Despite Good Upkeep, Mechanical Failures Still Happen, Part 1
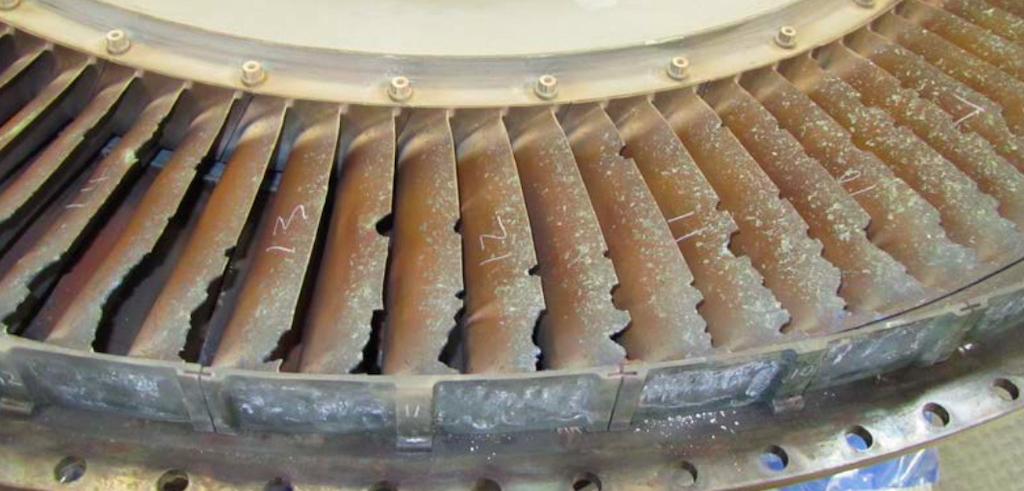
The failure of this engine occurred during an oceanic flight from Sydney to Signapore. Engine vibrations increased beyond the normal operating level and the flight crew elected to shut down the engine. This necessitated descending to a lower altitude.
Simulator training has been the industry standard for many decades to train pilots for mechanical system failures in a no-risk environment. But time in a flight simulator is limited and expensive, and there are a multitude of mandatory items that must be jammed into those 4-hr. simulator training sessions.
The basic premise of this article is to look back at accident and incident data to question whether training curricula are adequately addressing the higher-risk failures, or perhaps more importantly, which layers in the system safety process need improvement to prevent these mechanical failures from occurring and/or progressing into a threatening event.
A few cherry-picked data points are woefully insufficient to make sweeping generalizations, thus this author reviewed a total of 251 accidents and 808 reported incidents involving business jets that occurred during a 12-year period. Of these, 82 accidents and 414 incidents involved a mechanical failure.
Often systems are dependent upon each other. For example, electrical and hydraulic systems depend on the engine to power their respective pumps. Events within this data sometimes involved a cascading failure of dependent systems. For simplicity, this review categorized each event depending on which major system was the first that failed.
Engine Malfunctions Are Most Common

It shouldn’t be a surprise that powerplant failures were the most commonly reported category. Powerplant failures caused 201 reportable incidents (15 accidents and 186 incidents). Landing gear malfunctions caused 69 reportable events, while closely behind that were tire failures with 64 reported events (10 accidents and 54 incidents). Loss of the hydraulic system or components were reported in 51 events (11 accidents and 40 incidents.)
Pressurization system failures caused 41 incidents, and these often resulted in emergency descents. Electrical system failures (not caused by a lightning strike) caused 30 reported events (two accidents, of which one was fatal, and 28 incidents.) The rest fall into the “miscellaneous” category, of which windshield failures were the most common.
Three of the 201 engine failures resulted in fatal injuries. Thankfully, the remainder of the engine-failure accidents (12 out of the 15 total engine-failure accidents) and 186 engine-failure incidents were resolved without injury to the aircraft occupants.
It is interesting to divide engine malfunctions into those that require prompt response versus those that occur during a low-workload phase of flight in a low-threat environment. Notice that the majority of engine failures occurred during cruise, and the vast majority of these ended with a safe landing of the aircraft.
Roughly one-third of the engine failure accidents occurred during takeoff. Malfunctions during the high-speed moments of takeoff leave precious little time for pilot recognition and proper diagnosis of the problem. Five of the rejected takeoff accidents in this population sample were aborted at a speed above V1. It should be no surprise that all of these resulted in a runway overrun.
In contrast, 19 engine-failure events during takeoff were safely resolved when pilots made the proper split-second decision to abort below the takeoff decision speed or continue the takeoff with an engine malfunction above that speed. These events were resolved with no further aircraft damage.
According to the FAA’s Takeoff Safety Training Aid, 58% of 74 rejected takeoff (RTO) accidents examined in a special study on airline RTOs were begun at speeds greater than V1. In February 1990, the U.S. NTSB issued a special investigative report, “Runway Overruns Following High-Speed Rejected Takeoffs,” that states: “Few safety margins are included in the calculations of accelerate-stop distances. Therefore, any substandard performance by the pilots, brakes, or other airplane equipment related to the airplane acceleration or stopping performance will result in the airplane overrunning the end of the runway.”
From this data, one can argue that we have reached a point of diminishing returns where any further simulator practice of engine failures will yield further benefits. The possible caveat with this category depends on each flight operator’s area of operations. If your flights are solely concentrated at airports surrounded by relatively flat terrain, the current training scenarios are sufficient. However, if your flight organization conducts operations at topographically confined airports such as Aspen, Colorado, then prudent risk mitigation would suggest training your flight crews in special procedures to safely conduct an engine failure departure from those airports.
Incidents Involving Landing Gear Failures
Landing gear failures caused 69 of the events studied. Sometimes these were a relatively simple nose gear collapse at a relatively slow speed, causing minor damage to the nose gear doors. These resulted in 46 reportable incidents. Inevitably, some of the landing gear malfunctions involved failure of a main gear to extend on approach, and these often resulted in more serious damage to the aircraft, enough to be considered an accident by the NTSB. Circumstances similar to this occurred in 23 accidents.
One of the difficulties created by landing gear malfunctions was the timing involved with the discovery of the malfunction. These usually occurred during those busy moments on takeoff and departure, or during approach and landing, both of which require very precise aircraft handling due to the proximity to the ground, and very high workloads due to the terminal area environment.
From most of the incident reports, it appears that the flight crews properly followed the abnormal procedures. Sometimes they were able to remedy the malfunction, and sometimes not.
Did the accident and incident reports of the landing gear failures indicate any systemic weaknesses in our training? Not really. What can we do to prevent more of these “hard-to-solve-in-the-air” landing gear problems? The answer is proper preventive maintenance and pre-flight inspections. It has always been good practice to properly pre-flight an aircraft’s landing gear to make certain there are no loose objects in the wheel well area; that the hydraulic lines are not chafing and in good shape; that the micro-switches are not covered up with excessive grease; and that the up locks are unobstructed.
In Part 2 of this article, we analyze tire, hydraulic and pressurization failures.