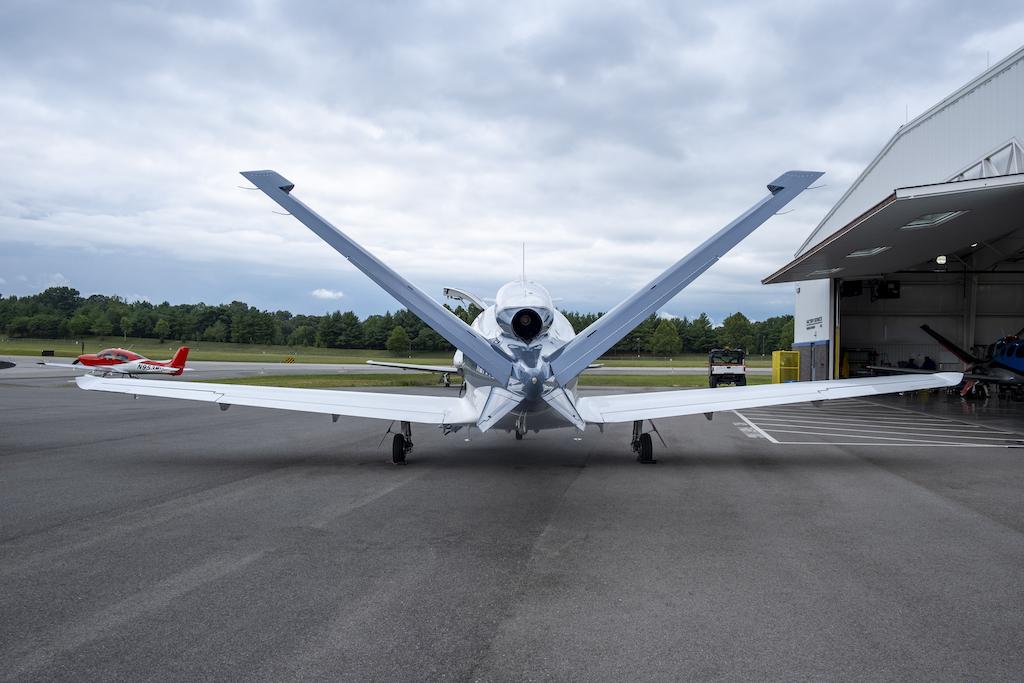
Editor's note: James Albright's article about preparing and training for flying the Cirrus Vision Jet appears here.
Strapping into the left seat of the Vision Jet, I was treated to my first look through the largest pilot’s windscreen I had seen since my days flying bubble canopies in the U.S. Air Force. The view is not only wide (at least 200 deg. left to right) but also provides good visibility forward from low to high. Two 14-in. color landscape-oriented flight displays--a primary flight display (PFD) and a multifunction display (MFD)--fill most of the instrument panel. Below them are three touchscreen controllers that round out the “Cirrus Perspective Touch+” system by Garmin.
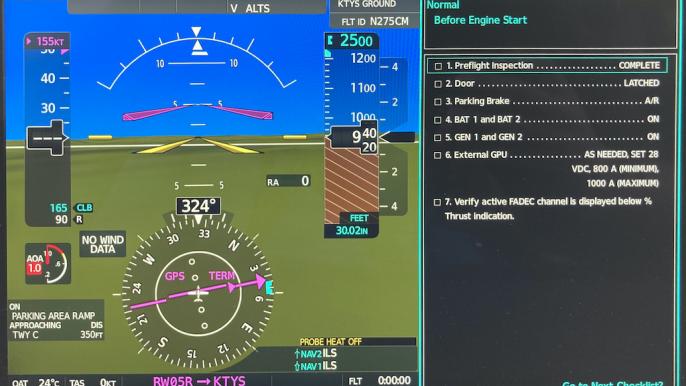
An external ground power unit is rarely needed, and we were ready for engine start just a few seconds after turning the battery switches on. Turning a knob to the “run” position and pressing the start button allowed the full authority digital engine control (FADEC) to control and monitor the start. The engine produces a pleasant hum, which I am certain would delight anyone more used to a piston engine’s rumble, but the fact it is mounted just behind and above the fuselage means a bit more noise in the cockpit. The aircraft is 14 CFR Part 36 Stage 4 compliant, with a maximum noise level of 80.3 during a full flap approach.
A press of a button below the PFD activates an electronic checklist that makes quick work of all checklists. My first challenge was to learn to taxi using differential braking. I imagine that if you are used to taxiing an aircraft without nosewheel steering and a free-castering nosewheel, you will be at home with the Vision Jet. I am not and had to rely on frequent brake application to point the airplane where I wanted it to go.
Takeoff and Climb

The aircraft’s performance computer figured our takeoff weight to be 5,958 lb. and predicted a ground roll of 2,700 ft. on Runway 23L, which is 9,000 ft. long. Bergwall went through a departure briefing, which was novel to me but nicely summarizes the safety capability of the aircraft. “If we have any failures before Vr, apply brakes and then bring the throttle to idle. For an engine failure after that point but before 600 ft., land straight ahead. For an engine failure above 600 ft. but before 2,000 ft., pull the CAPS T-handle. Above 2,000 ft., establish best glide speed.”
