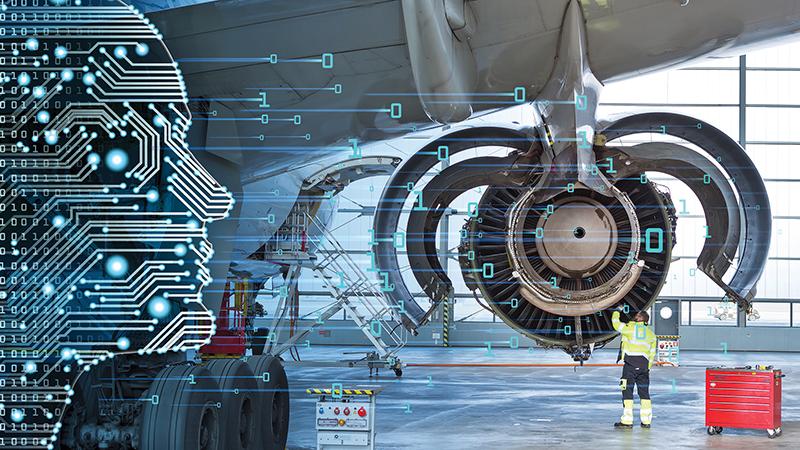
MTU Maintenance monitors health trends for about 2,000 engines.
Credit: MTU Maintenance
Digitalization has been one of the major trends in aviation maintenance over the past two decades, and at its heart lies the burgeoning capabilities of health monitoring systems. Each new generation of aircraft and engines features more sensors than the last. This, alongside new machine learning...
Aviation’s Data Revolution Spurs Health Monitoring Advances is part of our Aviation Week & Space Technology - Inside MRO and AWIN subscriptions.
Subscribe now to read this content, plus receive full coverage of what's next in technology from the experts trusted by the commercial aircraft MRO community.
Already a subscriber to AWST or an AWIN customer? Log in with your existing email and password.