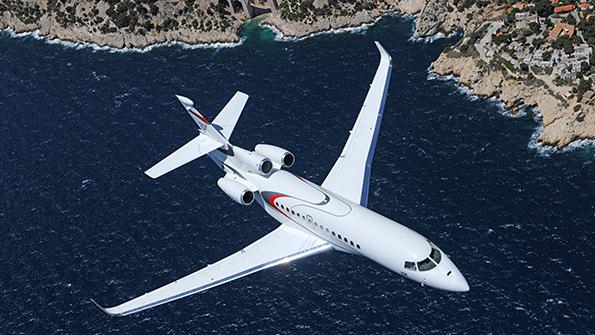
Dassault’s Falcon business jets have long been praised for their fuel efficiency and flying qualities, and its current flagship Falcon 8X is no exception. Compared to the Gulfstream GVII-G500 that I fly in my full-time job, the Falcon 8X is about 10 ft. shorter and 7,000 lb. lighter. But if you need to carry eight passengers a long distance, the 8X will go 6,450 nm at Mach 0.80, much farther than the G500’s 5,300 nm at Mach 0.85.
Besides maintaining the marque’s legendary efficiency, the latest Falcons are notable for their advanced digital flight control system (DFCS). Dassault says that with its latest DFCS, the pilot flies a “trajectory rather than an attitude.” In a closed-loop, trajectory-based flight control system, the pilot sets the desired path, and the DFCS monitors the resulting path, using control-law logic to move the surfaces as necessary to match the desired path.
Invited by Dassault to fly the Falcon 8X, I wanted to understand the aircraft’s ability to extract so much performance from every drop of fuel and also to explore the unfamiliar “closed-loop” and “path-stable” concepts behind its fly-by-wire (FBW) flight control system.
Dassault Falcon Jet Chief Pilot Franco Nese brought the 8X demonstrator to Hanscom Field in Bedford, Massachusetts. The aircraft’s ramp presence is misleading. It is smaller than other ultra-long-range business jets in terms of length and fuselage height. But upon entering the cabin, all preconceived notions of size evaporate. At 74 in. high, 92 in. wide and 42.8 ft. in length, the 8X’s cabin nearly equals that of the G500.
My attention was drawn to the cockpit and the EASy III avionics. The system is based on Honeywell’s Primus Epic avionics, as used by other manufacturers but tailored for Dassault as the Enhanced Avionics System (EASy).
Thanks to my experience with Gulfstream Primus Epic systems, I was immediately comfortable. The four 14.1-in. displays are arranged in a “T” configuration—an integrated primary flight display (IPFD) for each pilot, with two multifunction display units (MDU) stacked vertically in the center. Each pilot has access to ownside and center displays through dedicated cursor control devices (CCD) with trackballs and multifunction keyboards.
The cockpit feels spacious, owing to the wide fuselage and absence of control yokes in front of each pilot. The layout is designed to minimize workload, with all flight avionics directly in front of each pilot and a guidance panel for flight director and autopilot on the center eyebrow panel.
Each pilot has an electronic flight bag (EFB) outboard of their IPFD. The EFBs are Windows tablets that can be loaded with approach charts and other applications, including Dassault’s FalconSphere II suite of performance calculation, dispatch, documentation and planning apps.
Other than the EFBs, none of the displays are touch screens. Most systems are accessed through physical controls and adhere to the “dark cockpit” concept: If they are not illuminated, they are in a good flight mode. The final distinguishing components of the cockpit are the dual sidesticks and large head-up display (HUD). There are plans for a dual HUD installation this year.