Once on the runway and cleared for takeoff, I pushed the throttle beyond its first detent to full forward and allowed the FADEC to ensure we had 100% thrust for takeoff. At 85 kt., I pulled back on the stick and watched as the nose obediently climbed to about 5 deg., just inside the flight director’s “V-bars” set for the takeoff rotation. I called for “gear up,” but Bergwall reminded me, “You can get that.” Oh yeah, single pilot.
Considerable nose-down trim is needed during acceleration after takeoff. While electric trim is available on the stick, I found the manual trim wheel more responsive. At 115 kt., I retracted the flaps and a few seconds later reduced the throttle to maximum continuous thrust (MCT). I continued to hand-fly until we approached reduced vertical separation minimum (RVSM) airspace and let the autopilot take over.
The climb to FL310 was comfortable and took about 28 min. in ISA+15C conditions. The view from the pilot’s seat is spectacular, almost like flying in a glass bubble. The PFD provides just about all the information you need plus a feature I haven’t seen before, something Garmin calls the “pathway” of its synthetic vision system. The pathway provides a series of small magenta boxes starting at infinity, which grow in size as you approach, providing a tunnel visual effect of where the desired course is. While the PFD uses conventional aircraft and flight director V-bars, a flight path marker (FPM) is included. Keeping the FPM flying into those magenta boxes provides assurance you are headed in the right direction.
Cruise
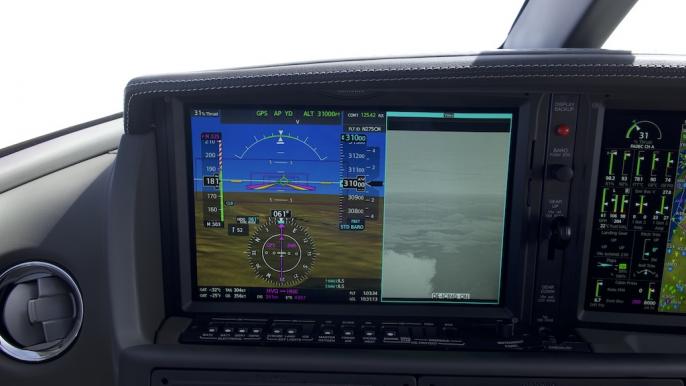
With the engine thrust set at MCT we were still well below our maximum velocity and there was little to do other than talk on the radio and ponder the weather. During one of our frequency changes I got one of the digits wrong. Bergwall hit a “Replay” button on one of the touchscreen controllers and we heard a repeat of our frequency assignment again. That is a neat feature I’ve not seen before.
As we burned fuel at 60 gal. per hour the aircraft gained speed. “Why not pounds per hour?” I asked. “We want to keep it familiar for those coming from pistons,” explained Bergwall.
That is a recurring theme in the Vision Jet. The cockpit will be an easy transition from the Cirrus SR22. Many of the switches and instruments are in the same position; even checklist terminology is similar.
As we neared our maximum velocity, I pointed to the airspeed indicator. “You forgot the autothrottle,” Bergwall said. I pressed the button and the thrust reduced slightly. “What would happen if I forgot and failed to notice?” He explained that the Garmin Electronic Stability and Protection (ESP) system would keep us within attitude, airspeed and AOA parameters. ESP can reduce or increase thrust as well as adjust pitch and roll. The aircraft also has a conventional stick shaker and pusher.
Our original flight plan took us from TYS to HVQ to HNK to GDM, direct to ASH. “That’s not going to last,” I said. Sure enough, we got an amended clearance that would have given the most seasoned Northeast veteran trouble, but the programming chores were almost effortless. Looking at one of the touchscreen controllers and selecting a waypoint offered the chance to load an airway with various points, or the waypoints alone. The touchscreen controllers double as cursor pads, allowing pilots to scroll and resize the map depiction of the MFD.
A Rainy Arrival
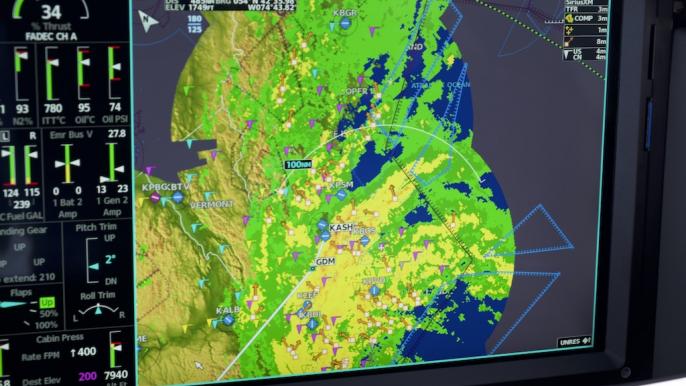
The navigation display also offers pilot-selectable Iridium weather products, such as NEXRAD composite radar, airport METAR and TAF reports, winds aloft, NOTAMs and satellite imagery. The onboard 12-in. radar provided a good picture of what we were headed into. There were no icing reports, but we ran with the pitot/static systems heated and the engine anti-icing system activated. The large, unheated windscreen is deiced using fluid dispensed from a nozzle on the nose of the aircraft.
