
Aer Lingus put this Airbus A320neo, its first, into service on Sept. 28.
Javier Jimenez, chief technical officer at Irish airline Aer Lingus, discusses the carrier’s MRO strategies and how it is looking to empower its maintenance workforce with technology.
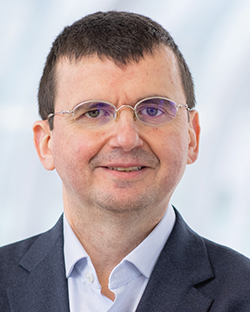
What are the key elements of Aer Lingus’ maintenance strategy?
The main element of Aer Lingus’ strategy is our people, especially so after the pandemic. Following on from COVID-19, we want to continue and indeed deepen engagement with our people and enable Aer Lingus to excel. We want to deliver the highest levels of maintenance in terms of performance, safety and cost to the airline. Engagement and empowerment of our people is critical to that. We are continuing to invest to ensure Aer Lingus is a great place to work. This means we also need to provide the tools to excel. One way we are doing this is through digitalizing some of our maintenance activities. We want to implement technology to try to facilitate the way our people work and try to give them more information and data to help them make decisions. We want to be the best maintenance organization we can be, but we can’t do that without our people.
Which technologies are the Aer Lingus maintenance division looking to invest in?
There are several streams. The first is around IT. We use an AMOS system, and we want to reassess the way we are using it. There are still some processes that are running outside of AMOS, so our objective is to include all those processes into the platform. We also want to integrate these into AMOS mobile to facilitate tasks to our people. This will enable engineers to carry tablets and access AMOS to open and close work orders while they are working on the aircraft, rather than going back and forth between the office and aircraft. In terms of being more efficient in the way we manage our inventories, we want to implement a digital tool to optimize the way we plan our parts stock. We are looking at partnering with a specialist for this process, which has traditionally been done manually by airlines. We want to bring artificial intelligence to the system, so it is continually learning about our stock requirements. We will also place a lot of focus on predictive maintenance, which will be very important for the airline. To date, the maintenance we’ve undertaken has primarily been preventative and done to avoid issues. Now, we want to anticipate maintenance problems before they occur. To do this, we are exploring several tools available in the market including Airbus’ Skywise and Lufthansa Technik’s Aviatar. We are still in the process of deciding how to move forward with our predictive maintenance.
What does Aer Lingus look for in a supplier, whether that is an MRO provider, logistics specialist or a maintenance training partner?
While cost is an important factor, we value performance highly, as that is something we don’t want to compromise on. It is very important for us to find a partner to help us get through issues that arise. Typically, we have partnerships in place for a number of years. For example, most of our contracts related to engine and component maintenance are long-term, so it’s important that all sides are happy, trust each other and share the same goals. There will be times when the supplier will need our help, and there will be times when we need the help of our suppliers. Given the longevity of these agreements, there will be different cycles in the life of the contract. The pandemic was a bad time for airlines. Suppliers were also hit by this, yet were still in a better position than airlines. This meant we had to turn to them for help, signaling a true partnership between airline and supplier.
How has Aer Lingus changed its maintenance contract arrangements during the pandemic?
COVID-19 highlighted issues that weren’t considered before. During the pandemic, airlines with committed, fixed-price maintenance contracts tended to suffer more than those with flight-hour agreements, which provided variable costs. There is now a good understanding that our costs should be variable as much as possible. Many of our contracts, especially in engines and components, are flight-hour agreements and fit very well for that purpose. However, before COVID-19, everyone was very optimistic, and flight-hour agreements may have included a number of minimum hours that we were committed to fly per year, and nobody thought that the flown-hours were going to be below that. When COVID-19 hit, those minimum hours couldn’t be fulfilled. Despite being a variable type of contract, there were still financial obligations to be met. Going forward, we anticipate all airlines will be seeking to eliminate those minimum-hour requirements from agreements. At the moment, the impact of higher inflation and the increase in costs of materials means we are seeking protection against those escalations. However, our parent company, IAG, and more specifically our centralized procurement team have been good at providing effective protection from these inflation impacts.
