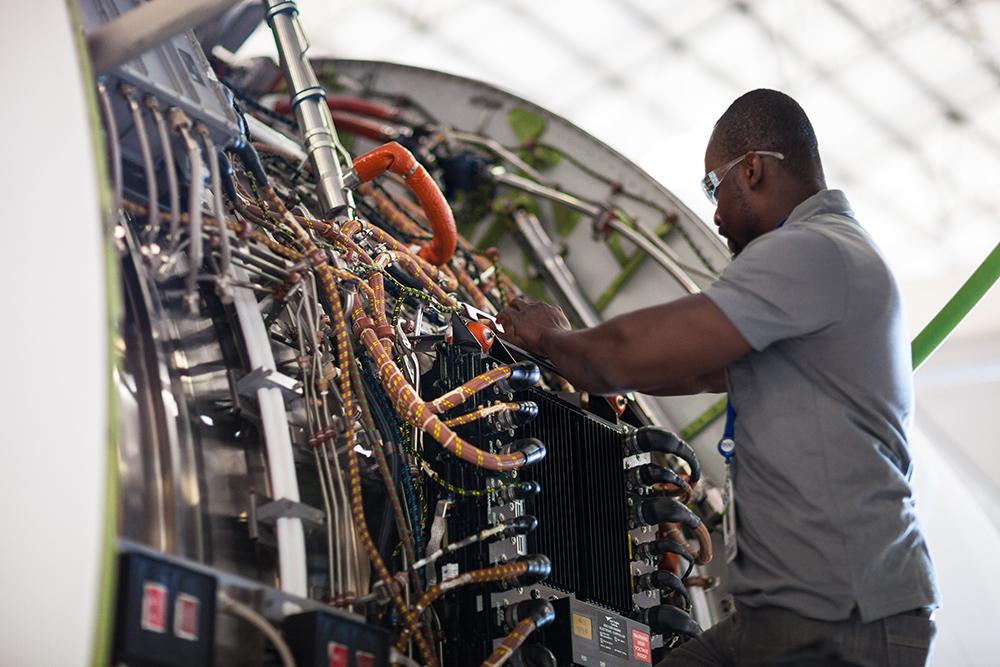
New heavy maintenance and cargo conversion provider Aspire MRO has successfully rolled out a new digital system, and President and CEO Phil Bathurst says the company benefited compared to legacy MROs because it was able to optimize its processes alongside digitalization.
Aspire MRO, which is doing heavy checks and cargo conversions on Boeing 777s, chose EmpowerMX as its digital solution, an application also used by Embraer, American Airlines and Delta Air Lines.
It spent 3-4 months designing its processes and work flows to be as efficient as possible under the new system. The consultancy SeaTec assisted in this process design, while EmpowerMX staff implemented the IT solution.
Bathurst recommends using an aviation consultancy to address the process changes. “Otherwise, the IT company will just do what you tell them to, and there will be no improvement,” he says. “You will just be digitizing bad processes.”
It took Aspire three months to implement the maintenance execution part of digitization, work cards and so forth. Finally, Aspire had to spend six months implementing the materials parts of EmpowerMX and cleaning up the materials data.
“We’re still cleaning up materials data,” Bathurst says. There are over 100 line items and each part must have the correct part number, manufacturer, vendor and other data. Aspire had inherited both stocks and stock data from the former owner of its facility, GDC Technics. “We made every effort to ensure that it is correct—we need mechanics to have complete confidence in the supply chain,” he adds.
Bathurst says the new system is enforcing the improved processes designed into it. For instance, a mechanic cannot close a task card until they return all tools to storage. “That was always a good policy,” Bathurst explains. However, with paper cards, the policy might not be enforced, especially at midnight after a long, tiring shift.
Mechanics can use the software to see if necessary parts are in stock before beginning any task. Aspire also reorganized its storerooms, moving frequently used parts to the front.
Both routine and non-routine tasks are digitized, and all non-routine tasks are also generated according to an agreed upon, highly efficient rule. “At some MROs, if you ask at a meeting how non-routines are generated, you get 12 different answers,” Bathurst says.
Mechanics get all the data and documents they need for their tasks on tablets. They can print out a document at a desktop if they want to, but Bathurst says this is not typically necessary. “If an FAA auditor comes in, he can see the mechanic has all the documents right on the tablet,” he says. Electronic signatures are used for sign-offs.
Some large diagrams, such as for the 777’s new cargo door, may be difficult to display clearly on tablet screens. Therefore, Aspire has set up large smart TV screens on work-stands that can be used to project images from tablets.
Mechanics get their tablets when they check in each day by inserting a chip in a cabinet. The cabinet charges the tablets and ensures they are all updated with the most current information. At present Bathurst prefers this shared tablet approach over issuing a dedicated tablet to each mechanic because the cabinet ensures all tablets are fully charged. Aspire is still trying to determine how many mechanic tablets will be needed, since Bathurst says that sometimes six mechanics will go out on a single job and only need one tablet.
Bathurst notes that the system has made the work of managers easier, too. “The big thing for us is now we have real-time data,” he says. For instance, Bathurst says paper reports do not need to be printed before project managers’ morning meetings and there is no confusion about whether printed versions are up-to-date. “It’s all live on the screen,” he says. “Project managers can devote time to running their projects rather than reading reports.”
In addition to digitizing its maintenance processes, Aspire plans to grow its workforce. It expects to hire another 150 mechanics in the comings months and plans to have 600 working by 2025 on five lines of heavy checks and conversions.