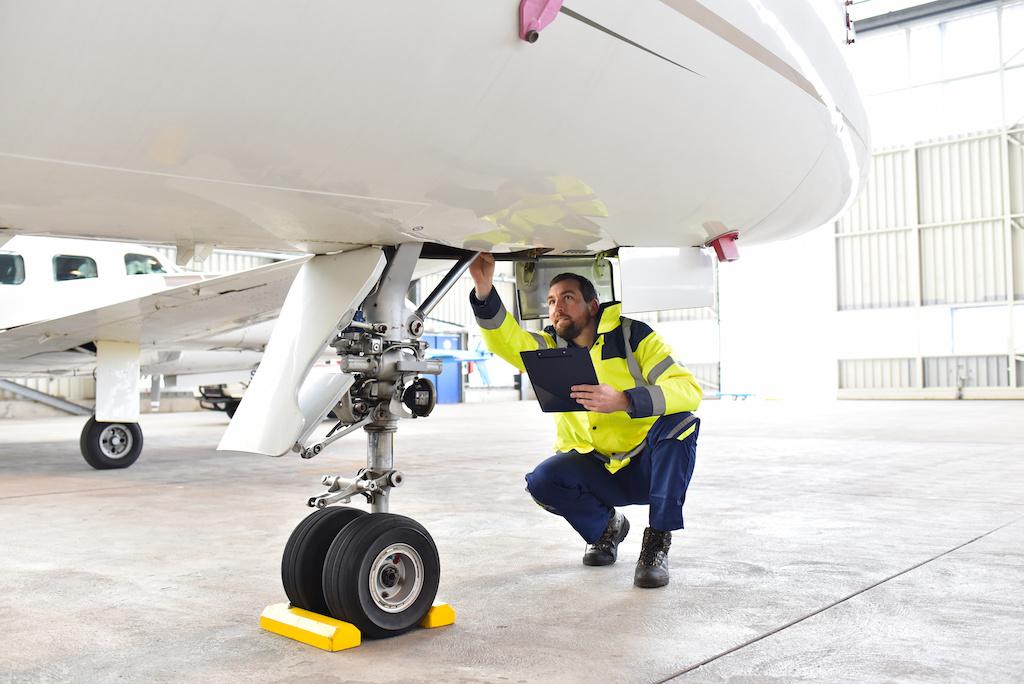
Editor's note: This is the first of a four-part series of articles.
At Qantas Airways, there has been a long-standing tradition among flight crews and maintenance techs of exchanging humorous rejoinders in post-flight (now digital) paperwork. For example:
Flight Crew: “Autoland inop.”
Maintenance: “Aircraft not equipped with autoland system.”
And that’s only a sample. But this repartee notwithstanding, it’s no secret that a rivalry has existed between pilots and mechanics, or maintenance technicians, since day one of professional aviation. As Dow Chemical Corporate Aviation’s director of maintenance, Chris Trautman, tells BCA, “Traditionally, the techs grumble: ‘When the flight comes in, they’re out the door and leave.’ And the pilots complain: ‘They never fix that [the glitch du jour] and just sit around the hangar all day when the flight is gone.’”
Of course, Trautman, who is in his 25th year as a director of maintenance and has seen it all, is making light of the time-worn competition between the people who fly the machines and those who maintain and repair them--that is, keep them flying. While both disciplines are dedicated to enabling safe, reliable air transportation, each harbors its own perspective of how to get the job done and, accordingly, lives in its own unique world.
“I think that to build a team that works together,” Trautman says, “the pilots and maintenance crews have to understand each other and their respective challenges. Time is our biggest enemy. A team has to understand everybody’s role toward the goal of satisfying the passengers, who are our customers.” This means being well-trained on the specific aircraft, “understanding what is deferrable on the aircraft and what is not, and most importantly, that communication is key.”
In Dow’s case, this is essential, as the FAR Part 91 flight department constitutes a fleet of Gulfstream 650 and 550 long-range business jets and a brace of Dassault Falcon 2000LXS super-midsizes. It employs 13 pilots and five maintenance techs, the latter under the supervision of Trautman. Additionally, the company operates an in-house Part 125 corporate shuttle service, fielding a pair of Bombardier CRJ900s on scheduled runs between Dow plant locations; it is set up as a separate entity from the Part 91 flight department. Finally, under its corporate aviation umbrella, Dow has established its own drone operation under the new Part 107 rule to conduct aerial plant inspections of stacks, roofs, tanks, etc., obviating the need for expensive shutdowns at those facilities.
Avoiding Silos
“It’s all about the working relationship with the pilots,” Trautman says by way of explaining his philosophy of maintaining two-way communication. “It’s easy to be a ‘silo’ and just say ‘I’m a maintenance tech, period,’ but it has to be a joint relationship. The maintenance guys have to realize that the pilots are as much a customer of ours as the passengers.”
