
A technology that can expedite the process of inspecting aircraft structures for cracks received FAA approval on March 3. While the supplemental type certificate (STC) applies to one specific application, which would be installed in one specific area of the aircraft, expect others to follow.
The first FAA-certified application for Structural Monitoring Systems’ Comparative Vacuum Monitor (CVM) sensor technology is for a Boeing 737-800’s Wi-Fi system antenna structure. The sensor system provides an alternative means of compliance for certain continued airworthiness structural inspections required for the Gogo (Intelsat) 2KU Wi-Fi antenna support structure.
Structural Monitoring Systems’ (SMS) patented technology uses “vacuum and differential pressures to detect if there is a crack in the surface of the fuselage,” says Rich Poutier, executive vice president for business development. “The simplest way to explain it: We pump air into and out of a sensor, and our PMA200 test box technology measures the differential airflow. If the airflow returning back to the test equipment is more air than what we pumped into the system, we know we have a crack.”
The PM200 test box costs about the same as a traditional nondestructive inspection device. “The sensors enable remote inspections, eliminating the need to remove any of the typical items to gain access to inspection areas such as ceiling panels, pneumatic ducting and insulation blankets,” Poutier says.
In addition, because maintenance teams are not removing these items, the process eliminates potential damage from uninstalling and reinstalling material. Because pneumatic ducting is not removed and reinstalled, pressurization tests afterward also do not need to be performed.
“This technology allows an airline or an operator to do this specific structural inspection during a normal overnight operation,” says Dave Thompson, Delta TechOps vice president for engineering, quality and safety. “You can do this inspection in a matter of an hour, compared to a full day and a hangar visit.” Delta TechOps has been testing the sensors with SMS for a few years for this antenna area application to “look for opportunities to reduce the maintenance burden—both labor hours and ground time—for the mandatory inspections that are required,” he says.
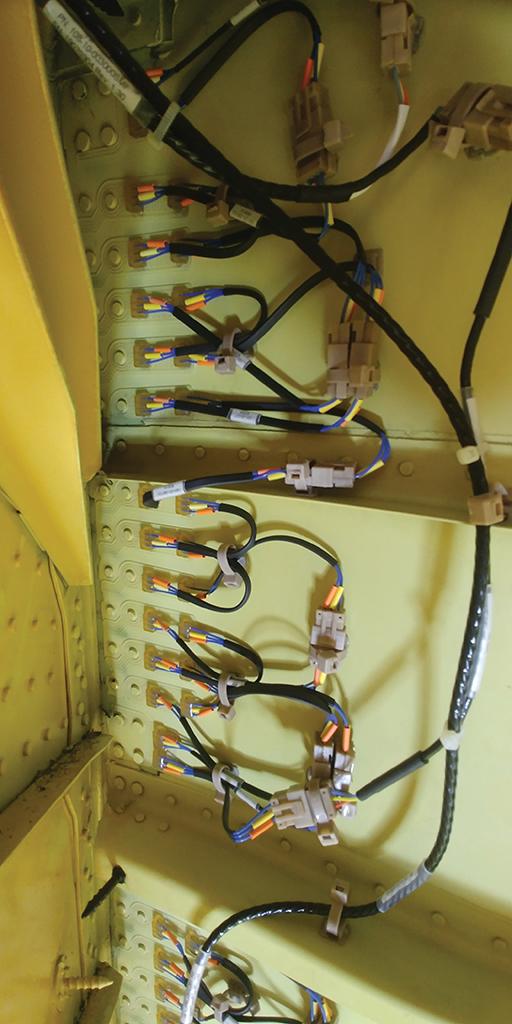
“Having these sensors on the aircraft in various locations that we can get approval for not only allows the airline to complete required structural inspections during the normal operation without any scheduled interruption, it obviously gives flying days back to the airline because it prevents having to pull an aircraft out of the [flying] schedule for a scheduled maintenance visit in a hangar,” Thompson notes. “That allows the use of an asset more.”
The companies are partnering to develop other applications for structural inspections of 737-800s. While those would still need FAA and Boeing approval, given that the sensor technology is the same, subsequent application approvals should take less time.
SMS applied to the FAA for this first STC in January 2019.
Thompson says for the specific antenna application that the STC covers, the SMS sensor technology can be installed within a day during a maintenance check “when that area undergoes a regular, routine inspection.”
In addition to the time and money saved by not having to perform the inspection in a hangar, the CVM sensor technology also could help maintenance planning departments sequence inspection tasks. “If an airline has two out-of-sequence inspections due, one at 3,500 cycles and another at 4,500 cycles, the planning group is forced by operational and regulatory requirements to route the aircraft into the hangar to perform the lowest inspection task (3,500 cycles). Typically, both inspection tasks (at 3,500 and 4,500 cycles) would be packaged and/or scheduled together to reset the interval clock for aircraft operations. Many times this results in discarding more than 1,000 cycles of available operation,” says Poutier.
To put that 1,000 cycles in perspective, for a North American legacy narrowbody operator flying four cycles per day, that would equate to about 250 days of extra flying, according to Oliver Wyman/Cavok data, says Brian Prentice, a Cavok partner and global leader of the MRO practice. For a low-cost or ultra-low-cost carrier that flies 4.5 cycles per day, that would equate to about 220 extra days. For a widebody aircraft being flown 1.75 cycles per day, that number jumps to about 550 days.
The FAA issued the STC on March 3, but subsequent European Union Aviation Safety Agency (EASA) approval could follow. SMS is speaking with European airlines that have expressed interest in its technology. “We believe it would be reasonable to expect EASA approval when they are approached by an airline since the FAA has issued its approval,” says Poutier.
When asked whether Delta Air Lines would consider using the technology for other aircraft types it flies, Thompson says, “we would definitely consider it” if Structural Monitoring Systems, the owner of the technology, looked for opportunities with other OEMs.