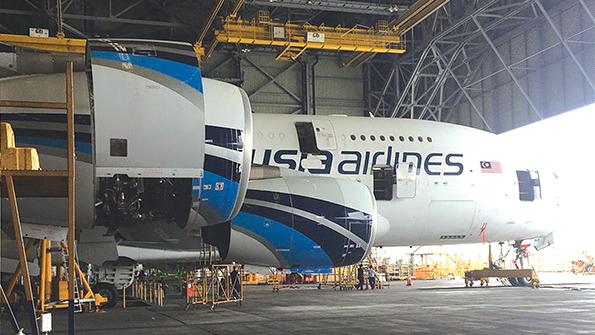
Having successfully resumed third-party MRO services in 2019, the COVID-19 pandemic has posed unprecedented challenges for Malaysia Airlines. A representative from the airline explains how the carrier is using technology to meet demands across the supply chain and for its day-to-day operations.
Which tools has Malaysia used to help it gain greater visibility into its aftermarket operation?
Successfully implemented in March 2019, MAB Engineering has been using AMOS, MRO software designed for the airline’s engineering department as part of its ongoing transformation that serves as its maintenance information system. It also uses Skywise as its big data analytic platform. With AMOS, the airline ensures the airworthiness, operational and financial control at an enhanced level with the longer-term objective of benefiting from process and organizational efficiencies. The system manages end-to-end processes within engineering, enabling the airline’s engineering department to better manage costs and increase efficiency in maintenance.
How have these tools helped you gain greater visibility of the business and the wider supply chain?
The AMOS software can provide real-time airworthiness information and requirements, which is crucial for our operations, while Skywise provides statistics of past consumption, giving us the ability to estimate the reordering level for future needs.
How do you manage MRO spending effectively?
Due to volatility in the market, compounded by the COVID-19 crisis, we have been adopting lean and agile cost structures to ensure cost efficiency. We continuously pursue operational improvements to optimize cost efficiency across the board by simplifying and digitizing processes. We are also capitalizing on big data analytics output and are driving for greater automation and efficiency through digitization to find solutions to bring our cost structure down without impacting safety, quality and customer experience. We are focusing on preserving liquidity and investing in safety and maintenance projects. We took advantage of the aircraft grounding period to use available resources and ground time productively to refurbish our cabins in supporting the airline’s Fly Confidently campaign, repainting our livery and performing modifications to increase aircraft efficiency. This is crucial to ensure that these aircraft are in immaculate condition once we are back in full service.
How has using big data aided both your decision-making as a maintenance provider and your operational management of the airline?
We are currently using our big data of historical consumption to predict future ordering requirements. At the same time, we are embarking on proactive maintenance, using the analytic platform to analyze recurring aircraft defects and current aircraft sensor output to predict impending failures of aircraft systems. These have certainly increased our operational efficiency and improved technical dispatch reliability.
Where do you source your parts from, and what are some of the challenges related to this?
