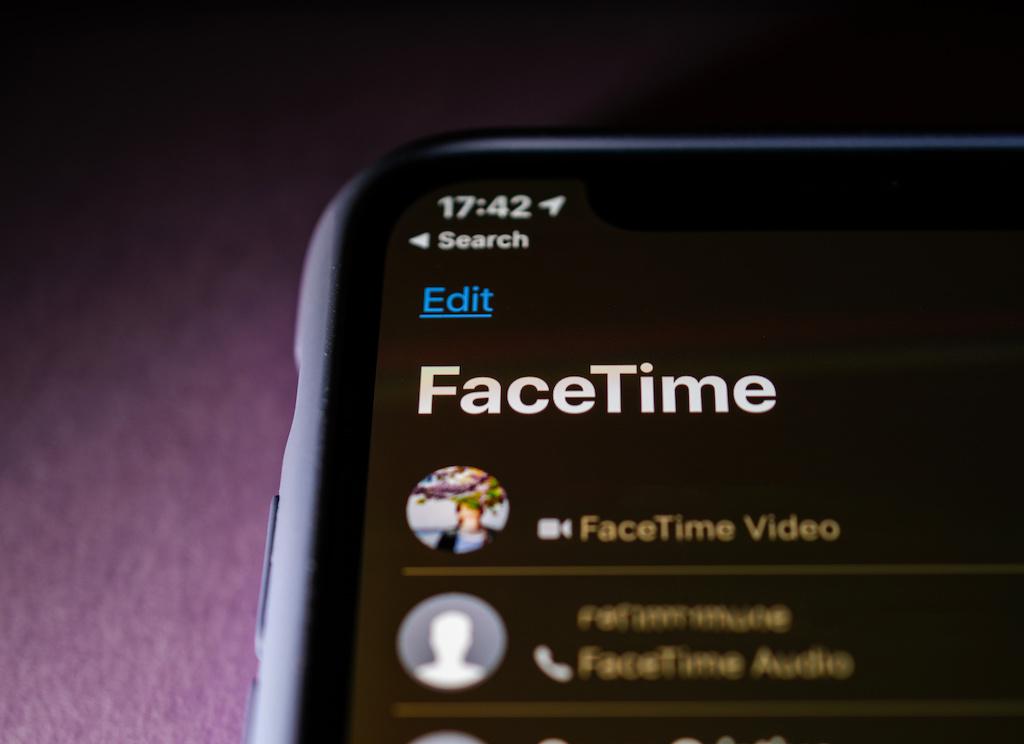
Editor's note: This is the second in a four-part article series. Here is the first part.
Using smartphone apps can improve communication between pilots and maintainers.
“I use the phone to photograph stuff like engines or systems to attach to emails to crews and techs. My kids think I’m crazy for having all this ‘weird stuff’ on my phone, but pictures are worth a thousand words. Same with crews: They often capture stuff on the cockpit displays with their phones to send to maintenance and communicate with other pilots so everyone is informed,” says Greg Hamelink, Stryker’s senior manager, flight operations and maintenance.
Reminding readers that a contemporary airplane is now “a computer with wings,” Hamelink points out that a “glitch” on a flight requiring a reset can be electronically tagged as a “watch-list” item that could be an anomaly or something that the onboard maintenance computer missed. “We track that with the maintenance program and leave it up for a month for the flight crews’ information, although after that, it is still retained in our database in case it comes up six months later. You can make a judgment call then--should we do something or refer to the OEM? It could be a fleet-wide problem. We use it as a learning tool, too. We are all carrying around these little computers on our hips, so why not leverage this technology.”
And aircraft “talk” now without flight crews having to do anything. “We trend-monitor our engines,” Hamelink says, by way of example, “and we get an email when the wheels leave the ground with all the relevant data on the engines. We have onboard diagnostics on the Falcons. At 18,000 ft. on descent, I get an email from Falcon Broadcasting [a subscription service that uses datalink to communicate data from the onboard maintenance computer on the aircraft] on everything that has happened on the flight. We have the visibility now to see everything that is happening on the airplane. When the aircraft departs for home, the pilots hit the ‘Pilot-Event’ button, and I get a report. If there’s a CAS event, I can question the crew in terms of what they’ve done in response. It keeps all of us in the loop and forces us to communicate.” He says it has also helped develop a camaraderie between maintenance and the pilots.
Chris Trautman, Dow Chemical Corporate Aviation’s director of maintenance, is keeping everyone in his flight department on the same page with electronic tablets. “We have electronic maintenance records, and everyone has been issued a company iPad,” he says. “The status of every maintenance action can be communicated via the iPads. So, every single maintenance function is electronically ordered and documented: discrepancies, the do-list--90 days out, and after that, archived--and historical data for each airplane, as much as anyone would want to scroll. That’s the first level of communication with the flight crews.”
But Trautman and his team still believe in the power of face-to-face communication. “So, the next level, after the pilots have done their flight briefing at home and arrived at the hangar is to have a conversation with the designated ‘flight handler.’” This is a technician assigned to a specific flight who serves as a single point of contact for the crew operating that trip. Also familiar with the specific aircraft assigned to the trip, the technician will brief the pilots on any deferred items affecting it. The purpose of the resulting collaboration is to review any work that has been performed on the airplane and if there are any actions the pilots should perform once aloft, e.g., a VOR check.
