
Boom provided updates on its planned supersonic Symphony engine at Farnborough Airshow.
FARNBOROUGH—Boom Supersonic is accelerating development of the Symphony engine for its Mach 1.7 Overture airliner and has expanded its partnership with Standard Aero to include production of the powerplant at the maintenance provider's site in San Antonio.
Announcing details of the 35,000-lb.-thrust engine development plan, Boom founder and CEO Blake Scholl says the intent is to begin full-scale core tests in 18 months.
“Our plan is to get to hardware quickly, and let’s learn and iterate," Scholl says. "Eighteen months ago, the Symphony was a sketch on a napkin. Now the conceptual design is complete, and we’ve said, ‘Great, let’s go.’”
Aware of the central importance of the engine design to the success of Boom’s supersonic airliner concept and broader industry confidence in the overall project, Scholl says the plan is to put the propulsion system through a rapid test and development cycle. “The core is the hardest part, so let's go build the first one as quickly as we can, and let's go put it on a test stand. We are 18 months out from that.”
“As we go into next year, the full-scale core of the Symphony should be running on a test stand in prototype form. We'll iterate from there, and that should put us in a place where the rest of the program is more attainable,” Scholl says.
Boom Supersonic has begun rig tests of the combustor section in collaboration with its design partner Florida Turbine Technologies (FTT), a business unit of Kratos. Tests are being conducted at FTT’s design and test facility in Jupiter, Florida, using an additively manufactured one-eighth section of the combustor module. Colibrium Additive, a supplier owned by GE Aerospace, has meanwhile produced the first 3D-printed parts for Symphony, including fuel nozzles and turbine center frames.
The two-spool, medium-bypass turbofan engine will be equipped with a single-stage 72-in.-dia. fan and be optimized for prolonged supersonic operation with an air-cooled, single-stage high-pressure turbine and three-stage low-pressure turbine. The Symphony’s compressor will be made up of a six-stage high-pressure unit and a three-stage low-pressure section, while the engine’s mixed compression supersonic inlet, diffuser and exhaust design is devised to meet Chapter 14 noise levels.
The agreement with StandardAero also marks a key move to industrialize production of the engine for both Overture and, according to Scholl, other potential unidentified high-speed platforms. “There's over 100,000 ft.2 in that facility there that will be dedicated to Symphony and to test cells. That's sufficient to get us to 330 engines a year, which is about where we need to be for full rate on Overture with two final assembly lines—plus we need spares,” Scholl says.
Russ Ford, chairman and CEO of Standard Aero, says: “We began working with the Boom team several years ago, initially to introduce the ideas of maintainability and a sustainable supersonic aircraft engine. Over the last couple of years, we're now pleased to announce that we've expanded that partnership, and we have dedicated a portion of one of our facilities to not only the assembly and test of engines but also full-scale production to really try to be a part of this program.”
Flight Deck Plans
Boom also unveiled additional details of Overture’s flight deck, which is based on Honeywell’s new Anthem avionics suite with four main 17-in. touchscreen multifunction displays. Features now include BAE Systems' active control force-feedback sidesticks, which will enable pilots to physically feel both aircraft response and inputs made by each crewmember or the autopilot. Although active sidesticks are increasingly used in military aircraft and new business jets, their use on Overture represents their first planned installation in a Western civil airliner.
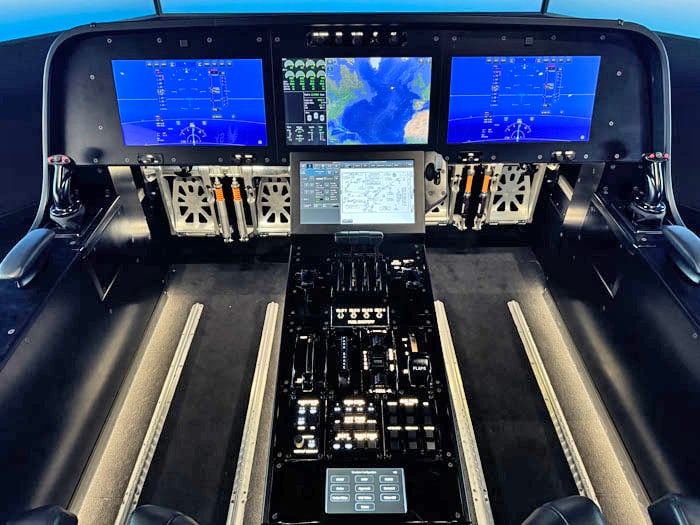
Building on the system flown on the company’s XB-1 supersonic demonstrator, Overture will also incorporate an advanced augmented reality vision system for takeoff and landing, eliminating the need for the droop nose used on the Anglo-French Concorde. Crew will also be aided by an autoland system or augmented reality views provided on the primary flight display and a head-worn device developed by Universal Avionics.
