
Elodie Donne is a multiskilled operator on Mecachrome’s Leap engine turbine blade production line in Sable-sur-Sarthe. Hiring has been shaping production rates in the French supply chain.
Every week at Mecachrome’s metal component factory in Sable-sur-Sarthe, France, plant manager Etienne Braud leads a tour for job seekers. The idea is to show that working in an industrial facility is not necessarily difficult.
“The time when a human resources director could tell job seekers they were part of a long waiting line is over,” he says. “A company now has to attract them.”
- As production ramps up, hiring becomes a major concern
- Improved production techniques could help on-time delivery and quality
His task epitomizes the aerospace supply chain’s struggles. The COVID-19 pandemic caused serious problems in the European industry due to a sudden drop in demand. Since 2021, OEMs such as Airbus and Safran have asked suppliers to ramp up their production more quickly than expected after the slowdown. That stop-and-go sequence is creating a new predicament, this time because the supply chain cannot keep up with demand.
Having emerged suddenly after a demand crisis, the supply problem may take years to resolve.
Suppliers are facing various issues, from component shortages to inflation and hiring trouble—with the latter increasingly seen as the most pressing. And that is precisely what Mecachrome is experiencing. Airbus suppliers in France would have had to hire more workers regardless of the pandemic and already were engaged in a long-running recruitment endeavor. COVID-19 just added hurdles, including a high number of workers leaving, both forced and voluntary. Some white-collar workers who were involved in production indirectly left as well, and the number of apprentices decreased.
- Download Aviation Week’s new app at AviationWeek.com/App for our team’s up-to-the-minute coverage from the Paris Air Show
“During the crisis, the general public repeatedly heard that aerospace would not recover for several years,” Sunaero CEO Jean Roussel says. “Because of that, skilled candidates became reluctant [to join] the industry.” To overcome that reluctance, Sunaero, which specializes in fuel tank repairs and seal-and-paint-defect corrections on production lines, welcomes apprentices and interns enthusiastically.
Recruitment has become so challenging that it is impeding the production ramp-up led by Airbus and Safran. In fact, it has surpassed energy prices as the priority issue among members of French aerospace lobbying group GIFAS, Airbus CEO Guillaume Faury, who is also GIFAS chairman, said in late April.
The association’s member companies intend to hire 25,000 workers this year, up from the 18,000 added last year. By comparison, the industry’s hiring plans in 2019 were for 15,000 employees, according to the association. GIFAS companies had a combined payroll of 195,000 at the end of 2022 and are targeting 200,000—with the hoped-for additions and factoring in retirements—by year-end.
Recruitments in 2022 were effectively more numerous than the expected 15,000 but were still short of actual needs. “Some small companies cannot run their production equipment because they do not have enough workforce,” reports Clementine Gallet, president of GIFAS’ committee for small businesses and CEO of Coriolis Composites. “That is not just a French problem. It started with the loss in employees during the COVID-19 [crisis] in 2020. Getting them back is challenging. That is a global issue.”
Some jobs are particularly hard-hit. In welding, sheet-metal work and industrial maintenance, the number of newly qualified students at the end of a training program is below expectations. It stands at only half of what the French industry—including aerospace, naval, nuclear and energy sectors—needs, according to a survey in the metallurgy branch.
It is unlikely the problem will be solved soon. In 2020, due to COVID-19, some students left their training program before they completed it. The schools that train production workers still face an enrollment shortage.
Various training schemes are available. It can take five years for a young production worker to be fully trained between ages 15 and 20, including the first three years in a professional high school, Sunaero’s Roussel says.
If started later, initial training may take up to 450 hr. spread over a few months, according to French employment agency Pole Emploi. That should be followed by a work-based learning contract with a company. And aerospace competes with other sectors in France, such as nuclear power plants.
At Mecachrome’s factory, more straightforward jobs may involve three weeks of initial training followed by three weeks on the job.
Is the industry suffering from an image problem? “We should do more communication about our careers, the content of our jobs, the high technologies they involve and the sovereignty aspect, as well as the fact that the solution to decarbonization will be found in the industry,” says Philippe Dujaric, the social and training affairs director at GIFAS.
Working in the aerospace industry still is perceived as hard. “In fact, it is no harder than working in the building or hotel sectors,” says Annick Senat, Pole Emploi’s local director of the Haute-Garonne department, where Airbus is based. “Also, in the current context of environmental concerns, graduate engineers tend to favor the renewable energies sector, walking away from aerospace. We have to show the industry is not a frozen one; it is a dynamic one, striving to become sustainable.”
