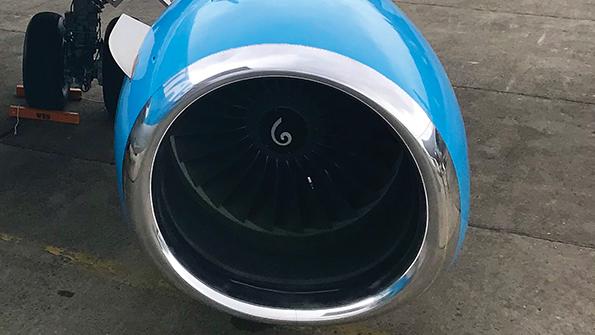
Forged paperwork led thousands of bogus CFM56 engine parts to be accepted as new and airworthy.
The question was posed to many panelists at the recent Aviation Week MRO Europe gathering: How much will the AOG Technics fake paperwork scandal change the way you buy parts?
Most answered the same way: Not much, if at all.
Representatives of both airlines and MRO shops emphasized the long-term relationships they have with their vendors and how they put new ones through a careful vetting process. The safeguards in place work, and eliminating opportunists—even ones that forge paperwork that claim used parts are factory-new—is impossible.
“The processes, I believe, are robust,” said Ivan Gonzalez Vallejo, Iberia Maintenance’s director for supply chain and MRO strategy. “Maybe some more controls or technology could have helped. But if you want to forge paper, you can forge it, as well as a digital certificate.”
British Airways Chief Technology Officer Andy Best suggested the current mix of airline cost scrutiny, high demand for narrowbody lift and supply chain challenges creates an appealing scenario for profiting from attractively priced parts. Opportunity triggers ingenuity among legitimate companies and criminals alike.
“I don’t think we should be blaming the airlines per se or the [manufacturers],” he said. “We should be blaming the person that did it. That’s where it starts.”
The facts of the AOG case suggest that more can be done, however.
GE Aerospace would likely call its vendor oversight system robust. It even has a safety management system, putting it well ahead of its U.S. Part 21 type and production certificate peers and even the FAA, which is in the process of mandating them. But its shops still wound up with CFM International CFM56 engine parts sold by AOG, backed by bogus paperwork.
An FAA notice warning about GE CF6 parts sold by AOG with forged paperwork suggest the vendor used basic tactics. Some falsified FAA 8130-3 airworthiness approval documents, supposedly prepared by GE, list the accompanied part as a “bushing.” But GE’s common terminology for the form is “bushing shrd (IGV),” the FAA notice said.
Language is also missing from the form’s “user/installer responsibilities” block. “GE does not remove boilerplate language from the FAA Form 8130-3,” the notice said.
The FAA also flagged boxes not grayed out on the CF6 forms that should be grayed out “for new articles.”
The situation prompted GE Aerospace and Safran, 50-50 owners of CFM, to act. CFM started by stepping in where regulators and law enforcement hesitated to go. Its September lawsuit forced AOG Technics to hand over transaction documentation to help validate where the bogus UK vendor bought its parts and where they ended up. (The most visible move regulators made was to warn industry in early August that AOG was up to no good—something CFM had done weeks before.)
The manufacturers will not drop the case once the immediate hazards are identified. CFM and its owners plan to explore both internal and industry-wide steps to help reduce the chances that parts with fake or improper paperwork are accepted by airlines and repair stations.
Specifics on any potential changes would take time to develop, a CFM representative cautions. But one of the ramifications of the AOG scandal is an examination of both internal and external processes for possible gaps that could be filled without disrupting long-established industry processes, the company confirmed.
The work is likely to extend well beyond validating a vendor’s claims. AOG’s scheme underscores a larger, all-too-familiar challenge: parts traceability that ideally comes with a maintenance history. Absent real-world ramifications like bent metal or worse, one Suspected Unapproved Parts case—even as one as large as the AOG saga—is unlikely to trigger a major change in how parts are procured, tracked or validated. But it may help tilt cost-benefits analyses in favor of adopting, or at least testing, new processes.
At the very least, it will give those exploring more digitalization another use case.
“We are currently investigating other technologies in terms of traceability of documentation for blockchain,” Ben Moreau, AFI KLM E&M senior vice president for strategy and business development, told MRO Europe attendees. “We believe it could be an answer, but it’s not the only one.”
How to proceed is “definitely an industry question,” Moreau added. “Traceability is not a matter of one player, but all players [throughout] the value chain, from the new [parts] through the full life and the dismantling of the aircraft.”
The investment would pay off, he added, even without the threat of criminal activity.
“Even in a world of people acting well, this would generate significant savings,” Moreau said.