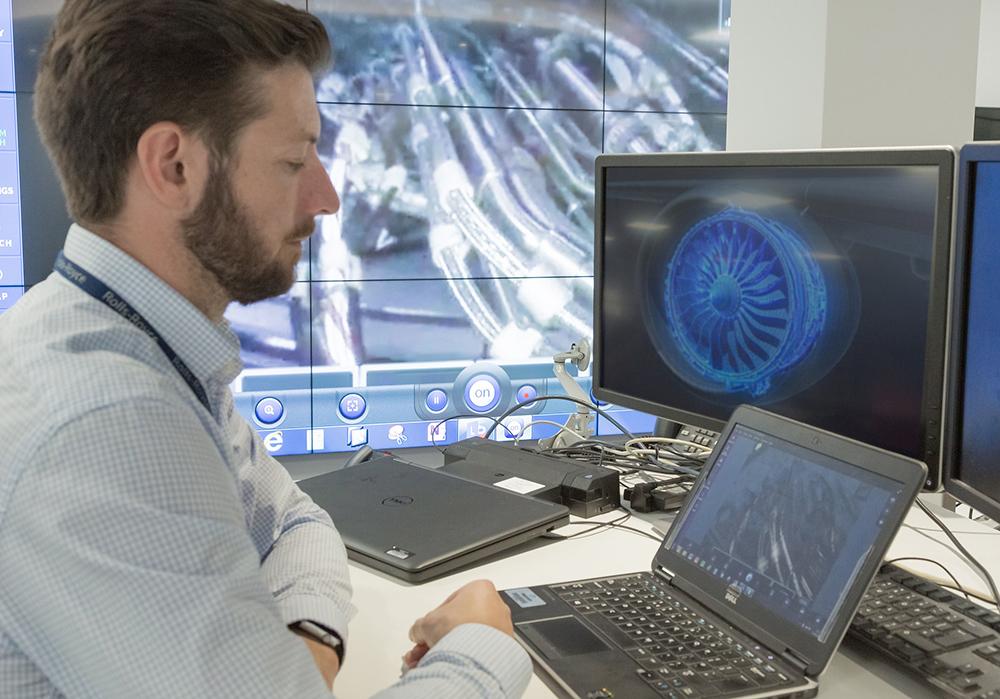
The faster relevant operating and performance data comes to data scientists, the better predictive maintenance models can be. Engine OEMs have been working on predictions, analysis and speedy data transfers for many years. They are still developing new methods that can point the data paths for prediction of other component challenges.
For example, Pratt & Whitney receives engine monitoring data from its own engine monitoring systems, designated engine trend analysis services and aircraft OEMs, according to Arun Srinivasan, associate director of strategy, engine health management.
Traditionally, Pratt could receive snapshot data on engines through ACARS messages. However, if an airline works with Teledyne Controls as a data delivery solution or uses a similar service offered by another Pratt partner, the engine OEM can now capture data over the entire course of the flight.
Pratt’s primary means of obtaining this high-quality full-flight engine data is its own FAST system, which captures, analyzes and wirelessly sends full-flight engine data to operators within minutes of the pilot shutting down the engine.
FAST is available on many Pratt powerplants, but the OEM says it is especially important for the new geared turbofan engines, which generate 40% more data than V2500s. “An average two-hour flight for a GTF engine generates about 4 million data points,” Srinivasan explains.
Older engines can also yield quick data streams. For its PT6E engines on Pilatus PC-12s, Pratt offers its Data Collection and Transmission System (DCTS), which it says is a simple turnkey solution for operators to obtain high-quality, reliable, consistent data on engine performance and health. Both FAST and DCTS can be readily retrofitted.
Pratt says it is always upgrading its data ecosystem, data transmission methods and analytic tools. Traditionally, predictive algorithms have been mostly physics-based, but the engine OEM is now working on artificial intelligence and machine learning solutions, both of which it says can better exploit the power of full-flight data delivered quickly. Under flight-hour maintenance programs, operators obtain all upgrades as well as predictive recommendations.
GE Aviation’s digitally-focused Fleet Support Group supports more than 30,000 commercial engines by exploiting more than 120 million packages of data per year.
All GE-powered aircraft provide snapshot data from ACARS reports and other aircraft systems, such as aircraft condition monitoring systems. Snapshot data includes engine instantaneous health data captured at discrete points in flight and data on faults. For older engines, snapshot data has been manually logged by the pilots. Snapshot data can be transmitted in near-real time to GE by ground radio or satellites. Operators can also forward snapshot data—which has been offloaded from aircraft manually, by Wi-Fi or cellular—through email or a secure file transfer protocol (FTP).
For some engine types, GE also uses continuous data captured throughout flight. This continuous data is typically recorded on the quick access recorder, digital flight data recorder or electronic engine controller. Data retrieval from aircraft may be manual, Wi-Fi or cellular. It is sent to GE using FTP or GE software provided to operators.
These data transmission methods have been standard for some time, but growth in data volume has increased costs of transmission. GE and operators are now focusing on lowering costs by replacing manual downloads with wireless transmission and cellular networks at gates. However, deployment of these better technologies is primarily the decision of airframe OEMs, airlines and airports.
Rolls-Royce recently partnered with QOCO Systems for fast and validated transfer of data from airlines’ IT systems to its data analysis group.