Antiviral Cabin Technologies Could Help Airline Recovery
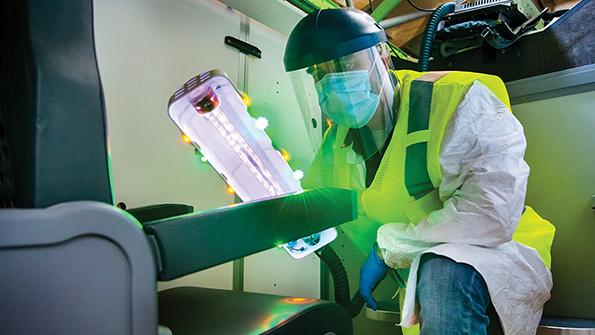
After a devastating year, airlines are hoping that the rollout of COVID-19 vaccinations and a gradual easing of travel restrictions will pave the way for the beginnings of a recovery—and antiviral technologies and materials in the cabin could help reassure passengers nervous to fly again that they are safe.
However, airlines’ dire financial situation, with demand set to remain below pre-pandemic levels for years and many carriers relying on state aid to survive, means large-scale cabin revamps will not be on the agenda for some time.
- Antiviral cabin technologies could help airline recovery
- Airbus and Boeing are researching clean cabin solutions
- Diehl is betting on touchless lavatory technology
Manufacturers, equipment suppliers and technology specialists know that if airlines are to adopt new solutions to improve cabin hygiene in a post-COVID-19 world, modifications will need to be affordable and easy to integrate into existing layouts.
Nevertheless, such cabin improvements could be a differentiator for airlines, convincing apprehensive post-coronavirus passengers that it is safe to fly. The good news is that manufacturers believe the pandemic has proved a catalyst for such development.
Antiviral technologies such as HEPA filters—which remove viruses, bacteria and fungi from cabin air before it is returned to the cabin—are nothing new, and airlines and manufacturers have been at pains to point out the low risk of catching COVID-19 on board because of cabin air filtration technology.
“The design of our airplane cabins helps minimize contaminants from spreading throughout the airplane, from the rapid cabin air exchange rate to the use of HEPA filters,” says Mike Delaney, Boeing’s chief aerospace safety officer.
An Airbus study carried out last year used 3D computer simulation to understand potential particle propagation from a passenger. It was based on computational fluid dynamics, analyzing 50 million points inside the cabin and finding that significantly fewer particles emitted by a passenger in an airliner cabin reached the breathing zone of other passengers, compared with particles emitted in a typical commercial indoor space.
Antimicrobial coatings can be added during manufacture or applied to selected surfaces as polishes that last for a set time frame. Airbus is also looking into antimicrobial stick-on decorative foils, which can have the added advantage of reinforcing an airline’s branding, or the impregnation of fabrics with antimicrobial agents.
“The goal is to cover areas that are high-touch,” says Bruno Fargeon, leader of the Airbus Keep Trust in Air Travel initiative. The manufacturer is adopting a threefold strategy for protecting passengers against transmission of viruses, many of which are much more transmissible by touch than SARS-CoV-2, the virus that causes COVID-19, Fargeon says. “First, you want to remove touch points, so that’s why we’re looking at touchless features, which are already embedded in newer cabins, such as infrared water dispensers or touchless flaps,” he notes. For this, the airframer must take care to strike a balance between complexity and reliability.
“Second, when touch cannot be avoided, we try to cover the surface with antimicrobial products. And third, if covering with an antimicrobial product is not possible, make sure it is easily disinfected,” Fargeon says.
