This article is published in Air Transport World part of Aviation Week Intelligence Network (AWIN), and is complimentary through Jan 04, 2025. For information on becoming an AWIN Member to access more content like this, click here.

Low-altitude dust in places like Dubai is causing wear-and-tear on new generation engines.
Problems with new generation engines have been keenly felt in dust-laden regions such as the Middle East, where heavy intakes of particulate matter have exacerbated existing engine problems from all three major powerplant manufacturers.
A study this year by European scientists noted that the amount of mineral dust reaching an engine core during a flight sector can typically be around 5 grams—a negligible problem.
“However, when it is considered that many engines see this level of dust ingestion every flight—especially those operated by airlines with hubs at dusty airports—the cumulative dose starts to represent more of a problem; 1,000 landings and subsequent departures from a dusty airport represents around 10 kg of cumulative dust ingestion,” the study notes.
“The impacts of a controlled dust ingestion test, conducted in 2018, which delivered approximately 5 kg of dust with a composition representative of the region around Dubai, [meant that] the level of contamination in the engine hot sections was enough to result in accelerated engine performance deterioration and substantially reduced component lives.”
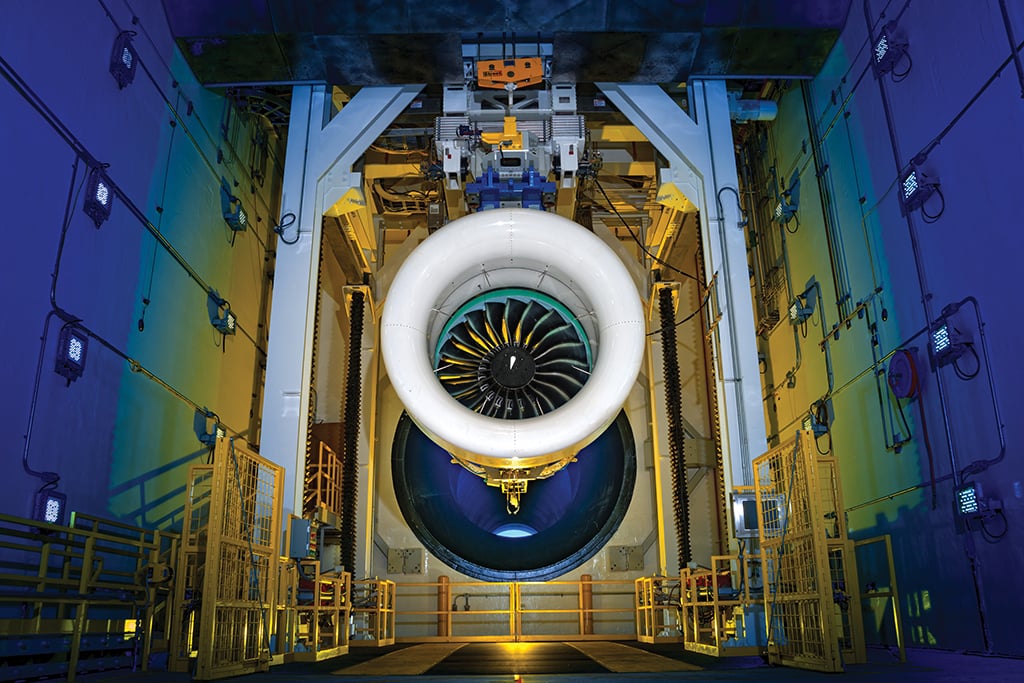
Greatest damage is caused during take-off and climb, when the engine is at its hottest, Rolls-Royce technical lead, R&T demonstrators hot end Andy Mitchell explained.
“During these flight phases, dust gets drawn into the engine core, broken up into smaller pieces and eventually melts onto the hot turbine blades,” he said.
“This molten rock, calcium-magnesium aluminosilicate, or CMAS, can seep between the material components of the turbine blades as they expand and contract in the changing temperatures. Over time, this breaks down the turbine blade thermal barrier, meaning more frequent servicing and downtime for the aircraft.”
Mitchell said that older generation engines were less susceptible to damage because they operated at lower temperatures than, for example, the Trent XWB-97, which powers the Airbus A350-1000.
