Beta Opens Electric Aircraft Manufacturing Plant, Launches Production

Beta’s first Alia proof-of-concept demonstrator has been flying in eCTOL configuration since June 2022.
While publicly traded electric aircraft startups trumpet every financial and technical milestone to reassure shareholders, Beta Technologies has made substantial progress within the relative sanctuary of private ownership.
Two piloted, full-scale demonstrators have logged more than 500 flights, with both conventional and vertical takeoffs and landings. Hundreds of electric motors have completed more than 10,000 hr. of ground testing. And on Oct. 2, Beta opened its manufacturing facility at Patrick Leahy Burlington International Airport in Vermont.
- The manufacturing facility can produce 300 aircraft a year
- A type-design motor is flying on demonstrators
- Production-intent battery systems are taking shape
A visit by Aviation Week to Burlington in August underlined Beta’s quiet progress, from the aircraft on routine test flights, motors undergoing endurance runs and battery packs being built to the wing-assembly fixture already in position in the nearly complete manufacturing facility.
This is not a pilot production facility like those where Joby Aviation and Archer Aviation are assembling their first aircraft. The first prototypes of Beta’s electric aircraft will be manufactured on the same tooling and in the same building where certified production aircraft are scheduled to begin rolling off the line in 2025.
Those first aircraft will be the CX300 electric conventional-takeoff-and-landing (eCTOL) version of Beta’s Alia design. The startup decided in 2022 that customer demand for an electric aircraft justified moving ahead first with a fixed-wing version that would be easier to certify. FAA certification is targeted for 2025.
CX300 deliveries to customers such as Bristow Group and United Therapeutics will bring in revenue while Beta continues development of the A250 electric vertical-takeoff-and-landing (eVTOL) version of the Alia, planned for certification in 2026. Both versions are 80% common and will be built on the same tooling.
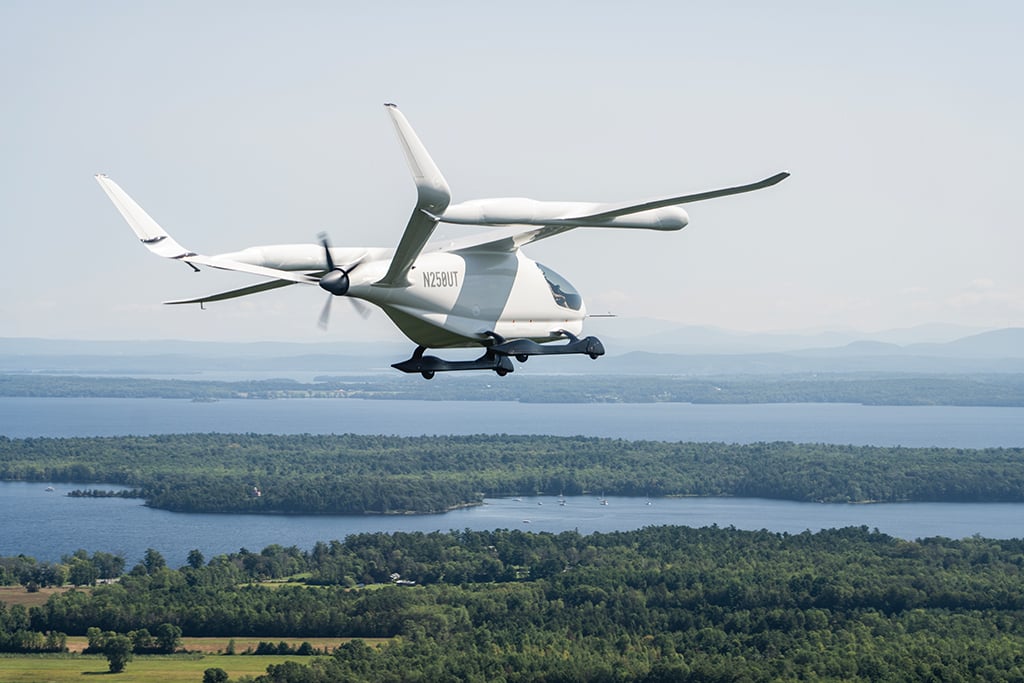
INDUSTRIALIZING ALIA
Founded in 2017, Beta has raised more than $800 million from private investors, ranking it fourth in the advanced air mobility industry in total funding secured behind Joby, Archer and Lilium. Beta says it has invested more than $150 million in capital facilities, including the manufacturing plant.