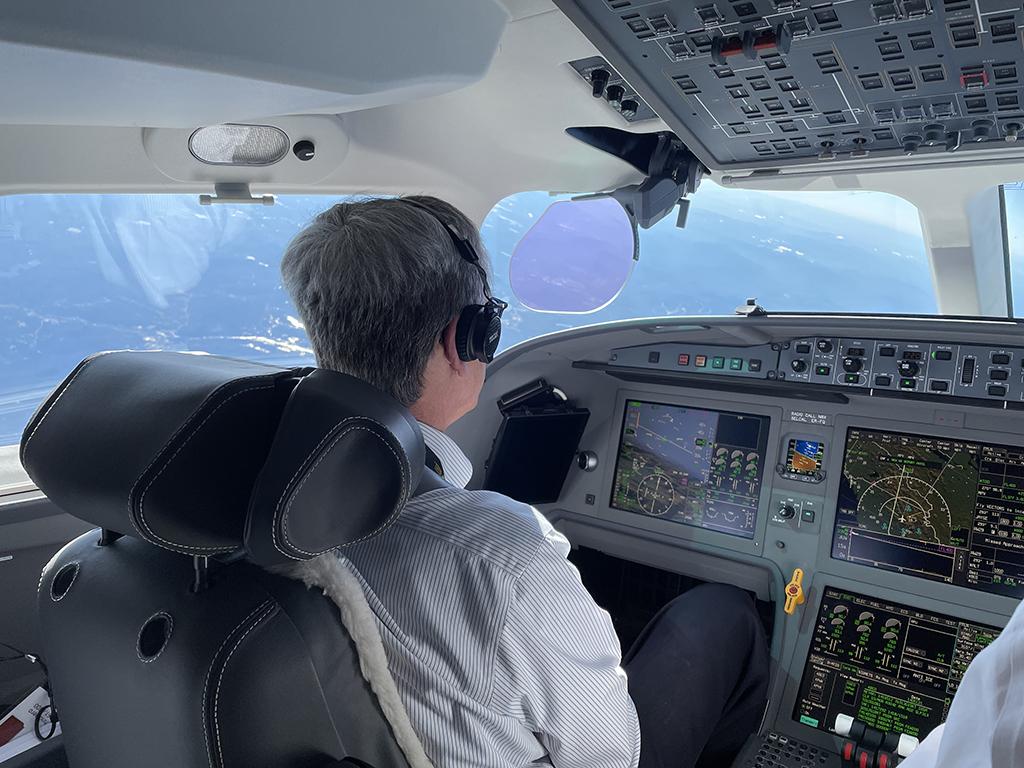
Nese downloaded the flight plan using the aircraft’s airborne flight information system. This uses either VHF or satellite data link, automatically prioritizing VHF if available. The downloaded flight plan is displayed in the center top display in a large waypoint list window. The flight plan can be modified by using the CCDs to select the desired waypoint and the keyboard to make the changes, or changes can be made directly on the map display.
Engine start is accomplished by moving the selected engine’s fuel switch from OFF to ON and rotating another switch to START. The full-authority digital engine control handles the start from that point on. Aircraft electrical and pneumatic systems switch automatically from the auxiliary power unit (APU) to engine electrical and air outputs.
After all three of the 8X’s 6,722-lb.-thrust Pratt & Whitney PW307D turbofans were started, Nese untied the electrical bus, shut down the APU and completed several systems checks. The flight control check is conventional except that it is accomplished by each pilot in turn and then by the FBW system itself.
The sidesticks are not linked mechanically and do not move in response to inputs from the other pilot, autopilot or air loads on the control surfaces. I asked to see what happens when both pilots move their sidesticks in opposition. Nese moved his stick to the right stop and asked me to move mine left. A voice announced “Dual input” and the stick vibrated.
How to best alert pilots to a dual input has been a hot topic since the 2009 crash of an Air France Airbus A330. In that accident, the right-seat pilot was pulling his stick full aft, causing the aircraft to stall. The left-seat pilot was pushing his stick full forward, attempting to recover, but the right-seat pilot had priority. Neither was aware of the dual input. The crash could have been prevented had the left-seat pilot understood he was not in control.
I think auditory senses are the first to go in a highly stressful situation, and an audible alert is insufficient. The haptic feedback on the 8X stick is better—the vibration in your hand is hard to miss. Another solution is to have one stick move in response to the other, as with Gulfstream’s active sidestick. I prefer that but was still learning the 8X’s “hands off” approach to flying.
Once we completed our flight control checks, Nese prompted the FBW system to perform its own check. While it is only required once every 24-hr. period, he activated the check for my benefit. Most manufacturers opt for three flight control computers, including a backup. The 8X has a total of six—three main and three secondary—as well as an additional backup computer.