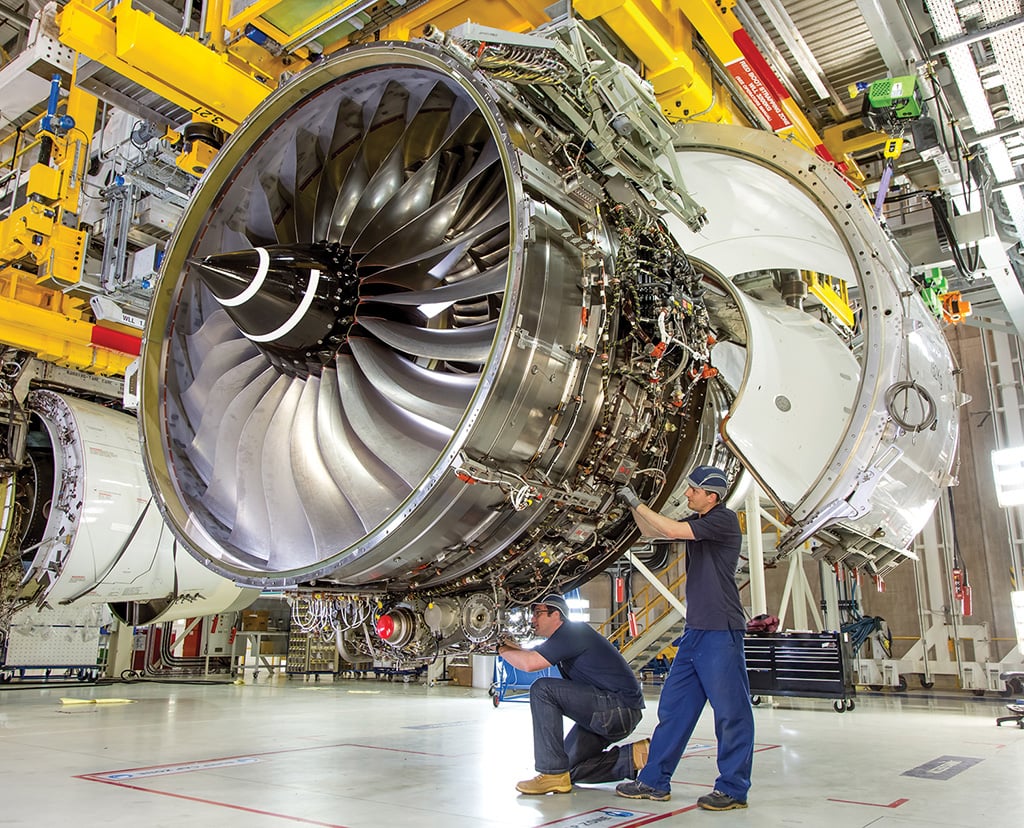
The problem has spurred research into keeping engines cool in hot and harsh environments.
“At Rolls-Royce, we’ve developed and tested an innovative new coating that increases the lifetime of these thermal barriers and extends time on wing by up to 30%,” Mitchell said. “The coating is made up of a gadolinium zirconate, which interacts with the CMAS to increase its viscosity, so it doesn’t penetrate the material in the same way. This coating is now in service on the Trent XWB-97.”
Developing the coating “meant understanding the workings of the CMAS itself and how its chemical makeup changed as it travelled through an engine,” he added.
A Rolls team worked with geologists and professors at the University of Manchester in the UK, to create a dust that would help simulate the conditions of the Middle East.
“The testing process involved various stages of monitoring the impact of the CMAS on hot materials of up to 1,400°C (2,552°F). We ran what we call rainbow tests, applying different standards of the coating to the 62 turbine blades to assess the comparative results.”