Also, the flight handler will inform the crew of any company cargo or passenger personal items that should be packed on the airplane. There will also be verbal reminders, such as draining water from the lav if the airplane is slated to be parked outside overnight, if the battery should be removed overnight for a flight headed somewhere in freezing temperatures, or certain procedures to be attended to if the aircraft will be sitting on the ground for more than seven days.
FaceTime on the Road
“When they’re on the road,” Trautman continues, “we use a cellphone that is passed along from flight handler to handler per shift for a given trip. We also purchased iPhones so pilots could use FaceTime with the flight handlers to diagnose problems when they come up.” Pilots can also text through the aircraft’s WiFi system. On inbound flights, 15 min. out, a text is sent to the handler’s phone with the ETA and any specific instruction for passenger or aircraft needs on arrival.
Electronic communication has also supplanted the ink-and-paper post-flight write-up. “It’s amazing what you might see in a write-up,” Hamelink observes. “With the technology, we can see [a problem] coming up all over the department. The obscure write-up is now permanently in the past because we now have the technology to elaborate on the subject, and I don’t have to wait until the flight gets back to base to figure it out. It gives us the details.
“On the other hand,” he continues, “I once had a pilot who gave us too much information--we need the relevant details of the glitch, not a novel. We have the beauty now of having it all on an iPad and can do research before we ever talk to the [flight] crew. We have so many more tools now than we had in the past. It ties us to each other 24/7. So, there is always the minimalist and the other one who tells you how to build the airplane. But the tools allow us to understand each other correctly. We are always looking for that happy medium,” says Trautman.
But the real test for effective communication between the pilots and the technicians who maintain their aircraft is how the operation handles breakdowns on the road--especially on international flights. “My biggest gripe is lack of reporting problems,” Trautman says. “If they [the flight crew] don’t tell us, we don’t know what they need or how much time it will take to set out a work list. They may receive a CAS message but not understand the background of it. They only see the surface of the system, only what the aircraft tells them, not what is beneath the alert or advisory message. So, they get only enough information for what they need to do, not what’s really wrong or how to fix it.”
And if the crew doesn’t report it right away, maintenance may lose a lot of time to plan for parts ordering and receiving and devising a repair plan. “This becomes a massive challenge if there is a problem on an international flight,” Trautman emphasizes: “customs issues, arranging maintenance support in a country where you don’t speak the language, and so forth. We do have meetings with the pilots, though, so they understand the urgency of reporting discrepancies.
“If we have a flight on the ground six time zones away and the crew didn’t promptly report a problem--for example, with an engine--they need to understand there is analysis that needs to be done,” he continues. “These time zone differences can play havoc with the work schedule back at base, and time is our biggest enemy in maintenance. We run two shifts a day here from 0600 to 2330 or midnight, plus overtime, if necessary, to adjust for a problem with a flight.”
A tactic the Dow operation has come up with to address analysis of inflight problems is to have pilots photograph CAS messages with their phones and attach the images to a cloud-based maintenance tracking system as part of the description of the discrepancy. Received at home base, the photo and message are historically logged in case the message comes up again. “It’s a snapshot that includes all the operational parameters--how the aircraft is flying--that MX can use for analysis,” Trautman says. “We use the photo in conjunction with aircraft health monitoring to determine courses of action.”
Sean Bates is aircraft maintenance and facilities manager for glassmaker Owens-Illinois, which employs five pilots and three maintenance technicians (including him) and fields a Gulfstream 280 super-midsize jet. “After the flight is dispatched, we are on call if anything goes wrong,” he says. “We also do a debrief after the flight and try to get as much information as we can. An early gripe was that the crew would disappear, and that night I’d get a call that there was a problem; the post-flight debrief has pretty much eliminated that. Now we get a positive handoff of the airplane back to the maintenance crew.
“We did three trips to Germany in the last 12 months,” Bates continues. “On one of the returns early this year, there was a pitot failure (thankfully at a decent time for us here at home), so the crew called and asked us what to do. This was at the height of the COVID pandemic, so our options for a drop-in were limited. I got on the phone for maintenance scheduling with Gulfstream, and they arranged for the flight to divert into Farnborough [U.K., EGLF]. Gulfstream gave us several options, and Farnborough was the best for being able to do the work on that day.”
So, the G280 crew diverted to Farnborough and parked the aircraft at the executive FBO operated by TAG Aviation, and Gulfstream did the fix. “It was a little weird to just drop it there,” Bates says, “but Gulfstream did the work with a replacement part and a follow-up check. They then alerted the crew to come and pick it up. Altogether, it took just over a day, and the crew departed for the U.S. the following day.”
Probably one of the most nerve-wracking inflight glitches Bates and his technicians had to deal with involved a Gulfstream 450 the company formerly operated. In 2010, headed to Europe, the aircraft experienced the failure of a modular avionics unit over the North Atlantic at approximately 30-deg. west longitude. “Of course, the crew called me on the satphone to report the problem, and then I got on the phone with Gulfstream,” Bates says, “and they recommended pulling breakers to isolate the failure and reset it. That solved the problem.”