We were ready to taxi in a few minutes. The nosewheel steer-by-wire is electrically controlled and hydraulically actuated for a maximum of 60-deg. turning authority at low speeds, decreasing as speed increases. Once we were moving at a fair pace, idle thrust was more than sufficient to maintain taxi speed.
Nese selected Slats Flaps 1, or “SF1” in Falcon-speak, which means all six leading edge slats and the trailing edge flaps extended to 9 deg. SF2 is also available for takeoff, increasing the flap angle to 20 deg. Slats and flaps are selected manually through a four-position handle (SF0, SF1, SF2, SF3) or can be deployed automatically by the flight control system if necessary to reduce the angle of attack.
We then reviewed our performance numbers, generated by the avionics and displayed on the bottom MDU. The aircraft had just under 10,000 lb. of fuel added to our basic operating weight of 36,100 lb. and three pilots, bringing our takeoff gross weight to 46,400 lb. The weather was clear, temperature around 20C (68F), and we had a right-quartering headwind, giving us our performance numbers and a takeoff distance of 2,813 ft.
Once cleared for takeoff, I aligned the aircraft with the runway and moved all three throttles to their forward limit, the takeoff detent. The aircraft accelerated nicely and in a few seconds reached the 111-kt. VR (rotation speed), and I pulled back on the sidestick to increase pitch to about 20 deg. With a positive rate of climb, Nese retracted the landing gear and, passing 400 ft., the slats and flaps.
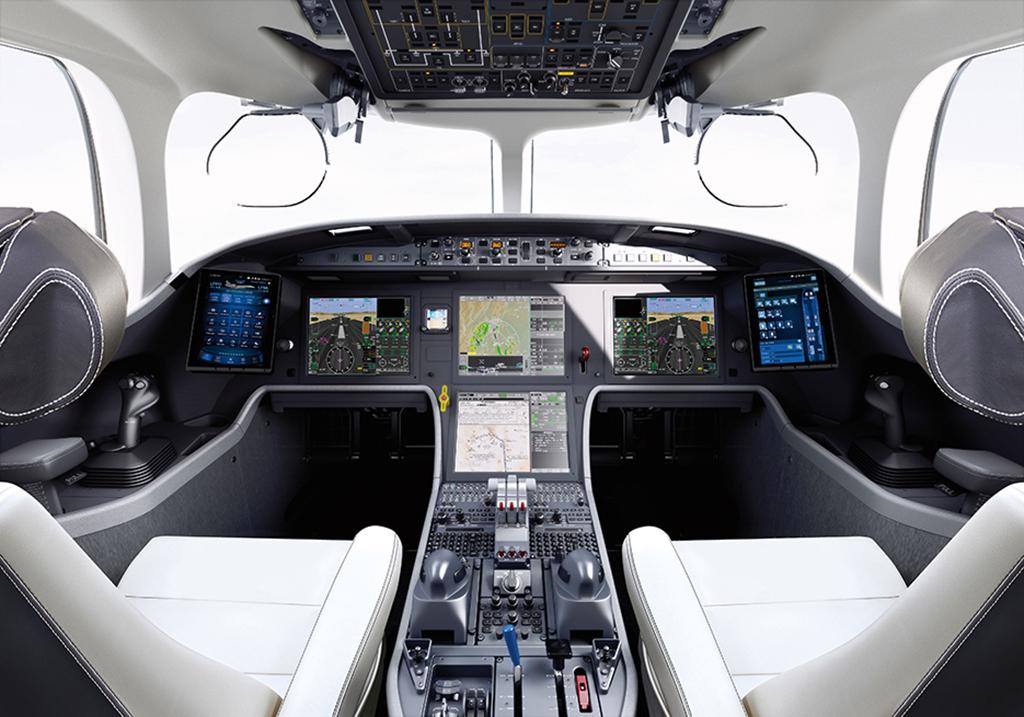
The pull on the stick took more force than I expected. Falcon 8X instructors teach students to move the stick until the path of the aircraft is as desired, then release the stick and guard it. Climbing through 500 ft., I released the stick and watched the nose stay right where I had left it.
