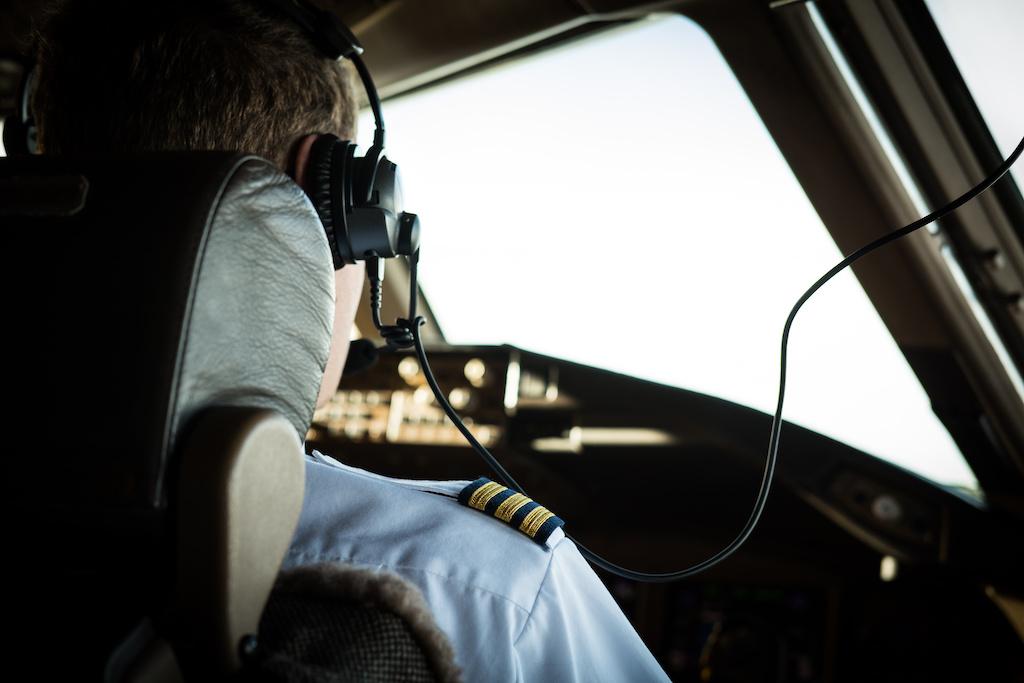
Editor's note: This is the third in a four-part article series about improving communications between pilots and maintainers. Here is the first part and second part.
So far in this story, BCA has reported from the maintenance side of the typical business aviation operation. Now, we will provide an operations perspective, in this case, from the chief pilot of a major U.S. charter/management company overseeing a large fleet of midsize and long-range business jets as well as transport-category aircraft. In addition to performing FAR Part 91 operations on behalf of its owner-clients, this company holds Part 135 and 121 certificates for charter and long-term contract operations. Both the pilot and his employer asked for anonymity.
When the pilot signed on with this company more than two decades ago, he says, there was a “running joke” among the ops department: “Our pilots could be handed a box of parts and build an airplane. There was no support network for business aviation in the countries we went to when the company started flying jets. We were the first into Beijing and initially were handled by Air China. So, we had to know the airplane so that when a problem came up on the road, the pilot became an ‘informed reporter’: The mission was to get the airplane airworthy while inconveniencing the customer as little as possible.”
By being informed about the airplane, the pilots become an active participant in reporting and solving problems, the chief says. “Sometimes this is welcome, and other times it is not.”
Pilots were trained to call the maintenance department to arrange getting parts and getting the airplane fixed when something broke “or whether we could move it to where it could be fixed. If you are in a foreign country, getting parts in there can be a showstopper. Sometimes a mechanic would be dispatched with the part with instructions that it was not for importation to avoid customs duties,” says the chief pilot.
With proper training, the flight crew can coordinate work at a remote site. Among the multiple reasons for ops to keep an open line to the maintenance department, the chief points out, “is so a crew can call home, explain the misbehavior they’ve witnessed, and coordinate local repairs. This way, they can participate in the diagnosis and possible repair. Maybe they could have seen something that could save everyone a lot of work. For example, we had a situation where an engine on a Hawker couldn’t be shut down at the trip destination. The problem turned out to be an improperly calibrated fuel scheduling unit, and the solution was a simple readjustment with a screwdriver.”
Another example of a malfunction away from home involved a bleed valve that was closing prematurely. “Because we [the flight crew] had studied the airplane, when maintenance suggested that they were going to change out sensor A, we suggested that it would be a good idea to also have sensor B sent to us, just in case the problem would be the B sensor and not the A one. The B sensor would cause the valve to close at a lower temperature, and maintenance agreed, and it turned out to be the B sensor that was causing the problem, and we swapped it out and flew away. In another case, a pitot tube on a Boeing had to be replaced, so one pilot looked for the part and the other looked for a lift to get it 30 ft. up to the vertical stab where it’s mounted.”
