Despite Good Upkeep, Mechanical Failures Still Happen, Part 2
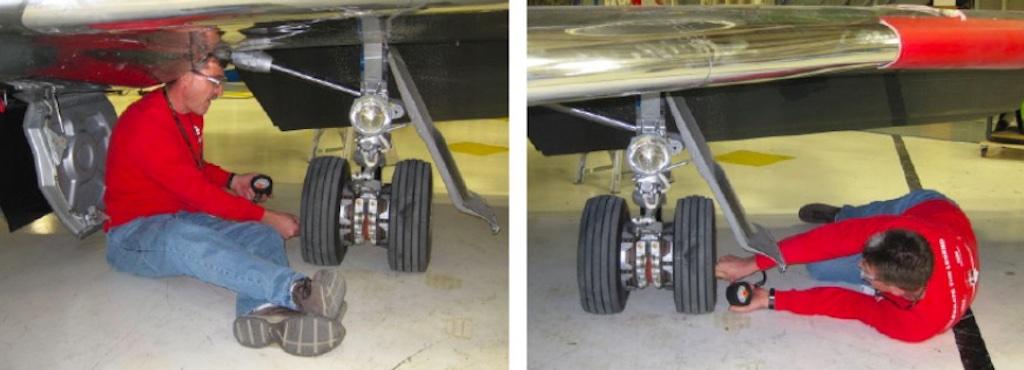
A Learjet factory technician demonstrates checking the inboard and outboard tire pressure.
The fatal accident of a Learjet 60 on Sept. 19, 2008, during a rejected takeoff at Columbia Metropolitan Airport (CAE) in South Carolina highlights that other malfunctions can occur during takeoff. The NTSB determined the probable cause was the operator’s inadequate maintenance of the jet’s tires, which resulted in multiple tire failures during takeoff roll due to severe underinflation, and the captain’s execution of a rejected takeoff after V1.
This unfortunately was not the first accident involving a flight crew’s errant reaction to a high-speed tire failure. In 1990, the NTSB issued a special investigation report, “Runway Overruns Following High-Speed Rejected Takeoffs,” that examined high-speed rejected takeoffs (RTO) involving commercial airliners. The safety board reviewed three studies, which included data from the NTSB, NASA and Boeing, related to the causes and outcomes of RTOs. The special report found that tire failures led to more high-speed RTOs than engine-related anomalies.
This collection of special studies consistently found that many other pilots have misinterpreted tire anomalies and responded by initiating an unnecessary RTO after V1. These instances resulted in runway overrun accidents that might have been avoided had the takeoff been continued.
FAA Advisory Circular 120-62 provides useful information about takeoff safety and cautions pilots about misinterpreting tire events. However, the NTSB investigation found its effectiveness is limited because it does not prepare flight crews for the startling cues, which include loud noises, airframe shaking and unusual vibrations.
Nearly 75% of the tire-failure incidents examined for this article resulted in the aircraft departing the runway, adding further potential for injury and aircraft damage. The ability of the aircraft to abort the takeoff within the remaining runway is not guaranteed since the accelerate-stop performance data is based upon an engine-failure event as opposed to a tire-failure event. Failed tires produce miniscule traction needed to transmit the deceleration required from the brakes to the pavement. The amount of runway necessary to decelerate an aircraft with failed tires is immense.
The examination of the business jet example also revealed that tire failures caused secondary damage to other critical systems in nearly two-thirds of the tire-failure events, all of which compounded aircraft damage and in many instances led to a further decrease in braking effectiveness and aircraft control problems.
This category highlights the importance of preventive maintenance and pre-flight inspections. As a general rule, the major manufacturers of tires recommend a daily cold-temperature inflation-pressure check and maintenance of a written record. The check should include measurement of pressure with a calibrated hand-held gauge, noting ambient temperature. “Cold tire” refers to a tire at approximately the same temperature as the surrounding air, typically after a post-flight cooling period of 2-3 hr.
Hydraulic System Failures
Hydraulic failures were the fourth-most-common mechanical failure. Most of the reported events involved failures of the multiple sub-systems that depend on the hydraulic pumps, such as gear, brakes, nosewheel steering, flaps, divebrakes/lift dump/spoilers and thrust reversers. In general, most of the incidents ended with the flight crews successfully completing the abnormal checklist procedures and getting the aircraft safely onto the ground.
Pressurization Failures
The fifth-most-common mechanical failure is a malfunction that we practice during every initial and recurrent simulator training course—and it is probably a good thing that we do. The FAA incident database contained 41 reports of malfunctions with the pressurization system, of which 24 resulted in emergency descents. I suspected this was “just the tip of the iceberg” and read an additional 68 “rapid decompression” events in NASA Aviation Safety Reporting System (ASRS) records. I stopped counting after that, because there were many more related incidents described as “loss of cabin pressurization.”
More than 40% of these were “rapid” decompressions, and an additional third were termed by the flight crews as a “moderate” depressurization rate. High altitudes teamed with rapid or moderate losses of pressurization create a significant physiological threat to the aircraft’s occupants.
Among the problems that pilots reported in NASA ASRS reports were difficulty donning the emergency oxygen mask for a pilot wearing protective eyewear (32%), re-establishing communications with the controller (27%), problems hearing the controllers (26%), difficulties with the communication panel switches (15%), difficulties in obtaining clearance for lower altitudes (11%) and distractions with passenger safety (10%).
If there are some pointers to learn from the ASRS reports on this that would benefit from a few extra minutes during ground training, it would be reviewing which switches on the audio panel to use for the overhead speaker. Realize that if you leave the intercom button on “hot mic” and you switch the sound to the overhead microphone that you are going to be listening to each other’s pronounced breathing on the overhead. It is loud and it distracts from listening to ATC’s emergency instructions.
In Part 3 of this article, we analyze electrical and windshield failures and offer our thoughts on safety risk analysis.
Catch up with Despite Good Upkeep, Mechanical Failures Still Happen, Part 1.