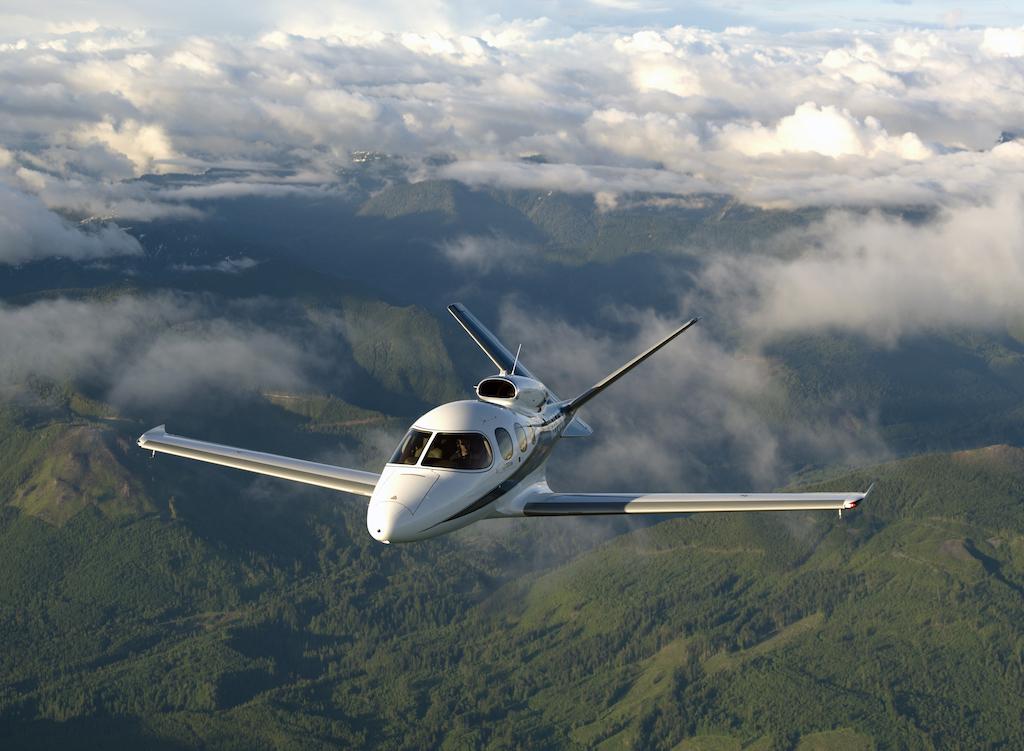
Like most aviators, I tend to focus primarily on my niche of aviation and perhaps I pay a less attention to things that are outside my day-to-day interests. I am aware of many of the innovations in military fighter aircraft, for example, but I would be hard pressed to tell you why an F-22 Raptor can defeat an F-35 Lightning in air-to-air combat or if there is anything like air-to-air combat these days. In a similar vein, while my primary interest is in passenger-carrying aircraft, I can tell you more about recent-generation Gulfstream, Bombardier and Dassault business jets than about Boeing or Airbus airliners. I do, however, pay attention to innovations throughout our industry that can be game changers for all aviation, and that is how I became interested in Cirrus.
Cirrus Airframe Parachute System
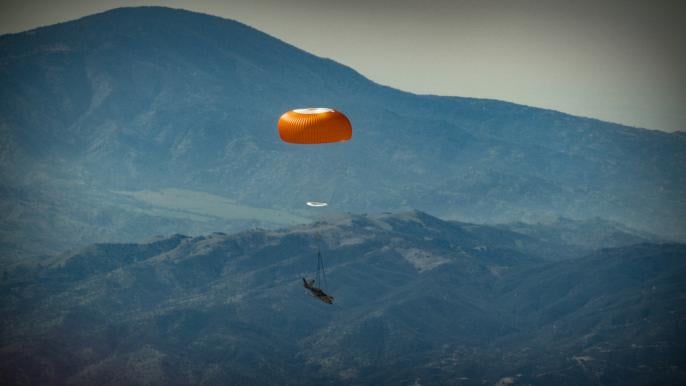
Many of us were introduced to Cirrus Aircraft and its SR20 and SR22 piston-engine aircraft because of the Cirrus Airframe Parachute System (CAPS), the first FAA-certified whole airframe parachute system. In the event of an emergency, the parachute lowers the aircraft to the ground in a level attitude designed to keep its occupants unharmed. Since its introduction in 1999, CAPS has saved more than 200 lives.