What about hiring more women? “The proportion of female recruits has grown to 27% from 25%,” Gallet notes. “We see that as progress.”
And how to convince them to join aerospace? “We should tell them they can find other jobs than in marketing and sales. . . . Educating them should start early, at the end of middle school or early in the high school years,” Gallet answers.
At the university level, the CEO of a small GIFAS-member company may have found a trick. “You can find many young women studying mathematics,” Gallet says. “That CEO needed employees for his automated machining tools. That is a job for mathematicians. He promoted the positions to female students and was successful, filling the vacancies with five of them.”
“We have role models we did not have 10 years ago,” Faury adds. At Airbus, Sabine Klauke is chief technology officer and Sandra Bour Schaeffer is senior vice president for procurement for cabin interiors.
At the Paris Air Show, students and unemployed persons may enter for free June 23-25. Companies currently hiring will be easy to spot, thanks to red balloons on their stands.
The “career plane” (known as the Avion des Metiers in French) will showcase demonstrations of a number of jobs, some involving spectacular manufacturing equipment. A number of elementary schools students and teachers will be invited as well.
Pole Emploi plans to sign an agreement with GIFAS at the show on June 23. Under the deal, both parties will commit to providing maximum visibility to aerospace industry job offers. They will exchange more information, such as surveys, designed to meet the industry’s needs.
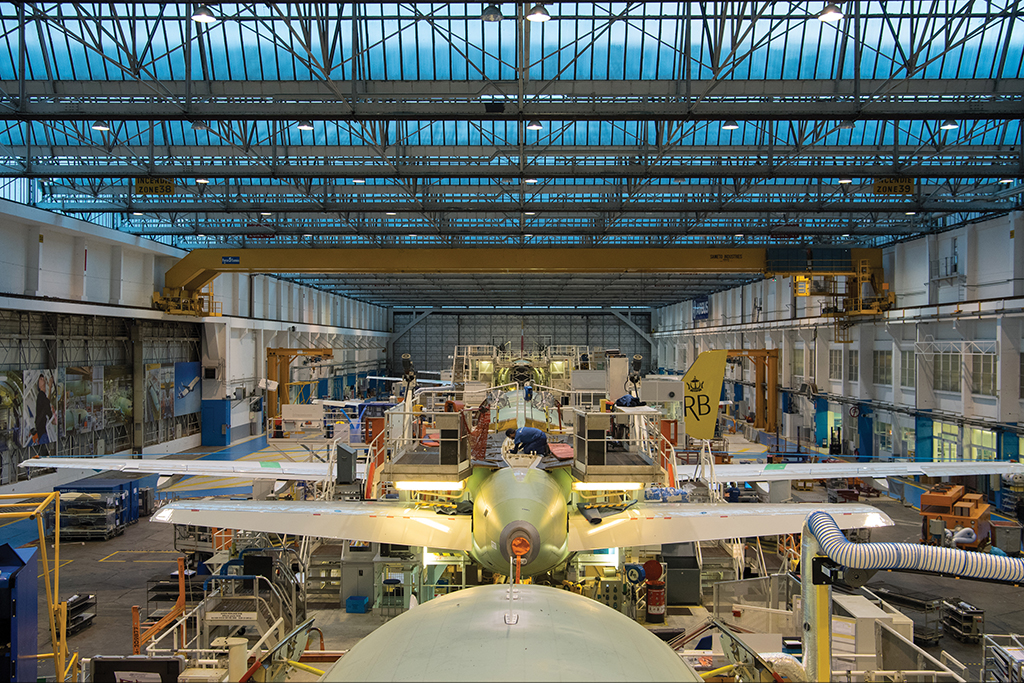
In salaries, aerospace is well positioned, says Senat. Nevertheless, one will see differences between small companies and large OEMs, which can offer more social benefits.
Salaries are 15% higher than in the services sector, according to Dujaric. An 18-year-old, after three years of technical high school classes, may earn an annual €20,000 ($21,400, after deduction of social security contributions), Dujaric says. Another two or three years of training bring initial salaries to €23,000.
Recent bankruptcies in clothing retail chains in France have left thousands of workers unemployed. GIFAS is trying to make the most of the situation, seeing a recruitment ground for aerospace technicians. The employment rate for the 15-24 age category is at its highest level since 1990, Dujaric notes.
