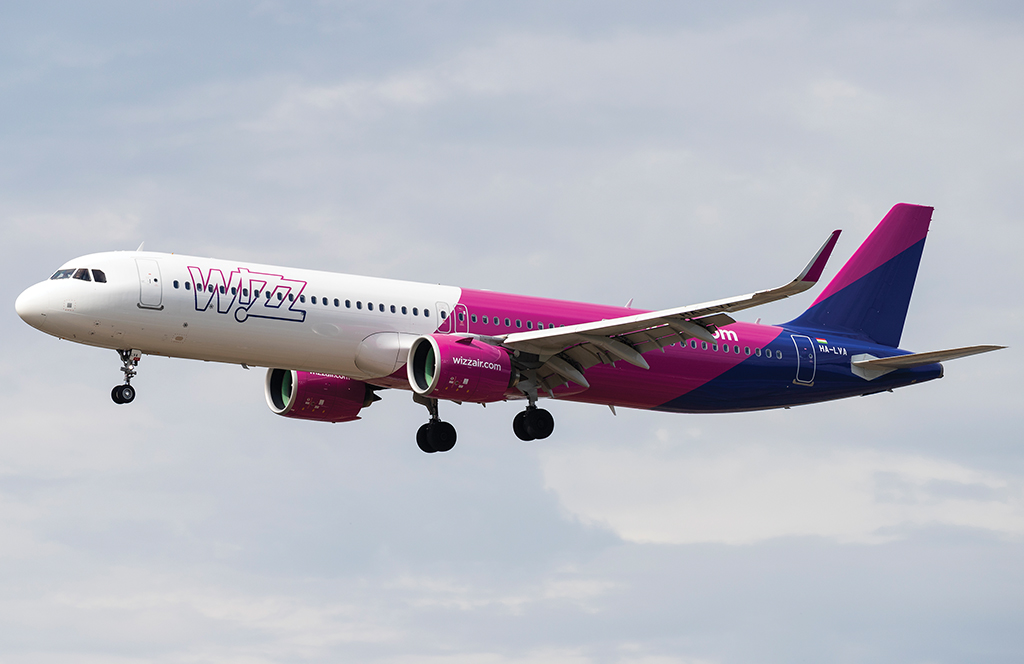
At Air Baltic, Zalkalns confirms that “there are ongoing supply chain issues with the Pratt & Whitney engines on the airline’s A220-300 aircraft,” but he cannot say when such issues will be resolved.
“The airline is in regular communication with Pratt & Whitney, and the company is actively working on mitigating the issue,” he adds.
To cut costs at the start of the pandemic, Air Baltic phased out its Boeing 737 and De Havilland Canada Dash 8 fleets while also terminating the associated maintenance contracts. But for airlines transitioning more gradually from older to newer equipment, another wrinkle in their planning has been delivery delays for new aircraft, requiring older aircraft and engines to remain in service longer. Often this requires more use of green-time equipment as well as adjustments to the management of deadlines such as end-of-lease checks.
Managing Life-Cycle Savings
To appreciate how airlines have adjusted MRO cost management, it pays to understand the factors driving these changes. Putting aside minimum safety and regulatory requirements, which are nonnegotiable regardless of any cost strategy, normally an operator will seek to minimize the life-cycle cost of aircraft and engine assets by performing additional repair or replacement work in the short term to guard against expensive problems in the long run. Likewise, during engine overhaul events the extra expense of a wider workscope and extensive life-limited part (LLP) replacement helps to protect long-term asset value and ensure simpler maintenance planning for the future.
“Generally, the objective is to continuously keep the engine total life-cycle cost front and center and make choices that optimize both cost of ownership and airline value creation, rather than looking only at short-term maintenance costs,” says Michael Grootenboer, senior vice president of engine products for AFI KLM E&M.
However, the approach outlined by Grootenboer went out the window for many airlines during the pandemic, when financial constraints forced them to focus on immediate costs rather than a long-term strategy—a shift in emphasis that will take time to unwind.
An easy way to cut costs quickly is to reduce workscopes during shop visits, thereby saving on labor and materials, albeit at the expense of settling for shorter on-wing times—and kicking the can down the road for a more expensive MRO visit in the future.
Many airlines have also opted to change the type of work performed for big-ticket items such as engines, IBA’s Seymour explains. “A scheduled full overhaul and LLP stack replacement tended to become a repair with targeted LLP replacement in order to reduce the cash expenditure. But that will result in a premature next shop visit since the build standard will have been reduced. The long-term cost per hour/cycle will have increased, but short-term cash-saving was the priority,” he says.
A quicker, cheaper alternative to a full engine overhaul is a module replacement, and there is evidence that these are becoming increasingly popular. Asset manager FTAI Aviation offers these for CFM56 engines and saw revenue in that part of its business rocket 156% in the second quarter of 2023.
“We think that it’s a great product if airlines really need to hunker down and focus on cost-cutting,” commented FTAI Aviation Chairman and CEO Joseph Adams on an earnings call.
Other adjustments have been applied to engines on long-term maintenance deals even when airlines have operated enough flight hours to initiate an overhaul, since many of these contracts exclude expensive LLPs from the cost-per-flight-hour rates.
“Even though an engine shop visit cost may have been accrued over previous years, it wasn’t always put through the full process without consultation between the parties to ensure that an acceptable build standard and turn time was achieved,” explains Seymour.
For airframe heavy checks the situation is a bit different, as many of the individual tasks are packaged together and it is not practical to carve them out into intermittent hangar visits.
Even so, airlines must also contend with longer turnaround times for maintenance due to a combination of labor and material shortages in the aftermarket and a rapid uptick in demand for checks from operators around the world. “Turnaround times for heavy maintenance are much longer; roughly they are doubled,” comments Air Baltic’s Zalkalns.
Airlines do retain some flexibility to defer certain parts replacements in cases where they can be accomplished in future overnight stops.
Parts Strategy
Across airframe and engine checks, airlines can also pursue savings by opting to install used serviceable material and parts manufacturing approval (PMA) parts and rely on designated engineering representative repairs.
“The result will be some compromise on the time on wing, but again, cash savings are the priority,” says Seymour.
Demand for such savings has only increased since the pandemic, as geopolitical events have fed into parts price inflation, which has long been a headache for airlines.
“Unfortunately, A220 component maintenance costs have been increased worldwide by around 15% on average, including the power-by-the-hour contract portion related to components MRO support services,” says Zalkalns.
Speaking to Inside MRO earlier this year, several PMA manufacturers noted that inflation was driving higher demand for their parts, as well as other factors such as supply chain bottlenecks for OEM equipment and the extended service lives of older aircraft due to new-build delivery delays.
Zalkalns now sees some of these problems easing, at least for Air Baltic. “There are some occasional challenges with parts suppliers that increase engine MRO turnaround times, but overall we see a positive trend for engine turnaround times improving, and it seems that the engine OEM has fixed the spare parts availability problem.”