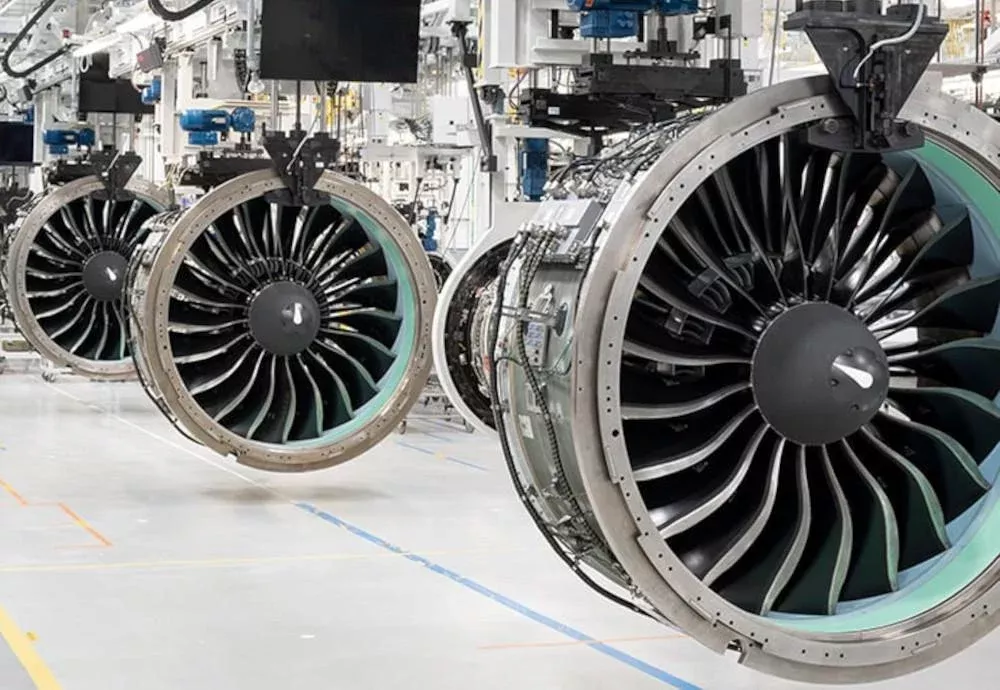
AMSTERDAM—Engine specialists are looking to develop more parts repair capability for both new and legacy powerplants to better control material costs and turnaround times, with strong long-term demand expected across multiple platforms.
Speaking at a panel on the topic of parts repair development at Aviation Week’s Aero-Engines Europe, Matthias Niessen, senior director for engine parts repair at Lufthansa Technik (LHT), which overhauls and repairs a full, broad scope of legacy and new-generation engines, says the cost of materials is the main driver for the MRO choosing to repair rather than order new parts, with the majority of engine maintenance spend being directed toward material costs in today’s market.
Availability of parts and turnaround times (TAT) are also factors, Niessen says, as LHT looks to keep costs down in its engine repair network. Given the volume of new engine types coming online, particularly in the narrowbody segment, Niessen says LHT is further ramping up its repair development for new-generation engine types and cites strong future demand for specific services such as non-destructive testing on both the Pratt & Whitney geared turbofan (GTF) and the CFM International Leap. “Investing in repair depth is the key driver to being a cost-efficient MRO provider,” he cites as a solution to this, stating that LHT in addition to OEM-approved repairs also develops repairs independently outside of the manufacturer.
These ramp-ups also extend to legacy engines, with demand expected to continue for several years on certain programs. Niessen estimates that LHT expects to see legacy engine types entering its shops over the next one to two decades. “If we look at the number of repairs we execute and do in our shops, it’s by far the legacy engines and we are still developing repairs for them,” he says.
Barnes Aerospace, a manufacturer and repair specialist of internal engine components, has grown its engine capabilities since acquiring MB Aerospace last year. Ian Taylor, the company’s vice president for repair sales, says engine OEMs have also driven the company to undertake and develop more repairs in recent times due to the state of the industry’s supply chain. “We need more parts because the supply chain for the raw components, metals, casters castings and forgings is in such a mess due to several factors,” he says.
He believes operational performance is driving competition in the current market. “Over the past three to five years and through COVID, everything was just about performance. If a shop could deliver they could even charge higher prices—it didn't matter. It was about just getting those parts back, because paying a bit more money for a repair was still a lot cheaper than having an entire engine in the shop for an extra 10-20 days.”
Taylor says Barnes Aerospace proactively looks to work with and do more OEM-approved repairs across many engine and part types. “We do some limited DER repairs, which are on the PW4000 engine—they’re kind of quasi-licensed repairs and we developed them having been approved to do so by the OEM,” he adds. Taylor says Barnes Aerospace is investing across multiple engine platforms to ensure a diversified portfolio. “The future-generation engines are the next 25 to 30 years, but around 10 years ago many thought the CF6 and PW4000 were going to stop flying, but look where we are now—these engines have a long time to run. There are also plenty of V2500s and CFM56s that are still waiting for their first shop visits, so it’s about investing across the whole portfolio of all engine OEMS in commercial and defense.”
Iberia Maintenance, the Madrid-based airline MRO, services CFM International CFM56, International Aero Engines V2500, Rolls-Royce RB211 engines and, more recently, the GTF, having inducted its first engine last year. Luis Filipe Parreira Augusto, head of engine parts repair services at Iberia Maintenance, says the business has invested heavily in technology over the past few years to drive down lead times while handling large volumes of engine parts.
He estimates that the Madrid-based MRO typically receives around 250 parts for a CFM56 or V2500 shop visit while taking 400 parts for the larger RB211 engine. “It’s a broad spectrum of parts from casings to high-pressure compressor blades, shafts and life-limited parts,” he says. Like Niessen, Augusto identifies cost and keeping TATs as low as possible as among the primary drivers behind its engine parts repair strategies, and it does this through utilizing closed-loop repairs, which he says gives Iberia Maintenance greater capacity to bring TATs under control.
Being aligned strongly with OEMs has seen StandardAero introduce engine capability, which is an extension of the manufacturer’s capabilities, says Henk Smeulders, vice president of marketing and sales for component repair services at the U.S.-headquartered company. StandardAero entered into a CFM Branded Service Agreement with CFM International for the Leap family 18 months ago, and in that time period, Smeulders says it has invested millions of dollars into developing capability for the new-generation narrowbody engine. Meanwhile, legacy engines account for just a small percentage of its repair development capability.
While the consensus of the panel suggested there was a lack of capacity in the engine parts market, Smeulders believes it is beginning to stabilize somewhat. “We are going from a seller’s market to a buyer’s market again … that will not be far away.”