As incredible as it may seem to have a parachute for a 3,600-lb. SR22, Cirrus included a larger version for its 6,000-lb. Vision Jet. Cirrus Aircraft was awarded the 2017 Robert J. Collier Trophy for “developing the world’s first single-engine personal jet and implementing the Cirrus Airframe Parachute System (CAPS) on the aircraft.”
The Personal Jet
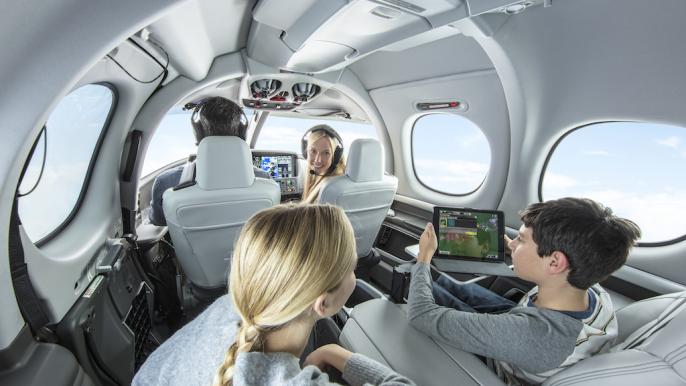
Cirrus Aircraft quite boldly claims its Vision Jet is “The Personal Jet Defined”--and for good reason. It has carved out a niche of the market that didn’t exist before but now appears to be here for good. Are there any competitors out there that can beat its performance? The Vision Jet can carry five adults and two children 1,275 nm at 240 kt. or 1,100 nm at 305 kt. Oh, and by the way, it is a jet. With more than 260 aircraft delivered since 2016 and a production rate of 80 new aircraft per year, the industry has taken notice. Commercial customers have discovered the value of the Vision Jet as a charter aircraft and that has caught my interest as well.
Safe Return Emergency Autoland
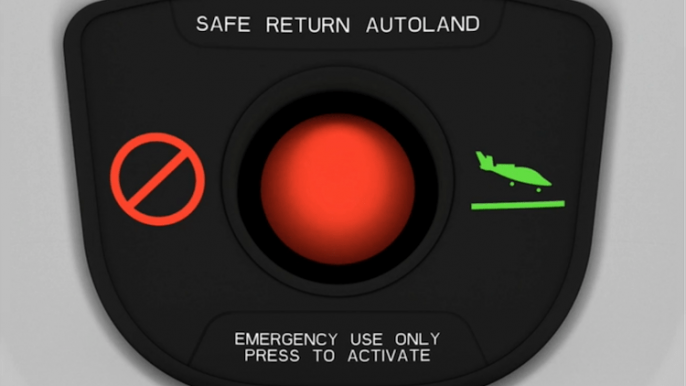
In 2019, Cirrus added Garmin “Safe Return,” a revolutionary emergency autoland system that enables passengers to land the Vision Jet with just the touch of a button in the event their pilot is incapacitated. Once activated, the autonomous system analyzes terrain and data-link weather to determine the optimal airport for landing, and simultaneously communicates with air traffic control (ATC). The system considers available fuel and weather when selecting an airport and transitions to final approach for the appropriate runway based on ground winds. Safe Return uses the automatic flight control and autothrottle systems to manage the aircraft’s speed, altitude and path, and then automatically lowers the flaps and landing gear on final approach, lands the airplane, brakes to a stop, and shuts down the engine. Through it all, the system keeps the passengers informed with flight progress and can even help them to talk directly to ATC.
As Matt Bergwall, Cirrus Aircraft’s director of the Vision Jet product line, said, CAPS will save you if anything goes wrong with the aircraft; Safe Return saves you if anything goes wrong with the pilot. Clearly the company has safety in mind. I had to find out more. Bergwall invited me to Cirrus’ Vision Center Campus for a tour and to fly the recently announced Vision Jet Generation 2 Plus.