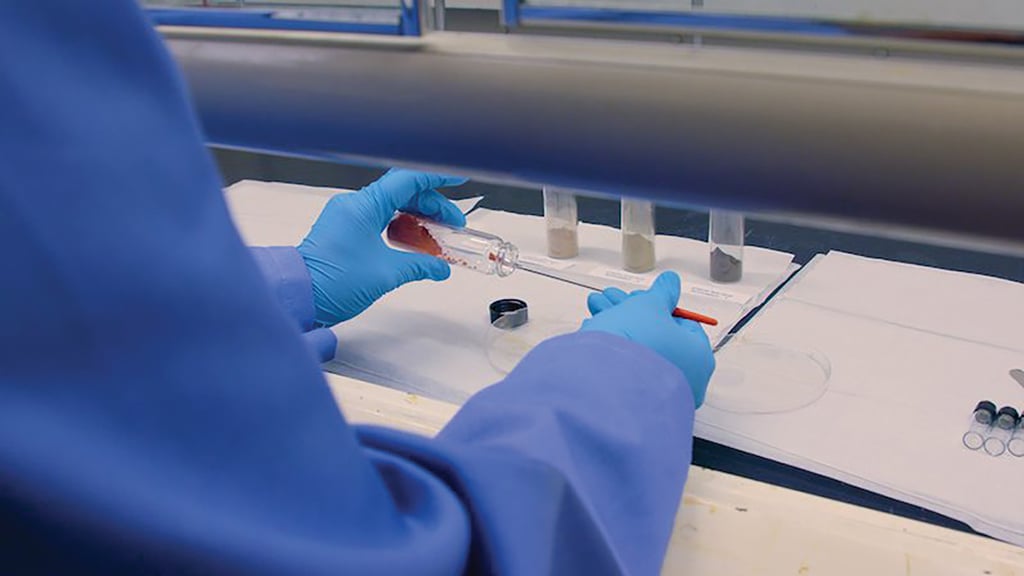
The need to find a solution to the dust problem is pressing, said Michael Winter, chief scientist at Pratt & Whitney parent company RTX.
“Some of the strongest future growth in aviation demand is expected to be in regions of the world with hotter, dustier operating environments.”
With that in mind, Pratt has developed several measures to mitigate the problem, including an advanced high-turbine airfoil incorporating proven CMAS-resistant coating technologies; optimized cooling hole size, shapes and location for the combustor and high-pressure turbine; and advanced alloy turbine blades that provide more efficient cooling and have coatings to reduce oxidation and corrosion effects.
“The GTF Advantage engine, the next evolution of the powerplant, is fundamentally a more durable configuration. We’ve combined increased airflow through the core, which delivers more thrust while lowering operating temperatures, and a state-of-the-art hot section to increase time on wing,” Winter said.
RTX is also developing measures to minimize exposure to damaging dust conditions, he added.
“For example, Collins Aerospace [also an RTX company] manages air traffic control through satellites and ground stations, providing operators with real-time weather updates to inform flight paths, and real-time tracking with FlightAware, along with flight path adaptation [and] recommendation software.”
Meanwhile, GE Aerospace engineers have turned to the unlikely ingredient of “pixie dust” to help understand the problems faced by the CFM International LEAP.
In a GE Reports article, GE Aerospace services engineering manager Carlos Perez recalled dust tests of the early 2000s on LEAP’s predecessor, the CFM56.
“We used sand, because our hypothesis was that this dust was coming right off the side of the runway. We put a dustpan filled with Arizona road dust in front of the engine to see what happened,” he wrote.
Perhaps unsurprisingly, there was damage to the engine’s fan blades.
However, some re-engineering of the dust was necessary, as firing a collection of tiny stones and pebbles into the fan did not replicate real-life conditions.
GE Aerospace engineers analyzed typical desert conditions and quickly discovered that the problem was not with ground-level dust, but airborne particles.
“These immensely powerful jet engines were being degraded by this really fine dust suspended in the air. We’re talking about particles that are one-tenth of the width of a human hair,” Perez wrote.
GE therefore created its “pixie dust.”
“Working with three PhD-level geologists, we’ve manufactured our own concoction,” Perez explained. The resulting compound has the consistency of talcum powder, which floats in the air like smoke rather than falling to the ground.
To simulate the flow of this ultra-fine dust, engineers then built a metal structure in front of a LEAP engine on a test stand, which supported equipment that could regulate dust flow right into the core of the engine. This enabled them to repeat engine cycles thousands of times.