Rather than be vertically integrated like Joby or outsource major aerostructures like Archer, Beta has elected to buy parts and assemble aircraft in-house. This will allow the startup to keep control of process changes as production ramps up and decide when and where to invest and automate.
Albany Engineered Composites (AEC), a supplier to Boeing and Airbus, is providing the “big bones” of the Alia’s composite primary structure. Automated tape-laying of the first wing skin was completed in late August at AEC in Salt Lake City. Solvay is supplying the carbon-fiber prepreg material system.
Other supplier partners announced by Beta include Garmin for the integrated flight deck, Triumph for the landing gear and Hartzell for the pusher propeller, which is fitted to both the eCTOL and eVTOL versions. Sensata Technologies is providing the pilot inceptors and Volz Servos the electromechanical rotary actuators for the flight control surfaces.
Advanced Integration Technology is providing the assembly tooling and equipment as well as supplying tooling to Beta’s composite parts suppliers. There are assembly positions for the wing, booms, empennage, fuselage and final assembly. Built on a 60-ft. tool, the one-piece wing is common to both Alia versions, although the eCTOL version does not have high-voltage wiring for the lift motors on the eVTOL variant.
Built on a 40-acre site and entirely powered by solar and geothermal energy, the 188,500-ft.² facility is designed for a production rate of up to 300 aircraft a year but could double its size in a Phase 2 expansion.
Beta also has locations in Montreal; Plattsburgh, New York; Raleigh, North Carolina; Springfield, Ohio; and Washington. A former Strategic Air Command airbase and a short flight from Burlington across Lake Champlain, Plattsburgh International Airport is home to Beta’s flight-test center, where two hangars house the demonstrators, telemetry system, pilot briefing facilities and test control room.
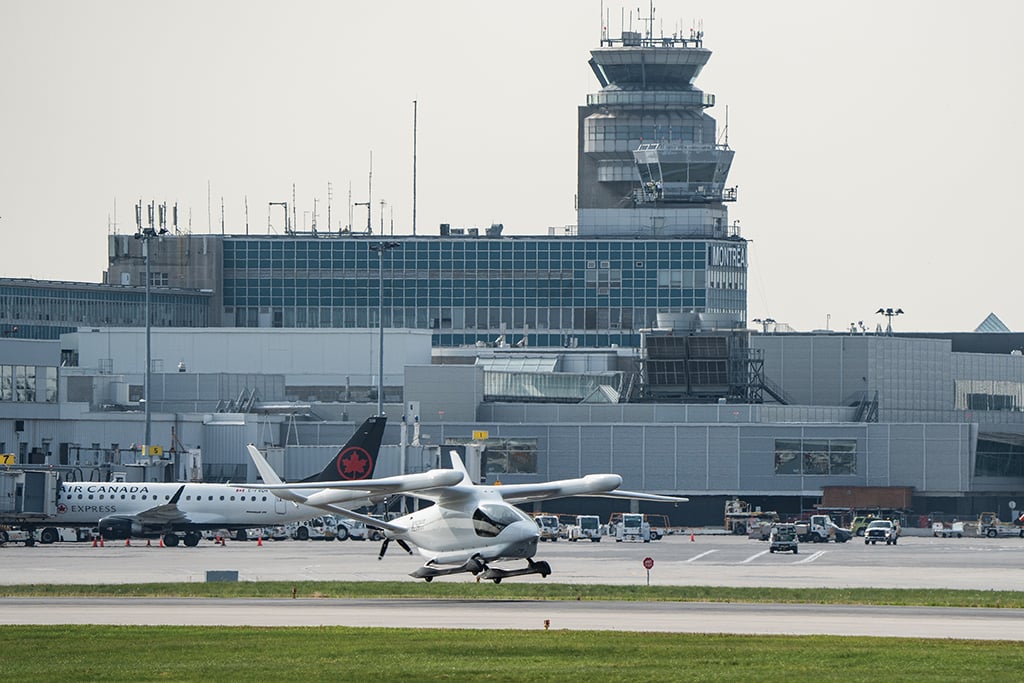
Expected to roll off the assembly line before year-end, the first prototypes will be used to prove out the manufacturing process and then go into testing with customers rather than straight into for-credit tests for FAA certification.