The Vision Center Simulator
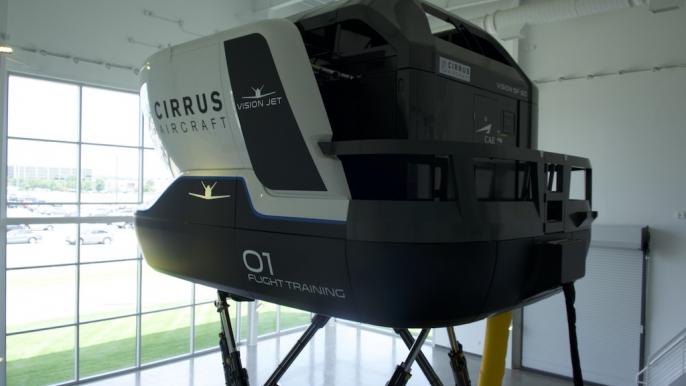
The Cirrus Vision Center is at McGhee Tyson Airport (KTYS) in Knoxville, Tennessee. While the aircraft is manufactured in Duluth, Minnesota, the training center in Knoxville is home to classrooms, flight training devices and a full-motion simulator. Instructor Matt Manifold took me through a short session to see normal flight procedures, steep turns and stalls. The aircraft flies conventionally, with a mechanical sidestick connected to ailerons and the distinctive V-tail. Once we finished, Manifold asked if I felt like seeing the CAPS in action. “Absolutely.”
I had already seen several YouTube videos of CAPS in action with the SR22 piston-engine aircraft and a Cirrus presentation of a test done on a Vision Jet; the simulator gave me an even better view. The one-step procedure is simple: Pull the red handle. The aircraft pitched up briefly to improve our airspeed and attitude for the parachute to eject from the nose of the aircraft and deploy itself. The front strap was immediately in view from the cockpit as two other straps cut through specially designed carbon fiber panels to their anchor points near the wing. Once all three straps were taut, the aircraft returned to a level attitude as we descended at about 1,000 fpm. “Gear?” I asked, as I watched the terrain rise. “No,” Manifold said. “We keep the gear up to prevent puncturing the wing and risking a fuel leak when we contact the ground.” While the force of impact is lessened in the simulator, in actual use it has been more than survivable. In the case of the SR22, whenever the parachute system has been deployed within its envelope, there have been no fatalities and more than half the aircraft have returned to service. Even when deployed at too high an airspeed or too low an altitude, the system has a remarkable record of success.
Pulling that red handle is obviously left for times when no other options are left. CAPS is standard equipment on all Cirrus aircraft and training includes courses in Aeronautical Decision Making (ADM), the system itself, preflight procedures, how to deploy it, and what to do post-deployment.
Training
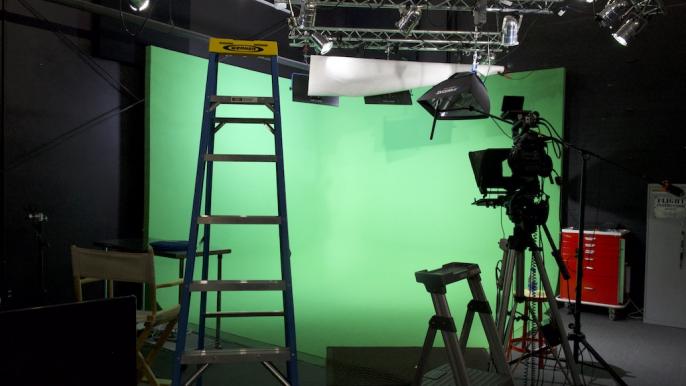
I was treated to a series of training videos designed to bring new Vision Jet pilots up to speed. Every video seemed to come right out of a Hollywood studio. Anthony Bottini, Cirrus Aircraft director of media productions, emphasized that their goal was to keep every Vision Jet pilot well- trained and eager to learn. The videos far exceed anything I’ve seen from the training vendors I normally use. Bottini said everything from the classroom to the simulator, to ongoing online training is designed to provide a “clear path to success.” Of course, I come from another world: a world of heavy iron where most of the pilots have long resumes of multi-engine, instrument and international jet experience. We tend to be easily jaded by FAA-choreographed syllabuses designed to crank out pilots in large numbers by instructors who do nothing but teach in the classroom or in the simulator. Cirrus does all of this “in house.” From the minute I walked into the training center I realized I was in a different world. It has to be.
The vast majority of new Vision Jet pilots have a private pilot certificate with an instrument rating and will be earning their first type rating. As of this writing, 550 pilots have been trained. Cirrus has also trained a few FAR Part 135 pilots as the Vision Jet has now entered commercial charter service.