Communication Can Avoid Expensive Oversights
Yet another example of why the flight crew might want to “have a conversation with the maintenance department” about diagnostics is illustrated in this story the chief pilot claims he’d heard about an AOG at a faraway destination: “A mechanic was dispatched to Australia with a display unit for a Gulfstream IV, and when he got to the airplane, he applied power to the unit and turned the brightness knob up and--voila!--solved the problem!”
Apropos to on-site diagnoses, the chief points out, the minimum equipment list (MEL) stipulates that the pilot may perform “certain maintenance procedures” if they do not require specialized knowledge or tools. “So, there may be a procedure that requires maintenance coordination, but others may perform it if it falls within those parameters. This may be as simple as pulling and collaring a circuit breaker. Thus, we can pull and collar a breaker in coordination with the maintenance department. Otherwise, someone has to come and do that from the maintenance department--silly, if you have the option to do it on site under the coordination with the maintenance department.”
The continuous back-and-forth between the chief pilot’s crews and the company maintenance technicians has led to backups to support work on the road and especially abroad. “We have a ‘fly-away kit’ we carry on our larger aircraft--400 lb. of tooling in a steel box--so our mechanics [dispatched to a grounded aircraft] don’t have to bring that many tools with them to work on the airplane in the field. It’s like taking the tow bar and a built-up spare wheel and tire. This derives from conversations with maintenance to learn what we need to take to the far reaches of the planet.”
In the “old days,” the pilot says, “one of the most-critical components of the Gulfstream IV was the electrical converter, so we carried a spare under the forward couch [in the cabin] whenever we went on a foreign trip, just in case. Gulfstream publishes a ‘top-20 removal list’ of parts that have had to be replaced during the previous calendar quarter on particular models. At our operation, we use that list to help focus ground school. For each item, we ask what we would do if [the designated part] broke on the ground or in flight.
“For the ground case, the question is, ‘Is it deferrable?’--that is, am I grounded, or can I fly? That then fosters a comprehensive discussion of how it works and how losing it in the field would impact the operation. Finally, the ground instructor might coordinate with the maintenance department to learn how hard it is to obtain any of these parts.”
This gets dicey for parts on older airplanes that might have to be obtained on the secondary market. The tabletop ground-school exercise described above “helps us in how critical it would be [to have] hard-to-get parts before we need them,” the chief says. “It also helps identify issues with aging aircraft like the GIIB we used to operate. The example here is cabin windows that would begin to fail at a certain age and, thus, be ranked up on the quarterly removal list.” The flight department ordered several new ones to be safe.
It’s About Respect…
Finally, and most important for this discussion, communication can lead to mutual respect and camaraderie within a flight department or commercial operation. Or in the words of our unidentified chief pilot, “Two-way communication fosters a companywide approach to fixing problems. It fosters mutual respect. We recognize that if the maintenance tech does his or her job, it makes my life easier: Their job is to keep me alive, and I have the greatest respect for that.”
Greg Hamelink, Stryker’s senior manager, flight operations and maintenance, agrees and advises that other directors of maintenance and their technicians develop a rapport with pilots. “Don’t start off on an adversarial note. Gain their trust so they know what you’re talking about and they can explain a problem to you. Have a frank conversation on working together and reminding both sides they need each other and have to work together toward the common goal of making the flight seamless to the passengers. When you’re not seamless is when you have issues, flights get canceled or delayed, and the passengers are upset. And then you have to answer the question from the principal: ‘Why weren’t you proactive?’ Make communication effective. It is being driven home with SMS [safety management systems] all over the industry--stuff we’ve done for years but haven’t documented. Effective communication makes your operation safer.”
Chris Trautman, Dow Chemical Corporate Aviation’s director of maintenance, suggests having a dedicated communication channel. “‘This is how we communicate for this issue, on this device, and how we share it amongst our group.’ You have to define your processes so each can interface with the other seamlessly, efficiently and consistently: the process, the technology and an understanding of what has to be done. You have to be clear on expectations in terms of each discipline,” he says.
Sean Bates, aircraft maintenance and facilities manager for glassmaker Owens-Illinois, provides a list of his guidelines for maintenance directors and ops managers seeking a more productive and mutually respective relationship between pilots and technicians. “The ops manager and I did a lot of work to get the maintenance team and flight crews working together. Each has to respect what the other brings to the table” because “none of us can do this job without the other--without them there is no us.” His advice to other directors of maintenance:
- “Be mindful of your tone and communication with flight crews--it’s easy to get sarcastic if they’re not giving you the information you want. Don’t put them on the defensive when you’re trying to get that piece of information you need.”
- “Ignore stereotypes, and see the flight crews for what they contribute: One pilot may offer to help us clean the aircraft after a trip, another may be a pain but works his butt off to fly successful trips.”
- “We all have egos: ‘That airplane is our baby, and when someone brings it back with a problem, that’s like telling us we have an ugly baby.’”
- “Take the time to train them [the pilots] in what you’re looking for. One of the big things I got hung up on early in my career was that crews would come back and tell me what was wrong with the airplane when what we are looking for are symptoms of what the airplane is doing as opposed to what it should be doing.” Context is everything.
- “Don’t assign blame--get facts and present the findings. After we work the squawk, it’s easy to lay blame, so present it in a manner that doesn’t assign blame.”