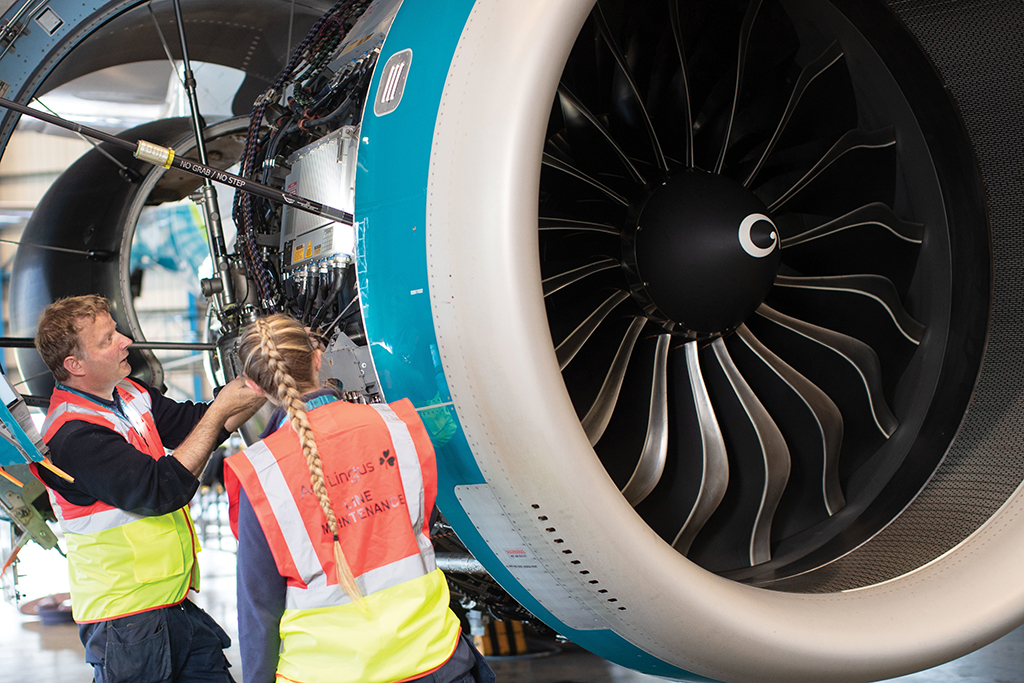
How have airline operations recovered in 2022, and how have you ramped up your maintenance division to deal with this?
Even when our whole fleet was grounded, it still required maintenance, and our people were committed and remained at work; in fact, they were very busy at the height of the crisis. Restarting flight operations was a challenge, given the scale of the undertaking for reactivating so many aircraft. This year, we’ve flown around 90% of our operational capacity versus 2019, which is a serious achievement. We planned for the recovery phase for a long time and were ready to meet the ramp-up. Our technical staff worked hard to get aircraft ready and delivered a good technical performance, especially during the summer. This again shows the importance of our people and our maintenance and engineering teams.
What are you seeing in relation to supply chain delays and maintenance turnaround times? Where do the challenges lie?
At this time, the supply chain is complicated, and possibly the weakest point in it are the OEMs. The delays we face with heavy maintenance and engine overhauls are often caused by the lack of availability of new parts, which we need from manufacturers. This means we have been actively working with those suppliers. In the IAG Group, there are some considerations about increasing our capabilities for repairs for parts rather than overly relying on new components coming from OEMs. As it has for other airlines, the availability of parts and the scarcity of raw material along with logistics delays are undoubtedly the main problems the industry faces today. However, the situation has improved in recent months, and we continue to work effectively with our suppliers. I’m very optimistic about next year, but obviously with increased flying volumes next summer it’s going to be a challenge, and our suppliers will need to be ready for this.
How are you managing engine shop visits differently compared to pre-pandemic times?
Given the supply chain issues mentioned, turnaround times have been longer than expected in relation to engine maintenance. Shop visits of 60 days have turned into 120 days, for example, and this has obviously been a big challenge to the maintenance operation. We are working with our suppliers to address this issue. We are doing this through sunset programs to optimize the life cycle of our CFM56 fleet.
What are you seeing in relation to the labor market? Has recruiting skilled people been challenging, despite Ireland’s status as an aviation hub?
Over the past few years, the pool of people willing to work in aviation globally has declined. Due to factors such as COVID-19, people have seen first-hand how unexpected events and circumstances can impact the aviation industry. In my professional career, I certainly haven’t seen an impact as deep as this one. The aviation sector and Aer Lingus have a strong record of attracting and developing talented engineers and maintenance specialists, but we are very aware that we have a competitive labor market in this country, given the demand for skilled and experienced people by other industries including the finance, technological and pharmaceutical sectors. From an Aer Lingus perspective, we have a high level of retention across our maintenance operation, and we do not take that for granted.
However, when trying to recruit new people into the business, it is becoming very competitive, especially in skilled areas such as B1 and B2 certified engineers. We are going down two routes to address this. The first is benefiting from Ireland’s status as a member of the European Union, which we use to attract labor from overseas across Europe. The other is in our apprenticeship program, which is very important in creating new talent avenues. Every year we take 15-20 new people who graduate in four years to become qualified engineers in the Aer Lingus maintenance team.