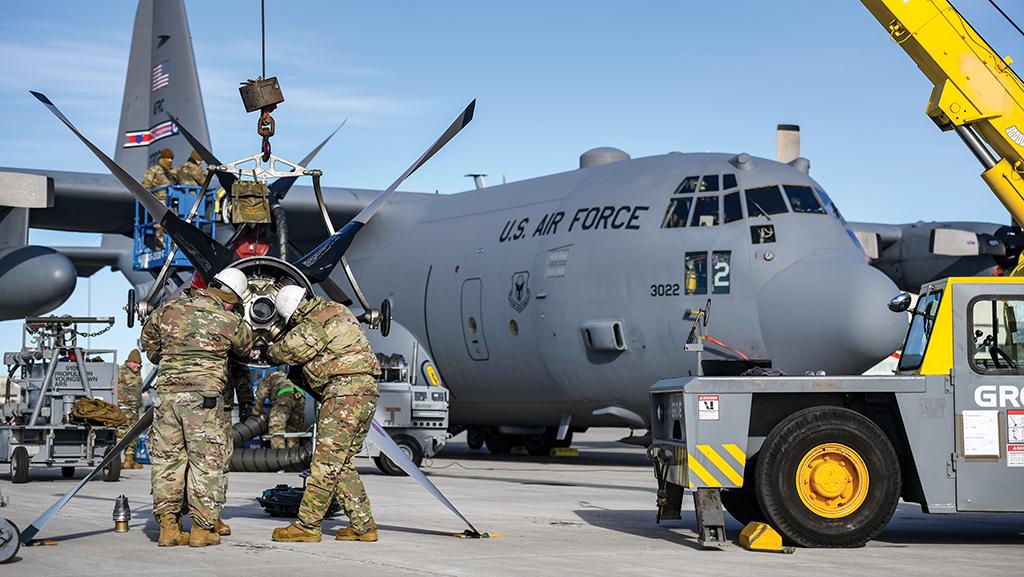
The Pentagon’s top weapons buyer and sustainment official has a common line he likes to use for CEOs who may be overconfident in their supply base. And because he is a former CEO, Bill LaPlante is comfortable saying it publicly.
“Any CEO who says, ‘I know my supply chain’ is like a CEO who says, ‘I’ve never been hacked,’” the under secretary of defense for acquisition and sustainment says. “They just don’t know it.”
- Top weapons buyer calls for supply chain illumination
- Tankers, airlifters, helos grounded by bad parts last year
The Defense Department’s sustainment office has raised concerns about the integrity of supply chains and parts inventories from first-tier suppliers down to those providing raw materials. The Pentagon is undertaking several steps to shore up the security of its supply chains, following multiple high-profile incidents of the wrong parts and even Chinese-produced materials making their way into critical aircraft.
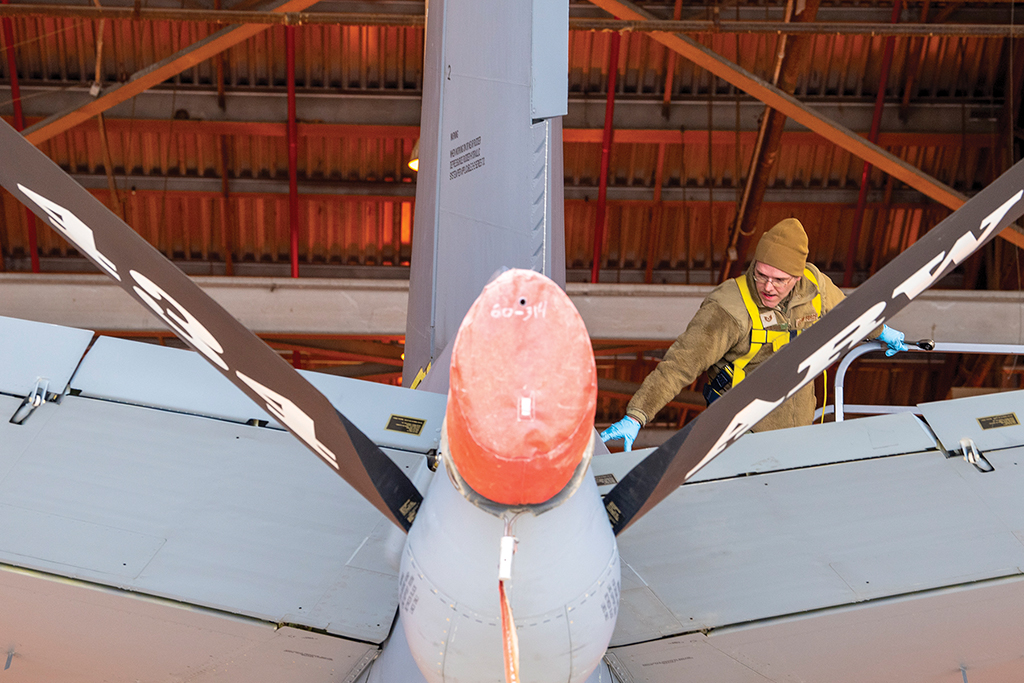
LaPlante says a key focus in this area is the adoption of a private-sector approach called supply chain illumination. It applies big data analytics to open-source and other sets of information to monitor supply chains for the defense industrial base and those who maintain the aircraft and weapons. Dozens of companies in the private sector can provide this capability, and the Pentagon needs to adopt it.
“This is a big thing in the commercial world,” LaPlante says. “It’s going to have to be a big thing in the [Defense Department], and we’re exploring it.”
The integrity of parts supply for the defense industrial base made headlines in September 2022, when it emerged that a Chinese-made component had been found deep in the F-35 supply chain. All jets delivered before that month included Chinese materials in samarium-cobalt alloy magnets within the Honeywell integrated power package system. Deliveries of the aircraft were halted until LaPlante signed a waiver the next month stating that the acceptance of the aircraft is needed, the magnet did not harm the aircraft, and Honeywell would seek an alternative source of the metal.
LaPlante says a common issue within the defense industrial base is contract privity, which can mean that a subcontractor’s suppliers are kept as a trade secret from the prime contractor unless otherwise outlined.