The course begins with a flight with an instructor to evaluate instrument skills and design a student-specific training program. Then, at-home training materials are used to allow each student to learn at their own pace. The on-campus training is planned for 10-14 days with five simulator sessions and a check ride. A “Jet Readiness” course is optional but is usually taken by most students. The initial pass rate is about 85%. Once the course is completed, pilots are awarded a type rating with a requirement to fly with an instructor for 25 hr. Cirrus provides a mentorship program designed under Part 142 to remove that Part 61.64 restriction. Classroom and simulator instructors double as mentorship instructors. This is very different from the philosophies of the “name brand” trainers, which tend to stovepipe instructors into specific roles. This ensures every instructor has recent and real-world experience.
Flying in the ‘Real World’
I finished my visit with a flight from Knoxville to Boire Field (KASH), Nashua, New Hampshire. Weather for our departure was almost VFR, for en route it was often IFR, and for our arrival we would be near minimums. In other words, it was a perfect test to demonstrate the aircraft’s IFR flight chops. Bergwall completed the preflight of our “Generation 2+” aircraft as I looked on.
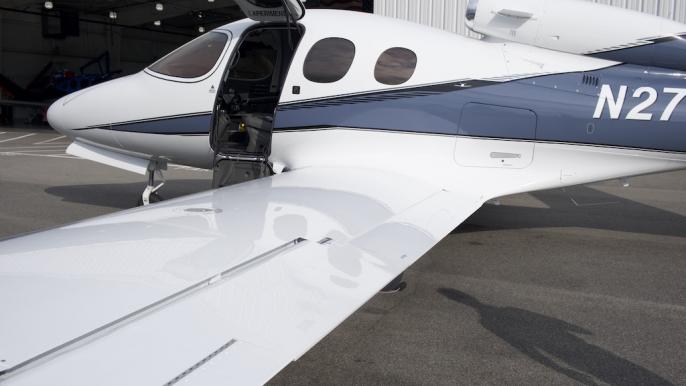
The large clamshell cabin door is on the left and an emergency egress window is on the right side of the aircraft. The pilot’s seat moves well out of the way to provide easy access to the two rows of five seats behind the front two seats. The aft five seats and a center console are of modular design, offering users the ability to customize the configuration for each flight. Turning the two battery switches on allowed a quick check of the avionics and other systems, as well as the fuel on board. We had a full load of 296 gal. of jet fuel, which is automatically fed from integral tanks in each wing.
The aircraft is 30 ft. long, has a wingspan of 39 ft., and the tail is 11 ft. high. Standing in front gives a good view of the engine inlet. The Williams International FJ33-FA engine is mounted above the fuselage and produces 1,846 lb. of thrust. Most of the aircraft is manufactured from carbon fiber and the wing structure is seamless. Aluminum ailerons and flaps trail the wings. Preflight inspection of control surfaces, wheels, brakes and tires is typical for an aircraft of this size. On the left side, the inspection includes checking the security of a baggage compartment door.
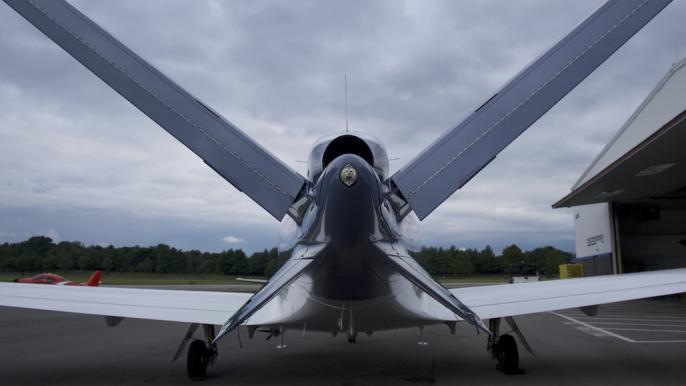
An aluminum V-tail ruddervator mechanically mixes stick inputs to produce pitch and yaw forces. (The ruddervators deflect symmetrically for pitch control and in opposite direction for yaw control.) All primary flight controls are connected to the control sticks and rudder pedals mechanically using cables, pulleys, bell cranks and push rods. Two carbon-fiber ventral fins mounted below the ruddervators are controlled by a yaw stability augmentation system designed to provide a smoother ride.
Inspection of the right side of the aircraft mirrors the left, with the addition of access to an engine oil inspection port, a 3-gal. windshield ice protection system fluid reservoir and an angle-of-attack vane. The nose has a spray nozzle for the deicer fluid and an enhanced vision system (EVS) camera. A thorough external preflight can be completed in just a few minutes.
Editor's note: The subsequent article about James Albright's flight appears here.
This article was first published August 21, 2021
Comments