The DFCS is designed to maintain the pilot-commanded bank angle “hands off” up to 35 deg. of bank unless disturbed. If the pilot rolls into 15 deg. of bank and turbulence increases it, the flight control system counteracts the disturbance. In pitch, the “flightpath stable” aspect of the DFCS adjusts the controls to maintain the desired flightpath angle.
I selected “Climb” mode—something others call “Flight Level Change”—-and the flight director displayed a magenta bar showing the path needed to maintain our desired climb speed. The auto-speed climb schedule starts at V2+10 kt. (takeoff safety speed) until cleaned up, 200 kt. until out of the airport traffic area, 250 kt. to 10,000 ft., 260 kt. to Mach changeover, then Mach 0.78.
A new litmus test for what makes a business jet fast is having a maximum operating Mach (MMO) speed of at least Mach 0.90, and the 8X does not disappoint. As maximum range numbers are based on a more economical Mach 0.80, I wanted to evaluate the differences in flight characteristics, noise levels and fuel burns. The aircraft’s maximum operating altitude is 51,000 ft., but I opted for 41,000 ft. to avoid having to don an oxygen mask.
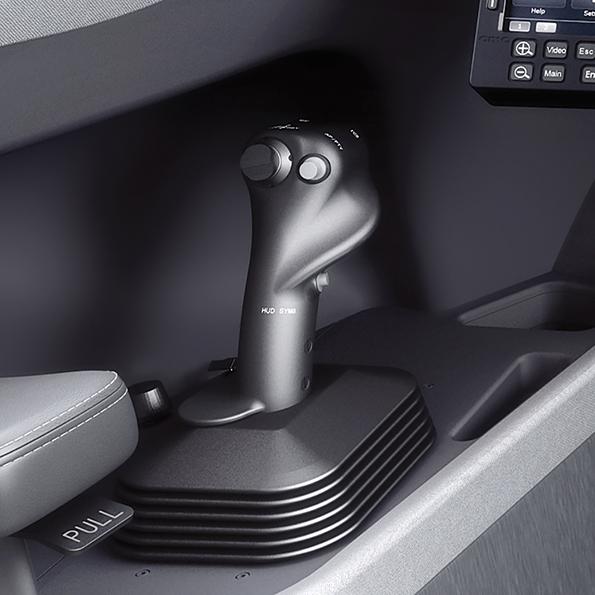
We made it to 41,000 ft. rather quickly, in about 17 min., at the recommended climb speed of Mach 0.78. In a few seconds, we stabilized at Mach 0.80. The aircraft was light at 44,700 lb., and the outside air temperature was nearly at standard, ISA+2C. The cockpit was very quiet, and the total fuel burn was 2,270 lb./hr. For comparison, I’ve flown a G500 in similar conditions at Mach 0.80 with a slightly higher total fuel burn of 2,300 lb./hr.
I then pushed the engines to maximum continuous thrust and watched the airspeed climb to Mach 0.878 but no further. We were at 44,500 lb., and the temperature was ISA+3C. Total fuel burn was 2,880 lb./hr. Most notably, the cockpit was still quiet. The G500 in similar conditions easily made it to Mach 0.90 with a fuel burn of 3,050 lb./hr. The G500’s cockpit, however, becomes noticeably noisier when above Mach 0.85.
The 8X does have lower fuel flows, but its superior range appears mainly due to its higher fuel capacity of 35,141 lb. compared to the G500’s maximum of 30,250 lb.
Nese then arranged for a block of airspace between Flight Level 390 (FL 390) and FL 410 (39,000-41,000 ft.) and asked me to complete a left 360-deg. turn at 60 deg. of bank. He clearly had something in mind, so I dutifully rolled into 60 deg. of bank and applied whatever back pressure was needed to nail the altitude. Placing the flightpath vector (FPV) on the zero-pitch reference line (ZPRL) made quick work of that, and the altitude indication remained glued to 40,000 ft.