In recent years, the integrity of spare parts inside military service sustainment facilities has come into question after aircraft had to be grounded, inspected and refitted after improper components were installed.
“It’s always a challenge making sure you have the right parts and that the right parts are in fact safe,” LaPlante says.
In February, the Air Force stopped flying its Boeing KC-135 Stratotankers, RC/WC-135s and E-3 Sentry AWACS once it was discovered that “nonconformal” vertical terminal fitting pins, or tail pins, had been installed during depot maintenance. A memorandum stated that if a pin failed in flight, the aircraft’s vertical stabilizer could fall off. The Air Force returned the aircraft to flight following inspections and replacement of the pins.
In September 2022, the Air Force was forced to ground its C-130H fleet after cracks were found in the aircraft’s propeller barrel assemblies. An Air Force investigation determined that a process of using an electric arc pen to engrave serial numbers in the propellers during depot maintenance likely caused the cracks. The Air Force must replace the propeller barrels, including with modernized Collins Aerospace NP2000 systems, and the process is expected to take several months or even years, Air Mobility Command says.
Gen. Mike Minihan, head of Air Mobility Command, tells Aviation Week that while the process for the C-130Hs and KC-135s affected flight operations, it shows the Air Force can identify and handle deficiencies quickly to avoid risk.
“There’s no part of my life that isn’t eventually associated with some factory producing things, and so there are some supply chain things that will affect when the get-well date is,” he says. “When it comes to the tail pins, that’s a pretty rapid fix. And most importantly, it’s the after-action report that happens after. It’s not just that we identified it, mitigated it and handled it; it’s how do we go back and make sure that it’s a learned process.”
The Air Force was not alone. In August 2022, the U.S. Army grounded its Boeing CH-47 Chinook fleet after faulty O-rings not produced by OEM Honeywell were installed on the T55 engines at the Army Depot. These faulty O-rings were linked to engine fires, and Army Aviation and Missile Command says the parts were mislabeled at the depot.