“Those first three or four aircraft are really line-commissioning aircraft,” says Kyle Clark, Beta’s founder and CEO. “We could put them straight into for-credit tests. We aren’t going to, for two reasons. One, there is a bit of a mind shift in aerospace around electrification, where we’re finding the ability to sell precertified aircraft. The other is that the learning curve is still really steep on not so much the design, but the process. And we will have a faster type and production certification if we tighten up that process.”
“In this refinement of commissioning the line, we’re really testing all the elements of industrialization not talked about publicly,” he says. “That includes the business systems, the quality management systems, the employee training handbooks and the billing mechanisms.”
The first structure that will go into conforming-article structural testing will come before the first fully conforming aircraft rolls off the line. “The reason is because we want to learn as much as we can about the airframe,” Clark says. “If there’s a problem, we want to know it soon. So we’ll actually break our first wing before we build our first airplane.”
VISIBLE PROGRESS
Beyond the manufacturing facility, evidence of Beta’s substantial progress is visible also in the test rigs, motor testing, battery assembly, aircraft charger and flight-training activities underway in other buildings around the Burlington airport.
An array of test rigs is visible through the fireproof glass that lines the office level looking into Beta’s research and development hangar. This openness is deliberate. “Teamwork, empathy and innovation don’t happen by email,” says Blain Newton, Beta chief operating officer. “Here you can see clear across the hangar, go talk to someone and create unintentional collisions.”
In the hangar itself is the final assembly line test rig or “FAL Bird.” This is a full-scale mockup of the vehicle, made from wood and 3D-printed parts, used to understand the integration of systems and sequencing of assembly and provide feedback into design for manufacturing and maintenance.
The focus is on areas where there is overlap, with the objective of de-risking the design before assembly of the actual vehicle begins. One example is access to the environmental control system in the nose with the correct tool, which required a redesign of the installation.
Across the hangar is the ergonomic test rig, or “Ergo Buck,” another full-scale partial mockup dedicated to crew ingress and egress. “Human factors is one of the most subjective certification areas of aircraft,” Clark says. If how the pilot exits the aircraft in an emergency is an afterthought, “you’re going to be upside down in certification” because it can affect structures, pilot visibility and other issues.
Also in the R&D hangar are the iron bird systems test rig and the proof-of-concept mockup for the flight simulator, which Beta is developing with training partner CAE. The center in which they will provide pilot and maintainer training for customers is adjacent to the manufacturing facility and home to a diverse fleet of aircraft Beta uses for flight testing, transport and training—including for its own employees.
While the Alia is designed for single-pilot, instrument-flight-rules operation, Beta plans to build a two-seat trainer version as well. This complies with the FAA’s proposed operating rule that would require powered-lift pilots to undergo training in a dual-control aircraft. As proposed, the rule is a major obstacle to most other eVTOL developers, as they have designed their aircraft with a single-pilot cockpit.
PROPULSION PIONEER
Beta has focused its in-house development on the electric propulsion system—the pusher motor, lift motors, power electronics and batteries. The startup has also brought the fly-by-wire flight control system in-house after acquiring an experienced development team from a major defense contractor.
Both demonstrator aircraft are now flying with the type-design pusher motors planned for certification, Beta’s sixth generation over four years of development. From Day One, the startup says, the goal was to develop a motor configuration and technology based on manufacturing at a scale beyond what is traditional in aerospace.
“What makes a high-performance motor good for aviation? The least complexity. So we remove things that fail,” says Manon Belzile, motor team leader. Beta’s motors are direct-drive and air-cooled, eliminating gearboxes and liquid-cooling. Two motors power the pusher propeller and each of the four lift props on the eVTOL version. Each motor is itself dual-redundant, with two three-phase windings. Each half of the motor has its own air-cooled silicon-carbide inverter/controller.
With the type-design pusher motor installed, the Alia demonstrator’s climb rate outperforms a Cessna Caravan, Beta test pilot Chris Caputo says. If the motor loses half its power during takeoff, the aircraft can still climb out and safely make the turn back to the departure runway and a downwind landing.