Up to 35 deg. of bank I did not need any back pressure at all, but above that the FPV started to nudge downward, and I needed aft stick to hold altitude. As we approached 60 deg. of bank and 2g, the aft force was considerable. Even with altitude and bank angle rock steady, the airspeed needle hardly moved. The autothrottles were responsible for the precision, but the fact that we had enough thrust to do that at 40,000 ft. was impressive.
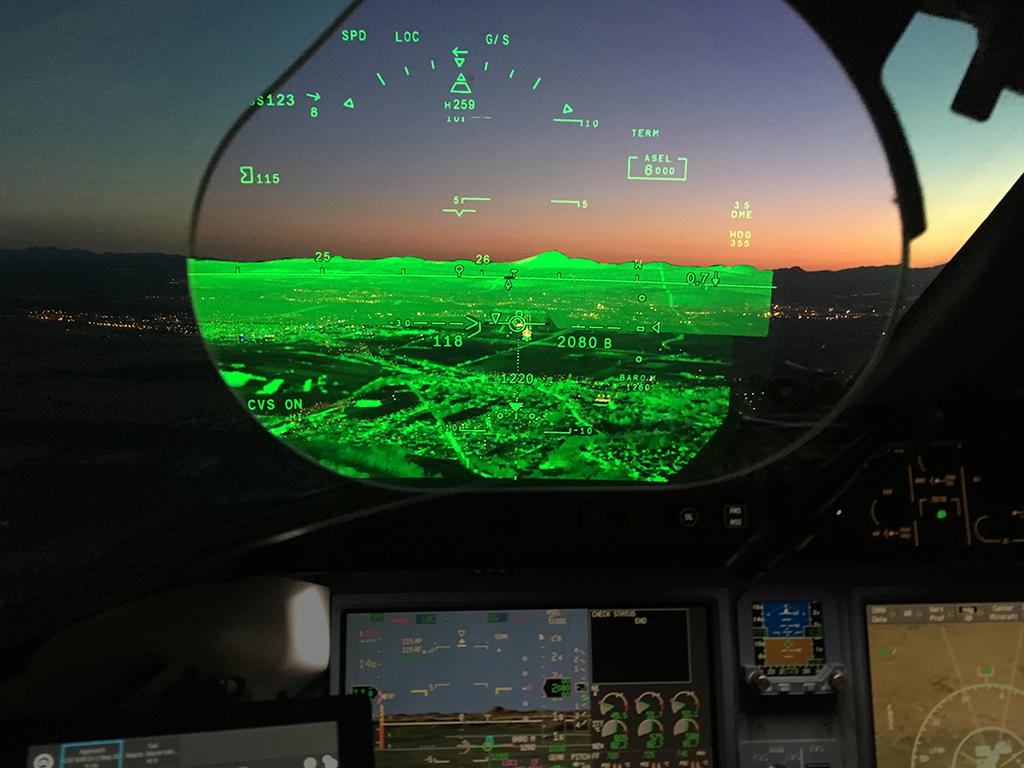
Nese suggested 10 deg. of lead would be ample to roll out. I thought that would not be enough but waited until we were 10 deg. off heading and then rolled. It was more than enough, due to the 8X’s nimble roll response.
I tend to think of maneuverability and stability as inversely related: The more maneuverable an aircraft is, the less stable it tends to be, and vice versa. So far, the DFCS seemed to break that rule—the 8X was both maneuverable and stable at these speeds.
We received clearance for an unrestricted descent to FL 230. With the autopilot engaged, I pushed the nose down to about 20 deg. below level flight. As we approached the Mach 0.90 MMO/370 KIAS VMO (knots indicated airspeed maximum operating speed), the autothrottles pulled back to maintain the limiting speed. Nese said this was a function of the automatic flight control system, which could be removed by disengaging the autopilot.
I disengaged the autopilot and pushed the nose farther down. The DFCS would have none of that and limited my pitch to prevent overspeeding the aircraft. The aircraft remained fully controllable in all axes, and as we neared our target altitude, I pulled aft on the stick to reduce our descent rate and level us at FL 230, then released the stick. Putting the FPV on the ZPRL results in level flight, as it does with any aircraft with an FPV. What sets the Falcon 8X apart is that when you take your hand off the stick, it stays there.
