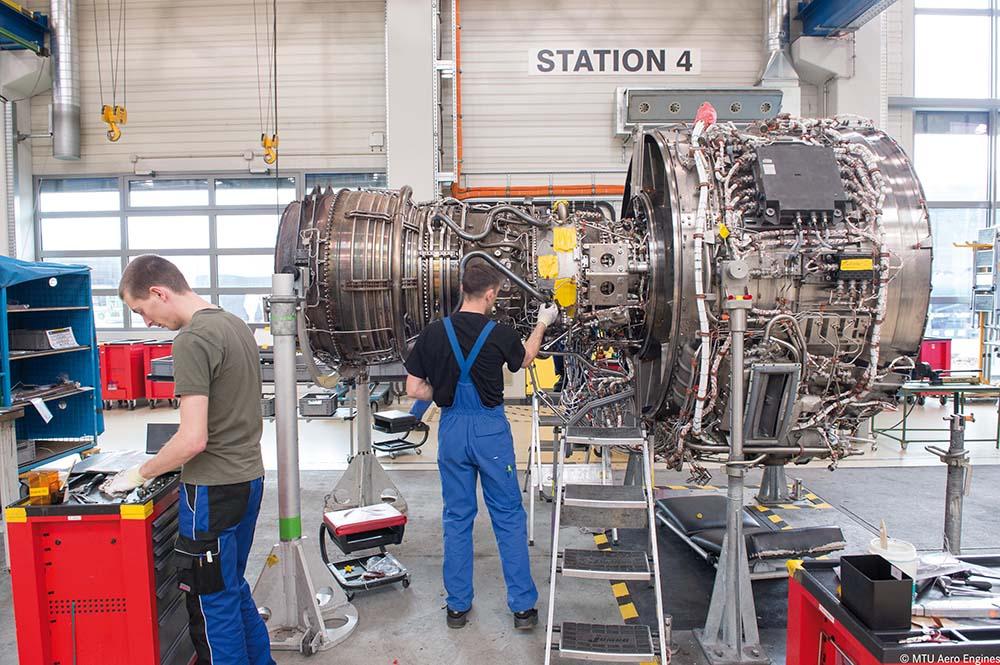
LONDON— Third-party repairs are proving to be a pinch point for legacy engine shop visit turnaround times, a panel of MRO providers said at Aviation Week Network’s Engine Leasing, Trading and Finance Europe conference.
“The problem is in the parts that go outside for repair and the backlog that still exists in the subcontracted repairs,” said Ana Bidarra, engine shop planning and control manager for TAP Portugal.
Alistair Forbes, senior market analyst for MTU Maintenance, noted that smaller, specialist repair providers continued to struggle with labor shortages, unlike many of the larger OEMs and maintenance providers.
“You can have 99.9% of the parts for an engine, but you can’t dispatch it until you get that last part,” said Forbes. “Most of the big people have been able to recruit and train, but some of the smaller outfits are finding it harder to get people in and that’s where we’re probably seeing the pinch point.”
Sourcing used serviceable material for the engines such as the CFM International CFM56 and IAE V2500 is another challenge as aircraft and engine retirements and teardowns have been pushed back. Forbes noted while 60% of aircraft retirements usually occur in the first half of the year, for CFM56-equipped aircraft that figure was only 20% for the first six months of 2024, suggesting that the full-year figure will also be very low.
New Engines
While repairs are not a pinch point for new-technology narrowbody engines, that is because they largely do not exist. Instead, MRO providers have to contend with “huge” lead times for new parts, according to Bidarra at TAP, which services the CFM Leap 1A.
She also noted the lack of available repairs on new engines meant that the need to replace one component could drive a cascade of other replacements.
“You only go to replace the [high-pressure turbine] blades but you have to replace the blades and the three discs that need to be rebuilt,” said Forbes, noting that “it’s in the OEMs’ interest for us to develop repairs and to make their products better.”
He added: “That model worked for the legacy engines and I see no reason why that model can’t be extended to the latest-generation engines. If you can repair a part rather than waiting to fit a new a part that isn’t there, it’s much better to have the repaired in and to get that product back in the air where it should be.”
Echoing those views was Vincent Metz, vice president business development for Europe at SR Technics, who also believes it is in OEM’s own interest to open up the repair market for new-generation engines, as it would put less pressure on their own material production.
“For the OEMs it’s an advantage because they can concentrate their supply chain more on the new-build,” said Metz.