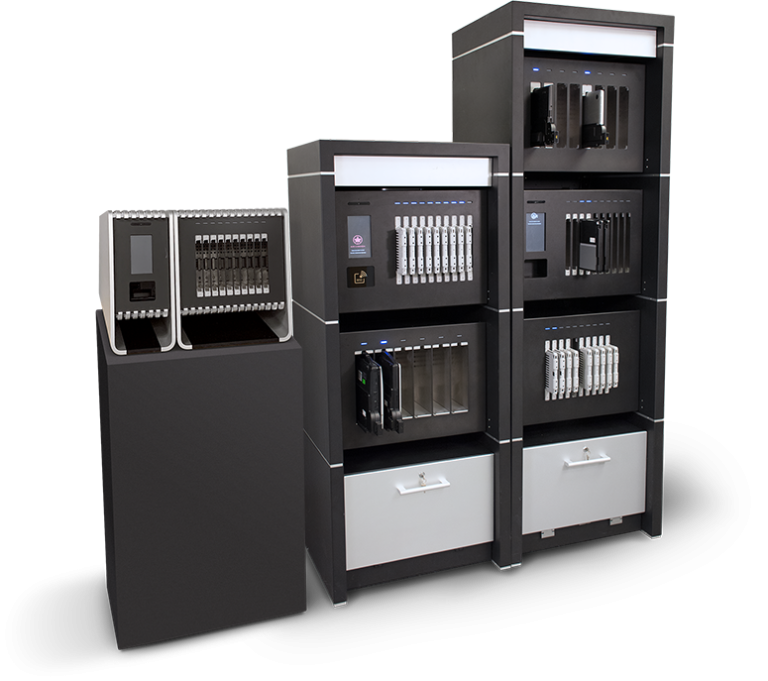
Mobile devices, such as laptops, iPads, tablets and smart phones, have proliferated on ramps and in hangars in recent years. However, simple deployment of these devices in MRO operations is not enough. Choices must be made and devices must be managed to yield the safest, most economic effects.
In a recent webinar, Keith Dugas, director of maintenance AI and connected operations at Air Canada, explained how this is done at the airline
Air Canada began thinking about mobility when it inducted its first Boeing 787s in 2013. The complexity of the new aircraft, plus the maturing of mobile options, urged a change. The old way of turning aircraft required mechanics to board aircraft, check for defects, return to offices, print out instructions, return to aircraft, perform fixes and then fill out paper logs to be entered in systems back in offices. Dugas estimates these pre-mobile procedures wasted 15-30 min. per aircraft turn.
Air Canada began digital proofs of concepts, mobile procedures and deployment for mechanics in 2015. Apps turned technical publications into large files distributed on iPads.
One major challenge was immediately synchronizing all iPads with the latest revisions in maintenance manuals and illustrated part catalogues when revisions came out every two to three weeks. Failure to synchronize risked safety, as technicians working on aircraft might not know of the latest correct fixes.
However, having IT staff manually update documents on just the first 80 iPads took 3-5 days, a huge manpower burden. The airline looked at several options and chose M3 Solutions kiosks. The M3 kiosks took over complete charge of both the iPads’ hardware and updating software.
The kiosks charge and securely store the iPads when not in use, report malfunctions to help desks for engineers to fix and ensure that all iPads are rotated so they are used for about the same number of hours.
Most importantly, the kiosks automatically ensure all iPads are synchronized to the latest software updates before they can be checked out. Air Canada says the kiosks allow it to time the release of its own new apps and app revisions on a set schedule, ensuring adequate time for training.
Using these kiosks required that mechanics share iPads, checking them out when they started work and checking them in when the shift was over. This differs from issuing each mechanic their own personal device, as is done at some airlines. Dugas acknowledges this shared approach was hard for some employees to accept. However, he says it was necessary to ensure absolute synchronization of all devices with the latest technical data.
Employee adoption was slow at first, because only Boeing manuals were on the iPads. Air Canada’s three OEMs—Boeing, Airbus and Embraer—did not want their data on the same device, with possible leaks of intellectual property among them.
It took ten months for Air Canada to develop software that would segregate the different OEMs’ data on the iPads and then to negotiate agreements with the OEMs to allow their data to be put on the same devices. Then, with all the OEMs’ data on iPads, “adoption skyrocketed,” Dugas notes.
Air Canada now has technical data on almost 600 technicians’ iPads, and it continues to expand its mobile apps. It added a QuickTurn app and a master list of parts. Next, it will add maintenance manuals.
Dugas says the chief gain from the M3-iPad approach is in safety by ensuring the latest and most correct data is used in repairs. He says the technology also saves up to 30 min. on each aircraft turn and reduces burden for the airline’s technology staff in updating tech data, deploying internal apps and dealing with refreshment of devices every three years. “This would require excessive resources,” he adds.
The M3 kiosks work any combination of mobile devices, laptops, iPads, tablets or smart phones.