MRO Memo: Considering Aftermarket Cabin Recycling Models
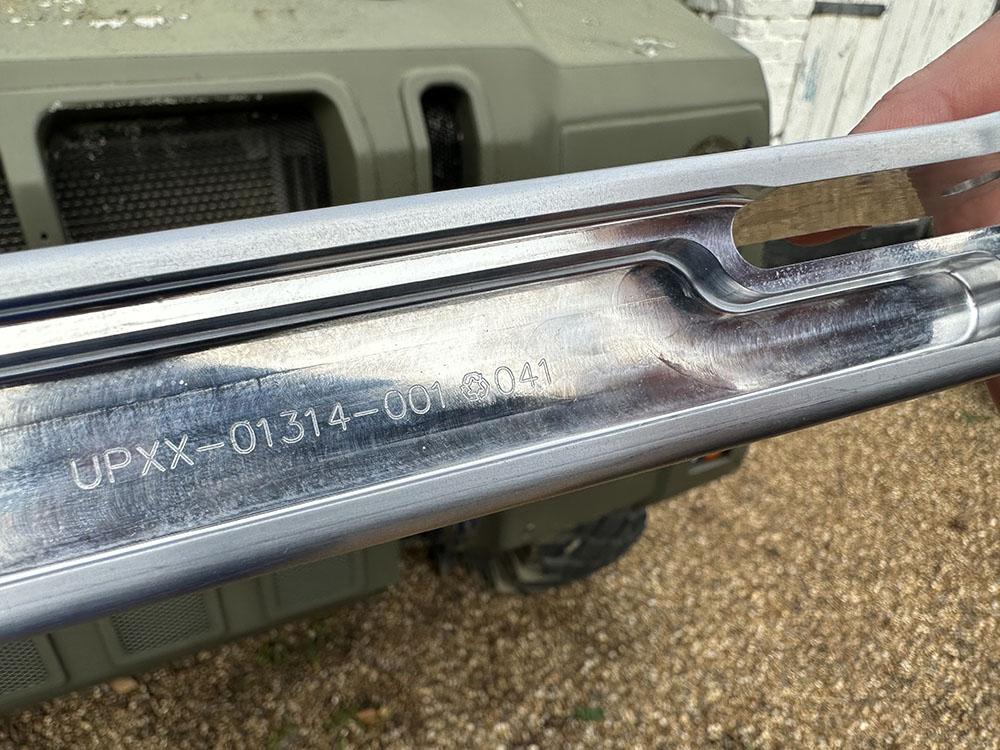
Unum Aircraft Seating stamps metal identifier recycling numbers on metallic elements of its seats.
The cabin interior of an aircraft is among the most complicated elements when it comes to recycling and disposal, but the aviation industry is assessing various options to address this.
One model comes from Lufthansa Technik, which proposes a system where its MRO locations essentially become recycling collection points for cabins and cabin components that are extracted from the aircraft.
The concept of operations is that these components would then be returned to central points, whether globally, regionally or a mixture, depending on the component. For example, a component such as a standard aluminum seat structure that is common or very simple to recycle might be separated and processed locally.
Something more complicated to recycle or requiring specific equipment—such as a glued sandwich of different plastics, composites or both—might be assessed separately and transported further for recycling. These are inherently complicated in the aviation context because of the need to pass flammability, smoke toxicity and heat release regulations, each of which may require additives or specific manufacturing processes that hamper recyclability.
There remain inherent questions about the overall emissions of recycling certain products, especially if they require transportation. From a sustainability standpoint, it may make more sense to send certain elements to a local landfill if they are too complicated to recycle, especially if they are heavy or bulky, rather than transporting them long distances to recycling centers.
A critical step in the recycling process is material identification. This is magnified since different elements of the cabin—such as seats, galleys, galley inserts, lavatories, carpets, dividers, bins and sidewalls—might all be produced by different suppliers. There may be some commonality between what is installed as supplier-furnished equipment or catalog-selected buyer-furnished equipment, but this may be minimal.
Two outwardly similar narrowbodies of the same vintage, which one might expect to be relatively similar, might have been initially outfitted for airlines anywhere on the low-cost to full-service spectrum and operated by half a dozen or more different airlines. These operators may have installed or removed different cabin elements, with different levels of customization, produced by a variety of suppliers.
Identifying precisely which materials make up a particular element is complicated, especially decades after its installation.
Labeling is a key part of the solution, and early progress is being made by industry organizations such as the Green Cabin Alliance. Unum Aircraft Seating is already stamping metal identifier recycling numbers on metallic elements of its seats, similar to those that consumers see on single- or multiple-use plastics. Meanwhile, thermoplastics manufacturers are starting to print material details on the back of their plastic sheets.
Even once identification is possible, the recycling process will require substantial training, expertise and oversight. A balance must be struck between the granularity of recycling collection and the knowledge required to do so.
One end of this spectrum would have highly trained staff at MRO locations and aircraft boneyards that could separate recyclable elements into very specific categories which could then be processed more efficiently. Of course, this comes at a cost—both monetarily and in terms of time for technicians amid the industry’s skilled labor shortage.
The other end of this spectrum envisions a “big box” of recyclable elements processed in its entirety. However, risks would include the cost of transport, especially if materials are placed in the box that are generally non-recyclable or that have been altered in some way to make them non-recyclable.
As the industry progresses in its analysis, it will be crucial to understand the full life-cycle costs and hidden carbon behind each model.