Raw material and component shortages have created another difficulty. Global supply chains—not only in aerospace—have struggled to recover from the COVID-19 crisis and ramp up production of wiring, small structural parts, electronic components and office computers, to name a few critical supplies.
The situation seems to be improving but has yet to come back to normal. Sunaero still faces delivery delays for the seals it uses on airframes. An outcome of shortages has been double-digit inflation, and Mecachrome was forced to increase the prices of its parts, says CEO Christian Cornille.
Despite those short- and medium-term issues, the supply chain is finding energy to solve more structural ones and adapt to new realities.
Consolidation is allowing a growing number of companies to become more robust and to invest in new programs. New methods of production are being found for faster and more cost-efficient parts manufacturing and better quality.
GIFAS has long urged small players to unite, targeting economies of scale and resilience. Consolidation creates larger companies that are involved in more programs and have contracts with a greater number of OEMs. It is at last happening in earnest.
Last year, Mecachrome completed the takeover of WeAre Group, another supplier of metal components. A few months later, Mecachrome acquired Rossi Aero, a specialist in ad hoc manufacturing of metal components.
The enlarged Mecachrome is owned by investment funds essentially linked to the government and the Big Four in France—Airbus, Dassault, Safran and Thales. The company is benefiting from new industrial possibilities, resulting in improved productivity. Latecoere, an expert in aerostructures and interconnection systems, last year acquired three foreign companies and invested in a fourth.
The Toulouse-based company, however, had to secure recapitalization agreements with majority shareholder Searchlight Capital Partners, the European Investment Bank and lenders. A memorandum of understanding signed in May is designed to reinforce the financial structure and cut the debt. While the outcome of the negotiations was positive, customer trust might erode, as the move is the latest episode in a long story of failed strategies.
The memorandum of understanding has yet to be approved by a local court specializing in trade issues. It was signed under the auspices of the French government’s interministerial committee for industrial restructuring.
The agreement includes a €45 million loan and a €100 million capital increase from Searchlight. In addition, the debt is being cut by €183 million. It was €297 million as of Dec. 31. The reduction is all the more significant because state-backed loans accounted for a large part. Latecoere was not in a position to repay them. Under the memorandum of understanding, the remaining debt is to be repaid in 2027.
As for production techniques, Mecachrome is proposing an original way to improve. For suppliers that know both the automotive and aerospace sectors, the difference in manufacturing performance is striking. Producing car parts results in virtually 100% on-time deliveries and 0% defects in factories with the highest standards. Aerospace struggles with both, and OEMs, despite recent progress, are used to facing late deliveries and quality issues.
Several factors explain aerospace’s relatively poor performance. An aircraft component often relies on more sophisticated production processes than does an automotive part. Production volumes are smaller, making it more difficult to make a business case for automation, which would allow more robust processes. Moreover, manufacturing relatively small batches of parts creates a stop-and-go flow in the factory. The overall aircraft production system involving multiple sites is another characteristic. What if aerospace could adopt the automotive industry’s methods?
Mecachrome’s factory in Sable-sur-Sarthe houses the production of Porsche engine components and aerospace parts. The concept of a “focus factory” has proven itself with cylinder heads and then Leap engine turbine blades. Implementation of stable—as opposed to variable—production processes is the overarching goal.
Cornille has approached Airbus about creating a focus factory for airframe components, aiming for a near-perfect outcome in on-time and on-quality deliveries.
To substantiate the investment, the production of parts using the same processes should be consolidated. Such an approach is different from Airbus’ long-standing philosophy, which is based on organizing multisite production. Airbus final assembly lines receive subassemblies from several factories in Europe. How an aircraft will be put together offers a giant construction puzzle as the starting point of Airbus’ thinking, Cornille emphasizes.
A focus factory tackles construction from a different angle. It looks at production processes regardless of where they are used, Cornille explains.
“We would like to explore the entire nomenclature and identify those parts that use the same operating modes,” he says. “The digitalization of aircraft blueprints makes it possible.”
A focus factory uses the idea of “one-piece flow.” Thanks to a QR code, the machine-tool identifies the part and sets itself accordingly. As a result, a human operator no longer has to wait for a batch of same-type parts to be ready before launching the process. For Leap turbine blades, the Sable-sur-Sarthe site is very close to the one-piece-flow concept, Braud says.
Meanwhile, it is very early for suppliers to start thinking about what hydrogen or other breakthrough technologies may mean for their businesses. Some nevertheless are considering changes. Sunaero, which has expertise in fuel leak-sensing, is studying the addition of hydrogen leak detection.