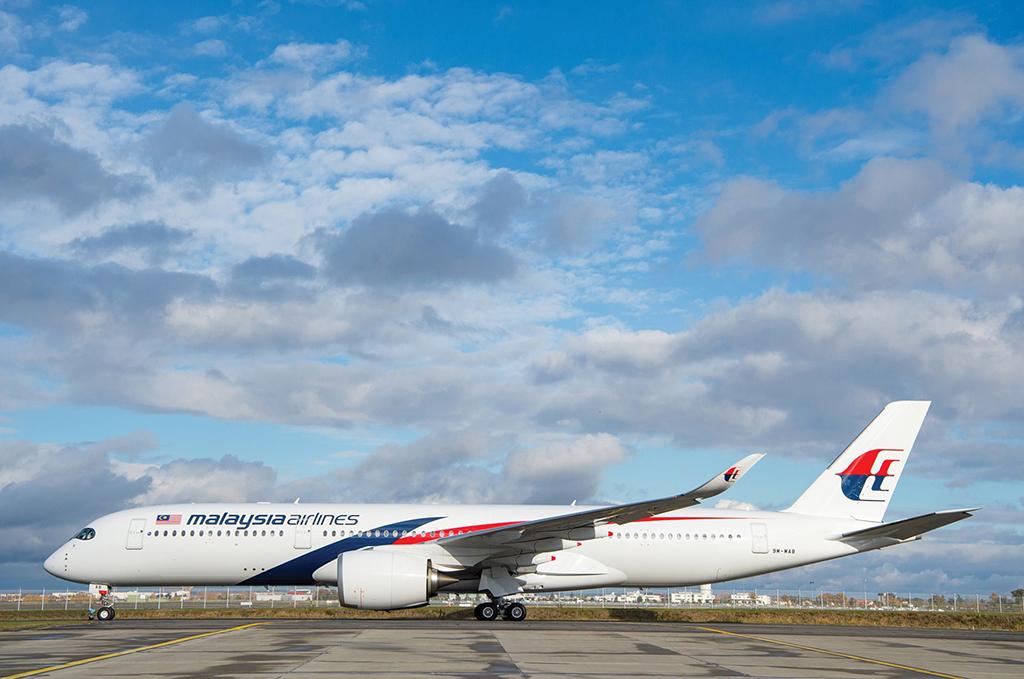
The majority of parts are secured through contract. We have a power-by-the-hour (PBH) contract that ensures availability of parts under Recommended Spare Parts List (RSPL) Essentiality (ESS). Additionally, we have consignment stock based on operational consumption at lower costs than on an ad hoc basis, thus improving the efficiency of working capital tied to inventory holding. Other than for contracted parts, the main supplier for our maintenance business are the OEMs themselves. The major challenges are to optimize the inventory levels and minimize the lead time. Many airlines have moved to asset-light operation. In achieving this, accurate parts-consumption prediction is required.
Going forward, which areas do you feel are ripe for further improvement in the Malaysia supply chain?
First, we have an internal supply chain including our own MRO that is capable to repair and overhaul aircraft and components. Second, strengthening our internal supply chain will further improve our cost structure. This is an integral part of the MAB MRO strategy as well. Recently, we signed a memorandum of understanding with Piedmont Propeller System to support Malaysia and regional ATR propeller repair. We have the infrastructure ready and skillset to further improve our MRO and supply chain.
Will COVID-19 have an impact on the way in which this is managed, or on any other parts of your maintenance operation?
COVID-19 has impacted the whole world, and the aviation sector is among the worst-affected industries. While the number of flights was significantly reduced, we took the opportunity to increase maintenance activities during downtime. We positioned our maintenance under active parking, a flight-ready condition where we have lower return-to-service costs and higher safety due to frequent maintenance. We keep the cost down by using our internal supply chain and consuming our existing inventory.
The longer you park an aircraft, the more you need to do to keep it in good shape and return it to flying condition. The aircraft needs to be kept in a condition that enables quick resumption of operations. In this case, the parking procedure is applicable so that the number of tasks needed to prepare the aircraft for flight operations is minimized. It must be noted that aircraft with only parking procedures applied still require several recurring maintenance actions to ensure that the aircraft remains in a “ready-for-flight” condition.
Our engineers are working around the clock maintaining the grounded fleet, a process that includes running engines and powering-up aircraft, checking flight controls, and covering sensors and engines to protect inner workings from insects and dust.
Where do you stand on blockchain, and do you believe it could give greater visibility across your operation in the future?
Blockchain is still nascent in aircraft MRO. There is currently no law that regulates blockchain in Malaysia, including the aviation industry. Blockchain verification requires exchanging information between members, and this would raise issues of trust and confidentiality. Blockchain can be used for tracing aircraft parts in use and their status and condition, and this will help in ensuring on-time-performance. We see this as the future and will evaluate this technology application for MAB.
In the future, how do you think MROs like yours will manage your supply chain differently from today? Will it be more technology-driven?
We are always looking for improvements in supply chain management through development of technology, since the industry is also heavily driven by its evolution. Our challenge would always be on the implementation of new technology to suit our business needs consistent with the latest technology development available. Currently, we are in the process of developing process automation and using AI to improve efficiency with the tools that we are using. We foresee that supply chain management will be more technology-driven, with progressive staff upskills needed more than ever.