Once we were level, with autopilot and autothrottles still disconnected, I pulled the throttles to idle and watched as the aircraft maintained level flight while we configured with landing gear down and full flaps, SF3. Once speed decayed to below around 110 kt., a warning voice commanded “Increase speed, increase speed,” leading-edge slats automatically deployed, and I was able to keep us level with added aft stick until I reached the aft stop. Once we reached about 90 kt., the aircraft started a gentle descent at 400-500 ft./min. The lowest speed I saw was 88 kt. before recovering with thrust.
Once level again, Nese negotiated our return to Bedford with Boston Center as I played with the pitch and started to come to terms with the “closed-loop” fly-by-wire system. Half the 8X pilots I talked to said the aircraft flies like any other. But the other half said, “Move the stick, release and guard,” to take full advantage of the aircraft’s “path-stable” flight control system. It turns out both are right. You can fly the 8X like any other aircraft. But only the “release and guard” pilots are taking full advantage of the closed-loop FBW.
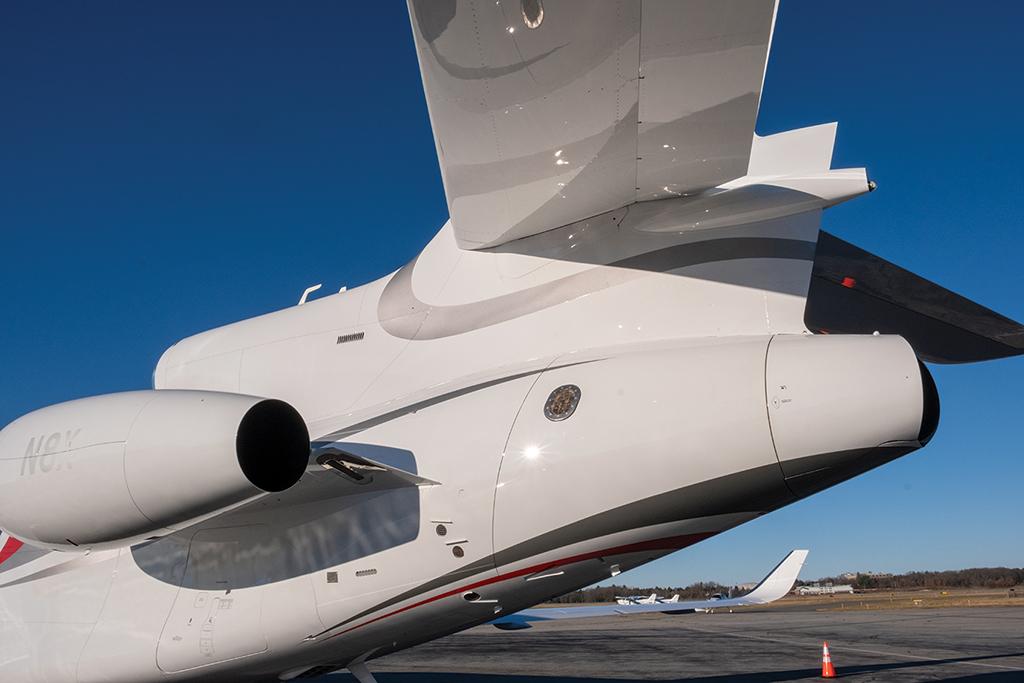
In a conventional aircraft, the pilot closes the control loop by monitoring and adjusting first attitude and then flightpath. A conventional FBW system does not change that input/output flow but adds flight envelope protection.
In the Falcon 8X, the DFCS closes the first loop by moving whatever control surfaces are needed to achieve the desired aircraft attitude. The pilot moves the stick to establish an aircraft path or trajectory, and the DFCS does whatever it takes to achieve and maintain that path, provided it is within the aircraft’s flight envelope. The DFCS then monitors the actual aircraft trajectory with its inertial reference systems and other computers to close the second loop.
The Bedford pattern was busy, and we were instructed to intercept a long final approach, giving me a chance to better understand the “path-stable” and “trajectory-based” flight control system. On final, I was able to see that positioning the FPV to establish a desired descent rate was quite easy. In non-Falcon terms, I moved the stick to put the nose where I wanted it, took my hand off the stick, and the nose stayed where I left it.