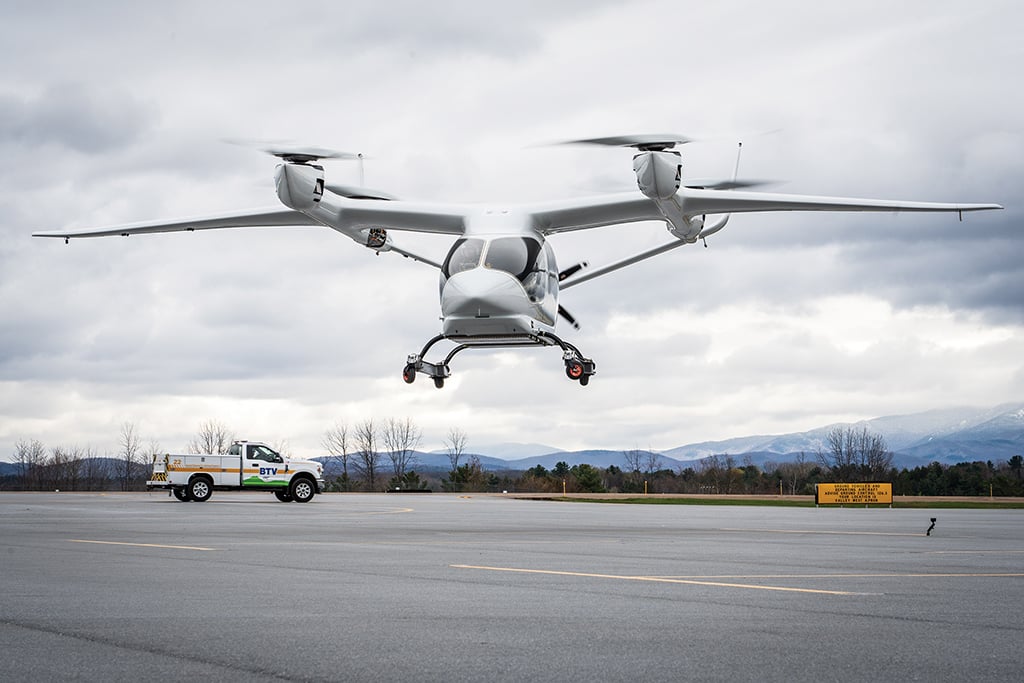
Beta’s motor design has an outer stator and inner rotor, which is easier to stabilize with bearings on a shaft, Belzile says. To date, the company has built 250 motors. The pusher motor has demonstrated 97.5% efficiency in cruise flight, Beta says. The lift motor has the same architecture but is wider and shallower, and cooling air flows differently through the stator. Power density is higher but efficiency slightly lower. The production eVTOL A250 will have two dual-redundant motors on each lift rotor, with a sprag clutch making them mechanically independent.
“It’s not just four motors tied to a shaft; it’s four motors tied in an elegant way,” Clark says. “They’re mechanically decoupled and electrically decoupled, and they have different control systems.”
Where other eVTOL developers have gone with six, 12 or even 18 lift props, Beta has stayed with its four-post design, choosing to put redundancy into motors rather than rotors. “Where you put reliability is in places where there is a propensity to fail,” Clark says. “You do not tolerate the separation of a propeller. That’s a prime reliable component. It can’t separate. But it does happen that engines shut down.
“It is inconceivable to me that a singular motor would ever be prime-reliable,” he continues. “So putting four on a post, all capable of safely landing the aircraft, separated so there’s no galvanic connection between the stators and no mechanical connection in a way that one can fail the other, you end up with a higher redundancy numerically than you do with six single systems.”
PUNISHING TESTING
Beta has multiple pusher and lift motors running endurance tests on dynamometer stands in Burlington and also continuously driving propellers at a “prop farm” across the lake in Plattsburgh. “The ratio of motors built to motors flown is roughly 40 to 1. The motors that we put into containers and heat up and cool down, they’ll never get flown,” Clark says.
So far more than 10,000 hr. of accelerated-life testing has been conducted with motors at elevated operating temperatures to gather reliability data. Endurance dynamometer testing equivalent to years of operation has been completed with no degradation seen on the motors, Beta says.
The pusher motor is the first product the startup plans to certify, by the end of 2024, well ahead of the eCTOL aircraft. The FAA has established the special conditions for Part 33 type certification of an electric engine, and Beta expects to be the first in the U.S. to achieve certification.
The certified pusher motor will then be incorporated into the type certificate for the eCTOL version, which is planned to be certified as a Part 23 general aviation aircraft. The lift motors are scheduled to be approved as part of the eVTOL aircraft’s Part 21.17(b) powered-lift type certificate.
Data collected from all the motor and battery testing, as well as from simulation runs and flight tests, goes into a central repository. This enables the company to understand how variability in manufacturing leads to variations in performance. “The data backbone that we’re aggregating is a phenomenal asset,” Clark says. “The fact that it’s parsable, searchable and operable on is an important part, so that anybody can take that historical data, make a good decision and show the FAA that we have a statistically relevant data set that informs that decision.”