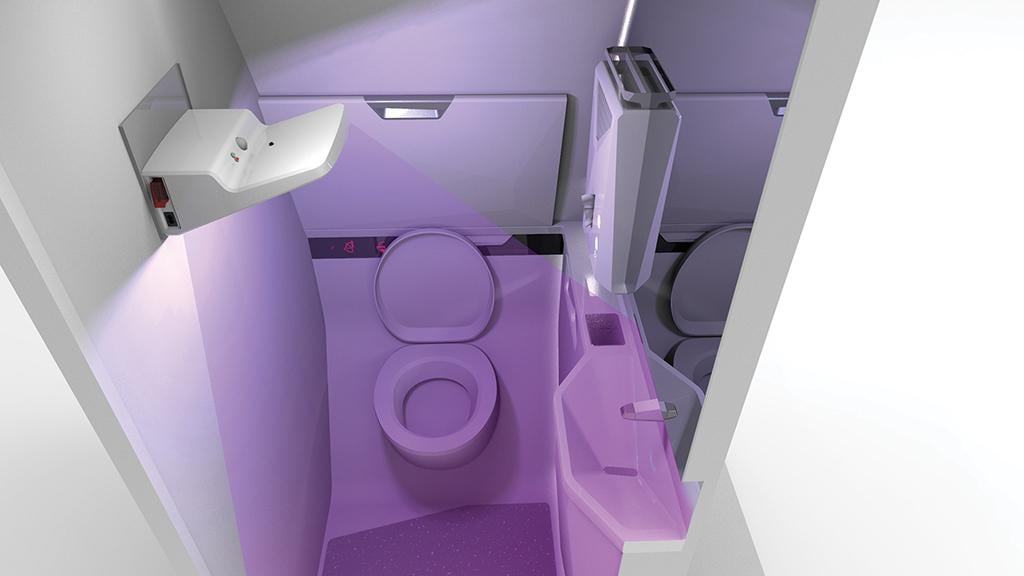
Along with lavatories, he highlights inflight entertainment (IFE) systems as a high-touch area and says he expects a trend toward passengers using their own devices to operate IFE will accelerate.
Fargeon acknowledges that airlines are under financial pressure, and cabin upgrades represent an investment, which is why Airbus is offering simple options that can be applied and make an immediate difference.
However, bigger changes will come further down the line, he believes, including possibly reconfiguring cabin geometry for easier cleaning.
“Do they have the choice? If airlines don’t take this direction, they risk passengers being less eager to fly with them,” Fargeon says. “In the industry at large, whenever we speak about what’s going to be next, I hear that we need onboard health to be on the same level as flight safety and security. There is a risk that for economic reasons some will forget about this, but this is the first time our whole industry has been grounded because of a simple virus—collectively, we will remember. The lesson has been learned.”
Fargeon expects the pandemic will act as an accelerator for technology that was already being explored.
German cabin technology specialist Diehl Aviation shares this view of adopting previously developed technology such as its touchless lavatory, which includes features such as touchless waste flaps, seat and lid. Diehl expects touchless technologies for lavatories, with their multiple contact points—door, lavatory lid, trash can, faucet—to be the norm within the next five years.
Diehl is talking to multiple airlines about retrofit options for the touchless lavatory, while the first such lavatory elements will be installed this year on the latest Airbus A320neo aircraft family being produced with the all-new Airspace cabin.
The company has also worked on a touchless and portable rechargeable ultraviolet-C (UV-C) disinfection device for cabin lavatories, which can be mounted inside the cubicle and quickly used by flight attendants to disinfect the area after the flight has landed.
“There is a completely different mindset and awareness, with our [OEM customers] and also with the airlines,” says Helge Sachs, Diehl senior vice president for product innovation. “There is an increasing willingness to prepare for the cabin of the future, the new normal and what passengers will expect.” Sachs says it will still take a few years for these changes to be implemented in cabins. But the company, confident that these evolutions will be put into place even if it takes time, has also been looking into other areas of innovation such as antimicrobial coatings and touchless solutions for luggage bins and window shades. Diehl also sees room for improvement in cabin air conditioning systems.
UV light could be incorporated in cabin lighting to disinfect the entire cabin, although research into that usage is very much at an experimental stage, Sachs says. “We do see COVID-19 as a driver of innovation in these circumstances, and maybe even an accelerator for some products,” he says.
Boeing has also been exploring the potential for disinfection with UV light. The manufacturer developed a portable UV wand designed to sanitize aircraft interiors, and in September 2020 it entered into patent and technology licenses with Far UV Technologies and Healthe Inc. to produce and distribute the commercial wand.
