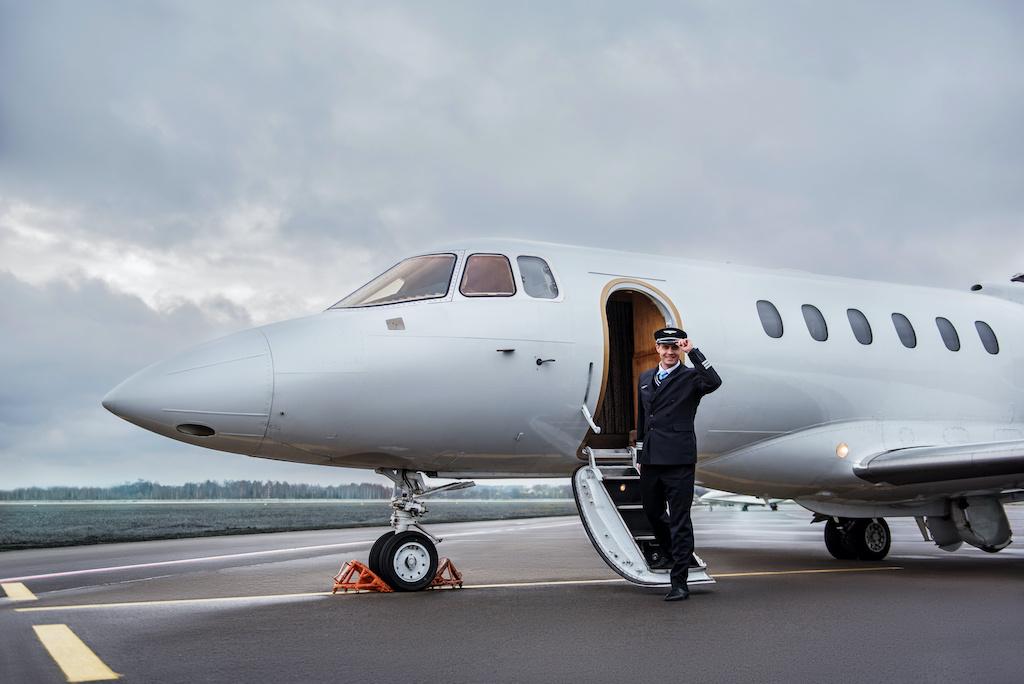
Editor's Note: This is the last article in a four-part series. Here's the first, second and third.
In an email following BCA’s interview with the anonymous chief pilot, the long-time aviator offered these perspectives on keeping an open line of communications between ops and maintenance:
“It is also very important for communication lines to flow in the other direction--that is, from maintenance to operations,” the chief observed. Three cases come to mind:
(1) Maintenance-initiated communication to crew. “This does not require a response from the crew; it’s just a heads-up alert to prepare for anything associated with the case at hand,” the pilot said. “Here’s an example: Maintenance changes a generator and lets the crew know it has been installed and tested. The crew now has an opportunity to review generator-out procedures as a ‘just-in-case’ fallback, rather than having the generator fail and catch them having to rely on knowledge that could be up to a year old.” It also places additional emphasis on preflight-monitoring of that system for the first few hours of operation as a health-check.
(2) Functional verification flights. “At a Boeing conference,” the chief continued, “I listened to a presentation by their chief test pilot on establishing safety parameters for functional verification flights. Boeing creates a grid of required conditions based on risk determined by what was done to the airplane.”
Example: Any flight control removed is rated a Level 5 risk. Therefore, the flight will only take place (a) during the day, (b) under VFR conditions, (c) within 50 nm of the airport and (d) only with essential personnel on board. At the other end of the spectrum might be a Level 1 risk, which could take place as a revenue flight. “This prompted our operation to have a discussion for establishing a baseline for any functional test flight and the required parameters thereto. For ETOPS operators, there may be a requirement to test a system in flight prior to entering ETOPS airspace that cannot be tested on the ground. We may be released to fly but must test the system, report back to maintenance control, and be released prior to entering ETOPS airspace [more than 60 min. from an adequate airport].” This requires coordination between departments (e.g., “What’s the best number to call you on in an hour?”), including additional fuel planning in the event there is a delay with the process. (See “Post-Maintenance Test Flying,” BCA, June 2016, page 49.)
(3) Ground functional checks. “Some maintenance departments have personnel/procedures for running engines and taxiing aircraft. Others will require pilots to perform those functions. It is essential for the two departments to coordinate for efficient use of everyone’s time, so the pilots don’t show up when the aircraft was supposed to be ready, only finding out it will be tomorrow or the next day.”
While the Aircraft Is Away
Pilots may grouse that when they’re away flying, the maintenance department may have nothing to do.
Au contraire, says Sean Bates, director of maintenance at Owens-Illinois’ flight department. “We also use the time while the aircraft is flying to catch up on any paperwork for maintenance that has been performed. The paperwork for the aircraft is vital to maintaining the value of the aircraft. We use this time to take care of any ground support equipment or hangar issues. The crew will text us if there are any changes in the schedule, and we watch Satcom Direct for tracking. Finally, we get a takeoff report for the last leg on Satcom Direct Pro (SDPro) and a further message when the flight is inbound.”
Before the flight departs, Bates and his maintenance team conduct a crew briefing, informing the pilots of any issues involving the airplane, how they were handled, and anything the flight crew should monitor. “I bring up ‘My CMP’ to acquaint them with the inspection status of the aircraft and any squawks or anything that has been worked on; we do this before every flight,” he says. “We also have a white board where we list issues we’ve attended to and whether any panels have been removed, or if the pitot tubes and static ports have been taped to wash the airplane, the tire pressures, whether the engine inlet covers are still on, and so forth.
“This keeps everyone on the same page, including us! We have a read-file system indicating if the weight and balance changes or there are notices to operators from the OEM, Jeppesen alerts, anything that could be critical to flight,” says Bates.