
Some MRO providers in Latin America are losing workers to competition from U.S.-based companies.
Commercial air traffic in Latin America has nearly returned to pre-pandemic levels, and forecasts paint a positive picture for its MRO industry. However, airlines and MROs in the region still face serious concerns about economic uncertainty, workforce shortages and ongoing supply chain issues.
Aviation Week’s MRO Latin America conference in Buenos Aires last month opened to mainly positive forecast indicators. Alton Aviation Consultancy expects Latin America’s commercial fleet to grow to more than 37,000 aircraft by 2032 at a compound annual growth rate (CAGR) of around 3%, while Aviation Week’s 2023 Commercial Fleet & MRO Forecast expects an even higher CAGR of 5.1% during this period. Aviation Week data further projects that Latin America will generate $55 billion in MRO demand in 2023-32. Alton also predicts that the engine market will grow faster than other MRO segments in the region.
While highlighting potential challenge areas for the region, Alton Managing Director Jonathan Berger pointed out the supply chain’s vulnerability to factors such as pandemics, geopolitical unrest and economic uncertainty. “Going forward, I think we’re going to see a lot more near-shoring,” which in the Americas will mean “a lot of North America looking to Latin America,” Berger says. “Perfectly positioned is Mexico. Growth in Mexico [in terms of] MRO and OEM supply chain will be booming over the next decade.”
Despite the potential benefits of a near-shoring trend, stakeholders in Latin America remain concerned about supply chain challenges. The majority of audience members responding to a poll at the event ranked supply chain delays and shortages as the factor expected to have the greatest impact on their business in 2023.
Within Argentina, operators are particularly concerned, given the country’s geographical distance from the rest of the Americas. Panelists from both Aerolineas Argentinas and Flybondi pointed out that with Miami as the closest hub at which to source parts from Europe and the U.S., delays contribute to anxiety.
“When we need parts to arrive on time here, it is a challenge, and it almost leads to a stop in the production line,” says Eduardo Enrique Gaspari, chief operating officer at Flybondi. Diego de Risio, MRO manager at Aerolineas Argentinas, notes that the airline now has longer waiting times for parts than it did pre-pandemic.
This is further compounded when suppliers cannot rely on promised lead times. In another audience poll, 53% of respondents identified “promised lead times that don’t happen” as their biggest supply chain frustration. Etienne Gombeaud, vice president of global sales at Setna iO, stresses that this lack of reliability is one of the biggest thorns in the supplier’s side. “We never really get the promised lead times,” he says, noting that a seller might quote 15 days for a part that actually takes up to 90 days to arrive.
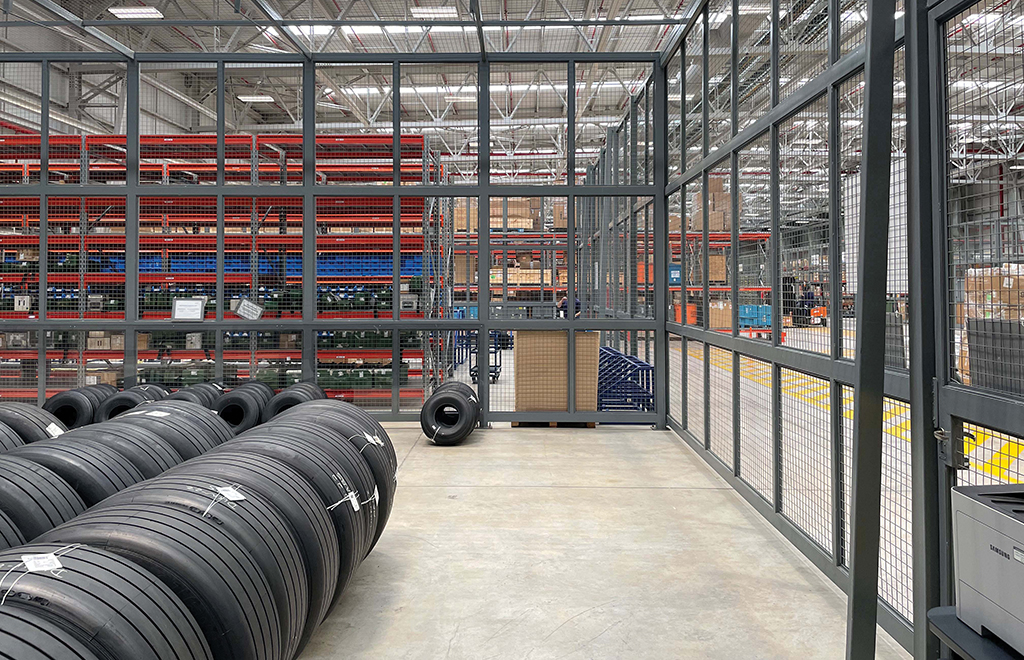
Panelists highlighted differing customs and paperwork requirements as well as credit issues between various Latin American countries as particular challenge areas.