Sachs acknowledges the “chicken and egg” dilemma that cash-strapped airlines may not be able to invest in the technologies that could set them apart and drive their recovering revenues. “We believe that it will be in the next two, three or four years that this will become the new normal, and airlines will have to give the right answers to their customer bases with touchless features, antimicrobial surface coatings and even thinking about improved air quality,” he says.
Nigel Goode, director of design consultancy PriestmanGoode, which last year launched the Pure Skies concept to explore how COVID-19 could change the cabin environment, agrees that new materials and techniques can be used to improve the feeling of personal space and reassure passengers about onboard hygiene—and that any structural changes to airline cabins may take 2-3 years.
Goode says financially struggling airlines will look at densifying their cabins, rather than creating more space. But in the short term, smaller changes will contribute to improving passenger confidence.
With the extra cleaning that has been taking place on board, in some cases seat covers, carpets and curtains now need replacing more quickly than normal. “In Pure Skies, we suggested concepts around antibacterial and antimicrobial coatings for dress covers and materials, and we have worked with suppliers to try to realize some of those things,” Goode says.
Looking further ahead, Diehl is working on ways to incorporate more touchless options into luggage bins or window shades, but airlines will have to weigh the additional maintenance costs of such features. Diehl, and other companies, are also researching antiviral and antimicrobial coatings that can be applied to surfaces within the cabin.
Like Airbus, Boeing is looking into coating and disinfection technologies. The manufacturer has been working with partners in academia on antimicrobial coatings and thermal disinfection for hard-to-clean and sensitive areas such as flight deck equipment.
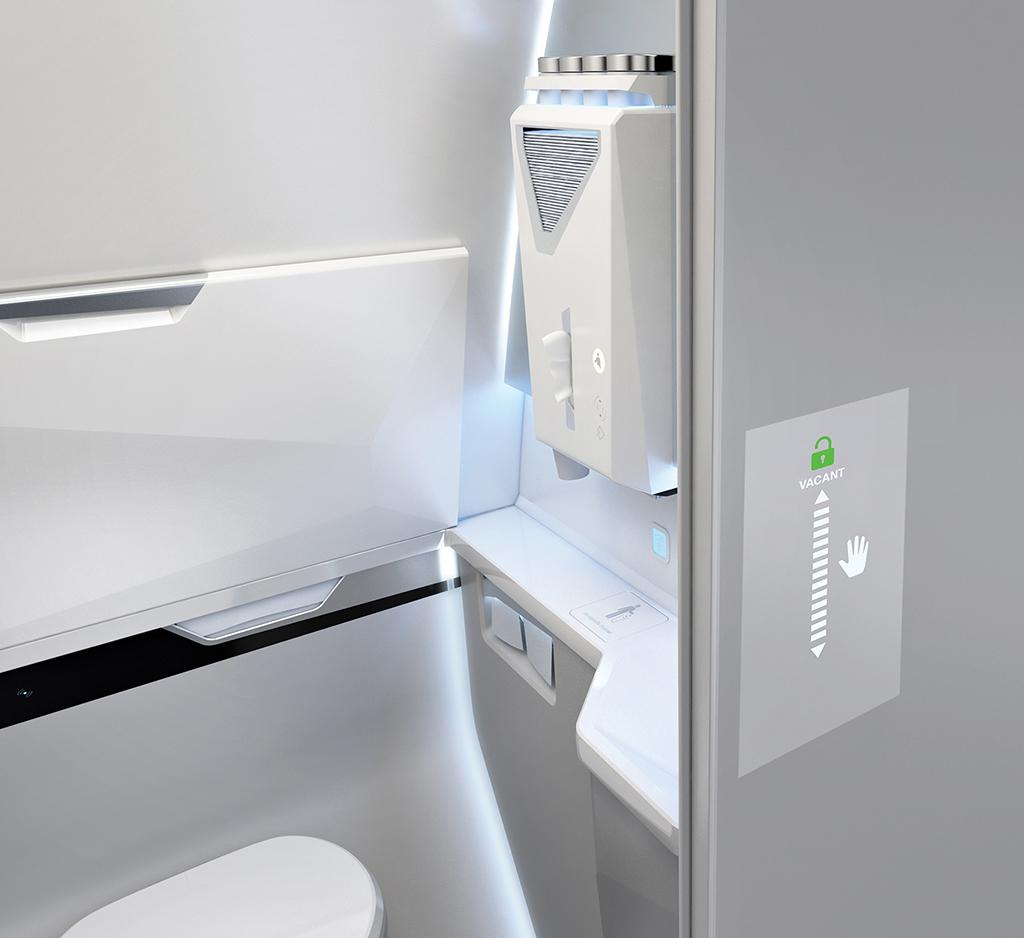
“Some areas we are evaluating include antimicrobial applications on surfaces, high-touch points throughout the cabin and self-disinfecting lavatories using UV light,” Delaney says. “The pandemic didn’t stop innovation at Boeing. In many ways, it sped it up.”