If the flight crew can’t depend on the reliability of the aircraft and prompt maintenance response time, that ends up being a problem for both groups, which ultimately affects the passengers, Trautman believes. “Each side has its own challenges--and they are often on opposite sides when competing. The pilots go home after the flight; we see the airplanes as static entities, but on the road [the pilots] live another life, and the maintenance guys don’t necessarily understand that challenge.”
In a previous job with another operator, Trautman often accompanied the flight crew on trips, “and that gave me a different respect for what the pilots’ challenges were on the road--the challenges of being away from home. It’s good to have that perspective because you understand that, as a pilot, you are in your own world on the road, and that’s what you have to deal with, and the maintenance department is your lifeline. So, you have to have a team that understands that each side has its needs and has mutual respect for each group’s challenges.” Accordingly, he recommends that maintenance directors send their techs on flights--if company principals permit--“so they can see how that world works and come back with a different perspective.”
Having both groups--pilots and technicians--understand that running a flight department is a team effort “is where you begin breaking down the walls,” Trautman says. “In my career, educating the pilots is continuing education; they live with procedures day in and out, performing the same processes every day. On the maintenance side, our world is both dynamic and technical--dependent on the machine--so what we have to do is maintain that machine. Addressing it and its problems often does not conform to a list of procedures: It is dynamic by nature. It involves problem solving, troubleshooting, processes and procedures, and often it is unpredictable.”
At medical equipment manufacturer Stryker, Senior Manager, Flight Operations and Maintenance Greg Hamelink has had the “luxury” of both perspectives in promoting two-way communication between ops and MX. “I’m a pilot as well and an A&P,” he explained to BCA. “I’ve been a DOM at three flight departments over 20 years and have always been a proponent of open communication. I’ve always encouraged it and look at it as a team effort--we both need each other. We’ve bred this into our flight department from the start.”
In one of his previous postings, Hamelink says, there was an atmosphere of “a lot of animosity between the two groups, and I had to work for 18 months to solve that.” After that experience, open comm became a personal goal. “I understand the pilots because I am one, too, but I’ve had to encourage my fellow techs to keep the lines open to the flight crews. Techs ask pertinent questions to be informed and understand what the pilots are dealing with in flight. Those who have difficulty with this have to step back and understand where the other side is coming from. Without that, you are compromising safety and efficiency. We have a robust safety management system [at Stryker] where we can communicate issues and problems with a maintenance procedure or a flight.”
Riding the Jump Seat and Observing
Stryker operates a Bombardier Global Express and two Falcon 2000s and, in a normal year, flies them in excess of 1,500 hr. total, 20% of that internationally. The company employs 10 pilots and five maintenance techs, including Hamelink. “We perform as much maintenance as possible in house. We usually send a maintenance tech on flights to take care of passengers and the airplane, and this helps to promote good communication with the pilots. They ride the jump seat and observe.”
During the first year of the COVID-19 pandemic, Stryker restricted its air travel primarily to day trips to avoid restrictions at hotels in some cities. That is, flights were dispatched out and back in one day to avoid having to billet crew and passengers in hotels. “During the slowdown, we’ve been maintaining currency with short training flights, juggling crews so everyone gets stick time,” Hamelink says. “Also, this exercises the airplanes, which weren’t designed to sit on the ground or fly around the pattern incessantly.”
The Stryker flight department relies heavily on the latest electronic technology for internal communication. An example is the Flightdocs maintenance tracking program, which cross-communicates among desktop and laptop computers, smartphones and iPads. “So, when a discrepancy arises, it can be entered into Flightdocs and tracked while informing everyone in the operation,” Hamelink says.
"As an example, let’s say a generator fails and grounds the airplane, and that line of communication is visible to all the crewmembers when they log in daily. Maybe they didn’t know we had a failure, but when they come to fly, they get a briefing on the recent history of the airplane they’re scheduled to fly. They also see the corrective action--that we replaced the generator,” says Hamelink. And that they should keep an eye on it, as a recently serviced essential component, to ensure it’s functioning properly.
Or maybe a CAS (crew alerting system) message, a fault, comes up during a flight. “So, the crew might clear it with a power cycle [i.e., rebooting the relevant system], but the incident is captured for future reference, as it might pop up again. The bottom line is that this a form of communication, an electronic one. You can write a message on paper, too, but with electronic messaging, crews and techs can get it, even if they are at home, and prepare accordingly. They can question it then, too, if necessary.” (This brings to mind enterprise software, where everyone in an organization who has a need to know is copied via message or in a relevant data flow.)