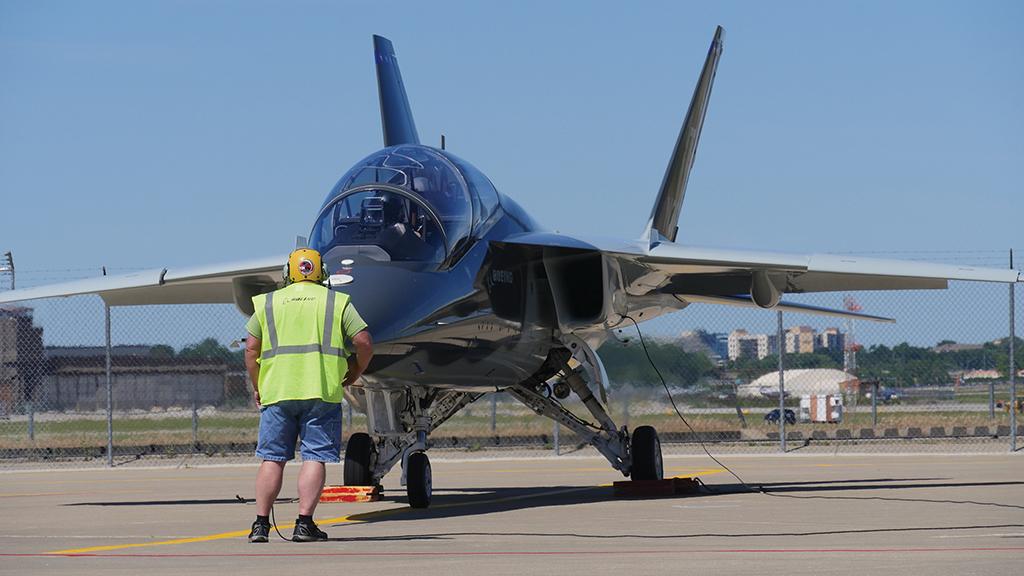
A Boeing-owned T-7A prototype launched a second phase of early flight testing on June 22, taking off into the St. Louis sky three times, after a hiatus of several months caused by a scheduled modification period.
But the normally routine milestone occurred in the context of a newly revealed schedule delay and budget cut by U.S. Air Force officials, along with the discovery of a previously undisclosed aerodynamic issue that raised fresh questions about Boeing’s assertions of the benefits of using a revolutionary design process for the T-7A.
- Phase II flight testing has begun
- Software fix loaded for wing-drop problem
The program, even so, shows no sign of further spiraling. A software fix for a wing-drop problem discovered during the Phase 1 flight testing—but acknowledged by Air Force officials and Boeing only in mid-June—was loaded into the prototype aircraft on June 17. The aircraft performed “wonderfully and as expected,” says Steve Schmidt, a Boeing test pilot for the T-7A.
The aerodynamic problem also played no role in the T-7A program delay, according to Boeing and Air Force officials. The Air Force’s official budget documents show a 16-18-month delay in the start of the production phase, which is now scheduled to begin in the fourth quarter of fiscal 2023. But Boeing says the budget documents included an outdated placeholder schedule that the Air Force set before contract award in September 2018. The internal schedule set after contract award shows a 7-9-month delay for the program, according to Boeing and the Air Force.
“The most recent [Milestone C] estimate was for the first quarter of fiscal 2023, which is now the fourth quarter of fiscal 2023,” an Air Force spokesman says. “So technically, [we’re] looking at a nine-month delay.”
The Air Force blamed the schedule slip on delays with completing the initial design of the T-7A and COVID-19 disruptions to Boeing’s supply chain. Answering a question from a lawmaker about a $17 million budget cut for the T-7A program in the fiscal 2022 budget request, Gen. Charles Brown, the Air Force chief of staff, revealed the delay during testimony to a House Armed Services Committee panel on June 16.
The update added the first setbacks to one of Boeing’s most important new military aviation programs. The Air Force selected Boeing for the T-X contract because its $9.2 billion bid for 351 aircraft and 42 simulators came in significantly lower than competitors’. Boeing’s aggressiveness caught competitors off guard; Lockheed Martin later said matching Boeing’s bid would have led to a $5 billion loss.
But Boeing remains confident the fixed-price contracts to develop and build the T-7A, simulators and other training devices will be profitable. That forecast is based primarily on what the company says was the U.S. aerospace industry’s most extensive use of model--based systems-engineering tools during the design phase. The approach replaces paper drawings with a digital model as the design reference. By establishing a 3D model—which the Air Force has branded the “eT-7A”—as the reference, the change also gives Boeing designers deeper insight into how design changes related to aerodynamic performance influence the cost and complexity of manufacturing and maintaining the aircraft.
If it works, Boeing expects to deliver T-7As at a unit cost well below the rates of any other U.S. defense contractor and still turn a profit. The Air Force also expects the new process to shave months off the overall development schedule. Even factoring in the new 7-9-month delay, the program expects to launch T-7A production within five years of contract award, compared with six for the Lockheed Martin F-35A.
Boeing has reported a series of successes related to the model-based systems-engineering approach. The fuselage sections of the prototype aircraft were spliced in 30 min. rather than the normal 24 hr. In May, the test aircraft ordered by the Air Force was assembled, with the front and aft fuselage sections joined in less than 30 min.
As flight testing of the prototypes and manufacturing of the Air Force’s test aircraft continue, Boeing will learn more about how the digital model of the T-7A helps the program avoid any further surprises with aerodynamic or assembly issues.
Comments
But if Boeing's model-based systems-engineering approach fails and the T-7 contract produces anything like the losses generated by the KC-46 program, it could potentially doom the company.
People need to give Boeing a chance to prove themselves again.
20% better than crap is still crap.