BATTERY EVOLUTION
Beta has also developed its own battery packs, and the fifth generation is flying in the first demonstrator aircraft. The company has built up a manufacturing capability focused on building these packs to support the experimental aircraft while also acting as a sandbox in which to gain experience for production. This includes building to a released design, tracking to the pack serial number and cell production lot, and conforming all the way back to the lithium-ion cell supplier.
The fifth-generation pack uses commercially available cylindrical cells for which the supply chain is mature. The Alia flies with between two and five of the 40-65-kW modular packs in a belly fairing; the number of packs is a trade-off between range and payload. The pack is air-cooled, so cells with low internal resistance are used that generate less heat. At its advanced battery research center in St. Albans, north of Burlington, Beta is testing pouch cells and advanced chemistries that could become available later this decade.
For the production aircraft, Beta has switched to a battery system that is liquid-cooled on the ground while it is being charged and the cells heat up. The production-intent battery now has subpacks with the cylindrical cells on either side of a cold plate. Other design and process improvements have been made for battery production, which is being set up in an area within the new manufacturing facility.
Aircraft charging is a key leg of Beta’s business plan, and the company now has 13 operational sites, mostly in the Eastern U.S. but extending as far as Arkansas. The network is being expanded continuously to support early customers such as Bristow, UPS Flight Forward and the U.S. Air Force’s Agility Prime program. Beta is installing a charging station at Duke Field on Eglin AFB in Florida to support eCTOL flight tests planned to begin this year.
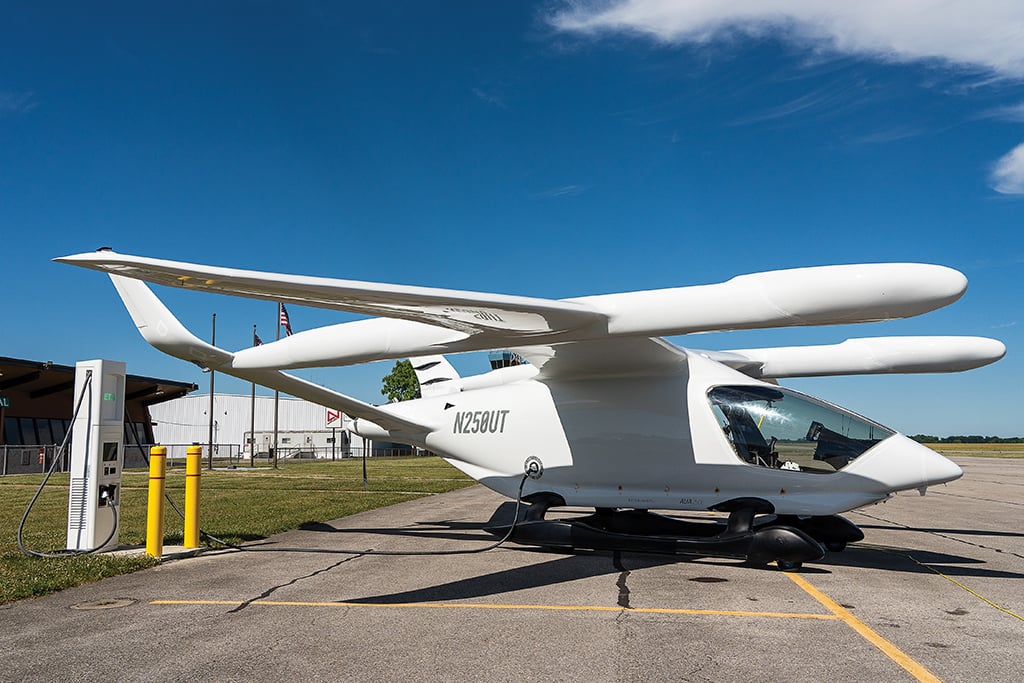
The company’s latest ground support equipment configuration has three modules, or “cubes,” for fast charging, battery conditioning and cabin conditioning. The temperature rise in the batteries during flight is minimized by the aircraft’s efficient design and architecture, Beta says, and any accumulated heat plus heat due to fast charging is removed through a liquid-cooling loop when on the ground. This is a simpler and lighter solution than providing active cooling in flight.
The charging station uses the Combined Charging System (CCS) standard developed for electric vehicles. Under an initiative led by the General Aviation Manufacturers Association and chaired by Beta, most electric aircraft OEMs and several vertiport developers have agreed to adopt the CCS standard.
