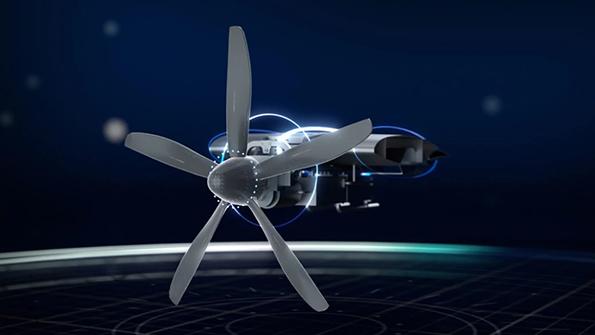
MTU’s Flying Fuel Cell propulsion system is planned to be tested on DLR’s Dornier 228.
MTU Aero Engines has been investigating fuel cell technology for many years, but so far, none of the initiatives have advanced beyond initial planning. This time around will be different, says Barnaby Law, chief engineer for MTU’s Flying Fuel Cell project.
“The automotive industry has matured technologies that did not exist 15 years ago,” Law says. “There are also good supplier networks for all sorts of components.” Maturity has improved for fuel cell stack components, while other parts of the hydrogen fuel system have been available for decades. “The trick now is to orchestrate the system,” he says. “We have to get it into the air.” And the political pressure to move to sustainable power is much greater than it was 15 years ago.
- Fuel cell subsystems already under test
- Iron-bird mission simulations planned for 2025
The Flying Fuel Cell (FFC) project is a joint undertaking by MTU and German aerospace research center DLR. The goal is to fly a reconfigured Dornier 228 in 2026 powered by one conventional turboprop and one hydrogen-electric powertrain designed by MTU. Over the past few weeks, all of the fuel cell subsystems have been tested, and engineers are beginning to explore interactions between them. By 2025, mission profiles are to be simulated in an iron bird ground-test rig.
The pace of the FFC program contrasts with more ambitious timelines pursued by startups. “We don’t want a quick marketing stunt, but to reach the highest possible [maturity] level to jump to a possible product,” Law says. An ATR 72-size aircraft can be developed by 2035, he says, although payload/range will be less than those of conventional aircraft. Part 23/CS-23 aircraft with up to 19 seats could be ready earlier—“2030-32 for a first product is realistic,” he says.
Law sees reliability as the biggest challenge. “Gas turbines have been optimized for 70-80 years and are incredibly reliable now,” he says. Industry will have to work hard to “even get close to that [level of reliability],” he notes. “We cannot cause extremely frequent [aircraft-on-ground incidents].” A lot of learning will be required in the initial operating phase, he says.
Suppliers will have to upgrade to aerospace industry performance levels. “In a car, the logic in a failure case is to shut down the engine. That’s exactly what we don’t want,” Law says. “We want to leave the decision to the pilot.” But as automakers move toward more autonomous driving, “the electrical components are developed exactly as they would be in aerospace,” he says.
“We are in intensive discussions with [the European Union Aviation Safety Agency (EASA)] and LBA [Germany’s aviation authority] and have a good idea about what requirements will be set. We have agreed a schedule with EASA and have worked through 90% of the relevant demands.”