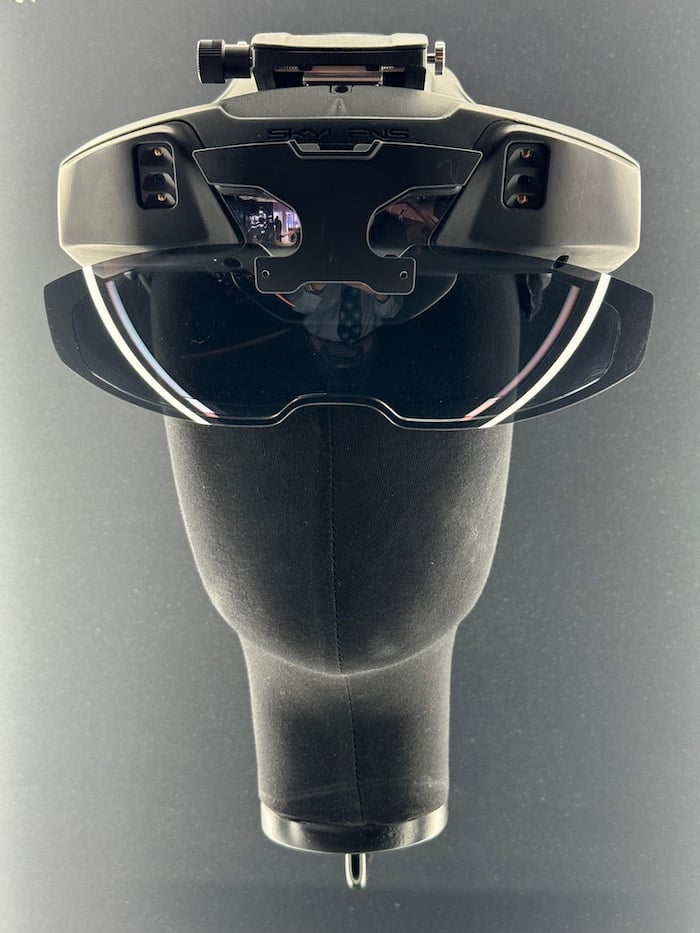
By combining active sidesticks and full envelope protection with the ability to provide pilots with override capability, Scholl says the Overture flight deck represents a new cockpit design philosophy that builds on the best of Airbus and Boeing.
On the airframe production side, Boom took possession of its newly constructed 200,000-ft.2 final assembly building in Greensboro, North Carolina, in June. Located at Piedmont Triad International Airport, the facility is sized for an initial rate of 33 aircraft per year. Construction work started at the site in January 2023 and was completed six months ahead of Boom’s initial schedule.
Tooling for the supersonic airliner is being developed by Plano, Texas-based Advanced Integration Technology (AIT), which is a supplier of turnkey custom machines and tooling as well as equipment and services for fabrication, machining and assembly. “We expect to be installing the first test cell around the end of this year or early next,” Scholl says.
Supplier partners are also accelerating their work on Overture structures and systems, Scholl says. Aernnova and Aciturri of Spain are developing the Overture wings and empennage, respectively, while Italy's Leonardo will provide the fuselage and wing box.
“Leonardo and Aernnova have started their wing work, and there's a Leonardo team that sits with us at our headquarters in Denver, working hand in hand on the airplane," Scholl says. "That's a relatively small group now, and next year we'll get a lot bigger. The major 2024 milestone for Overture is to completely freeze everything in the configuration."
Test Flights
Meanwhile, Boom’s XB-1 demonstrator is expected to make its second flight by the end of July following flight control system modifications. The aircraft, which made its first flight from Mojave Air & Space Port, California, on March 22, is central to proving the company’s ability to execute and demonstrate a supersonic flight-test program, as well as grow know-how in engineering software, digital modeling and production methods.
To continue test flights, the company is activating elements of an already-developed stability augmentation system and reducing the gain in roll with a combination of software and hardware modifications in the flight control system. The changes, which involve adding a damper to the mechanical portion of the control cabling, are intended to reduce pilot workload and enable the program to push forward to supersonic flights later this year.
“We actually had better-than-forecast handling qualities on both pitch and yaw," Scholl says. "But as our test pilot put it, roll was a little bit 'exciting,' so to reduce pilot workload, in the interest of safety, we decided to add a digital stability augmentation system for roll. And the team developed that in record time and just about eight weeks.”
The aircraft is expected to conduct a final taxi test on July 23 with the roll stability system activated. “Assuming today's test goes well we are going to be back in the air for flight two as soon as weather permits, most likely well within the next week," Scholl says. "This keeps us on track to break the sound barrier later this year, and at that moment XB-1 will become the first independently developed supersonic jet to fly faster than the speed of sound."