Beta’s station provides DC fast charging up to 350 kW, enabling a full recharge in 50 min. The cable motors out and back, to prevent the connector from being dropped. And there is no display: A software app keeps track of the operator, aircraft and battery and how much charge is needed for the mission, Newton says.
INTO EXECUTION
The manufacturing facility, training center, R&D hangar, and battery and charger shops in Burlington are all clear signs of the progress Beta has made and evidence that the startup is one of a small handful of electric aircraft developers ready to move into certification and production.
“That’s an indicator to me that the next phase of the business is very much an execution phase built on that plateau of capital that we’ve put down. And so as we work into the execution phase, the question is: What’s our strategy to execute?” Clark says.
“A saying that I learned from Martine Rothblatt in the pharmaceutical world was: ‘Approve then improve.’ We are well aware that our best aircraft, best design, best software, is our next aircraft, next design, next software,” he says. Rothblatt is CEO of United Therapeutics and an early Beta investor and launch customer.
“And so being intensely pragmatic—some may accuse me of being dogmatic—we know what our next step is,” Clark says. “We need to focus on a technology that can be understood and certified today, a market that is willing and able to accept it, in a regulatory framework that works today.”
This is the thinking behind Beta’s decision in 2022 to complete design of the eVTOL Alia and then determine what could be removed to produce a viable eCTOL aircraft that could be brought to market sooner and with less certification risk—in response to a demand signal from customers keen to gain early operating experience with an electric aircraft.
“It seems so clear to me that this market is begging for a stepwise pragmatic entry into service,” Clark says. “So we completed our design on the A250 and submitted our proposed means of compliance to the FAA. And the CTOL aircraft is the A250 minus a bunch of stuff. And that’s really important in that the entire certification basis of the CX300 is portable into 21.17(b).”
That pragmatism is evident across Beta’s activities. The full-scale demonstrators have been piloted from the outset, while other OEMs have flown only remotely piloted. “It drives the thinking,” Clark says. “If we’re going to fly into Class B airfields like Montreal or Lousiville, [Kentucky,] on a motor, it better be a motor that has seen that times 10 in every stressful dimension, voltage, current, temperature, salt fog, humidity—all the things that we have to be really comfortable with before we put ourselves and our customers in the aircraft.”
Aviation Week saw this approach in action during a visit to Beta’s flight-test center in Plattsburgh. In the meticulous preparation for an eCTOL test flight, the test director, test pilots and flight-test engineers methodically ran through the procedures that would be required to respond safely to a potential failure unique to an aircraft with electric propulsion and therefore new to the industry.
The demonstrators have gone through multiple incremental improvements in motors and batteries. The eCTOL aircraft now has slimline booms where the eVTOL aircraft has large fairings over the lift motors. The booms will be removed ahead of the wing for the production CX300. Other design changes are tricycle landing gear, a bulkhead between the cockpit and cabin, gull-wing cockpit doors and a larger cargo door.
The eVTOL demonstrator has been flown along the long Plattsburgh runway at up to 62 kt. to begin exploring the transition between thrustborne and wingborne flight. The full transition corridor is expected to be cleared by year-end. Beta has been refining the design of its lift rotors in stages. “I think that the more refined system that will go into the production vehicle . . . that will be a transition that the FAA will consider an average pilot can’t break,” Clark says.
PRACTICAL MAGIC
Beta’s no-nonsense, stepwise approach to introducing electric aviation has resonated with industry analysts. SMG Consulting ranks privately held Beta second to publicly traded Joby in its influential Advanced Air Mobility (AAM) Reality Index. “I would say that the first AAM vehicle going into service is going to be a two-horse race between Joby and Beta, each more advanced than the other in some areas,” says Sergio Cecutta, founder and partner at SMG.
“The strategy of Beta to go eCTOL before eVTOL is a winner, as it allows for the regulations to stabilize while they derisk certification with an aircraft almost identical to the eVTOL,” he says. CX300 deliveries will also generate revenues to help derisk investment in certification of the eVTOL A250.
Finally, Cecutta says, Beta’s cargo-first approach to putting electric aircraft into operational service “allows them to sign up customers that are eagerly waiting for the aircraft, have put deposits down, and that do not have to worry about infrastructure and customer adoption.”
Editor's note: This article has been updated to remove proprietary information at the request of Beta Technologies.