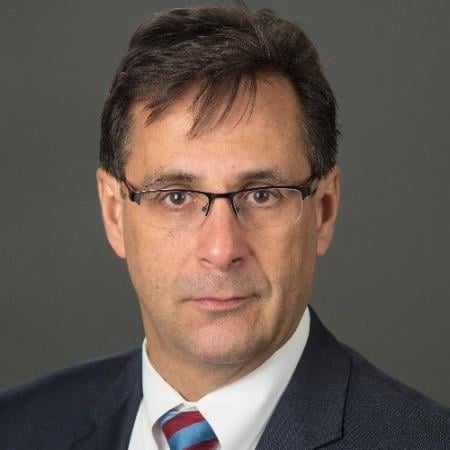
Dana Stephenson, vice president of customer support, aerostructures of Collins Aerospace, talks about how his business was hit by the pandemic, what it looks like now and the digital progress Collins has made in nacelle repair.
Did nacelle overhauls slow down with engine overhauls, and are they recovering now?
Certainly nacelle overhauls and repairs slowed down during this pandemic but not because they are associated with engine overhaul maintenance or removals. Nacelle removals and maintenance are all on condition, which is defined in accordance with the airline’s prescribed maintenance practices. Many customers stopped all discretionary maintenance spending and on-condition components certainly fell into that category. Other customers, however, that prescribe more proactive approaches to maintenance requested the continuation of established overhaul and repair programs that they had with us. Additionally, as the pandemic and its recovery has moved throughout regions of the world, we have seen different behaviors in repair and maintenance. With our eight MRO facilities regionally located worldwide, we get to see activities across diverse regions and have been able to support variation in demand.
We are cautiously optimistic from what we are seeing now. As a nacelle MRO business, we never dropped as low as the RPK-reduction forecasts would lead you to believe. As airlines are pulling planes back out of storage and readying them for increased utilization, our level of activity in the first four months of this year across eight MROs has improved on where we thought we would have been a year ago.
For which aircraft types do you expect nacelle overhauls to recover soonest?
The single-aisle products will recover the soonest and will require attention, as many have predicted and as we have observed in our MRO facilities.
Have you had any difficulty getting parts for nacelle overhauls?
Being the OEM for many of these nacelle products, we have a very robust supply chain of parts support for the MRO activities required. For more than 10 years, we have maintained an on-time-to- customer-request-date performance of 95% for customer lead-times that average three days or less. We continued to support all customers with these same performance levels during the pandemic. Collins has had a long-standing policy to assure that the part stocking and forecasting that we perform are world class, and we invest in that inventory required by our customers when they want it. It is clear to us that customers have options, and if we do not fulfill their request for fast delivery of parts or service, they will seek others that will.
Have you been able to retain all the staff needed for nacelle overhauls?
Yes, we have maintained the staff without exception in our eight worldwide MRO facilities throughout the pandemic and are closely watching the upturn to continue to ensure that we have the resources necessary. For many months we have leaned forward with various webinars, and where travel allowed, on-site teams at airlines to help review products on aircraft to facilitate the flow of material at the airline that needs repair.
Have there been any changes or innovations in your nacelle overhauls in the past year, or coming up soon?
The acceleration of digital tools has been a big part of what we have done in the last year. These digital tools have increased the flow of information throughout our MRO factories, mechanized inspection processes with the use of robotics and allowed us to make decisions more quickly, with the resultant impact of being able to reduce repair and overhaul lead-times and to pivot to the immediate needs of customers that need our services to return aircraft to operational service.