Despite Good Upkeep, Mechanical Failures Still Happen, Part 3
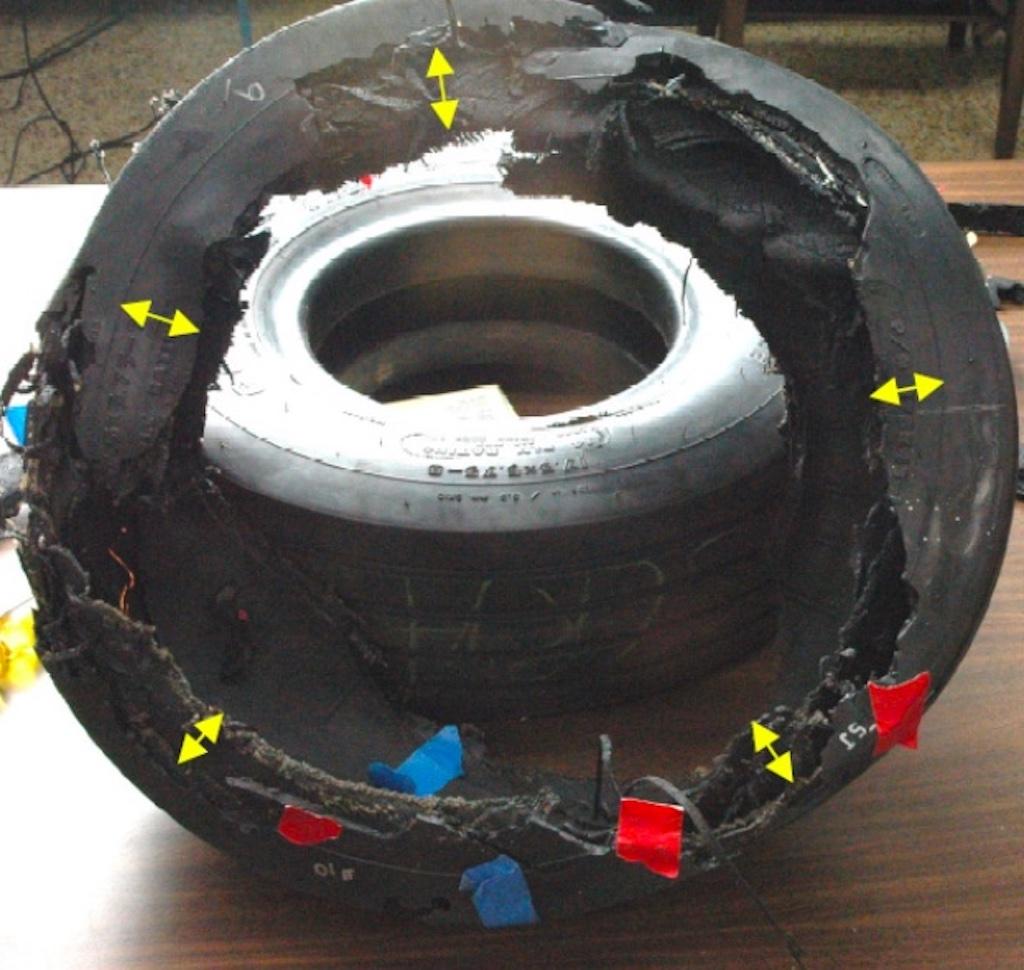
Under-inflation of a tire increases the risk of a catastrophic tire failure during the high speed phase of takeoff.
Electrical failures caused 31 of the mechanical failures reviewed for this article. Four of these became serious in-flight events and produced smoke and/or fire. The worst of these occurred on Dec. 14, 1994, near Fresno, California, when the flight crew of a modified Lear 35A twinjet declared an emergency inbound due to engine fire indications. The flight crew was heard on the tower frequency attempting to diagnose the emergency conditions and control the jet until it crashed into a residential area, killing both pilots and causing injuries to 21 persons on the ground.
The NTSB’s investigation revealed that special mission wiring was not installed properly, leading to a lack of overload current protection. The in-flight fire most likely originated with a short in the special mission power supply wires in an area unprotected by current limiters. An intense fire burned through the aft engine support beam, which may have precluded a successful emergency landing.
The value of an astute pre-flight inspection to prevent an in-flight fire is given in an incident report by a pilot who dutifully flipped the battery switch to the “emergency” position during the cockpit checks to verify the activation of the prescribed lights. Not only did those required lights illuminate, but so did a variety of other lights and avionics that were on completely different electrical circuits.
The perplexed pilot re-performed the check, with the same results. The pilot proceeded to write up the discrepancy in the aircraft logbook. Hours later when a maintenance technician disassembled the instrument panel to look at the hidden circuits, plentiful evidence of electrical soot and smoldering was evident. The information exchange between the maintenance technician and pilot centered on the theme: “Thank heavens this was discovered on the ground. If this had continued, it probably would have grown into an out-of-control fire.”
Anyone who flew the Boeing 727 might remember that the smoke detection checklist could easily consume 30 min. of time, during which a smoldering component could openly combust into a raging fire. Fighting a fire in the air is an environment solely in the fire’s favor. The safety advocates clearly agree that there is one immediate action that a crew should undertake at the very first indication of smoke, fire or fumes—and that simply is, “Get the aircraft on the ground now!”