“When it comes to customs, Brazil is one of the most challenging countries in the world,” says Francisco Mendes, StandardAero’s regional manager of airlines and fleets for Latin America and the Caribbean. “Our government has made some progress that most companies we know of have been a part of, and we can anticipate the release, so fortunately, we don’t usually see that many problems with customs in Brazil anymore. But there are some particularities that we need to follow and requirements for paperwork. When every country has their own rules, it’s pretty hard to keep up with all the requirements from every country that issues a part.”
Mendes says the biggest issue now is the increase in logistics costs, considering fuel prices and other inflation. “It’s not easy to work on that because that always affects the final costs of the part shipped out from Miami,” he says. “It’s really hard when you don’t have a local storage inventory close by because it’s a different price when you need to ship a part out of Miami versus out of Sao Paulo, Santiago or any close location, so that affects the whole operation.”
While inflation and currency fluctuations certainly affect costs in the region—particularly for countries like Argentina that are seeing local currencies valued at a fraction of the U.S. dollar—some countries are experiencing less of a squeeze.
Julio Gamero, CEO of Guatemalan carrier TAG Airlines, says the country’s currency stability and that of the countries to which it flies—including El Salvador, Honduras and Mexico—have shielded it somewhat. “Where we fly has given us protections,” he says. And since the airline operates turboprops that use less fuel, it has experienced less impact from higher fuel prices.
“We’re not exposed to dollar fluctuations,” says Alejandro Echeverria, CEO of Salvadorean MRO Aeroman. “The issue we face is supply chain cost increases.”
Ranked second behind supply chain issues in the audience poll about factors expected to impact business most in 2023 was the industry’s workforce shortage. Several companies, including TAG Airlines, Aeromexico and MRO Iberoamerica, reported challenges with technicians going to work for companies in the U.S. due to pay rate competition.
However, Frank Stevens, vice president of global MRO centers for Embraer, notes that the Brazilian OEM is seeing more competition for talent locally—both from other Latin American countries and technical industries outside aviation. “Our poaching comes from down the street, not the U.S.,” he says.
Latin American companies are tackling workforce recruitment and retention from several angles. For instance, Aerolineas Argentinas, Embraer and TAG Airlines are working with universities and technical schools to recruit more technicians and pilots. Aeroman recently built an office in a shopping mall and a sports center with basketball and soccer facilities to improve employee quality of life and appeal to young people.
Aviation companies in Latin America also are hoping to improve workforce diversity. Aerolineas Argentinas President Pablo Ceriani is aiming to have 25% of positions at the airline held by women by 2025, so it is working to improve hiring practices, culture and infrastructure (such as adding women’s bathroom facilities) to make the airline more inclusive. However, Technical Director Diego Georgiadis says women currently only comprise about 5-7% of the airline’s staff, “which is too low.”
Even with improved recruiting and retention, Boeing’s most recent Pilot & Technician Outlook predicts that Latin America will need 35,000 new technicians over the next decade. In light of the industry’s retirement boom and a growing proportion of younger workers, Latin America will face what the OEM calls an issue of “juniority of the workforce” as well.
“When you bring a new technician into the organization, now you’ve got to be skilled in what we traditionally call ‘tribal knowledge,’” Stevens says, highlighting that this extends past what can be found in a maintenance manual to an experienced technician’s knowledge about internal processes and practices that make maintenance more efficient.
“We have determined that, for the first six months, a mechanic is inefficient,” Stevens adds. For example, he points to avionics and sheet metal skills as areas that are consistently lacking for new technicians entering the workforce.
To tackle this, Embraer is working on a program called GIFT (Guiding and Influencing Future Technicians) in which Embraer’s experienced technicians teach new recruits over a 12-14-month period. Stevens says the program will help the younger generation learn Embraer’s values, culture and aircraft.
Georgiadis says Aerolineas Argentinas did not lay off any staff during the pandemic so it is not facing a workforce shortage. However, it is trying to move some younger staff into the types of roles currently held by older mechanics who could retire in the next few years. He adds that the airline moves its most experienced staff into line maintenance positions.
At Aeroman, Echeverria says on-the-job training plays a large role in tackling this issue. “Workforce development has been key,” he says, explaining that the MRO uses a 12-18-month program in which supervisors transfer knowledge to less experienced workers.