The limiting flap speeds are tightly spaced at 200, 190 and 180 KIAS for SF1, SF2 and SF3. The landing gear operating speed is also 200 KIAS. Once at 200 kt., we quickly configured and settled on an SF3 approach speed of 117 kt. at a gross weight of just over 43,000 lb.
Once we intercepted the glidepath, I placed the FPV on the touchdown zone of the runway using the HUD and took my hand off the stick. The FPV just stayed there, even as the wind changed in direction and increased in velocity as we descended.
The synthetic vision system (SVS) showed a clear view of the terrain on the top portion of the HUD. The bottom depicted the view from the enhanced vision system (EVS). Unlike other EVS installations, the Falcon 8X’s FalconEye system uses a combination of six sensors that fuse infrared and visible light together to create a combined vision system (CVS).
With the runway clearly in view, I used the panel-mounted SVS Split control to maximize the SVS display. The system automatically cuts out a trapezoid for the EVS image where the runway appears. This ensures pilots are seeing an actual view of the runway, not one generated by an SVS database. Even in daylight visual conditions, the utility of the system was clear. Adding the SVS makes this a much better HUD solution than any other I have seen.
I pulled the throttles to idle at about 30 ft., and we touched down right at the 1,000-ft. fixed distance markers. Fully deploying the center engine’s thrust reverser and applying moderate pressure to the wheel brakes brought us to taxi speed in less than 3,000 ft.
As someone who started flying business jets with what Nese called “Brand G,” I came to the Falcon 8X with preconceived notions. Can the aircraft really be that much more efficient? What about those claims for the trajectory-based flight control system? And is the aircraft a step ahead of its competitors in safety, the most important metric?
The 8X’s maximum range number is due in part to efficient engines. It is also due in part to the aircraft having been designed to provide a lower basic operating weight, which allows for greater maximum fuel capacity. The trade-off is a lower cruise speed.
Higher speeds do impress on shorter distances. A G500 at Mach 0.90 will fly from New York to Frankfurt almost 30 min. faster than an 8X at Mach 0.83. But that extra speed is negated if a fuel stop is needed.
Dassault compares the 8X to Gulfstream’s longer-range G600, but because I am familiar with the G500, I used that to run the numbers for a flight from New York to Tokyo. The 8X took 13 hr. 47 min. nonstop at Mach 0.80. The G500 needed a fuel stop in Anchorage, Alaska, for a total flight time of 13 hr. 21 min. It is possible to fully refuel a G500 in under 36 min., but everything must go right.

And if we are measuring efficiency, we must consider fuel burn. The Great Circle route from New York to Japan is almost 800 mi. shorter than the combined routes from New York to Anchorage to Tokyo. While the G500 required a total of 45,311 lb. of fuel over both legs, the 8X used 32,300 lb.—40% less.
The Falcon’s controls are lighter and more responsive than those of older Gulfstreams I have flown, but I would place the GVII series on a par with or maybe ahead of the 8X. That might be due to my personal preference for an active sidestick. A seasoned 8X pilot would probably prefer its “hands-off” stick.
Is the Falcon 8X really path-stable? Pretty much. The aircraft will maintain a flightpath to a point. Turbulence or a shift in wind direction can disturb the targeted path, but corrections are easy to make because of the closed-loop flight control system.
Does the 8X “close the loop” in flight control systems? It does indeed. In a conventional aircraft, the pilot must constantly monitor the aircraft’s attitude and path to ensure they are as intended. If an 8X pilot has the discipline to release the stick after moving it, the DFCS should keep the aircraft on the intended path.
And is the Falcon 8X a step ahead in safety? My answer is an unequivocable “yes” for two reasons. First, the closed-loop DFCS provides a huge advantage to pilots who choose to use it. Second, the FalconEye CVS provides pilots a situational awareness tool that has no parallel. I have been flying with conventional EVS for a long time and can confidently say these systems are effectively blind in some conditions. Any HUD without SVS is at a severe disadvantage.
Comments