Incorporating antimicrobial technology into aircraft seat parts still involves a long development cycle. Since June, Acro Aircraft Seating has been exploring a collaboration with Addmaster, a supplier of additives for materials, with a view to incorporating Biomaster antimicrobial technology, which has been in use in London’s public transportation system for six years, into aircraft seat parts such as armrests.
When microbes land on an untreated surface, they multiply. But when they land on an antimicrobial protected surface, silver ions prevent them from growing, producing energy or replicating—and so they die. But for antimicrobial coatings to be adopted in aircraft cabins, they must be both effective and safe in terms of flammability and resistance to cleaning materials.
“We are well-advanced in creative collaboration with several key suppliers [including Addmaster], exploring the options for antimicrobial technology,” Acro says, adding that the technology offers protection and is cost-effective. The company has not mentioned a time frame for entry into service, however.
Safran Seats sees self-cleaning surfaces as the holy grail for hygiene. “Safety requirements in air transport, notably against fire and toxic smoke, are preventing the use of numerous materials that are used in other industries,” notes Quentin Munier, Safran Seats executive vice president for strategy and innovation. The development cycle of a usable product may lead to deliveries in 12-24 months from now, he adds.
In the meantime, the combination of face masks and manual cleaning is the only working solution, Munier says.
The company is carrying out tests on the effects of particular cleaning products on different materials. The many materials requiring cleaning and the number of candidate detergents means a four-digit number of tests will be needed. The idea is to assess the effect, including potential damage, of a detergent on a material. “We work with hospitals and have partnered with material specialists such as 3M,” Munier says. “Many results are shared between cabin equipment manufacturers and airframers under the oversight of civil aviation authorities.”
Another way to fight virus spread may lie in seat design. “Sleek lines are getting even sleeker as we eliminate potential dirt traps,” says Acro.
Airbus has also been working with laboratories and other industry players on research into disinfection.
Fargeon lauds the level of collaboration within the industry on solutions for post COVID-19 travel. “We’ve been testing various disinfection technologies and sharing results with airlines and within the community,” he says. “Our competitor is doing the same—it’s important that we build this common database.”
Airbus has been testing methods such as UV disinfection, chemical fogging, gaseous H2O2 disinfection using vaporized hydrogen peroxide, and thermal disinfection, evaluating factors such as the techniques’ efficiency, the resistance of materials and operational concerns. Even amid a drive for innovation, Fargeon notes that one tried-and-tested technique is still important.
“Spray-and-wipe is still very important. It might be labor-intensive, but it’s superefficient. Let’s not discard this good old technique,” he says. “We need layers of measures which all protect the passengers—and that includes wiping with disinfectant. There isn’t one single option.”
Boeing research carried out as part of its Confident Travel Initiative also highlights the efficacy of a wide range of measures. The manufacturer teamed up with the University of Arizona for research that found all recommended products, methods and technologies tested, including chemical disinfectants, UV light, and antimicrobial coatings, were effective in killing MS2, a virus that is harder to kill than SARS-CoV-2, when it was placed at strategic high-touch points throughout the cabin.