Windshield Failures
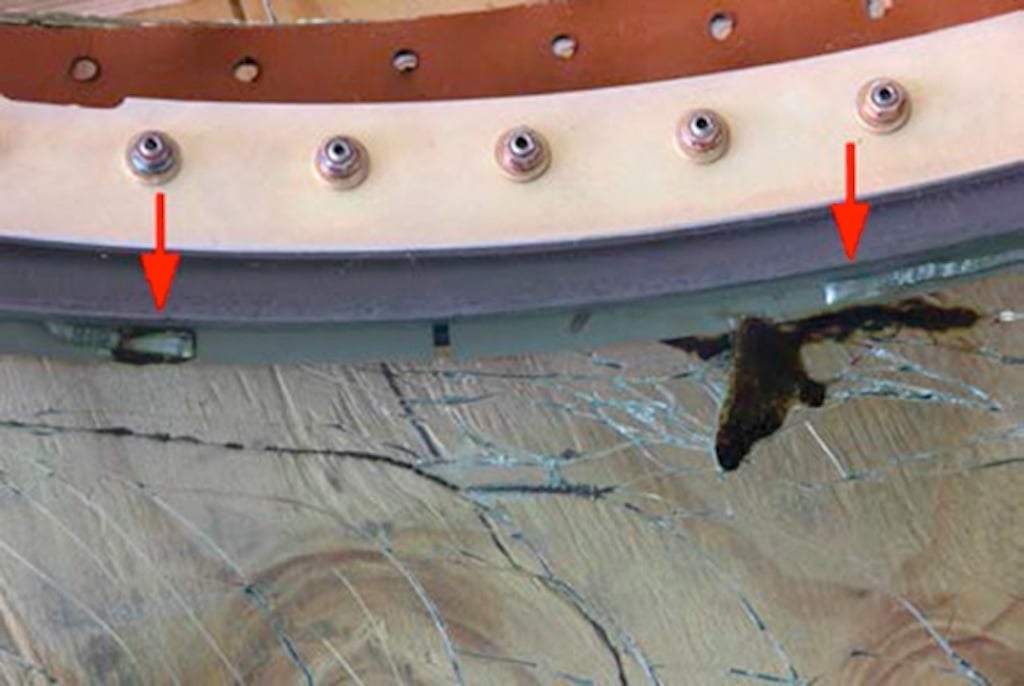
The most common event within the miscellaneous category involved windshield failures. (Note: this article does not discuss the windshield failures attributed to hail damage, bird strikes and lightning.) Flight crews were faced with a cacophony of challenges in the aftermath of these failures. Complications included the necessity to descend quickly, slow down, loss of pressurization in the cabin and the high workload associated with diverting to an emergency airport.
The predominant cause of failure was often attributed to deterioration of the windshield seal. Windshield seals are part of the pressure vessel of the aircraft. When an aircraft’s exterior windshield seal (often called an “aerodynamic seal”) deteriorates due to erosion by wind and rain, moisture seeps into the window assembly, causing problems such as window cracking. Proper inspection and maintenance of the aerodynamic seal is critical to prevent moisture ingress.
Each aircraft’s service and repair manual will contain the recommended visual inspection of the seal for erosion, cuts, nicks and overall condition. Other abnormalities—such as cloudy areas in corners of a window or around the window periphery in the interlayer—indicate moisture ingress should be brought to the attention of the aircraft’s maintenance technician. Burn marks, bubbles and moisture stains are other indications that a window may be reaching an unserviceable condition.
SMS Risk Analysis
The numbers presented in this article represent the aggregate from the industry, and this represents one source of information to help guide your organization’s own risk analysis.
One definitive conclusion is clear from this data. Events such as high-speed tire failures should not depend on simulator training as the first layer of defense. If your daily flights always originate at the home base and terminate back home each day, then following the important guidelines on tire pressure checks can be easy to implement. On the other hand, if your aircraft remains away from one of your approved maintenance locations for a longer period of time, your risk analysis needs to address incorporating the important daily tire pressure checks.
An organization’s safety management system (SMS) can help to guide which areas deserve further emphasis. Perhaps your highest-risk operations are at mountain airports, or maybe you conduct extensive oceanic operations. Certainly, an engine failure on takeoff from Aspen/Pitkin County Airport in Colorado or a rapid loss of pressurization while on the oceanic tracks is much more complicated than over the flat terrain in the middle of the U.S.
When a malfunction such as this occurs on a busy oceanic track, aircrews must follow the prescribed procedures to avoid causing a near mid-air collision in the non-radar environment. Descent to a lower altitude, consulting with flight-planning documents to determine the nearest en route diversion airport and re-computation of the aircraft’s emergency cruise performance in the thicker air with different winds contribute to the additional workload.
The aviation industry is well aware of the “Swiss Cheese Model” to capture threats and errors. Important layers to prevent threats from turning into undesired aircraft states include proper risk management, aircraft health monitoring systems, focused attention to preventive maintenance, earlier detection, better attention during pre-flight and possibly more attention during ground and simulator training.
Catch up with this series: Despite Good Upkeep, Mechanical Failures Still Happen, Part 1 and Despite Good Upkeep, Mechanical Failures Still Happen, Part 2.