As we neared our top of descent, we picked up the Automated Terminal Information Service (ATIS) weather for Nashua, which reported the ceiling at 400 ft. in moderate rain and a slight crosswind. We set up for the instrument landing system (ILS) to Runway 14 and Boston Center gave us vectors to intercept the localizer and then cleared us for the approach. I leveled off at the Final Approach Fix altitude of 2,500 ft., still flying at 200 kt., wondering how quickly the Vision Jet could configure for landing. “I’m ready to configure,” I said. “Sure,” Bergwall said while adjusting our speed bug to 150 kt.
I watched the airspeed obediently decrease. I was a little surprised at how nose low our attitude was, about 5 deg. below the zero pitch line (ZPL). As we slowed, the nose came up to just 2 deg. below the ZPL. I selected 50% flaps and watched as the nose dropped 5 deg. in about 2 sec. We stayed glued to the glidepath and as the speed came back, the nose climbed back to 2 deg. below the ZPL. At 120 kt., I repeated that process with 100% flaps. By the time we got to 800 ft. MSL, 600 ft. above the runway, I think we were fairly stable, perhaps a little fast at 90 kt. (Our approach speed should have been at a Vref of 75 kt. plus 10.)
The aircraft remained on course, on glidepath and on speed with little for me to do but scan our progress and search for the runway environment through the rain. At 600 ft. MSL, 200 ft. above minimums, I spotted the Medium Intensity Approach Lighting System and landed the airplane. The rain was bordering on heavy, and the runway was soaked. I took it easy on the brakes, but the aircraft slowed to taxi speed in about half the runway’s 6,000-ft. length. We had the ramp to ourselves as most of the locals were waiting out the weather.
Seasoning a New Generation of Jet Pilots
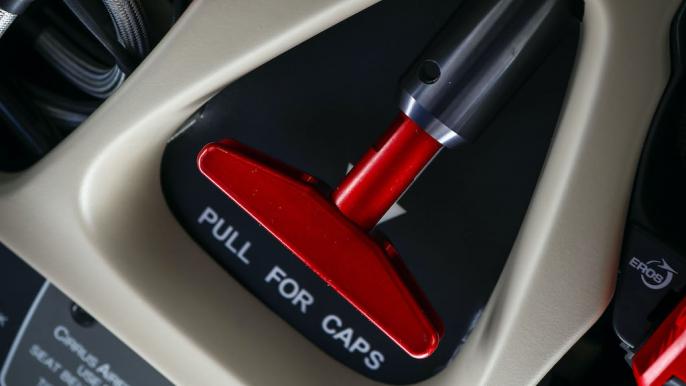
As we walked away from the aircraft, I concluded that the learning curve would be a gentle one for any pilot with previous jet experience and certainly manageable for a graduate of the Vision Center training program. I told Bergwall that I could see pilots getting lazy in an airplane designed to do so much to make life easier as a single pilot. “We keep a relationship with all our pilots,” he said. “We impress upon them the need to keep learning, and the price of annual recurrent is rolled into aircraft service contracts. Nearly everyone comes to recurrent every year.”
It seems to me a perfect setup for making sure pilots want to keep engaged with their training. Knoxville is centrally located for most Cirrus customers and offers good weather and lots to do when not in class. Anyone willing to invest in an airplane with CAPS and the Safe Return system must clearly be safety oriented. Recurrent training is a part of Cirrus Aircraft’s innovative “Jet Stream” program, which replaces the usual myriad maintenance, training, connectivity and other contracts of light jet ownership with a single bill. There is no incentive to skip training.
Is this airplane a competitive threat to Bombardier, Dassault or Gulfstream? Probably not. But at 60 gal. per hour, the economies of a single pilot and the safety features to allay the fears of not having a second pilot, the Vision Jet is clearly inventing its own market.
In the end, I learned quite a bit about the challenges of flying single pilot. I can’t imagine a better way to introduce jet aviation to new generations of pilots. But there is something even more important than that. Cirrus and Garmin are leading the way for a new level of safety with their Safe Return Emergency Autoland.
Modern aircraft with fly-by-wire flight control systems and electrically controlled flaps, spoilers, landing gear and brakes should only need some clever software and that magical red button to incorporate their own emergency autoland systems. The challenge will be greater for aircraft with conventional flight control and landing systems, but Cirrus has managed that feat with the Vision Jet.
Cirrus Aircraft has set a new safety standard; it is up to the rest of the industry to catch up.
This article was first published August 23, 2021.
Comments