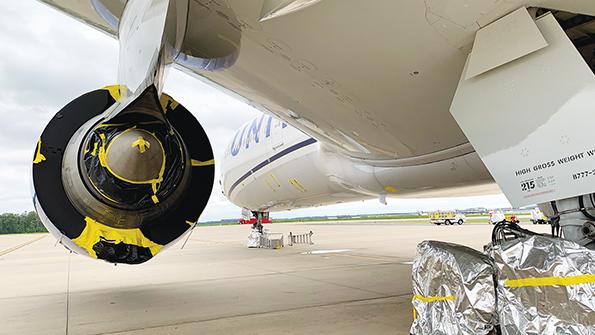
As aircraft operators continue to juggle their active fleets in response to shifting demand during the novel coronavirus pandemic, regulators are updating guidance to help minimize safety issues linked to new operational and return-to-service challenges. Two issues drawing significant attention are potential risks of new onboard cleaning protocols and those related to unplanned, extended aircraft downtime.
In an early November safety bulletin, the U.S. FAA called attention to adverse effects that new, more frequent disinfection processes to help combat COVID-19 can have on aircraft surfaces and components. The agency called on operators and maintainers to heed manufacturers’ guidance and take extra steps to protect sensitive equipment, wiring and other high-risk components.
“FAA notes that although the Environmental Protection Agency publishes a list of disinfectants effective at inactivating COVID-19, the majority of the products listed may not be suitable for use on aircraft, except in very limited and localized application,” the agency says.
The agency’s bulletin clarifies that aircraft disinfection is not considered maintenance under FAA regulations. “However, the FAA advises that aircraft owners and operators should approach the disinfection process similarly to any maintenance or repair action for which improper execution may compromise airworthiness,” it says.
Among the agency’s areas of concern: fogging and misting that allow disinfectant to penetrate areas where it could create problems, such as underlying structure or fan-cooled electronics. “Running aircraft ventilation will typically exacerbate this condition,” the bulletin says.
The FAA said it recommends electrostatic spraying over fogging, because sprayers offer more directional control.
“[Using] either technique with the ventilation system off will reduce the risk of unintended application,” it says. “Note that airframe manufacturers continue to assess the implications of an operating ventilation system using specific disinfectants and may identify exceptions to this general advice.”
The FAA also suggests frequent inspections for corrosion in any areas where disinfectants are used. Any procedure that creates pools of liquid should be avoided, with the flight deck requiring extra caution.
“Be especially careful when using liquid disinfectants in the flight deck, particularly when attempting to achieve a long ‘dwell time’ of the liquid disinfectant on the surface if recommended by the disinfectant manufacturer,” the agency says. “Liquids can intrude into flight deck switches and seals. Excessive liquid intrusion can lead to electrical shorts in the near term and unexpected corrosion in the long term.”
The agency “emphasizes that owners and operators should follow, and not exceed, the disinfectant manufacturer’s instructions for application of disinfectants identified as appropriate for the aircraft by the aircraft manufacturer.”
Issues related to returning aircraft from prolonged periods on the ground have caught regulators’ attention as well. In August, the European Union Aviation Safety Agency (EASA) called out “an alarming trend in the number of reports of unreliable speed and altitude indications” on initial flights following storage periods. “The risk of such contamination was increased if the aircraft storage/de-storage procedures were not completely or [were] improperly applied at the beginning, during or at the end of the storage period,” the agency said in a safety bulletin that urged operators to follow manufacturers’ procedures.
In November, EASA followed up with more detailed guidance on safely returning aircraft from storage. The guidelines highlight common airworthiness issues putting aircraft at risk, from possible fuel contamination to insufficient covering of holes or gaps that could allow wildlife to take up residence.
EASA also pointed out organizational issues that operators must consider as part of a broader safety assessment. Among the considerations EASA highlights are whether operators have enough properly trained staff.
“A dedicated risk-management [process] is recommended to be applied by the relevant organizations, proportionate and taking into account their particular situation and activities,” EASA said. “This customized safety risk management should identify the novel hazards, assess the related risks and determine appropriate mitigating measures.”
The International Air Transport Association (IATA) has published a more detailed guidebook that walks through specific steps operators should take to ensure aircraft remain airworthy. The guidance, first published in June and updated in early October, provides system-level details while reminding operators to reference relevant manufacturer maintenance information. The October update also includes a list of lessons learned from the initial grounding and return-to-service phases.